- お役立ち記事
- Supplier selection criteria for purchasing departments to increase material supply flexibility
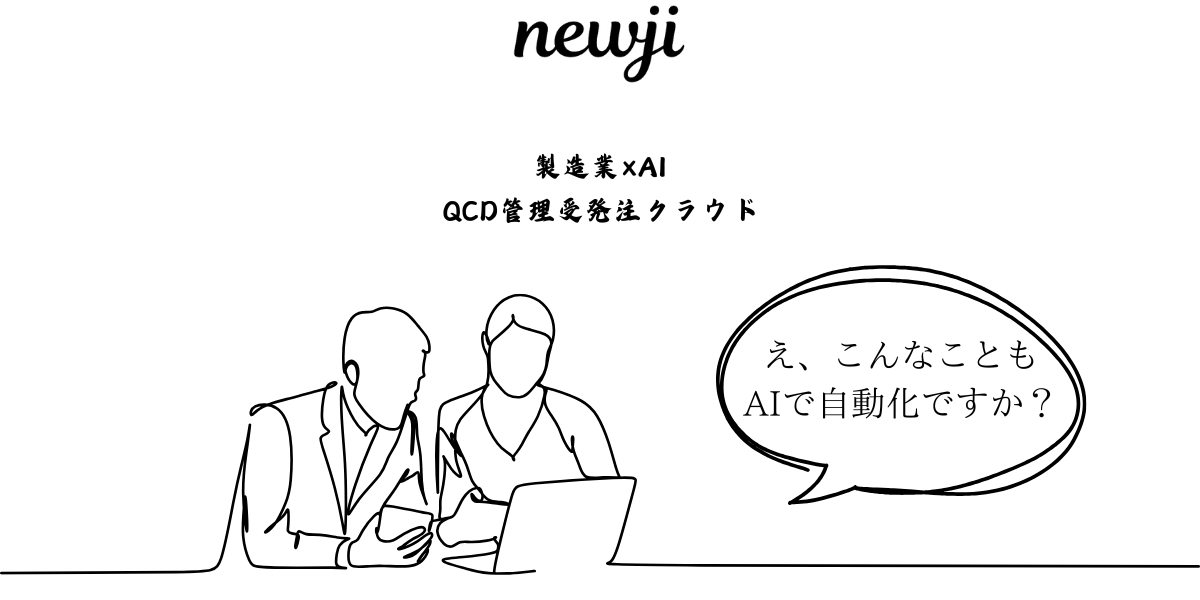
Supplier selection criteria for purchasing departments to increase material supply flexibility
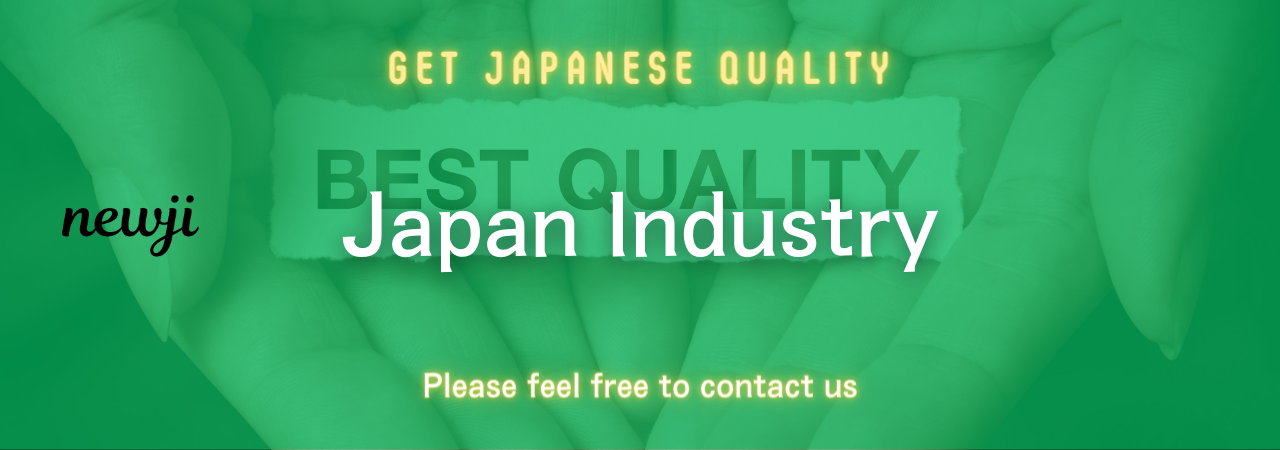
目次
Introduction to Supplier Selection
The purchasing departments of any organization play a crucial role in ensuring that materials are available for production and other operations.
One of the primary functions of these departments is supplier selection, which significantly impacts flexibility in the material supply chain.
In this article, we will explore the key criteria that purchasing departments should consider for choosing suppliers to enhance material supply flexibility.
Understanding Material Supply Flexibility
In today’s fast-paced business environment, flexibility in material supply is essential.
It allows companies to respond to changes in demand, market conditions, and unforeseen disruptions efficiently.
When a company can quickly adapt its supply chain to accommodate these changes, it holds a competitive advantage.
Supplier selection that emphasizes flexibility helps mitigate risks associated with supply shortages or delays.
