- お役立ち記事
- Supplier Evaluation Based on Quality Data Analysis
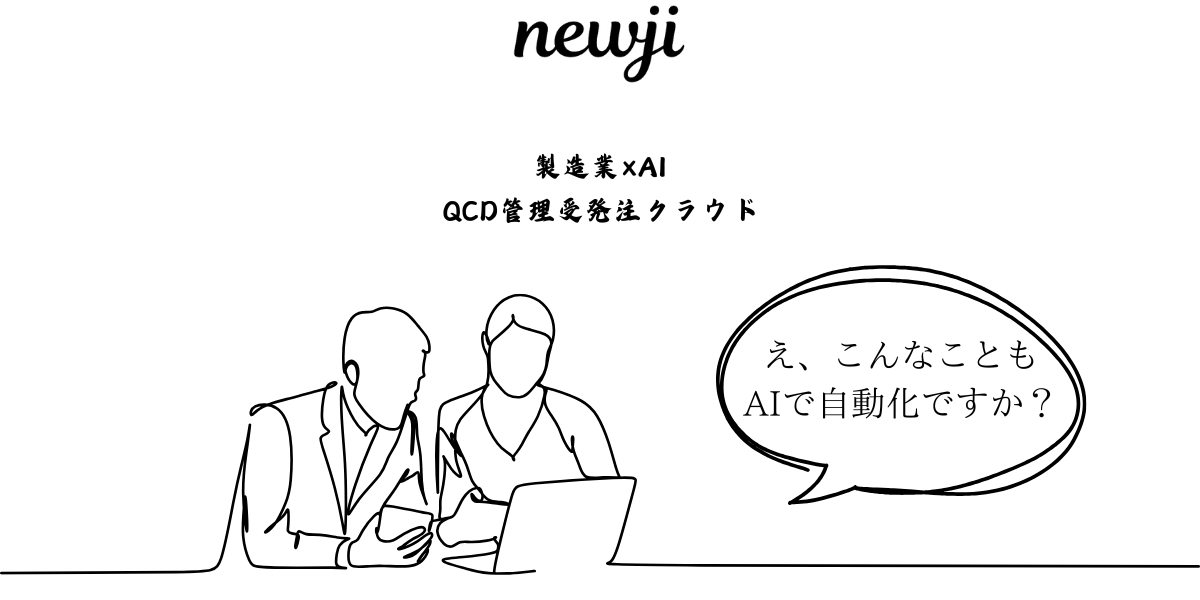
Supplier Evaluation Based on Quality Data Analysis
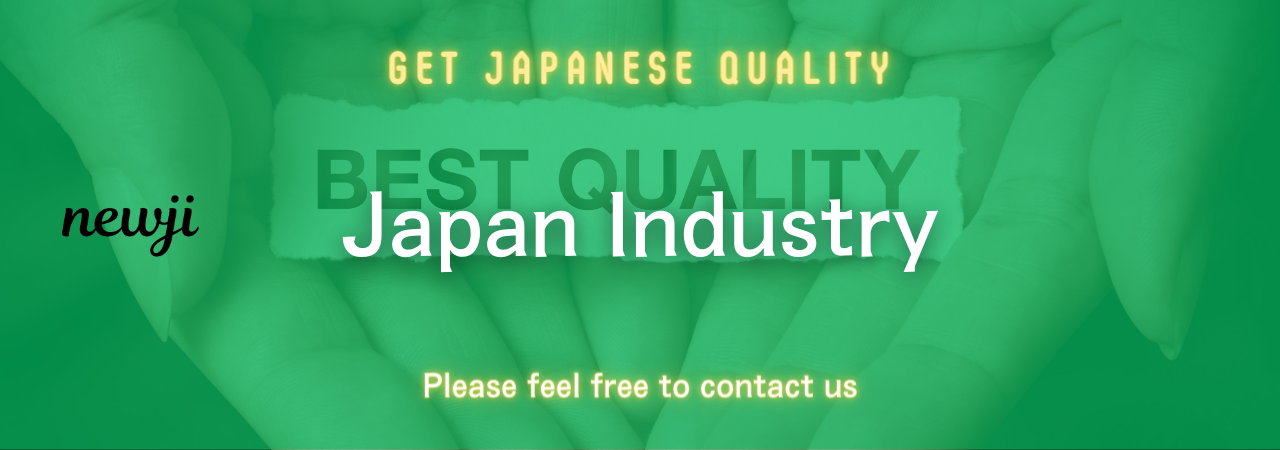
目次
Understanding Supplier Evaluation
Supplier evaluation is a critical process for companies that rely on external vendors for materials, services, or products.
This process helps businesses ensure that their suppliers meet certain standards, particularly in quality, delivery, and cost.
One of the most effective ways to assess a supplier’s performance is through quality data analysis.
The Importance of Quality Data Analysis
Quality data analysis is the examination and interpretation of data related to the quality of products supplied by a vendor.
This analysis provides invaluable insights into the supplier’s capability to meet the required standards consistently.
By scrutinizing this data, businesses can make informed decisions regarding supplier selection, retention, and improvement.
Key Metrics in Quality Data Analysis
To accurately evaluate suppliers based on quality data, it’s essential to consider specific key metrics.
Some of the most crucial metrics include:
Defect Rates
Defect rates measure the number of defective products delivered by a supplier relative to the total number of products supplied.
A low defect rate indicates that the supplier maintains high-quality control standards.
