- お役立ち記事
- Sulfide Process Quality Control and Procurement: Ensuring Product Durability and Safety
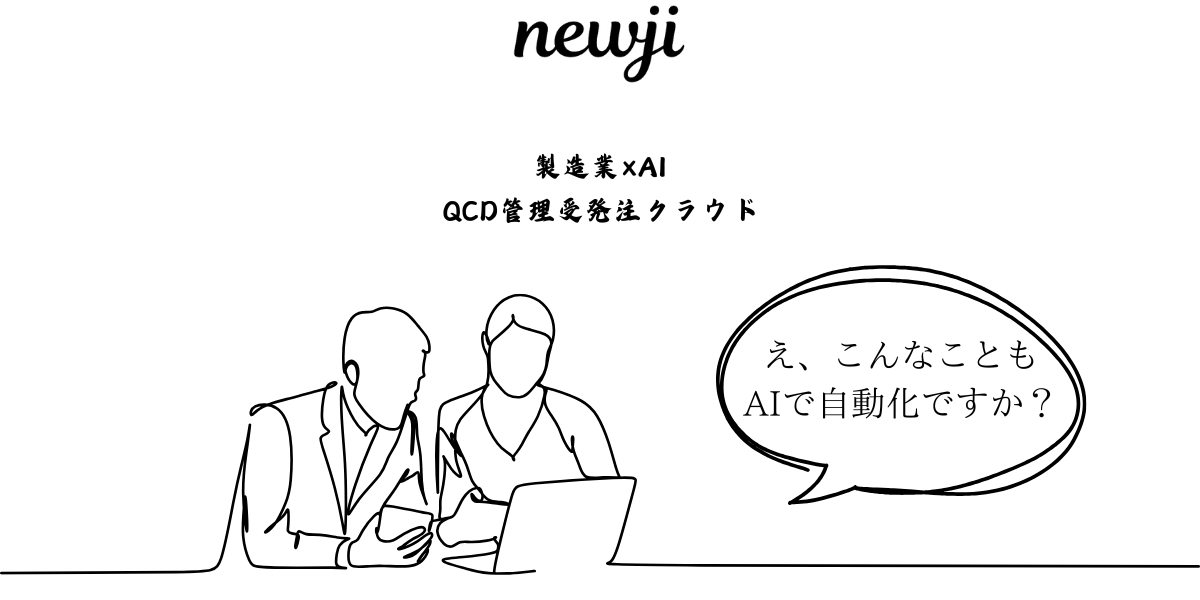
Sulfide Process Quality Control and Procurement: Ensuring Product Durability and Safety
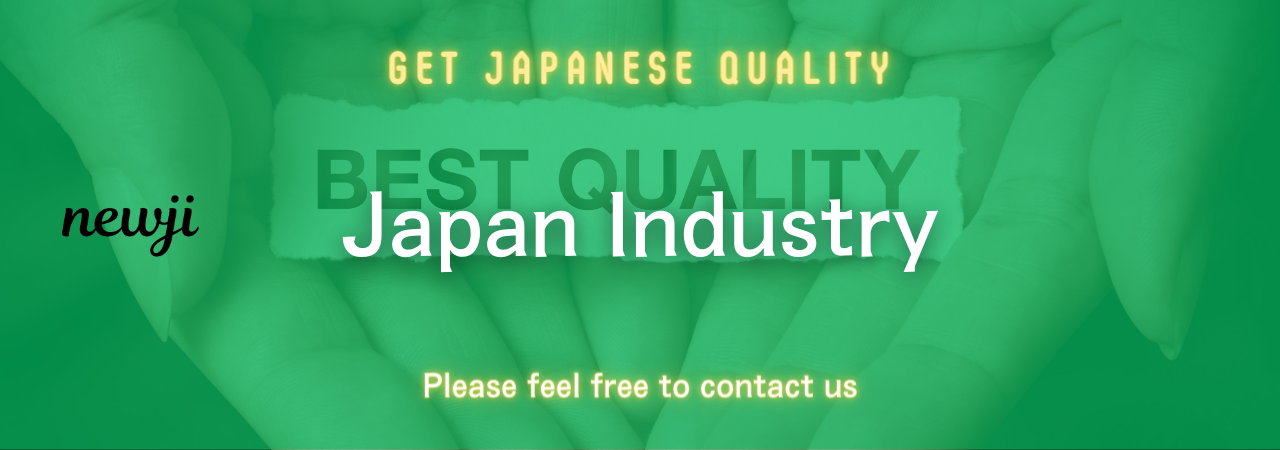
Maintaining high standards in the sulfide process is critical for ensuring the durability and safety of products.
This involves meticulous quality control and strategic procurement practices, which can significantly impact the overall performance and longevity of sulfide-based products.
By following well-established protocols and guidelines, manufacturers can achieve superior quality and reliability.
目次
Understanding the Sulfide Process
The sulfide process is commonly used in various industries, including mining, chemical manufacturing, and metallurgy.
It involves the use of sulfide compounds to produce essential materials and products.
High-quality sulfide processes are crucial for creating reliable and durable goods that meet safety standards.
In the mining industry, the sulfide process plays a pivotal role in extracting metals such as copper, nickel, and zinc from their ores.
Chemical manufacturing relies on sulfides for producing substances used in agriculture, medicine, and many industrial applications.
Metallurgical processes, too, often use sulfides to enhance the properties of metals and alloys.
