- お役立ち記事
- Supplier evaluation standards and improvement methods for purchasing departments in manufacturing industries
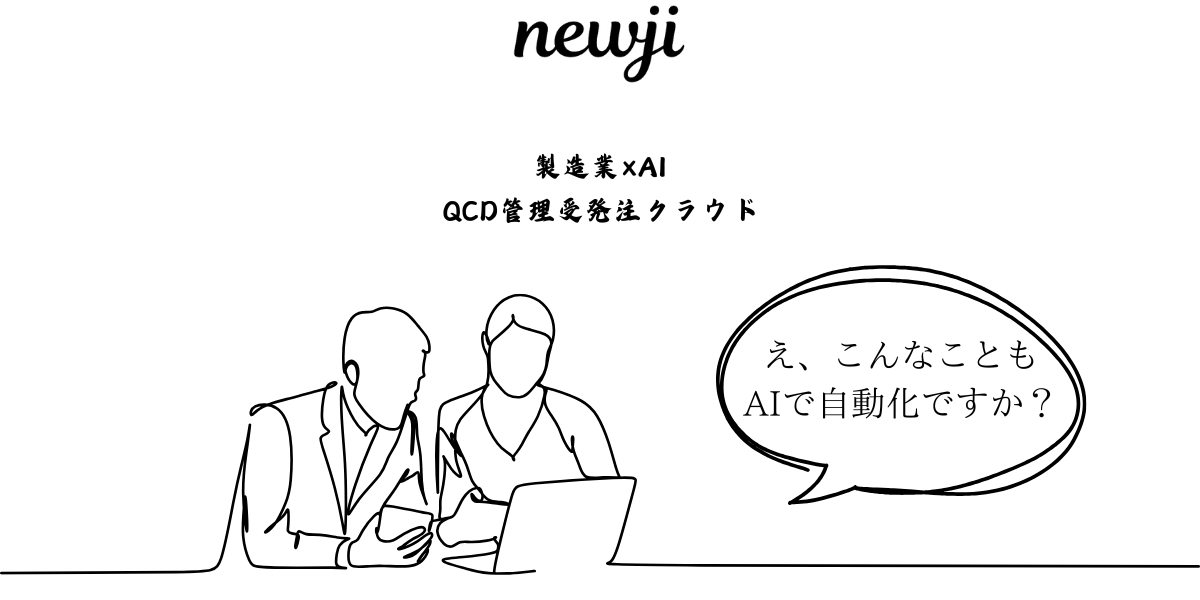
Supplier evaluation standards and improvement methods for purchasing departments in manufacturing industries
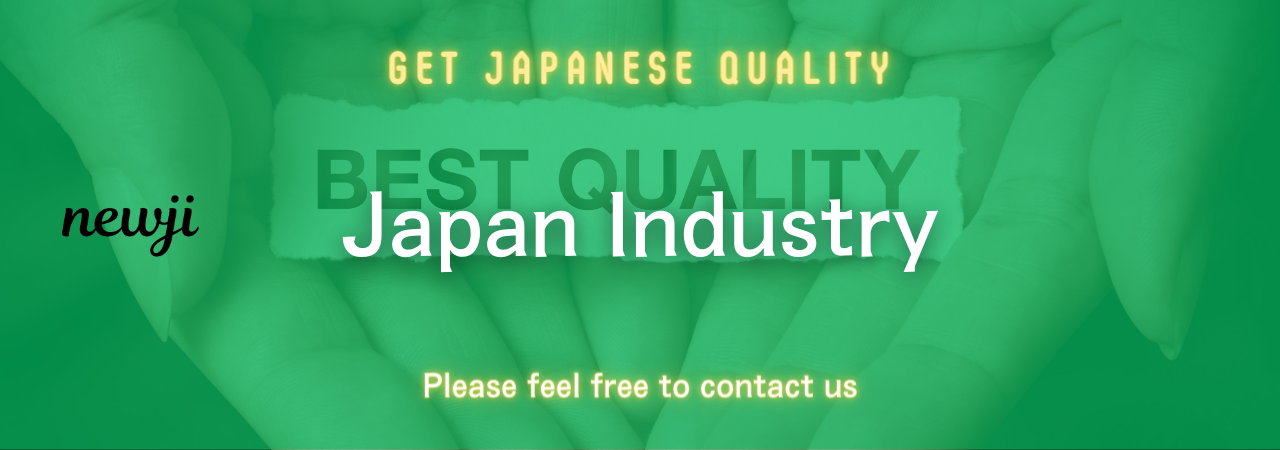
目次
Understanding Supplier Evaluation Standards
In the manufacturing industry, the purchasing department plays a crucial role in determining the success of the entire production process.
Key to this success is the selection and management of suppliers, which is governed by specific evaluation standards.