Conversely, a high defect rate suggests potential issues in the supplier’s manufacturing process or quality assurance practices.
On-Time Delivery
On-time delivery is another vital metric that evaluates how often a supplier delivers goods within the agreed timeframe.
Frequent late deliveries can disrupt production schedules and affect overall business operations.
High on-time delivery rates, therefore, reflect well on the supplier’s reliability and efficiency.
Response Time to Quality Issues
The time it takes for a supplier to respond and address quality issues is crucial.
Swift responses can minimize the impact of defective products on business operations and customer satisfaction.
Evaluating this response time helps businesses understand the supplier’s commitment to quality and customer service.
Customer Complaints
The number and severity of customer complaints connected to a supplier’s products serve as direct feedback on quality.
A supplier with fewer complaints is seen to provide higher-quality products.
Monitoring complaints can highlight areas for improvement and help businesses enforce stricter quality standards with their suppliers.
Steps to Conduct Quality Data Analysis
Conducting a thorough quality data analysis involves several essential steps.
Following these steps can help businesses effectively evaluate their suppliers and ensure continuous quality improvement.
Collect Data
The first step in quality data analysis is collecting relevant data from various sources.
This data can come from internal quality control records, customer feedback, and supplier performance reports.
Ensuring the data is comprehensive and accurate is crucial for a valid assessment.
Analyze Data
Once the data is collected, the next step is to analyze it using statistical tools and software.
This analysis involves identifying patterns, trends, and anomalies that could indicate quality issues.
The objective is to derive meaningful insights that can guide the evaluation process.
Set Benchmarks
Setting benchmarks involves defining the standards or criteria that suppliers must meet.
These benchmarks are based on the data analysis and industry standards.
They serve as a yardstick to measure and compare supplier performance.
Evaluate Suppliers
With benchmarks in place, businesses can evaluate suppliers against these standards.
This evaluation helps identify underperforming suppliers and highlights those that exceed expectations.
The comparison aids in ranking suppliers and making informed decisions about future partnerships.
Implement Improvements
The final step is to implement improvements based on the evaluation findings.
This could involve working with suppliers to address specific issues or making changes to supplier selection criteria.
Continuous monitoring and re-evaluation ensure ongoing quality improvements.
Benefits of Supplier Evaluation
Effective supplier evaluation based on quality data analysis offers numerous benefits to businesses.
Enhanced Product Quality
By utilizing quality data analysis, companies can ensure that their suppliers adhere to high standards.
This focus on quality leads to improved product quality, which enhances customer satisfaction and loyalty.
Cost Savings
Identifying and addressing quality issues early can prevent costly manufacturing errors and product recalls.
Consistent quality control through supplier evaluation results in significant cost savings over time.
Stronger Supplier Relationships
Regularly evaluating and communicating with suppliers about their performance fosters stronger relationships.
These partnerships are built on trust and mutual respect, leading to better collaboration and shared goals.
Competitive Advantage
Companies that maintain high-quality standards differentiate themselves in the marketplace.
Quality products and reliable suppliers provide a competitive edge that attracts and retains customers.
Challenges in Supplier Evaluation
Despite its benefits, supplier evaluation based on quality data analysis can present some challenges.
Understanding these challenges can help businesses navigate them more effectively.
Data Quality
One significant challenge is ensuring the accuracy and completeness of the quality data collected.
Inaccurate or incomplete data can lead to incorrect conclusions and ineffective evaluations.
Complexity
The process of analyzing quality data can be complex and time-consuming.
It requires specialized skills and tools to interpret the data accurately and derive actionable insights.
Supplier Cooperation
Some suppliers may be reluctant to share detailed quality data or may not have robust data collection systems in place.
Achieving transparency and cooperation from suppliers is essential for effective evaluation.
Conclusion
Supplier evaluation based on quality data analysis is an indispensable practice for businesses aiming to maintain high-quality standards.
By focusing on key metrics and following a structured analysis process, companies can derive meaningful insights and make informed decisions regarding supplier management.
While challenges exist, the benefits of enhanced product quality, cost savings, stronger supplier relationships, and a competitive advantage far outweigh the difficulties.
Continuous improvement in supplier evaluation procedures ensures long-term success and sustainability in an increasingly competitive market.
資料ダウンロード
QCD調達購買管理クラウド「newji」は、調達購買部門で必要なQCD管理全てを備えた、現場特化型兼クラウド型の今世紀最高の購買管理システムとなります。
ユーザー登録
調達購買業務の効率化だけでなく、システムを導入することで、コスト削減や製品・資材のステータス可視化のほか、属人化していた購買情報の共有化による内部不正防止や統制にも役立ちます。
NEWJI DX
製造業に特化したデジタルトランスフォーメーション(DX)の実現を目指す請負開発型のコンサルティングサービスです。AI、iPaaS、および先端の技術を駆使して、製造プロセスの効率化、業務効率化、チームワーク強化、コスト削減、品質向上を実現します。このサービスは、製造業の課題を深く理解し、それに対する最適なデジタルソリューションを提供することで、企業が持続的な成長とイノベーションを達成できるようサポートします。
オンライン講座
製造業、主に購買・調達部門にお勤めの方々に向けた情報を配信しております。
新任の方やベテランの方、管理職を対象とした幅広いコンテンツをご用意しております。
お問い合わせ
コストダウンが利益に直結する術だと理解していても、なかなか前に進めることができない状況。そんな時は、newjiのコストダウン自動化機能で大きく利益貢献しよう!
(Β版非公開)