Importance of Quality Control in the Sulfide Process
Quality control is an essential component of the sulfide process.
It ensures that each step, from raw material selection to final product testing, adheres to stringent standards.
This not only guarantees product durability but also compliance with safety regulations.
Monitoring the quality of raw materials is the first step in the quality control process.
Only materials that meet specified criteria should be used to prevent any variability in the final product.
Regular inspections and testing of raw materials help identify impurities and inconsistencies that could compromise product integrity.
During the production phase, continuous monitoring and testing of sulfide compounds are essential.
This can include checking the chemical composition, temperature, pressure, and other critical parameters.
Advanced analytical tools and techniques should be employed to ensure these parameters remain within acceptable limits.
Consistency in Production
Achieving consistent production quality requires adherence to standard operating procedures (SOPs).
These procedures provide a detailed roadmap for each phase of the sulfide process, outlining the specific steps and controls necessary.
By following SOPs, manufacturers can minimize variations and maintain uniform quality across different batches.
Regular maintenance and calibration of equipment are also vital to sustaining production consistency.
Well-maintained machinery operates efficiently and reduces the risk of defects.
Scheduled maintenance checks can help identify potential issues before they escalate into significant problems.
Testing and Inspection
Stringent testing and inspection regimes are crucial for verifying product quality.
This includes both in-process testing and final product inspection.
In-process testing involves evaluating the product at various stages of the manufacturing cycle, while final inspection examines the end product.
Common tests in the sulfide process might include spectroscopic analysis, thermal analysis, and mechanical testing.
These tests provide valuable data on the product’s chemical makeup, thermal stability, and mechanical properties, ensuring they meet the desired specifications.
Procurement Strategies for Quality and Safety
Strategic procurement plays a crucial role in maintaining the quality and safety of sulfide-based products.
Effective procurement strategies ensure the availability of high-quality raw materials while minimizing costs and risks.
Supplier Selection
Choosing the right suppliers is fundamental to procurement success.
Suppliers should be evaluated based on their ability to provide high-quality materials consistently.
This includes assessing their production processes, quality control systems, and compliance with industry standards.
Building strong relationships with reliable suppliers can lead to long-term benefits.
Suppliers who understand your quality requirements are more likely to meet your expectations and deliver materials that enhance product durability and safety.
Material Sourcing
Sourcing the right materials is another key aspect of procurement.
Raw materials should be chosen based on their suitability for the sulfide process and their impact on final product quality.
Sourcing strategies may involve procuring materials from multiple suppliers to ensure a continuous supply and reduce dependency on a single source.
Regular audits and evaluations of suppliers help maintain the quality of sourced materials.
These audits can uncover potential issues and drive improvements in supplier performance.
Ensuring transparency in the supply chain is also essential to track the origin and quality of raw materials.
Cost Management
Effective cost management strategies can help balance quality requirements with budgetary constraints.
Negotiating favorable terms with suppliers, bulk purchasing, and optimizing inventory levels are some ways to control costs without compromising on quality.
Investing in high-quality materials may have higher upfront costs but can lead to long-term savings by reducing defects, rework, and product failures.
Understanding the total cost of ownership (TCO) is crucial for making informed procurement decisions.
Risk Mitigation
Identifying and mitigating risks is a critical part of the procurement process.
This includes risks related to supplier reliability, material quality, and supply chain disruptions.
Developing contingency plans and maintaining buffer stocks can help manage these risks effectively.
Collaborating with suppliers to improve their quality control processes can also mitigate risks.
By sharing best practices and providing feedback, manufacturers can help suppliers enhance their performance and safeguard the supply chain’s integrity.
Conclusion
Ensuring the quality and safety of sulfide-based products through rigorous quality control and strategic procurement is imperative for manufacturers.
By maintaining high standards in both areas, manufacturers can produce reliable, durable, and safe products that meet market demands and regulatory requirements.
Through a combination of thorough testing, consistent production practices, strategic sourcing, and effective risk management, the sulfide process can deliver superior results.
Investing in these practices not only enhances product performance but also strengthens the manufacturer’s reputation in the industry.
By prioritizing quality and safety at every step, manufacturers can achieve long-term success and customer satisfaction.
資料ダウンロード
QCD調達購買管理クラウド「newji」は、調達購買部門で必要なQCD管理全てを備えた、現場特化型兼クラウド型の今世紀最高の購買管理システムとなります。
ユーザー登録
調達購買業務の効率化だけでなく、システムを導入することで、コスト削減や製品・資材のステータス可視化のほか、属人化していた購買情報の共有化による内部不正防止や統制にも役立ちます。
NEWJI DX
製造業に特化したデジタルトランスフォーメーション(DX)の実現を目指す請負開発型のコンサルティングサービスです。AI、iPaaS、および先端の技術を駆使して、製造プロセスの効率化、業務効率化、チームワーク強化、コスト削減、品質向上を実現します。このサービスは、製造業の課題を深く理解し、それに対する最適なデジタルソリューションを提供することで、企業が持続的な成長とイノベーションを達成できるようサポートします。
オンライン講座
製造業、主に購買・調達部門にお勤めの方々に向けた情報を配信しております。
新任の方やベテランの方、管理職を対象とした幅広いコンテンツをご用意しております。
お問い合わせ
コストダウンが利益に直結する術だと理解していても、なかなか前に進めることができない状況。そんな時は、newjiのコストダウン自動化機能で大きく利益貢献しよう!
(Β版非公開)