- お役立ち記事
- Supplier management methods for procurement departments to prevent delivery delays of processed goods
Supplier management methods for procurement departments to prevent delivery delays of processed goods
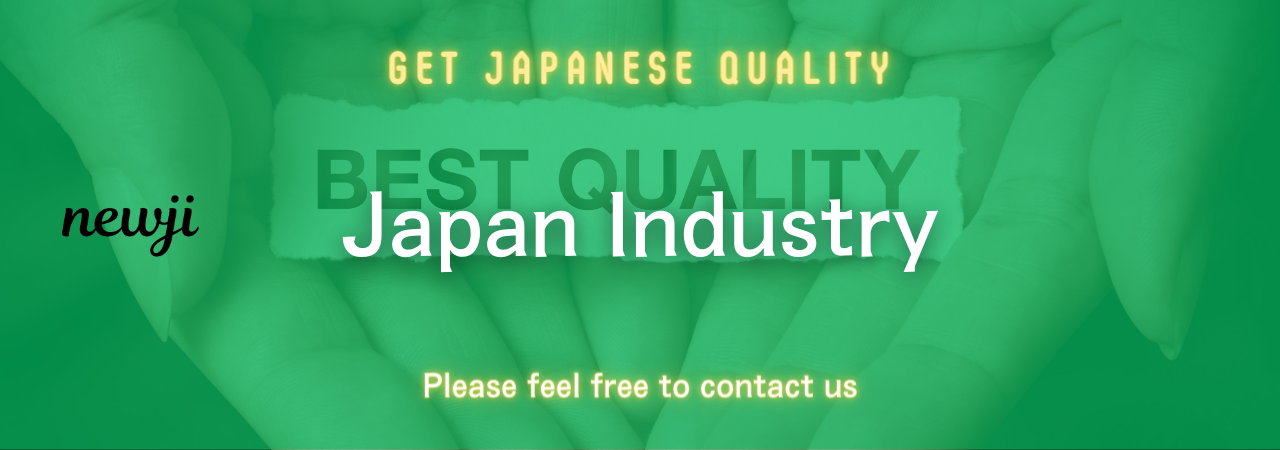
Effective supplier management is crucial for procurement departments to ensure the timely delivery of processed goods.
Delivery delays can disrupt production schedules and affect customer satisfaction.
By implementing robust supplier management methods, procurement teams can minimize risks and maintain smooth operations.
目次
Selecting Reliable Suppliers
One of the first steps to prevent delivery delays is selecting reliable suppliers.
Begin by thoroughly researching potential suppliers.
Look for reputable companies with proven track records.
Check their history of meeting deadlines, quality standards, and other key performance indicators.
It’s also a good idea to ask for references.
Speak with other businesses that have worked with the supplier to get an idea of their reliability.
Review any available performance data, such as recent delivery times.
Negotiating Clear Terms
Once you have selected your suppliers, make sure to negotiate clear terms and conditions.
These should specify delivery schedules, payment terms, and quality requirements.
Clear agreements prevent misunderstandings and set the foundation for a successful business relationship.
Ensure that all agreements are documented in a formal contract.
Contracts should include clauses for contingencies, such as penalties for late deliveries.
This provides a legal framework to address issues if they arise.
Regular Communication
Effective communication is essential in supplier management.
Maintain regular contact with your suppliers to stay informed about their operations and any potential issues.
This can be done through emails, phone calls, or regular meetings.
Establishing strong relationships with suppliers can lead to better collaboration.
When suppliers feel valued, they are more likely to prioritize your needs.
Use communication to share forecasts and upcoming demand patterns.
This helps suppliers plan their production and inventory better.
Using Technology
Leverage technology to improve communication and supplier management.
Use procurement software to track orders, manage contracts, and monitor supplier performance.
Automated systems can send alerts for potential delays, allowing you to address issues proactively.
Supplier portals can provide a centralized platform for sharing information.
These can include order details, delivery schedules, and performance metrics.
