- お役立ち記事
- Supply chain optimization tips for aerospace procurement departments
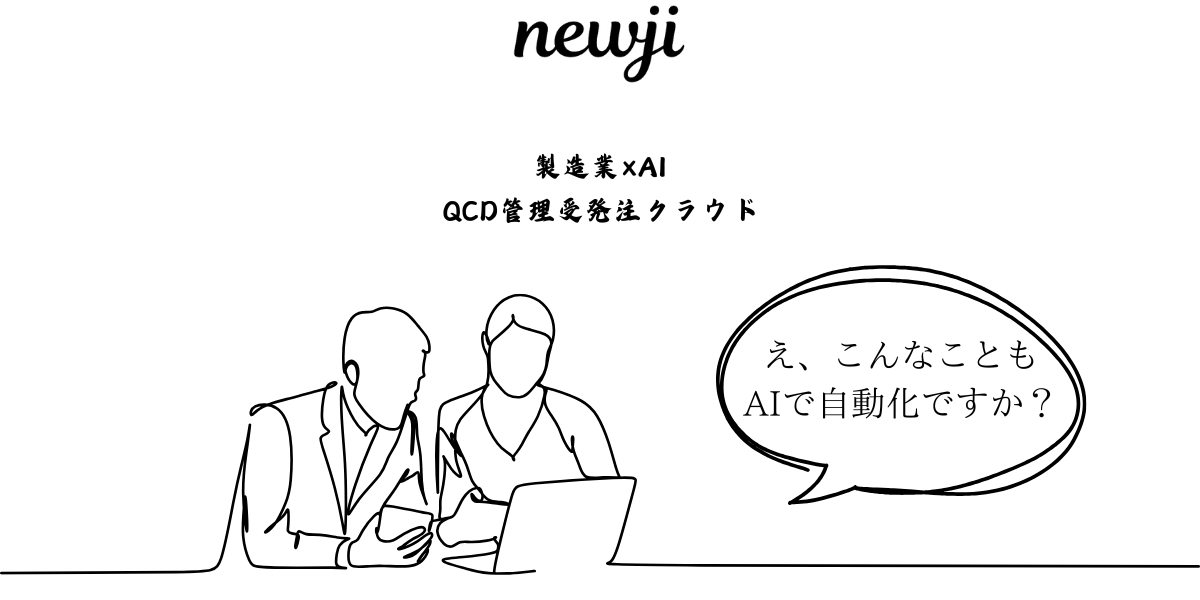
Supply chain optimization tips for aerospace procurement departments
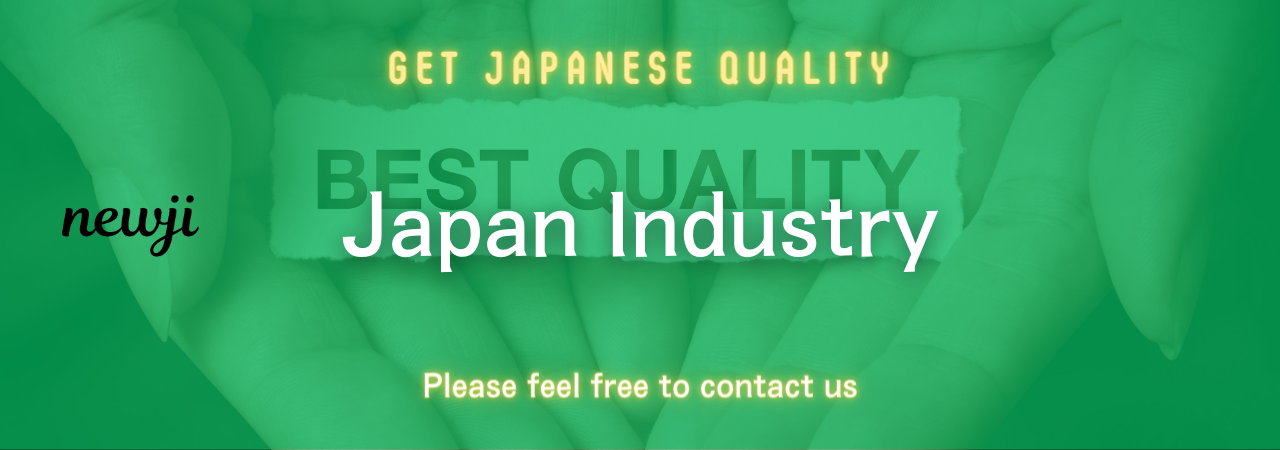
目次
Understanding the Importance of Supply Chain Optimization
In the fast-paced world of aerospace, efficient supply chain management is crucial.
With intricate components and strict compliance requirements, optimizing the supply chain can make a significant difference in operational success.
It involves improving processes to ensure that parts and materials are delivered on time, at reduced costs, and to quality standards.
Procurement departments in aerospace companies face unique challenges.
They must deal with complex logistics, a global supplier base, and compliance with stringent regulatory standards.
Therefore, understanding and implementing supply chain optimization strategies is vital for the successful functioning of aerospace procurement departments.
Identifying Challenges in Aerospace Procurement
Aerospace procurement is not without its hurdles.
Chief among these challenges are the dependencies on multiple suppliers worldwide, which can significantly affect timing and quality.
Any disruption, whether due to geopolitical issues, natural disasters, or logistical failures, can lead to delays in production.
