- お役立ち記事
- Supplier management framework to prevent quality problems: Practical guide for purchasing departments
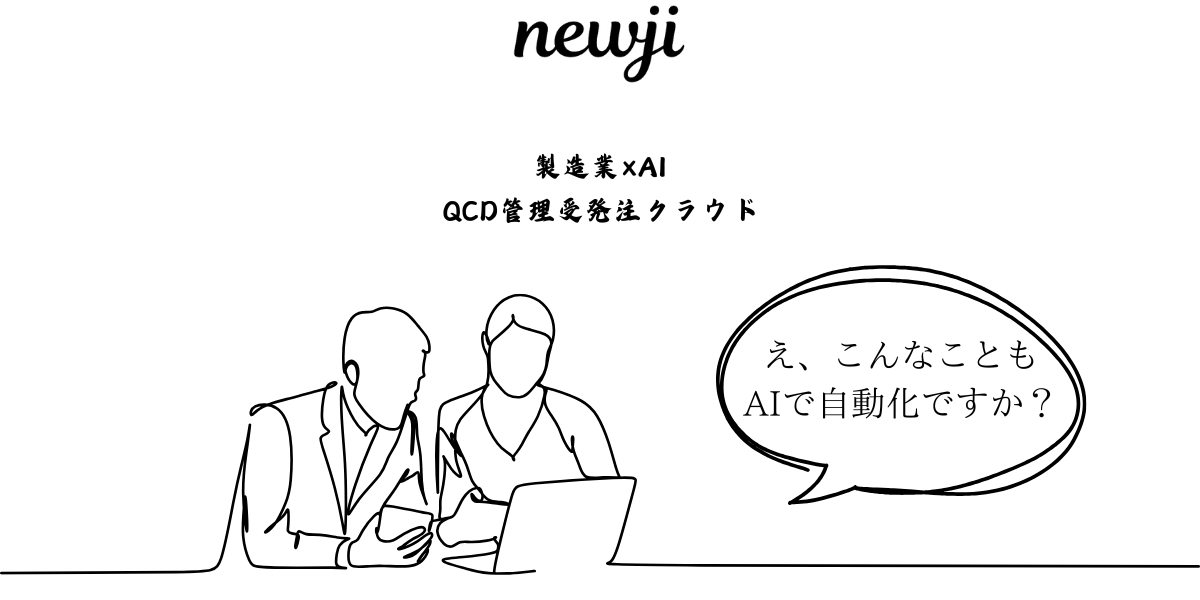
Supplier management framework to prevent quality problems: Practical guide for purchasing departments
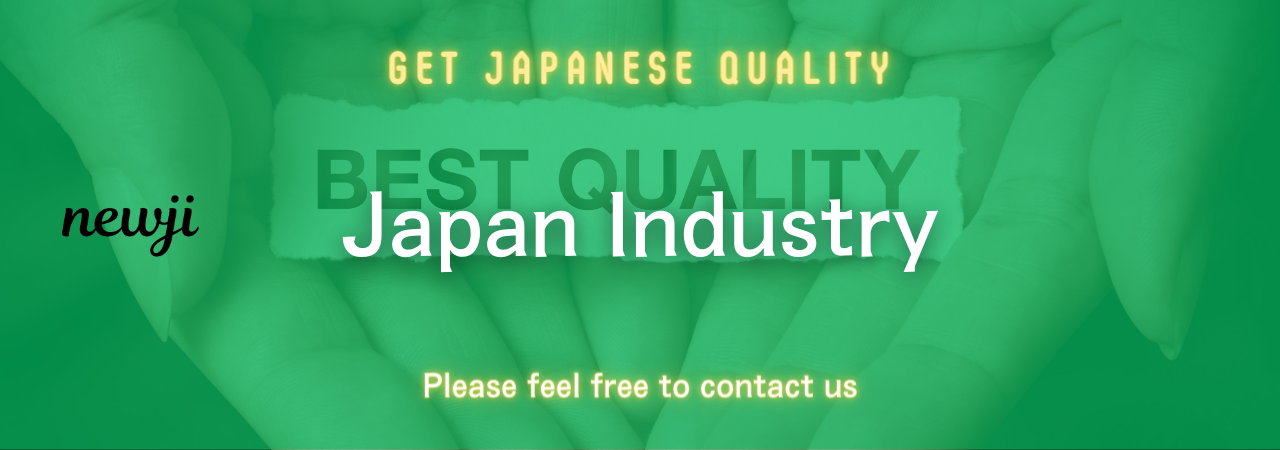
目次
Understanding Supplier Management
Supplier management is a critical process that involves managing relationships with third-party vendors that supply goods or services to an organization.
It centers on developing a robust framework to ensure that the procurement process is efficient, cost-effective, and produces high-quality outputs.
Without a proper supplier management framework, companies may face a myriad of challenges, including supply chain disruptions, increased costs, and compromised product quality.
For purchasing departments, setting up an effective supplier management system is essential to avoiding these pitfalls and maintaining a competitive edge in the market.
The Importance of a Supplier Management Framework
A well-structured supplier management framework provides a systematic approach to evaluating, selecting, and monitoring suppliers.
This framework ensures that suppliers consistently deliver goods and services that meet the company’s quality standards.
