- お役立ち記事
- Supplier evaluation points that management emphasizes and the role of the purchasing department
月間76,176名の
製造業ご担当者様が閲覧しています*
*2025年3月31日現在のGoogle Analyticsのデータより
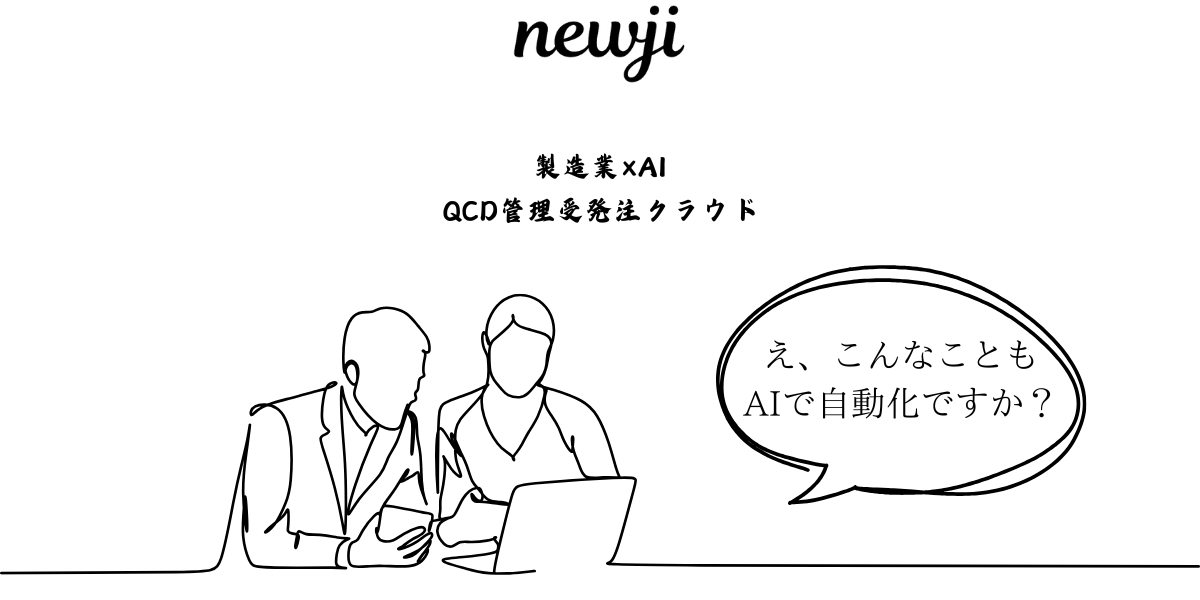
Supplier evaluation points that management emphasizes and the role of the purchasing department
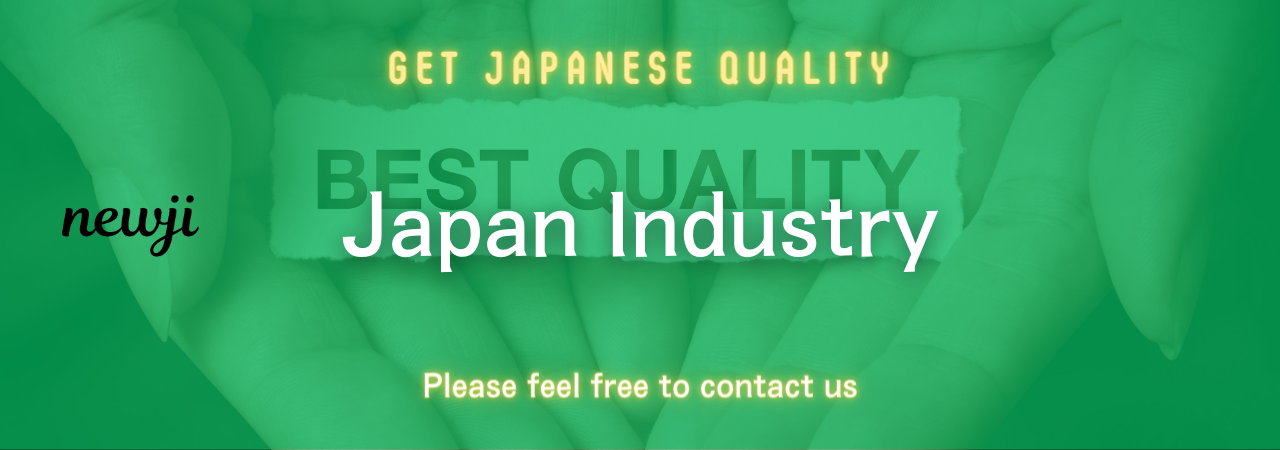
目次
Understanding the Importance of Supplier Evaluation
In the realm of business management, supplier evaluation plays a pivotal role in ensuring success and efficiency.
