- お役立ち記事
- “Supplier Risk Management” for mid-level employees—practical methods of risk avoidance that purchasing departments should suppress
“Supplier Risk Management” for mid-level employees—practical methods of risk avoidance that purchasing departments should suppress
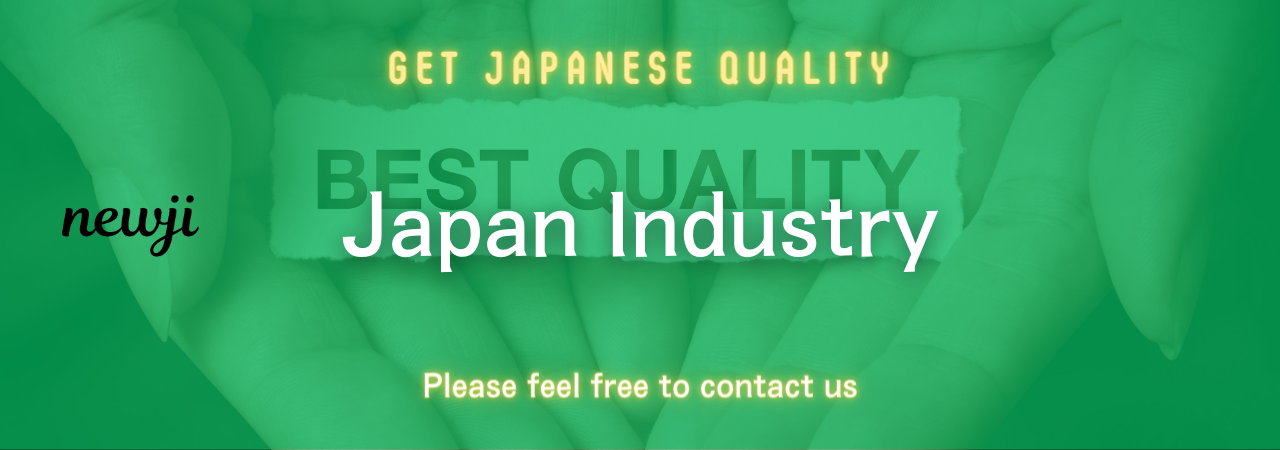
Understanding how to manage supplier risk is crucial for the smooth operation of any purchasing department.
By having a well-thought-out plan, mid-level employees can effectively avoid potential pitfalls and ensure that their company maintains a steady flow of goods and services.
目次
What is Supplier Risk Management?
Supplier risk management involves assessing and mitigating risks associated with a company’s suppliers and their ability to deliver the required goods or services.
These risks can stem from various factors such as financial instability, quality control issues, delivery failures, or even geopolitical events that could disrupt the supply chain.
It’s essential to recognize these risks early on and develop strategies to mitigate them.
Key Components of Supplier Risk Management
1. Identification of Risks
The first step in supplier risk management is identifying potential risks.
This involves analyzing your supply chain to spot vulnerabilities.
For example, if a supplier is located in a region prone to natural disasters or political instability, these factors pose a significant risk.
2. Risk Assessment
After identifying potential risks, assess their likelihood and impact on your business.
Consider both qualitative and quantitative measures to evaluate how each risk can affect your operations.
This assessment will help prioritize which risks require more immediate attention and resource allocation.
3. Risk Mitigation Strategies
Once risks are assessed, develop strategies to mitigate them.
This could involve diversifying your supplier base to not rely too heavily on a single source, investing in technology to improve supply chain visibility, or negotiating better terms with existing suppliers to accommodate potential disruptions.
4. Monitoring and Review
Risk management is an ongoing process.
Regularly monitor your supply chain environment and review your risk management strategies to ensure they remain effective.
Changes in market conditions, supplier performance, or new regulations might require you to adjust your approach.
Practical Methods of Risk Avoidance
As a mid-level employee in the purchasing department, implementing these practical methods can significantly reduce supplier-related risks.
Supplier Evaluation
Before finalizing any contracts, conduct a thorough evaluation of potential suppliers.
This includes financial reviews to ensure they are stable, site visits to assess operations, and reviewing their track record with other clients.
Such evaluations help ascertain a supplier’s capability to meet your quality and delivery requirements.
Building Strong Relationships
Fostering strong relationships with suppliers can lead to better risk management.
Suppliers are more likely to go the extra mile to maintain a good partnership.
Open communication helps in identifying issues early, preventing them from escalating into more significant problems.
Diversification
Avoid relying on a single supplier for crucial materials or services.
Diversify your supplier base to minimize the impact should one fail to deliver.
This redundancy ensures that you can still meet production demands without disruption.
Contractual Safeguards
Incorporate risk-sharing clauses in contracts, such as penalties for late delivery or failure to meet quality standards.
Contracts should also outline clear expectations and procedures for resolving disputes, ensuring that both parties have a mutual understanding of the terms.
Technological Integration
Invest in technology that improves supply chain management, such as real-time tracking systems.
These tools offer better visibility into the supply chain, making it easier to spot potential issues before they affect your business.
Internal Collaboration
Effective supplier risk management requires collaboration across departments.
Cross-Departmental Cooperation
Encourage communication between purchasing, logistics, and quality control teams to identify and address supplier risks.
Sharing insights and data can lead to more informed decision-making and a more cohesive risk management strategy.
Training and Development
Ensure team members are trained in identifying and managing supplier risks.
Regular workshops and seminars can keep everyone updated on best practices and emerging risks, enabling them to respond effectively.
The Importance of Ongoing Evaluation
Performance Metrics
Use key performance indicators (KPIs) to measure supplier performance and risk management success.
KPIs such as on-time delivery rates, defect rates, and order accuracy can provide valuable insights into how well suppliers are performing and where improvements are needed.
Feedback Loops
Establish regular feedback loops with suppliers to foster continuous improvement.
Constructive feedback on areas that need enhancement can strengthen the supplier relationship and improve their performance over time.
Conclusion
Supplier risk management is an integral part of maintaining a robust supply chain.
By understanding supplier risks and implementing practical risk avoidance methods, mid-level employees in purchasing departments can play a vital role in ensuring business continuity.
Developing a proactive risk management strategy, built on strong supplier relationships, diversification, technology, and internal collaboration, will help mitigate risks and sustain a competitive advantage in the marketplace.
Remember, vigilance and adaptability are key components in managing supplier risks effectively.
資料ダウンロード
QCD調達購買管理クラウド「newji」は、調達購買部門で必要なQCD管理全てを備えた、現場特化型兼クラウド型の今世紀最高の購買管理システムとなります。
ユーザー登録
調達購買業務の効率化だけでなく、システムを導入することで、コスト削減や製品・資材のステータス可視化のほか、属人化していた購買情報の共有化による内部不正防止や統制にも役立ちます。
NEWJI DX
製造業に特化したデジタルトランスフォーメーション(DX)の実現を目指す請負開発型のコンサルティングサービスです。AI、iPaaS、および先端の技術を駆使して、製造プロセスの効率化、業務効率化、チームワーク強化、コスト削減、品質向上を実現します。このサービスは、製造業の課題を深く理解し、それに対する最適なデジタルソリューションを提供することで、企業が持続的な成長とイノベーションを達成できるようサポートします。
オンライン講座
製造業、主に購買・調達部門にお勤めの方々に向けた情報を配信しております。
新任の方やベテランの方、管理職を対象とした幅広いコンテンツをご用意しております。
お問い合わせ
コストダウンが利益に直結する術だと理解していても、なかなか前に進めることができない状況。そんな時は、newjiのコストダウン自動化機能で大きく利益貢献しよう!
(Β版非公開)