- お役立ち記事
- Supplier audit method for purchasing department to prevent quality problems in manufacturing industry
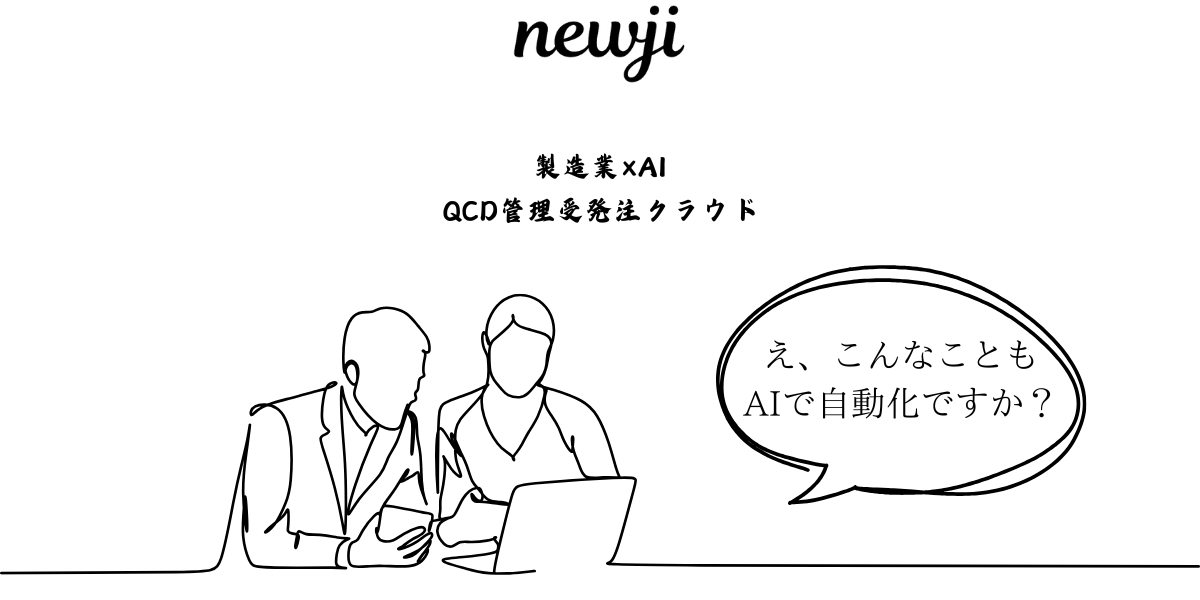
Supplier audit method for purchasing department to prevent quality problems in manufacturing industry
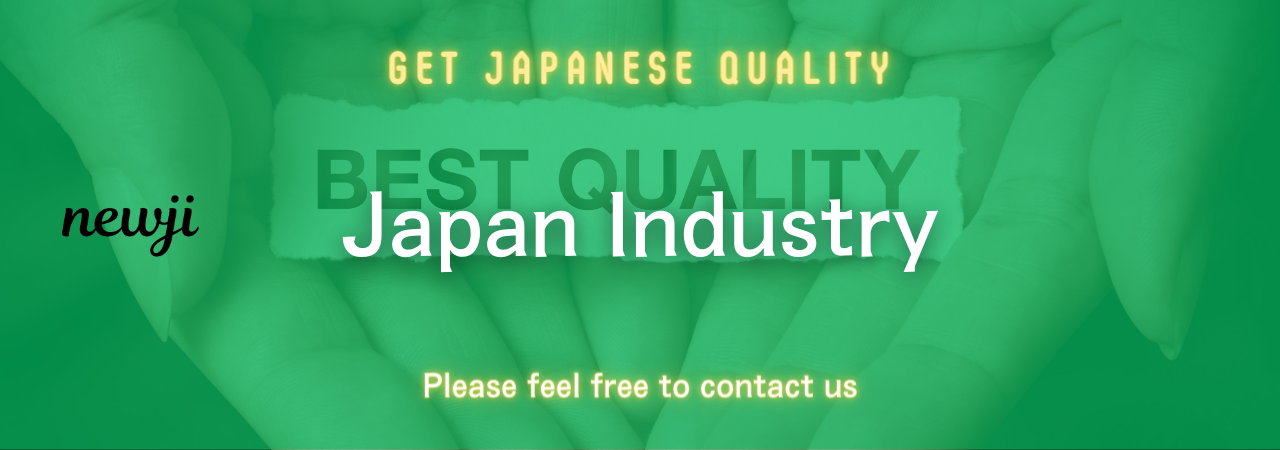
目次
Understanding Supplier Audits
In the manufacturing industry, ensuring high-quality products often begins with the components and materials supplied by external vendors.
A supplier audit is a critical process that purchasing departments use to identify and mitigate risks before they translate into quality problems.
Understanding how to effectively manage these audits can significantly enhance the overall quality and reliability of the products manufactured.
What is a Supplier Audit?
A supplier audit is a systematic examination of a supplier’s processes, systems, and facilities.
It aims to ensure that they meet the required standards and regulatory requirements necessary for producing quality products.
Audits can focus on several aspects, including production capabilities, quality assurance processes, compliance with industry standards, and overall financial stability.
The Importance of Supplier Audits
Supplier audits are crucial for maintaining quality in manufacturing for several reasons.
Firstly, they help identify potential quality issues before they become problems in the production line.
