- お役立ち記事
- Supplier Selection Based on Material Testing and Results
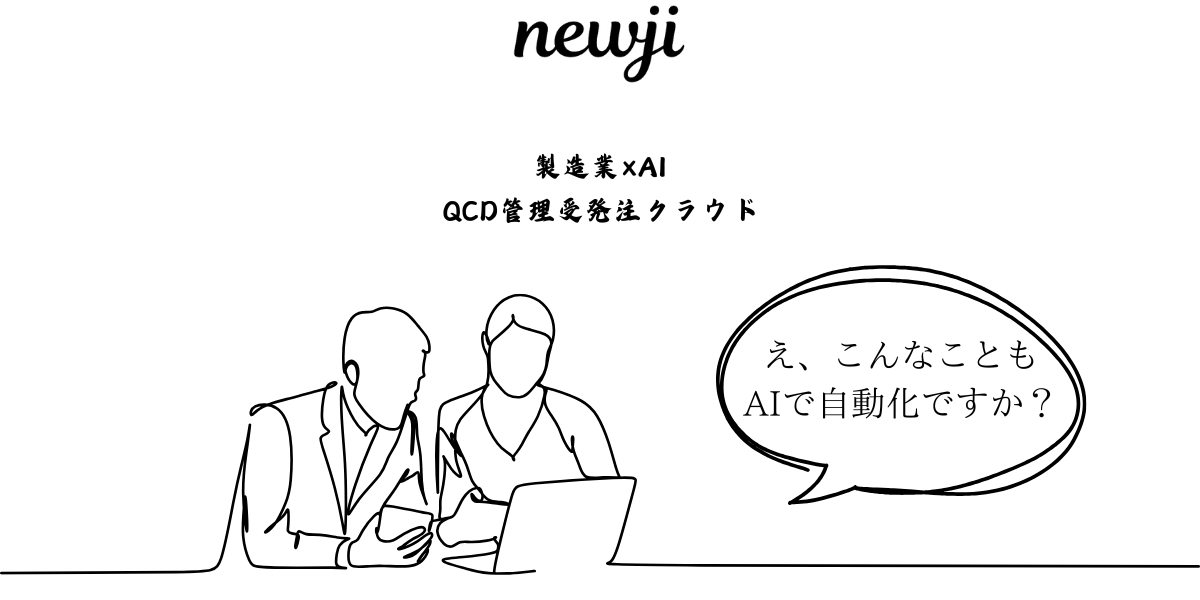
Supplier Selection Based on Material Testing and Results
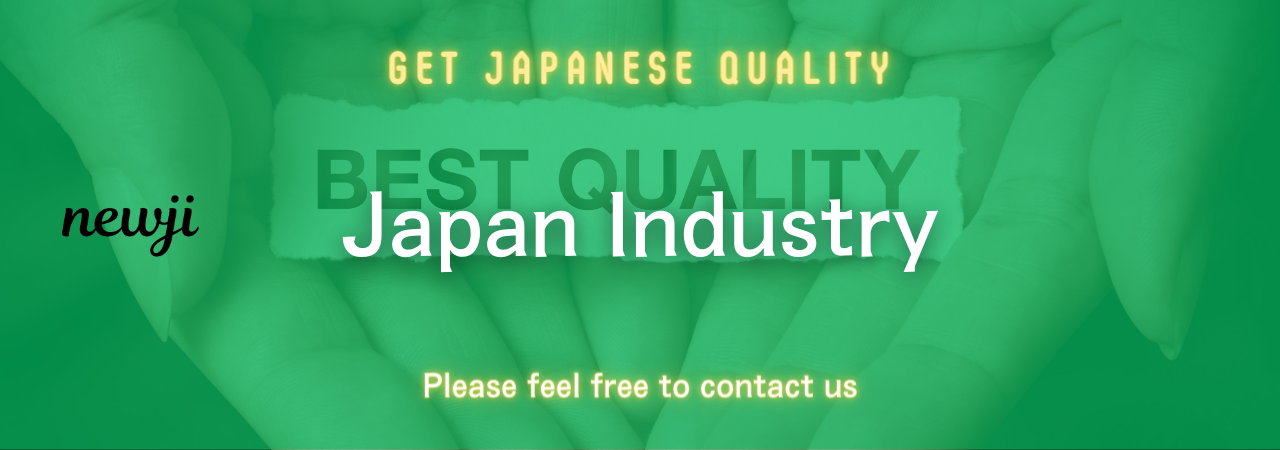
Selecting a supplier for your business is a crucial decision that can impact the quality and reliability of your products.
Especially when dealing with raw materials, thorough testing and evaluations are essential to ensure that you are making the right choice.
In this post, we will explore the significant steps in supplier selection based on material testing and results.
Let’s delve into the details to understand how to make informed and well-founded decisions.
