- お役立ち記事
- Supplier selection criteria for purchasing departments to increase material supply flexibility
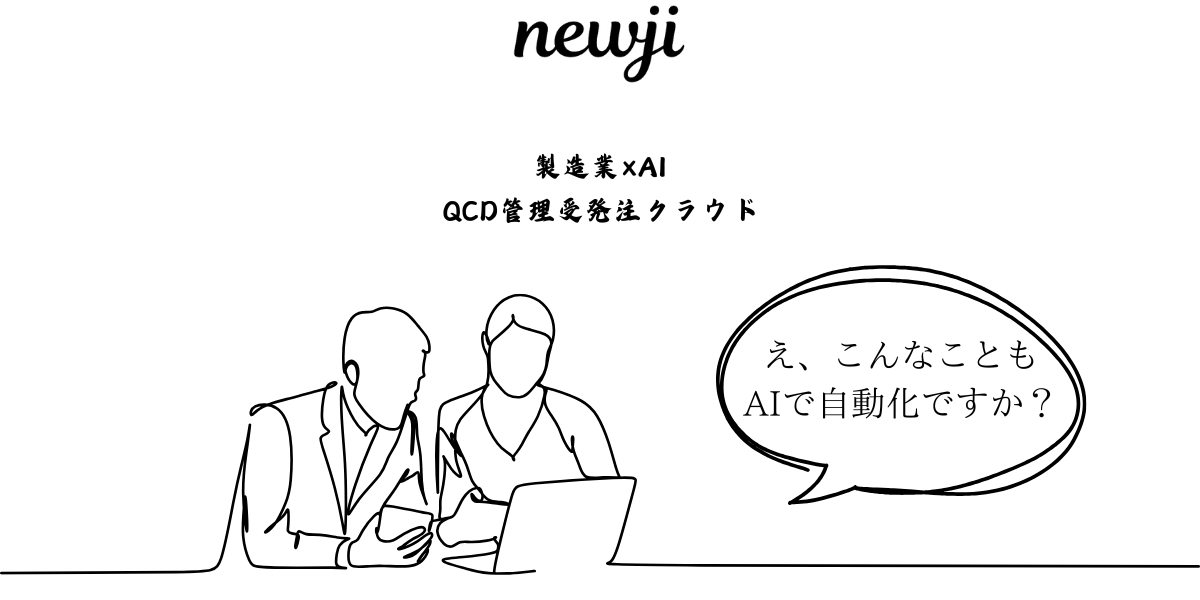
Supplier selection criteria for purchasing departments to increase material supply flexibility
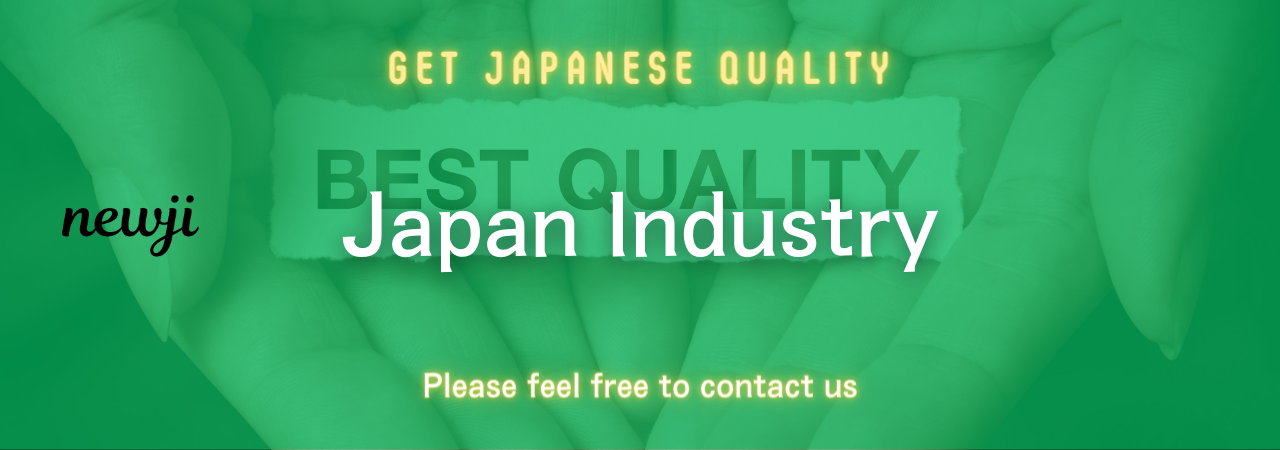
目次
Understanding the Importance of Supplier Selection
For purchasing departments, choosing the right suppliers is crucial to maintaining a reliable and flexible supply chain.
The ability to adapt to changing circumstances and meet the demands of production often depends on the suppliers that companies select.
Ensuring material supply flexibility requires a careful evaluation of potential partners.
This article will explore the key criteria that purchasing departments should consider when selecting suppliers to enhance material supply flexibility.
Quality and Consistency
One of the first factors purchasing departments must assess is the quality of materials provided by a supplier.
High-quality materials ensure the production of reliable and consistent products.
Therefore, selecting suppliers known for providing excellent quality should be a priority.
Moreover, consistency in the quality of supplies can prevent production delays and ensure customer satisfaction.