By identifying these issues early, companies can work with suppliers to correct them, reducing the likelihood of defective products reaching customers.
Secondly, supplier audits can help in building stronger relationships with vendors.
They open up lines of communication and encourage both parties to work towards mutual goals of quality and efficiency.
Lastly, regular audits can provide assurance that the supplier complies with industry standards and regulations.
This compliance is critical for legal reasons and maintaining a company’s reputation.
Steps for Effective Supplier Auditing
Implementing an effective supplier audit requires a well-structured plan.
Here are some steps to consider:
1. Define Audit Objectives
Before initiating a supplier audit, it’s essential to clearly define your objectives.
What are you hoping to achieve?
Are you looking to ensure regulatory compliance, improve product quality, or assess the overall reliability of a supplier?
Having clear objectives helps in focusing the audit and measuring its success.
2. Develop a Comprehensive Checklist
A comprehensive checklist ensures that auditors cover all necessary aspects of the supplier’s operations.
The checklist should include areas such as quality control processes, materials management, production capacity, and logistics.
Tailor the checklist to suit the specific products and industry standards relevant to your organization.
3. Assemble an Experienced Audit Team
The audit team should comprise individuals with the necessary expertise to evaluate the supplier’s operations effectively.
This team might include quality assurance specialists, engineers, or procurement professionals, depending on the focus of the audit.
Their combined knowledge will provide a more thorough assessment of the supplier’s capabilities.
4. Conduct the Audit On-Site
Whenever possible, audits should be conducted on-site at the supplier’s facility.
An on-site visit allows auditors to observe processes firsthand and engage with the supplier’s staff directly.
This direct interaction can provide deeper insights into the culture, operations, and potential areas of improvement.
5. Evaluate Documentation and Records
Reviewing documentation and records is a critical component of a supplier audit.
This process involves examining quality certificates, production logs, and compliance records.
These documents help verify that the supplier follows the necessary procedures consistently.
Post-Audit Activities
The supplier audit process doesn’t end with the on-site visit.
Several post-audit activities are critical to ensure the audit is effective in preventing future quality issues.
1. Create a Detailed Audit Report
After the audit, compile a detailed report outlining findings, observations, and any areas needing improvement.
The report should include both positive aspects and areas where the supplier needs to improve.
This transparency helps build trust and guides suppliers on where to focus their quality improvement efforts.
2. Conduct a Follow-Up Review
A follow-up review is essential to ensure that suppliers act on the findings from the audit report.
This review can be a scheduled meeting or another on-site visit.
It’s an opportunity to assess whether suppliers have implemented corrective actions and improvements as recommended.
3. Establish Ongoing Communication
Establishing regular communication with your suppliers is crucial for maintaining long-term relationships and continuous quality improvement.
Feedback from audits should lead to constructive discussions on future collaborative efforts to enhance quality and efficiency.
Setting up regular touchpoints ensures that both parties are aligned on expectations and any changes in standards or processes.
Tools for Supplier Audits
Technology can play a significant role in enhancing the effectiveness of supplier audits.
Some tools and systems that can support this process include:
1. Audit Management Software
Audit management software can streamline the entire audit process, from planning to reporting.
These tools allow audit teams to schedule audits, manage checklists, record findings, and generate reports efficiently.
By using such software, companies can ensure consistency and accuracy in audit activities.
2. Supplier Quality Management Systems (QMS)
A robust Supplier QMS helps in tracking supplier performance over time.
These systems provide valuable data on the supplier’s track record, issues arising, and compliance history, aiding in more informed decision-making during audits.
3. Cloud-Based Document Sharing
Using cloud-based platforms for sharing documents and records can improve transparency and accessibility.
Such systems allow auditors to view up-to-date information from anywhere, facilitating better audit preparation and execution.
Conclusion
Conducting supplier audits is a vital method for purchasing departments in the manufacturing industry to prevent quality problems.
An effective supplier audit involves thorough preparation, a systematic approach, and ongoing communication with the supplier.
By using structured audit processes and leveraging technology, companies can ensure supplier compliance, improve product quality, and foster long-term, effective partnerships with their vendors.
資料ダウンロード
QCD調達購買管理クラウド「newji」は、調達購買部門で必要なQCD管理全てを備えた、現場特化型兼クラウド型の今世紀最高の購買管理システムとなります。
ユーザー登録
調達購買業務の効率化だけでなく、システムを導入することで、コスト削減や製品・資材のステータス可視化のほか、属人化していた購買情報の共有化による内部不正防止や統制にも役立ちます。
NEWJI DX
製造業に特化したデジタルトランスフォーメーション(DX)の実現を目指す請負開発型のコンサルティングサービスです。AI、iPaaS、および先端の技術を駆使して、製造プロセスの効率化、業務効率化、チームワーク強化、コスト削減、品質向上を実現します。このサービスは、製造業の課題を深く理解し、それに対する最適なデジタルソリューションを提供することで、企業が持続的な成長とイノベーションを達成できるようサポートします。
オンライン講座
製造業、主に購買・調達部門にお勤めの方々に向けた情報を配信しております。
新任の方やベテランの方、管理職を対象とした幅広いコンテンツをご用意しております。
お問い合わせ
コストダウンが利益に直結する術だと理解していても、なかなか前に進めることができない状況。そんな時は、newjiのコストダウン自動化機能で大きく利益貢献しよう!
(Β版非公開)