- お役立ち記事
- Supplier management for reducing defective products by procurement departments in the electronic parts industry
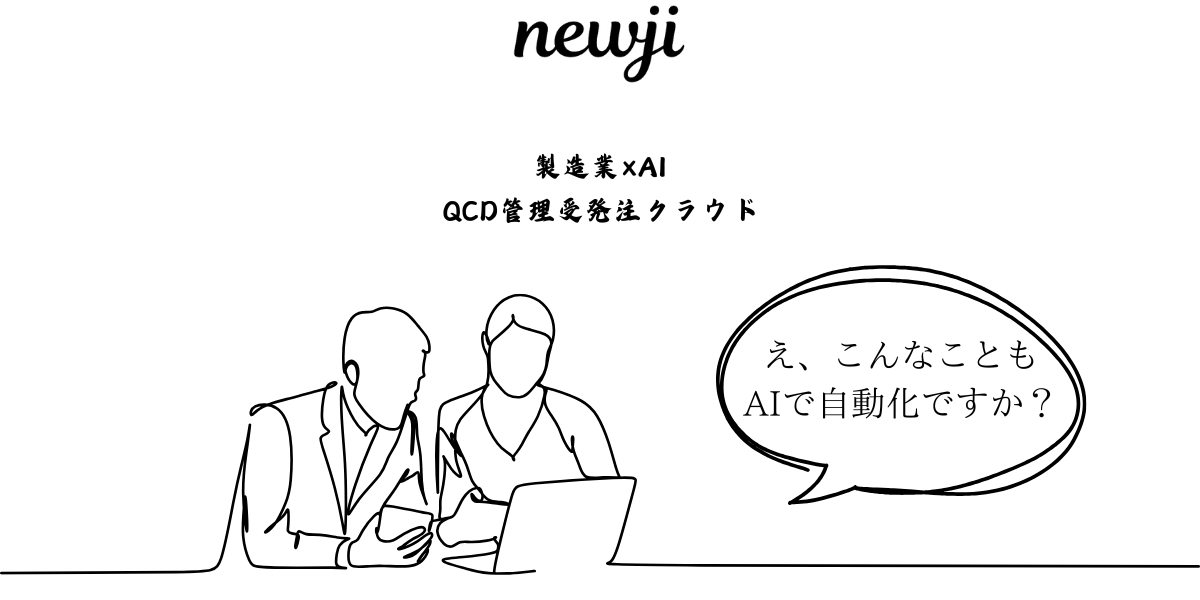
Supplier management for reducing defective products by procurement departments in the electronic parts industry
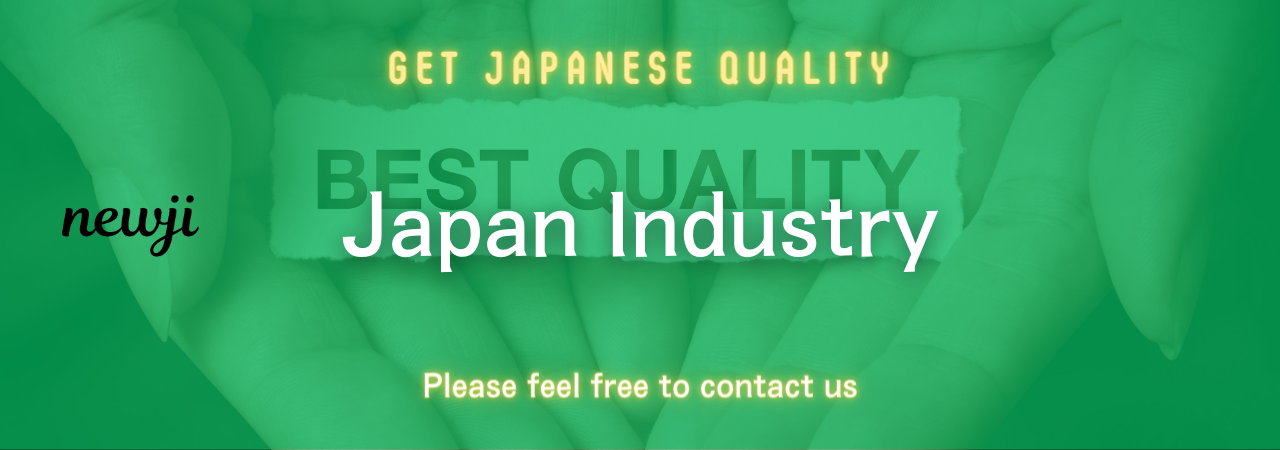
目次
Understanding Supplier Management
Supplier management is a critical aspect of the procurement process, especially in the electronic parts industry.
It involves the systematic management of vendors who supply goods and services, ensuring they meet predefined specifications and quality standards.
By effectively managing suppliers, companies can reduce the likelihood of defective products reaching the production line or end consumers.
The procurement department plays a pivotal role in supplier management.
It oversees supplier selection, performance evaluation, and relationship management.
This department ensures that suppliers provide materials and components that meet the required quality benchmarks.
The Importance of Supplier Management in the Electronic Parts Industry
In the electronic parts industry, supplier management is vital due to the complex and sensitive nature of the products.