Evaluating a supplier’s quality control processes can provide insight into their ability to maintain high standards.
Potential buyers should inquire about certifications, industry standards compliance, and any quality assurance programs the supplier participates in.
Pricing and Cost Management
Cost considerations are always significant in supplier selection.
While purchasing departments aim to secure cost-effective deals, it is important not to sacrifice quality for price.
An ideal supplier should offer competitive pricing without compromising the quality and reliability of materials.
It is beneficial for companies to have a clear understanding of their budget constraints and cost priorities.
Negotiating favorable payment terms, such as discounts for early payments or bulk purchases, can also improve cost efficiency.
Additionally, understanding the total cost of acquisition, which includes transportation, taxes, and potential tariffs, can provide a better picture of the financial implications.
Capacity and Reliability
A supplier’s ability to meet demand consistently without delays is another crucial factor.
Assessing a supplier’s production capacity can help determine if they can handle increased orders or sudden demand spikes.
Capacity issues during high-demand periods can lead to supply chain disruptions and impact the company’s operations.
Reliability also involves timely delivery and adherence to agreed-upon schedules.
Delays in receiving materials can halt production lines and lead to financial losses.
Therefore, checking a supplier’s track record for on-time deliveries can help evaluate their reliability.
Flexibility and Adaptability
In today’s fast-paced business environment, flexibility is key.
A supplier must be able to adapt to changing demands and specifications quickly.
Having suppliers who can modify order quantities or delivery schedules as needed can greatly enhance material supply flexibility.
Additionally, adaptability in terms of product development and customization can benefit businesses that require specialized materials.
Suppliers who are open to collaborating on innovative solutions can provide a competitive advantage.
Communication and Customer Service
Clear and effective communication is vital in maintaining a smooth relationship between purchasing departments and suppliers.
A supplier who is responsive and provides regular updates can help mitigate potential issues before they escalate.
Open lines of communication pave the way for better collaboration and problem-solving.
Evaluating a supplier’s customer service practices, such as response times and conflict resolution processes, is important.
Purchasing departments should ensure that the supplier values and prioritizes transparent communication.
Financial Stability
Partnering with financially stable suppliers reduces the risk of disruptions caused by business failures.
Financially viable suppliers are more likely to fulfill orders and maintain a steady supply of materials.
Assessing a supplier’s financial health involves reviewing their credit history, earnings, and any recent changes in ownership.
Purchasing departments should verify that suppliers possess adequate financial resources to support ongoing operations.
This ensures long-term business relationships built on stability and trust.
Location and Logistics
The geographic location of a supplier plays a significant role in shipping times and transportation costs.
Choosing suppliers that are closer to the manufacturing site can decrease lead times and reduce freight expenses.
Additionally, in times of global disruptions, locally sourced suppliers can enhance supply chain resilience.
Considering logistics capabilities, such as warehousing, inventory management, and distribution networks, can further streamline the supply chain.
Analyzing whether a supplier can efficiently deliver materials when and where needed is essential for maintaining supply chain efficiency.
Sustainability Practices
Environmental sustainability is becoming increasingly important in the supplier selection process.
Companies are now prioritizing suppliers who embrace eco-friendly practices and adhere to environmental regulations.
Purchasing departments can assess a supplier’s commitment to sustainability by reviewing their environmental policies, certifications, and waste management strategies.
Partnering with sustainable suppliers can align with corporate values and improve brand image.
Conclusion
Choosing the right suppliers is a critical task for purchasing departments aiming to foster material supply flexibility.
By carefully considering factors such as quality, pricing, capacity, flexibility, communication, financial stability, location, and sustainability, companies can build a robust and adaptable supply chain.
These criteria not only help in selecting the best suppliers but also contribute to creating long-lasting and mutually beneficial relationships.
Through thoughtful supplier selection, purchasing departments can ensure consistent and flexible material supply, leading to a smoother and more efficient production process.
資料ダウンロード
QCD調達購買管理クラウド「newji」は、調達購買部門で必要なQCD管理全てを備えた、現場特化型兼クラウド型の今世紀最高の購買管理システムとなります。
ユーザー登録
調達購買業務の効率化だけでなく、システムを導入することで、コスト削減や製品・資材のステータス可視化のほか、属人化していた購買情報の共有化による内部不正防止や統制にも役立ちます。
NEWJI DX
製造業に特化したデジタルトランスフォーメーション(DX)の実現を目指す請負開発型のコンサルティングサービスです。AI、iPaaS、および先端の技術を駆使して、製造プロセスの効率化、業務効率化、チームワーク強化、コスト削減、品質向上を実現します。このサービスは、製造業の課題を深く理解し、それに対する最適なデジタルソリューションを提供することで、企業が持続的な成長とイノベーションを達成できるようサポートします。
オンライン講座
製造業、主に購買・調達部門にお勤めの方々に向けた情報を配信しております。
新任の方やベテランの方、管理職を対象とした幅広いコンテンツをご用意しております。
お問い合わせ
コストダウンが利益に直結する術だと理解していても、なかなか前に進めることができない状況。そんな時は、newjiのコストダウン自動化機能で大きく利益貢献しよう!
(Β版非公開)