- お役立ち記事
- Supply Chain Optimization and Success Stories of Reshoring Strategies
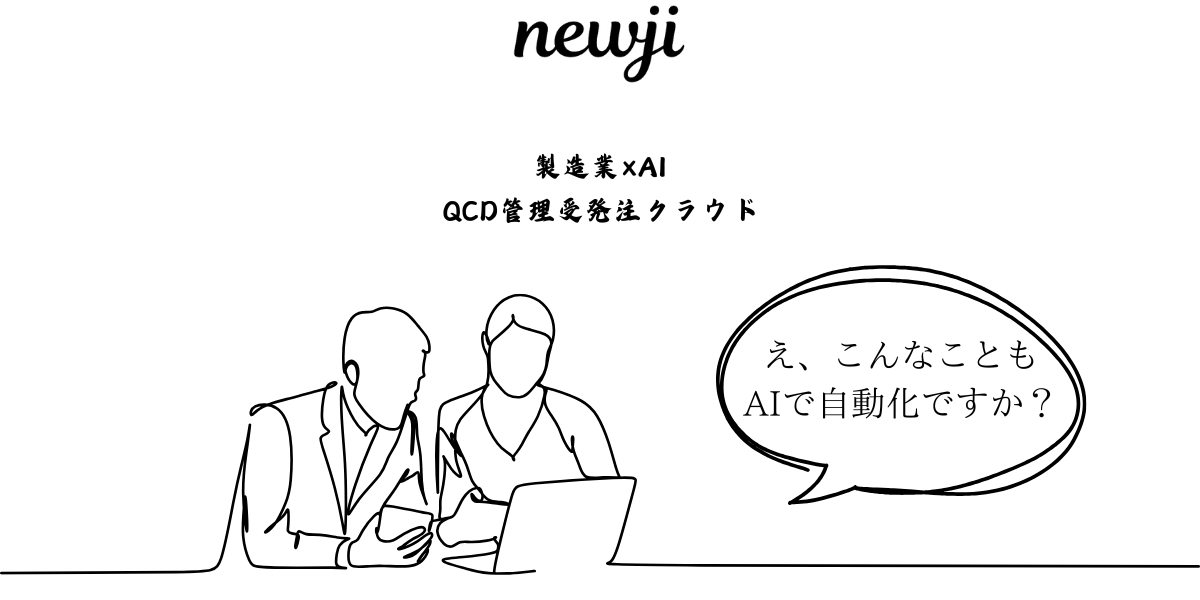
Supply Chain Optimization and Success Stories of Reshoring Strategies
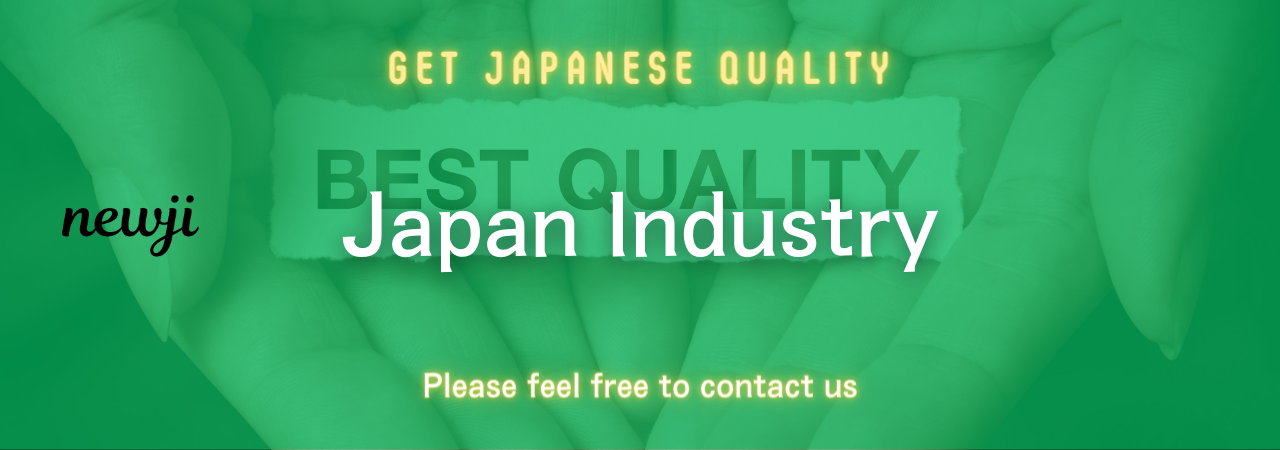
目次
What is Supply Chain Optimization?
Supply chain optimization involves making the supply chain as efficient and cost-effective as possible.
This process includes managing resources, technology, and processes to ensure that products are delivered timely, and meet customer demand while minimizing costs.
When properly implemented, supply chain optimization can lead to significant improvements in profitability and customer satisfaction.
Key Elements of Supply Chain Optimization
Several key elements are critical to successfully optimizing a supply chain.
First, it’s important to understand and map out the entire supply chain from start to finish. This visibility allows businesses to pinpoint inefficiencies and areas for improvement.
Next, data analysis plays a crucial role.
By leveraging big data and analytics, companies can forecast demand more accurately, manage inventory better, and reduce waste.
Technology integration, such as the implementation of advanced software solutions like ERP systems, can streamline operations.
Automation also reduces human error and speeds up processes.