Moreover, a strong framework helps foster long-term relationships with suppliers, facilitating better collaboration and mutual growth.
An effective supplier management system can also lead to improved cost efficiency, reduced risks, and enhanced innovation.
By developing clear guidelines and expectations, companies can better control their procurement activities and prevent quality issues before they arise.
Building Blocks of a Supplier Management Framework
Developing a supplier management framework involves several key components aimed at creating a sustainable procurement strategy.
The following are the critical building blocks:
Supplier Evaluation and Selection
The process begins with evaluating potential suppliers to assess their ability to meet the company’s requirements.
Evaluations should consider factors such as financial stability, production capacity, quality systems, and industry reputation.
Selection criteria should be clearly defined to ensure suppliers align with the company’s strategic goals and quality standards.
Supplier Relationship Management
Once suppliers are selected, managing the relationship is crucial.
This involves clear communication, establishing trust, and fostering collaboration.
Regular meetings and performance reviews help in addressing concerns and enhancing the supplier’s contribution to the company.
Performance Monitoring and Assessment
Creating performance metrics is essential for monitoring supplier activities.
Key performance indicators (KPIs) related to quality, delivery times, and cost control should be tracked consistently.
Regular assessments enable purchasing departments to identify issues quickly and implement corrective actions.
Risk Management
Risk management involves identifying potential risks in the supply chain and developing strategies to mitigate them.
This could include diversifying the supplier base, implementing contingency plans, or developing alternative sourcing options.
Continuous Improvement
Encourage suppliers to engage in continuous improvement initiatives.
This could involve adopting new technologies, streamlining processes, or enhancing their quality control systems.
A commitment to continuous improvement helps suppliers remain competitive and contributes to better overall quality.
Best Practices for Purchasing Departments
Purchasing departments play a pivotal role in supplier management.
Here are some best practices they can implement to enhance their supplier management framework:
Develop Clear Contracts
Contracts should clearly outline expectations, responsibilities, and deliverables for both parties.
Include specific quality standards, delivery schedules, and payment terms to minimize misunderstandings and disputes.
Invest in Supplier Development
Investing in supplier development programs can enhance their capabilities and align them with your company’s standards.
Providing training, sharing technology, or extending support can boost supplier performance and loyalty.
Use Technology to Your Advantage
Leverage technology to streamline supplier management processes.
Supplier management software can automate tasks, making it easier to track performance, manage contracts, and communicate effectively.
Conduct Regular Audits
Regular audits help ensure compliance with established standards.
Audits can be used to verify and validate supplier practices, thereby identifying areas for improvement and preventing quality problems.
Build Collaborative Relationships
Focus on building partnerships rather than transactional relationships.
Collaborative relationships enable better information sharing, problem-solving, and innovation, leading to improved quality and efficiency.
Challenges in Supplier Management
Building and maintaining a supplier management framework is not without its challenges.
Some common obstacles include:
Changing Market Conditions
Suppliers may face disruptions due to changes in market conditions, affecting their ability to meet contract terms.
It’s vital to have adaptable strategies to mitigate these impacts.
Communication Barriers
Effective communication is often hindered by differences in language, culture, or technical terms.
Purchasing departments should ensure clear and consistent communication channels with suppliers.
Compliance and Regulatory Issues
Suppliers must comply with various regulations and standards.
Failure to do so can result in legal ramifications and damage the company’s reputation.
Supplier Reliability and Loyalty
Maintaining supplier reliability and loyalty can be challenging.
Building trust through transparent interactions and fair dealings can help foster more dependable relationships.
Conclusion
A comprehensive supplier management framework is a cornerstone of successful business operations, especially for purchasing departments aiming to avert quality issues.
By focusing on supplier evaluation, relationship management, performance monitoring, risk management, and continuous improvement, companies can bolster their supply chain’s resilience and effectiveness.
Implementing best practices and overcoming challenges are crucial steps toward establishing a robust procurement strategy.
Ultimately, investing in a strong supplier management framework leads to enhanced product quality, reduced costs, and sustained business growth.
資料ダウンロード
QCD調達購買管理クラウド「newji」は、調達購買部門で必要なQCD管理全てを備えた、現場特化型兼クラウド型の今世紀最高の購買管理システムとなります。
ユーザー登録
調達購買業務の効率化だけでなく、システムを導入することで、コスト削減や製品・資材のステータス可視化のほか、属人化していた購買情報の共有化による内部不正防止や統制にも役立ちます。
NEWJI DX
製造業に特化したデジタルトランスフォーメーション(DX)の実現を目指す請負開発型のコンサルティングサービスです。AI、iPaaS、および先端の技術を駆使して、製造プロセスの効率化、業務効率化、チームワーク強化、コスト削減、品質向上を実現します。このサービスは、製造業の課題を深く理解し、それに対する最適なデジタルソリューションを提供することで、企業が持続的な成長とイノベーションを達成できるようサポートします。
オンライン講座
製造業、主に購買・調達部門にお勤めの方々に向けた情報を配信しております。
新任の方やベテランの方、管理職を対象とした幅広いコンテンツをご用意しております。
お問い合わせ
コストダウンが利益に直結する術だと理解していても、なかなか前に進めることができない状況。そんな時は、newjiのコストダウン自動化機能で大きく利益貢献しよう!
(Β版非公開)