Key Criteria for Supplier Selection
Selecting the right supplier involves evaluating multiple factors.
Here are the key criteria purchasing departments should consider:
1. Reliability and Consistency
A reliable supplier consistently delivers materials on time and meets quality standards.
Consistency in supply not only ensures smooth operations but also builds trust.
Purchasing departments should assess the supplier’s track record and seek out references or testimonials from other clients to gauge reliability.
2. Quality Assurance
Quality should never be compromised in the pursuit of supply flexibility.
A supplier with stringent quality controls ensures that materials meet the necessary specifications and requirements.
This minimizes the risk of product defects and associated production delays.
3. Pricing and Cost Stability
While competitive pricing is crucial, purchasing departments should also consider the stability of prices offered by suppliers.
Fluctuating prices can affect budgeting and cost control measures.
Establishing long-term relationships with suppliers often leads to better pricing arrangements and cost predictability.
4. Geographic Proximity
Suppliers located closer to the company can significantly enhance supply flexibility.
Reduced lead times, lower transportation costs, and minimized risk of supply chain disruptions are some of the benefits.
Geographic proximity enables quicker response times and fosters stronger relationships between companies and suppliers.
5. Production Capacity and Scalability
A supplier’s production capacity and ability to scale operations are essential factors for flexibility.
Pipelines with suppliers who can quickly increase production based on sudden demand spikes ensure material availability without delays.
Checking the supplier’s infrastructure and resource management capabilities helps in assessing their scalability.
6. Financial Stability
Choosing suppliers who exhibit financial stability is critical to ensuring they can meet contractual obligations.
The risk of supply disruption diminishes when dealing with financially stable suppliers.
Departments should evaluate the potential supplier’s financial statements, credit ratings, and market reputation.
7. Technological Capability
Tech-savvy suppliers are better equipped to integrate into modern supply chains.
Suppliers with technological capabilities can provide accurate tracking, better communication, and seamless systems integration.
This capability fosters improved information flow, which enhances supply chain flexibility.
Building Strategic Supplier Partnerships
Once potential suppliers have been assessed on the outlined criteria, purchasing departments should work towards building strategic partnerships.
Partnerships go beyond transactional relationships to involve collaborative planning, information sharing, and joint problem-solving.
Such interactions improve mutual understanding and lead to tailored solutions that enhance supply chain flexibility.
Mutual Benefits
Both parties benefit from strategic partnerships.
Suppliers gain a stable client base and insight into the company’s long-term plans, while companies enjoy prioritized service, exclusive access to resources, and improved supply terms.
This leads to a more resilient and adaptable supply chain.
Continuous Improvement
Constant engagement with suppliers creates opportunities for continuous improvement.
Regular performance reviews, feedback exchange, and open communication help address challenges promptly.
Implementing key performance indicators and performance monitoring systems fosters a culture of improvement.
Risk Management in Supplier Selection
Risk management should be integral to the supplier selection process.
Unforeseen disruptions, such as natural disasters, political upheavals, or pandemics, can affect supply significantly.
Thus, contingency planning with suppliers is vital to ensure continuity.
Diversification of Suppliers
Relying on a single supplier poses significant risks.
Diversifying the supplier base minimizes the impact of disruptions from one source.
By maintaining a network of well-vetted suppliers, companies enhance their capacity to switch sources in times of need.
Monitoring and Auditing
Regular audits and monitoring of suppliers enable early detection of potential risks.
Having a robust monitoring system helps purchasing departments act swiftly when issues arise, maintaining material supply flexibility.
Conclusion
In conclusion, the supplier selection process is pivotal in achieving material supply flexibility.
By considering factors such as reliability, quality, pricing, geographic proximity, and financial health, purchasing departments can make informed decisions.
Building strategic partnerships and focusing on risk management strategies further solidifies the supply chain’s adaptability.
With a careful approach to supplier selection, companies position themselves to navigate the dynamic business landscape effectively.
資料ダウンロード
QCD調達購買管理クラウド「newji」は、調達購買部門で必要なQCD管理全てを備えた、現場特化型兼クラウド型の今世紀最高の購買管理システムとなります。
ユーザー登録
調達購買業務の効率化だけでなく、システムを導入することで、コスト削減や製品・資材のステータス可視化のほか、属人化していた購買情報の共有化による内部不正防止や統制にも役立ちます。
NEWJI DX
製造業に特化したデジタルトランスフォーメーション(DX)の実現を目指す請負開発型のコンサルティングサービスです。AI、iPaaS、および先端の技術を駆使して、製造プロセスの効率化、業務効率化、チームワーク強化、コスト削減、品質向上を実現します。このサービスは、製造業の課題を深く理解し、それに対する最適なデジタルソリューションを提供することで、企業が持続的な成長とイノベーションを達成できるようサポートします。
オンライン講座
製造業、主に購買・調達部門にお勤めの方々に向けた情報を配信しております。
新任の方やベテランの方、管理職を対象とした幅広いコンテンツをご用意しております。
お問い合わせ
コストダウンが利益に直結する術だと理解していても、なかなか前に進めることができない状況。そんな時は、newjiのコストダウン自動化機能で大きく利益貢献しよう!
(Β版非公開)