Suppliers are integral to the supply chain, providing businesses with the raw materials, products, and services necessary to operate smoothly.
Thus, evaluating suppliers effectively is crucial to maintaining operational excellence and meeting organizational goals.
Key Evaluation Points Management Emphasizes
When it comes to supplier evaluation, management focuses on several critical points to assess suppliers effectively.
Quality and Consistency
One of the primary factors management considers is the quality of products or services provided by the supplier.
Consistent quality ensures that the end products meet the company’s standards, enhancing customer satisfaction and reducing returns or complaints.
Reliability
Reliability in delivery schedules and quantities is another key evaluation point.
Suppliers must be dependable to ensure that production processes are not interrupted, which could lead to delays and increased costs.
Cost and Value
While competitive pricing is important, management also looks at the overall value offered by a supplier.
This includes evaluating the total cost of acquisition, such as delivery fees, and the potential for long-term savings.
Financial Stability
A supplier’s financial health is crucial.
Management assesses whether a supplier is financially stable enough to sustain continuous delivery and support business growth.
Innovation and Capability
Suppliers that offer innovative solutions can provide a competitive edge.
Management values suppliers that demonstrate the capability to adapt to new technologies and market trends.
Compliance and Risk Management
Ensuring suppliers adhere to legal and regulatory requirements is vital.
Suppliers must align with environmental, labor, and safety standards to minimize risks.
The Role of the Purchasing Department
Purchasing departments play a significant role in supplier evaluation, acting as the bridge between management and suppliers.
Conducting Supplier Audits
Purchasing departments conduct regular audits to assess supplier performance.
These audits help identify areas for improvement and ensure that suppliers meet the company’s standards.
Negotiating Terms and Agreements
The purchasing department is responsible for negotiating contracts and agreements with suppliers.
They ensure terms are favorable, securing the best pricing, delivery schedules, and payment terms.
Building Supplier Relationships
Maintaining strong relationships with suppliers is crucial for ongoing success.
Purchasing departments cultivate these relationships through effective communication and collaboration, fostering mutual benefits.
Monitoring Supplier Performance
Continuous monitoring of supplier performance ensures that suppliers remain aligned with company requirements.
The purchasing department uses key performance indicators (KPIs) to track reliability, quality, and delivery performance.
Risk Assessment and Management
The purchasing department evaluates potential risks associated with suppliers.
They develop strategies to mitigate these risks, ensuring a resilient supply chain.
Integrating Technology in Supplier Evaluation
Technological advancements have significantly transformed the way supplier evaluations are conducted.
Use of Data Analytics
Data analytics tools help analyze supplier data comprehensively.
This aids in making informed decisions by highlighting trends, patterns, and areas requiring improvement.
Supplier Management Software
Utilizing supplier management software streamlines evaluation processes.
It provides a centralized platform for tracking supplier performance, compliance, and communication.
Automation and Efficiency
Automation in supplier evaluation reduces manual work and errors.
This enhances efficiency and allows the purchasing department to focus on strategic aspects of supplier management.
Conclusion
Supplier evaluation is a fundamental aspect of business management, assuring the quality and reliability of the supply chain.
By understanding key evaluation points and optimizing the role of the purchasing department, businesses can enhance supplier relationships and achieve operational efficiency.
Embracing technology further refines the evaluation process, allowing companies to stay competitive in a dynamic market.
資料ダウンロード
QCD管理受発注クラウド「newji」は、受発注部門で必要なQCD管理全てを備えた、現場特化型兼クラウド型の今世紀最高の受発注管理システムとなります。
ユーザー登録
受発注業務の効率化だけでなく、システムを導入することで、コスト削減や製品・資材のステータス可視化のほか、属人化していた受発注情報の共有化による内部不正防止や統制にも役立ちます。
NEWJI DX
製造業に特化したデジタルトランスフォーメーション(DX)の実現を目指す請負開発型のコンサルティングサービスです。AI、iPaaS、および先端の技術を駆使して、製造プロセスの効率化、業務効率化、チームワーク強化、コスト削減、品質向上を実現します。このサービスは、製造業の課題を深く理解し、それに対する最適なデジタルソリューションを提供することで、企業が持続的な成長とイノベーションを達成できるようサポートします。
製造業ニュース解説
製造業、主に購買・調達部門にお勤めの方々に向けた情報を配信しております。
新任の方やベテランの方、管理職を対象とした幅広いコンテンツをご用意しております。
お問い合わせ
コストダウンが利益に直結する術だと理解していても、なかなか前に進めることができない状況。そんな時は、newjiのコストダウン自動化機能で大きく利益貢献しよう!
(β版非公開)