- お役立ち記事
- Supplier risk assessment and management strategies that purchasing department managers should address
Supplier risk assessment and management strategies that purchasing department managers should address
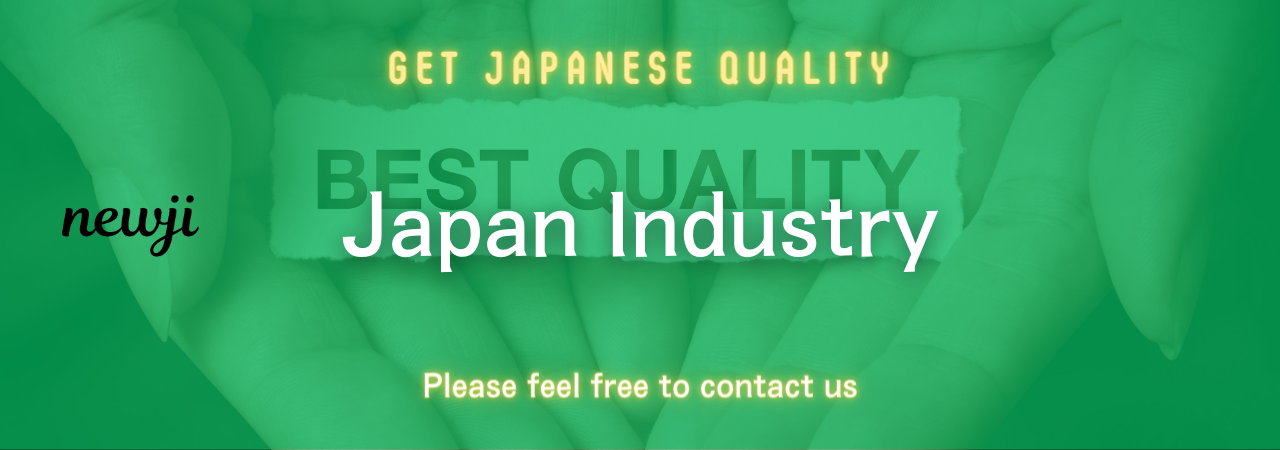
目次
Understanding Supplier Risk Assessment
Managing supplier risk is an essential aspect of procurement and supply chain management.
This involves identifying, assessing, and mitigating risks that could disrupt the supply chain or negatively impact a company’s operations and profitability.
Supplier risk assessment is not just a procurement responsibility but a strategic business imperative.
Identifying Potential Supplier Risks
The first step in supplier risk assessment is identifying potential risks that suppliers might pose.
These risks can stem from several sources, including financial instability, geopolitical issues, environmental concerns, and compliance with laws and regulations.
For instance, a supplier in a politically unstable region might pose a significant geopolitical risk.
Purchasing department managers must be vigilant and proactive in identifying these risks to preempt any adverse impacts on the business.
Evaluating Supplier Financial Stability
Suppliers’ financial health is a critical indicator of their ability to deliver goods and services consistently.
Financial instability can lead to service disruptions, delayed deliveries, or the complete shutdown of supplier operations.
Purchasing managers should regularly evaluate the financial status of their suppliers by examining financial reports, credit ratings, and market performance.
This assessment helps in understanding the supplier’s financial resilience and capacity to withstand economic downturns.
Importance of Supplier Diversification
Supplier diversification is a key strategy in mitigating supplier risks.
Relying excessively on a single supplier or a small group of suppliers can be risky.
If something goes wrong with one supplier, it can have a domino effect on the entire supply chain.
Diversifying the supplier base helps in building a robust and resilient supply chain.
Purchasing managers should aim to work with suppliers from different regions and specializations to ensure business continuity in the face of unforeseen challenges.
Assessing Quality and Reliability
The quality and reliability of a supplier are fundamental to the success of the supply chain.
Substandard goods or unreliable service can lead to production delays, increased costs, and customer dissatisfaction.
To mitigate these risks, purchasing managers must regularly assess the quality and service performance of their suppliers.
This can be done through audits, quality checks, and feedback from production teams to ensure that suppliers meet the required standards consistently.
Evaluating Supplier Compliance
Compliance with legal and regulatory requirements is a significant concern in supplier risk management.
Suppliers must adhere to industry standards and local laws governing labor, safety, and environmental protection.
Non-compliance can lead to legal liabilities, penalties, and reputational damage to the company.
Purchasing managers should ensure that suppliers have adequate policies, certifications, and procedures to comply with these regulations.
Developing Strong Supplier Relationships
Building and maintaining strong relationships with suppliers is crucial for effective supplier risk management.
A solid relationship fosters better communication, collaboration, and trust, which are essential when addressing and mitigating risks.
Purchasing managers should engage in regular dialogue with suppliers, sharing information and aligning goals to create a mutually beneficial partnership.
This proactive approach can lead to early identification and resolution of potential risks.
Implementing Risk Mitigation Strategies
Purchasing department managers should develop and implement risk mitigation strategies tailored to each identified risk.
Strategies could include diversifying the supplier base, negotiating flexible contracts, maintaining safety stock, or investing in alternative suppliers.
It’s crucial for managers to regularly review and update these strategies as market conditions and business needs evolve.
An agile approach to risk management helps companies respond swiftly to changes and maintain supply chain stability.
Technology and Data Analytics in Risk Management
Leveraging technology and data analytics is becoming increasingly important in supplier risk management.
Advanced analytics tools can provide insights into potential risks and trends, helping managers make informed decisions.
These tools can also automate risk monitoring and provide alerts on fluctuations in supplier performance or market conditions.
Integrating technology into the risk management process enhances efficiency and effectiveness, enabling managers to focus on strategic decision-making.
Conclusion
Supplier risk assessment and management is a continuous process that requires diligence and strategic foresight.
By identifying risks, evaluating suppliers’ capabilities, diversifying supply chains, and fostering strong supplier relationships, purchasing department managers can effectively mitigate risks.
Implementing a robust framework for supplier risk management not only protects the company from potential disruptions but also contributes to a competitive advantage in the marketplace.
Adapting and evolving with technological advancements ensures that risk management strategies remain relevant and effective in our ever-changing global economy.
資料ダウンロード
QCD調達購買管理クラウド「newji」は、調達購買部門で必要なQCD管理全てを備えた、現場特化型兼クラウド型の今世紀最高の購買管理システムとなります。
ユーザー登録
調達購買業務の効率化だけでなく、システムを導入することで、コスト削減や製品・資材のステータス可視化のほか、属人化していた購買情報の共有化による内部不正防止や統制にも役立ちます。
NEWJI DX
製造業に特化したデジタルトランスフォーメーション(DX)の実現を目指す請負開発型のコンサルティングサービスです。AI、iPaaS、および先端の技術を駆使して、製造プロセスの効率化、業務効率化、チームワーク強化、コスト削減、品質向上を実現します。このサービスは、製造業の課題を深く理解し、それに対する最適なデジタルソリューションを提供することで、企業が持続的な成長とイノベーションを達成できるようサポートします。
オンライン講座
製造業、主に購買・調達部門にお勤めの方々に向けた情報を配信しております。
新任の方やベテランの方、管理職を対象とした幅広いコンテンツをご用意しております。
お問い合わせ
コストダウンが利益に直結する術だと理解していても、なかなか前に進めることができない状況。そんな時は、newjiのコストダウン自動化機能で大きく利益貢献しよう!
(Β版非公開)