Collaboration with all suppliers and stakeholders ensures that everyone in the supply chain is aligned and working towards common goals.
Shared information and transparent communication can prevent bottlenecks and delays.
Understanding Reshoring Strategies
Reshoring involves bringing manufacturing and production processes back to the company’s home country from overseas.
This strategy often arises when companies face challenges such as rising overseas costs, supply chain disruptions, or quality control issues.
Advantages of Reshoring
Reshoring offers numerous benefits for businesses.
Firstly, companies can reduce lead times as production is closer to the end customer.
This can significantly improve service levels and customer satisfaction.
Second, reshoring enhances quality control.
When production is local, it is easier to monitor and maintain high standards, reducing the risk of defects and recalls.
By manufacturing closer to home, companies may also tap into local expertise and innovation, which can lead to the development of new and improved products.
Another benefit is the potential for cost savings.
While labor might be more expensive domestically, savings in transportation, tariffs, and lower inventory costs often offset these expenses.
Lastly, reshoring can help companies become more eco-friendly by cutting down on emissions resulting from long-distance transportation.
Success Stories of Reshoring Strategies
Many companies have successfully implemented reshoring strategies, reaping numerous benefits:
General Electric (GE)
General Electric is a prime example of successful reshoring.
By bringing some of its appliance manufacturing back to the U.S. from China, GE reduced lead times and improved product quality.
The company was able to react more swiftly to market demands and customer needs.
Apple
Apple has made headlines by bringing some of its component manufacturing back to the U.S.
This move allowed Apple to significantly enhance product quality, ensuring that its devices maintain the high standards the brand is known for.
Ford
Ford reshored some of its manufacturing operations, which resulted in better control over production processes.
This led to significant cost savings and improved product quality, allowing Ford to become more competitive in the automobile market.
How Reshoring Complements Supply Chain Optimization
Reshoring and supply chain optimization often go hand in hand.
When companies decide to reshore, they are taking a significant step towards optimizing their supply chain.
Shorter supply chains mean fewer risks and more agile operations.
Localizing production can lead to better inventory management.
Since products are manufactured and delivered faster, companies can adopt just-in-time inventory systems, minimizing storage costs and reducing waste.
Additionally, strong relationships with local suppliers can foster innovation and streamlined collaboration.
With closer proximity, businesses and suppliers can work together more efficiently, creating a more optimized supply chain.
Challenges of Reshoring
Despite the benefits, reshoring does come with challenges.
Companies often face higher labor costs domestically, which can impact their bottom line.
Finding skilled labor locally can also be difficult.
Not all countries have the workforce expertise required for specific manufacturing needs.
Furthermore, regulatory differences and environmental laws may pose challenges for companies used to operating in more lenient overseas markets.
Navigating these new regulations requires time and investment.
Steps to Successfully Implement Reshoring
Several steps can help companies successfully implement reshoring strategies:
Assess the Current Supply Chain
Begin by auditing the current supply chain system to identify inefficiencies and potential benefits of reshoring.
Consider factors such as costs, lead times, risks, and existing partnerships.
Build a Reshoring Plan
Develop a comprehensive plan that includes budgeting, timelines, and risk management strategies.
Ensure that the plan aligns with the company’s long-term objectives.
Engage with Local Suppliers
Forge strong relationships with local suppliers.
Establish clear communication channels and define expectations to ensure smooth operations.
Invest in Technology and Training
Adopt advanced manufacturing technologies to maintain cost efficiency.
Additionally, invest in training programs to equip the local workforce with the necessary skills.
Monitor and Adjust
Continuously monitor the reshoring process and make necessary adjustments.
Evaluate the performance regularly to ensure that the reshoring strategy meets the desired objectives.
Conclusion
Supply chain optimization and reshoring strategies are crucial for companies striving for efficiency, cost-effectiveness, and quality.
While reshoring comes with its set of challenges, the benefits often outweigh the obstacles, leading to improved customer satisfaction and overall success.
By carefully planning and strategically implementing reshoring, companies can create robust and resilient supply chains that stand the test of time.
資料ダウンロード
QCD調達購買管理クラウド「newji」は、調達購買部門で必要なQCD管理全てを備えた、現場特化型兼クラウド型の今世紀最高の購買管理システムとなります。
ユーザー登録
調達購買業務の効率化だけでなく、システムを導入することで、コスト削減や製品・資材のステータス可視化のほか、属人化していた購買情報の共有化による内部不正防止や統制にも役立ちます。
NEWJI DX
製造業に特化したデジタルトランスフォーメーション(DX)の実現を目指す請負開発型のコンサルティングサービスです。AI、iPaaS、および先端の技術を駆使して、製造プロセスの効率化、業務効率化、チームワーク強化、コスト削減、品質向上を実現します。このサービスは、製造業の課題を深く理解し、それに対する最適なデジタルソリューションを提供することで、企業が持続的な成長とイノベーションを達成できるようサポートします。
オンライン講座
製造業、主に購買・調達部門にお勤めの方々に向けた情報を配信しております。
新任の方やベテランの方、管理職を対象とした幅広いコンテンツをご用意しております。
お問い合わせ
コストダウンが利益に直結する術だと理解していても、なかなか前に進めることができない状況。そんな時は、newjiのコストダウン自動化機能で大きく利益貢献しよう!
(Β版非公開)