Such platforms make it easier for both parties to stay organized and aligned.
Quality Inspections
Inspect the quality of goods upon delivery to ensure they meet your standards.
Regular quality checks help identify issues early and address them before they become major problems.
This is crucial for maintaining the integrity of your supply chain.
Work with suppliers to develop quality control processes.
Encourage them to implement their own inspections before shipping.
This reduces the likelihood of defects and increases overall reliability.
Audits and Evaluations
Conduct regular audits of your suppliers.
Audits help assess their compliance with your terms and their capability to meet your demands.
Evaluations should consider various factors, such as financial stability, production capacity, and overall performance.
These assessments can uncover potential risks and areas for improvement.
Use the findings to develop action plans with suppliers to enhance efficiency and reliability.
Building Contingency Plans
Even with the best plans, unforeseen issues can occur.
Develop contingency plans to manage potential disruptions.
Identify alternative suppliers who can step in if your primary supplier faces difficulties.
Stocking safety inventory can also mitigate risks.
Having a buffer stock ensures that you can continue operations while resolving supply chain issues.
Regularly review and update contingency plans to adapt to changing circumstances.
Performance Monitoring
Consistently monitor supplier performance using key performance indicators (KPIs).
KPIs can include delivery times, order accuracy, and quality metrics.
Regularly review these indicators to track trends and identify any performance declines.
Supplier scorecards are useful tools for these evaluations.
They provide a visual representation of a supplier’s performance over time.
Discuss these evaluations with suppliers to set improvement goals.
Training and Development
Invest in training and development for your procurement team and suppliers.
Training helps your team understand best practices in supplier management.
Developing suppliers’ skills enhances their ability to meet your expectations.
Workshops and seminars can provide valuable knowledge on industry standards and advancements.
Encouraging suppliers to participate in these programs fosters a culture of continuous improvement.
Collaborative Problem-Solving
When issues arise, approach them collaboratively.
Work with suppliers to identify root causes and develop effective solutions.
Blaming suppliers can damage relationships; instead, focus on mutual benefit.
Develop joint action plans to address problems and prevent future occurrences.
This collaborative approach strengthens partnerships and promotes long-term success.
Conclusion
Effective supplier management is key to preventing delivery delays of processed goods.
By selecting reliable suppliers, maintaining clear communication, and leveraging technology, procurement departments can enhance reliability.
Regular quality inspections, audits, and performance monitoring ensure standards are met.
Building contingency plans and investing in training prepare teams to handle disruptions.
Collaborative problem-solving fosters strong relationships and continuous improvement.
With these strategies, procurement departments can maintain a smooth and efficient supply chain, ensuring timely delivery and customer satisfaction.
資料ダウンロード
QCD調達購買管理クラウド「newji」は、調達購買部門で必要なQCD管理全てを備えた、現場特化型兼クラウド型の今世紀最高の購買管理システムとなります。
ユーザー登録
調達購買業務の効率化だけでなく、システムを導入することで、コスト削減や製品・資材のステータス可視化のほか、属人化していた購買情報の共有化による内部不正防止や統制にも役立ちます。
NEWJI DX
製造業に特化したデジタルトランスフォーメーション(DX)の実現を目指す請負開発型のコンサルティングサービスです。AI、iPaaS、および先端の技術を駆使して、製造プロセスの効率化、業務効率化、チームワーク強化、コスト削減、品質向上を実現します。このサービスは、製造業の課題を深く理解し、それに対する最適なデジタルソリューションを提供することで、企業が持続的な成長とイノベーションを達成できるようサポートします。
オンライン講座
製造業、主に購買・調達部門にお勤めの方々に向けた情報を配信しております。
新任の方やベテランの方、管理職を対象とした幅広いコンテンツをご用意しております。
お問い合わせ
コストダウンが利益に直結する術だと理解していても、なかなか前に進めることができない状況。そんな時は、newjiのコストダウン自動化機能で大きく利益貢献しよう!
(Β版非公開)