目次
Why Material Testing is Important
When selecting a supplier, material testing ensures that the raw materials provided meet the required standards and specifications.
Quality assurance is paramount, as it directly affects the end product.
Inconsistent or substandard materials can lead to product failures, customer dissatisfaction, and potential recalls.
Material testing provides valuable data that helps in making informed decisions and minimizes any risk associated with the materials.
Types of Material Testing
There are various types of material testing techniques used in different industries.
Some common types include:
1. Mechanical Testing
Mechanical testing involves evaluating the physical properties of materials.
This can include tensile strength, hardness, and impact resistance.
These tests help determine how materials will perform under different conditions and forces.
2. Chemical Testing
Chemical testing examines the composition of materials.
It helps in identifying the presence of any harmful substances or contaminants.
Chemical testing is crucial for industries like pharmaceuticals, where purity is essential.
3. Thermal Testing
Thermal testing assesses how materials respond to heat.
This can include measuring melting points, thermal conductivity, and heat resistance.
It’s important for industries like electronics and aerospace, where materials are exposed to high temperatures.
4. Electrical Testing
Electrical testing evaluates the conductivity and insulation properties of materials.
This is particularly relevant for the electronics and energy sectors, where reliable electrical performance is critical.
Steps in Supplier Selection
Once the importance of material testing is understood, the next step involves the actual selection of a supplier.
Here are the key steps involved in the process:
1. Define Requirements
Start by clearly defining your material requirements.
Specify the properties you need, the acceptable standards, and any regulatory compliances that should be met.
This will serve as a guideline for both the testing process and supplier evaluation.
2. Identify Potential Suppliers
Search for suppliers who can provide the required materials and are reputed in the industry.
You can look for recommendations, search online directories, and attend trade shows to find potential suppliers.
Shortlist a few suppliers who seem promising based on their capabilities and reputation.
3. Initial Screening
Perform an initial screening of the shortlisted suppliers.
This can include reviewing their certifications, previous customer feedback, and visiting their production facilities if possible.
This helps in getting a preliminary understanding of their reliability and competency.
4. Request for Samples
Ask the shortlisted suppliers to provide samples of the materials you need.
These samples will be subjected to rigorous testing to evaluate their quality and suitability.
5. Conduct Material Testing
Perform the necessary material testing on the samples received.
This will include mechanical, chemical, thermal, and electrical testing as required.
Document the results meticulously to compare them against your defined requirements.
6. Compare Results
Compare the test results of the different suppliers.
Look for consistency in quality and ensure that the materials meet your standards and requirements.
Consider not only the test results but also the supplier’s willingness to comply with your needs and their customer service approach.
7. Negotiate Terms
Once you have identified a supplier whose materials meet your requirements, negotiations begin.
Discuss pricing, delivery schedules, and terms of quality assurance.
Make sure that the supplier is willing to provide ongoing support and stands by the quality of their materials.
8. Monitor and Review
After selecting the supplier and starting the procurement process, it’s crucial to continuously monitor the quality of materials received.
This not only ensures ongoing quality but also helps in building a solid relationship with the supplier.
Regular reviews and feedback can lead to improvements and long-term benefits.
Conclusion
Selecting a supplier based on material testing and results is a thorough process that demands attention to detail and precision.
By following the steps outlined above, businesses can ensure that they are partnering with reliable suppliers who provide high-quality materials.
Material testing serves as a protective measure against potential risks and paves the way for a successful and productive partnership.
Remember, the quality of your end product essentially begins with the quality of the materials you use.
資料ダウンロード
QCD調達購買管理クラウド「newji」は、調達購買部門で必要なQCD管理全てを備えた、現場特化型兼クラウド型の今世紀最高の購買管理システムとなります。
ユーザー登録
調達購買業務の効率化だけでなく、システムを導入することで、コスト削減や製品・資材のステータス可視化のほか、属人化していた購買情報の共有化による内部不正防止や統制にも役立ちます。
NEWJI DX
製造業に特化したデジタルトランスフォーメーション(DX)の実現を目指す請負開発型のコンサルティングサービスです。AI、iPaaS、および先端の技術を駆使して、製造プロセスの効率化、業務効率化、チームワーク強化、コスト削減、品質向上を実現します。このサービスは、製造業の課題を深く理解し、それに対する最適なデジタルソリューションを提供することで、企業が持続的な成長とイノベーションを達成できるようサポートします。
オンライン講座
製造業、主に購買・調達部門にお勤めの方々に向けた情報を配信しております。
新任の方やベテランの方、管理職を対象とした幅広いコンテンツをご用意しております。
お問い合わせ
コストダウンが利益に直結する術だと理解していても、なかなか前に進めることができない状況。そんな時は、newjiのコストダウン自動化機能で大きく利益貢献しよう!
(Β版非公開)