Furthermore, aerospace components must pass through rigorous testing and certification, unlike many other industries.
This adds an extra level of complexity, requiring procurement teams to maintain a delicate balance between cost and quality, while ensuring compliance with international regulations.
Dealing with Supply Chain Disruptions
To mitigate the risk of disruptions, procurement departments need robust contingency plans.
Developing strong relationships with a diverse supplier base is crucial.
This ensures alternatives are available should one supplier face difficulties.
Utilizing technology such as predictive analytics can help anticipate potential disruptions.
These tools analyze historical data and current trends to warn of potential risks, allowing procurement teams to act proactively rather than reactively.
Leveraging Technology for Optimization
One of the most effective ways to optimize the supply chain is through the integration of modern technology.
Aerospace procurement departments can benefit greatly from the application of digital solutions.
Implementing Automation in Procurement
Automating procurement processes can significantly reduce errors and increase efficiency.
From order processing to inventory management, automation can streamline operations, enabling procurement teams to focus on strategic tasks rather than administrative duties.
For instance, electronic procurement systems can automate order tracking and supplier management.
This ensures that orders are processed swiftly, and any discrepancies are identified quickly, minimizing delays.
Utilizing Advanced Analytics
Advanced analytics play a pivotal role in optimizing supply chains.
By harnessing data analytics, procurement departments can gain insights into cost-saving opportunities, supplier performance, and demand forecasting.
These insights assist in making informed decisions, leading to enhanced cost efficiency and improved supplier relationships.
Moreover, analytics can aid in identifying trends and predicting future demands, allowing for better planning and resource allocation.
Building Strong Supplier Relationships
A key element of successful supply chain optimization is nurturing strong relationships with suppliers.
Building trust and collaboration with suppliers ensures that the procurement process is smooth and predictable.
Engaging in Regular Communication
Regular communication with suppliers is critical.
Maintaining open lines of dialogue ensures that any issues are addressed promptly.
It also allows procurement departments to align closely with suppliers’ capacities and schedules.
Collaborative relationships encourage transparency and foster reliability, ultimately leading to a more resilient supply chain.
Negotiating Long-Term Contracts
Negotiating long-term contracts can provide stability for both aerospace companies and their suppliers.
Such agreements not only secure better pricing but also ensure that the suppliers prioritize the needs of the procurement departments.
Long-term relationships often result in mutual benefits, such as improved service level agreements and consistent quality.
Emphasizing Quality Assurance in Procurement
In aerospace, quality assurance is non-negotiable.
Thus, procurement departments must have rigorous quality control measures in place to verify that all parts and materials meet the necessary standards.
Compliance with quality certifications is indispensable in preventing costly recalls and ensuring customer safety.
Implementing Quality Checks at Multiple Levels
Setting up multiple levels of quality checks can prevent defective parts from reaching manufacturing phases.
This includes inspections at the supplier’s facility, upon delivery, and pre-production.
Data-driven quality control systems can also be implemented to enhance inspection accuracy and efficiency.
These systems can reduce manual errors and ensure comprehensive checks, ultimately safeguarding the quality of aerospace components.
Adhering to Compliance Standards
Aerospace procurement departments must stay abreast of current compliance standards, which are subject to regular updates.
Ensuring vendors comply with industry standards from the onset reduces the risk of non-compliance penalties and delays.
Providing ongoing training to procurement teams on the latest compliance developments is essential.
This empowers teams with the knowledge needed to evaluate and select suppliers who meet required certification standards.
Conclusion: Achieving Excellence in Aerospace Procurement
Supply chain optimization is an ongoing process, vital for achieving excellence in aerospace procurement.
By identifying challenges, leveraging technology, building strong supplier relationships, and emphasizing quality assurance, procurement departments can significantly enhance their supply chain efficiency.
Implementing these supply chain optimization tips can lead aerospace companies toward smoother operations, reduced costs, and maintaining high standards of safety and quality.
With continuous evaluation and adaptation, procurement departments will be well-equipped to meet the demands of the ever-evolving aerospace industry.
資料ダウンロード
QCD調達購買管理クラウド「newji」は、調達購買部門で必要なQCD管理全てを備えた、現場特化型兼クラウド型の今世紀最高の購買管理システムとなります。
ユーザー登録
調達購買業務の効率化だけでなく、システムを導入することで、コスト削減や製品・資材のステータス可視化のほか、属人化していた購買情報の共有化による内部不正防止や統制にも役立ちます。
NEWJI DX
製造業に特化したデジタルトランスフォーメーション(DX)の実現を目指す請負開発型のコンサルティングサービスです。AI、iPaaS、および先端の技術を駆使して、製造プロセスの効率化、業務効率化、チームワーク強化、コスト削減、品質向上を実現します。このサービスは、製造業の課題を深く理解し、それに対する最適なデジタルソリューションを提供することで、企業が持続的な成長とイノベーションを達成できるようサポートします。
オンライン講座
製造業、主に購買・調達部門にお勤めの方々に向けた情報を配信しております。
新任の方やベテランの方、管理職を対象とした幅広いコンテンツをご用意しております。
お問い合わせ
コストダウンが利益に直結する術だと理解していても、なかなか前に進めることができない状況。そんな時は、newjiのコストダウン自動化機能で大きく利益貢献しよう!
(Β版非公開)