Devices such as smartphones, computers, and other electronics require precise components.
Any defect at the component level can result in product malfunctions or failures.
Therefore, reducing defective products is not only a cost-saving measure but also a means to maintain a company’s reputation.
A well-managed supplier network ensures a steady flow of high-quality components.
This reduces delays and disruptions in the manufacturing process, enhancing overall productivity and efficiency.
Steps in Effective Supplier Management
1. Supplier Selection
The selection of the right suppliers is the first step towards effective supplier management.
Procurement departments should evaluate potential suppliers based on their ability to meet quality standards, pricing, reliability, and delivery capabilities.
Conducting a thorough assessment of the supplier’s capacity and production systems is essential to ensure they can consistently meet demands.
2. Establishing Clear Quality Standards
Once suppliers are selected, it is crucial to establish clear quality standards and expectations.
These standards should be documented and communicated to all suppliers to ensure they are aware of the criteria they must meet.
Regularly updated specifications help maintain consistency and quality across the board.
3. Performance Monitoring and Evaluation
Continuous monitoring and evaluation of supplier performance is vital.
The procurement department should establish key performance indicators (KPIs) to measure supplier effectiveness.
This could include metrics such as defect rates, delivery times, and compliance with specifications.
Regular audits and visits to supplier facilities can provide insights into their operations and highlight areas for improvement.
4. Building Strong Relationships
Building strong, collaborative relationships with suppliers is beneficial.
Open lines of communication facilitate the quick resolution of issues and foster a sense of partnership.
By involving suppliers in the planning process and sharing forecasts, companies can enhance cooperation and trust.
This often leads to improved performance and innovation in product development.
5. Implementing Corrective Actions
When defects or discrepancies are identified, it is essential to implement corrective actions promptly.
This involves working closely with the supplier to identify the root cause of the problem and developing strategies to prevent recurrence.
Corrective actions might include adjusting production processes, training employees, or even redesigning components.
Benefits of Effective Supplier Management
Effective supplier management brings numerous benefits to a company, particularly in the electronic parts industry.
1. Enhanced Product Quality
By reducing defects at the source, companies can ensure that their products meet high-quality standards.
This results in fewer returns, better customer satisfaction, and less rework, which saves costs and time.
2. Cost Savings
Managing suppliers effectively can lead to significant cost savings.
By minimizing defects and disruptions, companies can reduce production costs and avoid potential penalties associated with low-quality products.
3. Improved Supply Chain Efficiency
A robust supplier management system ensures reliable delivery schedules and reduces supply chain disruptions.
This strengthens the entire production process and aids in timely product launches.
4. Competitive Advantage
Companies that manage their suppliers well can achieve a significant competitive advantage.
By ensuring high-quality products and maintaining efficient operations, they can differentiate themselves from competitors.
Challenges in Supplier Management
Despite its importance, supplier management comes with several challenges.
1. Communication Barriers
Language and cultural differences can lead to misunderstandings when dealing with international suppliers.
Clear and regular communication is necessary to overcome these barriers.
2. Maintaining Quality Standards
Ensuring consistent quality from suppliers can be challenging.
It requires regular monitoring and a proactive approach to problem-solving.
3. Managing Costs
Balancing quality and cost is a common challenge.
While cheaper suppliers might be attractive, they may not always deliver the expected quality, leading to long-term losses.
Conclusion
Supplier management is a key strategy for reducing defective products in the electronic parts industry.
By selecting the right suppliers, establishing quality standards, and fostering strong relationships, procurement departments can enhance product quality and operational efficiency.
Although challenges exist, the benefits of effective supplier management far outweigh the difficulties.
Such management not only ensures product quality but also promotes cost savings, supply chain efficiency, and competitive advantage.
Organizations that prioritize strategic supplier management will likely thrive in the dynamic electronic parts market.
資料ダウンロード
QCD調達購買管理クラウド「newji」は、調達購買部門で必要なQCD管理全てを備えた、現場特化型兼クラウド型の今世紀最高の購買管理システムとなります。
ユーザー登録
調達購買業務の効率化だけでなく、システムを導入することで、コスト削減や製品・資材のステータス可視化のほか、属人化していた購買情報の共有化による内部不正防止や統制にも役立ちます。
NEWJI DX
製造業に特化したデジタルトランスフォーメーション(DX)の実現を目指す請負開発型のコンサルティングサービスです。AI、iPaaS、および先端の技術を駆使して、製造プロセスの効率化、業務効率化、チームワーク強化、コスト削減、品質向上を実現します。このサービスは、製造業の課題を深く理解し、それに対する最適なデジタルソリューションを提供することで、企業が持続的な成長とイノベーションを達成できるようサポートします。
オンライン講座
製造業、主に購買・調達部門にお勤めの方々に向けた情報を配信しております。
新任の方やベテランの方、管理職を対象とした幅広いコンテンツをご用意しております。
お問い合わせ
コストダウンが利益に直結する術だと理解していても、なかなか前に進めることができない状況。そんな時は、newjiのコストダウン自動化機能で大きく利益貢献しよう!
(Β版非公開)