These standards are essential in assessing suppliers’ ability to meet the needs of the manufacturing process, ensuring quality, cost-efficiency, and reliability.
In this section, we will delve into the fundamental aspects of supplier evaluation standards that purchasing departments must consider.
Quality Assurance
Quality assurance is one of the primary criteria in supplier evaluation.
Manufacturers need to ensure that the goods or materials sourced from suppliers meet the required standards and specifications.
This involves assessing the supplier’s quality control processes, certifications like ISO standards, and their track record for delivering defect-free products.
Consistent delivery of high-quality goods is vital to maintaining the overall product quality and reputation of the manufacturing firm.
Cost Competitiveness
Another critical aspect of supplier evaluation is cost competitiveness.
Manufacturers aim to minimize production costs without compromising on quality.
Purchasing departments must evaluate whether a supplier’s pricing is competitive within the industry and aligns with the company’s budget requirements.
This involves not only looking at the initial cost but also considering additional expenses like shipping, handling, and any potential tariffs or taxes.
Delivery Performance
Timely delivery is essential in manufacturing, where delays can disrupt the entire production schedule.
The evaluation process should include an analysis of the supplier’s delivery performance, including their average lead times and reliability in meeting delivery deadlines.
Suppliers with a history of on-time delivery contribute to smoother operations and reduced downtime in the manufacturing process.
Financial Stability
Financial stability is a crucial factor when evaluating a supplier.
A financially stable supplier is less likely to face disruptions that could affect their ability to deliver goods or services.
Purchasers should assess the supplier’s financial health, looking at factors such as credit ratings, financial statements, and market reputation.
A reliable supplier is one that will continue to operate efficiently even during economic fluctuations.
Methods for Improvement in Supplier Relationships
Once a purchasing department has established evaluation standards, it’s crucial to focus on continuous improvement in supplier relationships.
Effective management and improvement methods can lead to enhanced performance, innovation, and competitive advantage.
Regular Performance Reviews
Conducting regular performance reviews is an effective way to maintain and improve supplier relationships.
These reviews should include qualitative and quantitative assessments of the supplier’s performance against agreed-upon metrics.
Open communication during these reviews helps identify areas needing improvement and fosters a collaborative approach to problem-solving.
Collaborative Partnerships
Building collaborative partnerships with suppliers goes beyond traditional transactional relationships.
By working closely together, manufacturers and suppliers can achieve mutual benefits such as shared innovation, risk management, and cost reductions.
Encouraging collaboration can lead to the development of customized solutions that enhance product quality and efficiency.
Technology Integration
Integrating technology into supplier management processes can significantly improve communication and performance tracking.
Utilizing digital tools like supplier management software allows purchasing departments to streamline operations, reduce manual errors, and obtain real-time data for better decision-making.
Technology helps in creating a transparent supply chain and improves the accuracy of performance evaluations.
Supplier Development Programs
Implementing supplier development programs can enhance the capabilities and performance of existing suppliers.
These programs may include training, mentorship, sharing industry best practices, and co-investment in technological advancements.
By investing in supplier development, manufacturers can secure a more responsive and innovative supply base that aligns with their strategic goals.
Conclusion
In conclusion, supplier evaluation standards are an integral part of the purchasing process in the manufacturing industry.
These standards ensure that suppliers meet quality, cost, delivery, and reliability expectations.
By focusing on continuous improvement and fostering strong relationships through regular reviews, collaboration, technology integration, and development programs, purchasing departments can enhance supplier performance and drive better business outcomes.
The ability to adapt and improve supplier management practices will ultimately contribute to a more efficient, competitive, and resilient manufacturing process.
資料ダウンロード
QCD調達購買管理クラウド「newji」は、調達購買部門で必要なQCD管理全てを備えた、現場特化型兼クラウド型の今世紀最高の購買管理システムとなります。
ユーザー登録
調達購買業務の効率化だけでなく、システムを導入することで、コスト削減や製品・資材のステータス可視化のほか、属人化していた購買情報の共有化による内部不正防止や統制にも役立ちます。
NEWJI DX
製造業に特化したデジタルトランスフォーメーション(DX)の実現を目指す請負開発型のコンサルティングサービスです。AI、iPaaS、および先端の技術を駆使して、製造プロセスの効率化、業務効率化、チームワーク強化、コスト削減、品質向上を実現します。このサービスは、製造業の課題を深く理解し、それに対する最適なデジタルソリューションを提供することで、企業が持続的な成長とイノベーションを達成できるようサポートします。
オンライン講座
製造業、主に購買・調達部門にお勤めの方々に向けた情報を配信しております。
新任の方やベテランの方、管理職を対象とした幅広いコンテンツをご用意しております。
お問い合わせ
コストダウンが利益に直結する術だと理解していても、なかなか前に進めることができない状況。そんな時は、newjiのコストダウン自動化機能で大きく利益貢献しよう!
(Β版非公開)