- お役立ち記事
- Surface Cleaning Techniques for Manufacturing
Surface Cleaning Techniques for Manufacturing
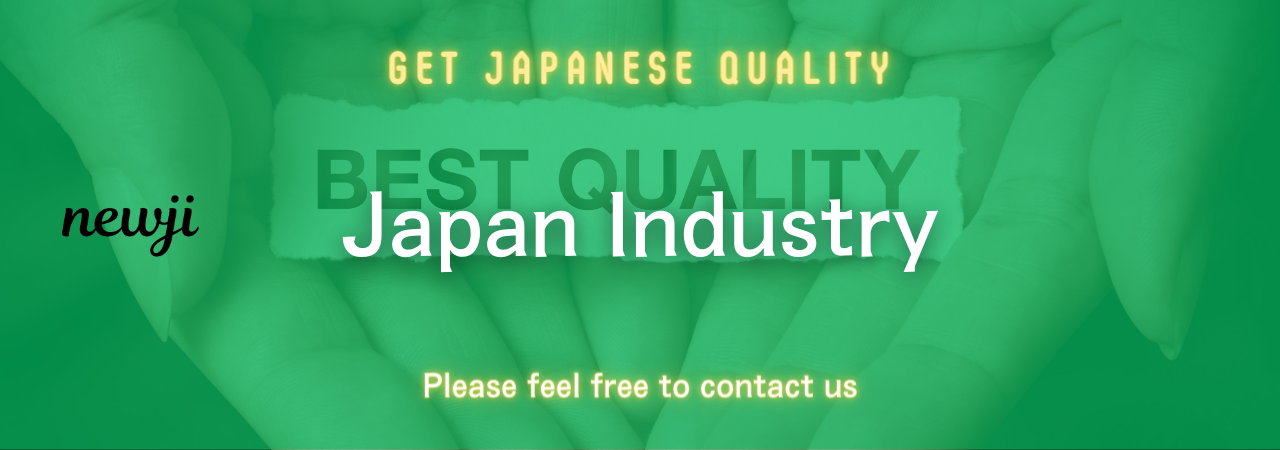
目次
Understanding Surface Cleaning in Manufacturing
Surface cleaning in manufacturing is a crucial process that ensures products are free from dust, dirt, grease, and other contaminants before proceeding to assembly or packaging stages.
Having clean surfaces is essential not only for aesthetic purposes but also for the product’s functionality, durability, and safety.
Contaminants left unchecked can compromise the quality and lifespan of the product, potentially leading to defects and recalls.
Why Is Surface Cleaning Important?
Surface cleaning plays a vital role in maintaining the integrity of products across various industries, including electronics, automotive, aerospace, and pharmaceuticals.
Imagine a computer processor that is assembled with dust particles embedded; it could easily overheat or malfunction.
Similarly, in the automotive industry, any remnants of solvents or oils could affect the performance of parts and lead to accidents.
Ensuring a clean surface improves the efficiency of subsequent processes, such as painting, coating, or bonding.
For example, paint applied on a dirty surface may peel off, leading to a poor finish and additional costs for rework.
By eliminating contaminants, surface cleaning supports compliance with industry standards and regulatory requirements.
Types of Contaminants in Manufacturing
Manufacturing environments are prone to a wide range of contaminants that can adhere to surfaces during various stages of production.
These contaminants include:
Particulate Contaminants
These are small particles such as dust, metal shavings, or lint that may settle on surfaces.
They are often invisible to the naked eye but can cause significant problems if not removed.
Organic Contaminants
Commonly, these include oils, grease, and residues from manufacturing processes.
They can often be more stubborn to remove and may require specialized cleaning solutions.
Inorganic Contaminants
These include salts, oxides, and minerals that may have formed on surfaces due to environmental exposure or chemical reactions.
They can affect the chemical resilience and reaction properties of a material.
Popular Surface Cleaning Techniques
Different surface cleaning techniques are applied depending on the type and level of contamination and the nature of the surface.
Below are some popular surface cleaning methods used in manufacturing:
Solvent Cleaning
Solvent cleaning involves the use of organic solvents to dissolve contaminants, particularly oils and grease.
This method is highly effective in degreasing surfaces.
Solvents such as acetone, alcohol, or trichloroethylene are commonly used due to their strong dissolving capabilities.
While effective, there are considerations related to health and environmental impacts, so proper ventilation and safety gear are necessary.
Ultrasonic Cleaning
Ultrasonic cleaning uses high-frequency sound waves to agitate a cleaning solvent, creating microscopic bubbles that physically remove contaminants from surfaces.
This method is ideal for cleaning detailed and delicate components that conventional cleaning may not effectively address.
Because it is non-abrasive, ultrasonic cleaning is suitable for sensitive materials and complex geometries.
Abrasive Blasting
Abrasive blasting, often called sandblasting, involves blasting a surface with fine particles to remove rust, paint, or other surface materials.
The abrasives can vary from sand, glass beads, to metal grit, and the choice depends on the surface being cleaned and the desired finish.
This technique is particularly effective for cleaning metal surfaces but must be carefully controlled to avoid damage.
Plasma Cleaning
Plasma cleaning employs ionized gas to remove organic contaminants, leaving surfaces ultra-clean.
This cutting-edge technique is used extensively in the electronics and biomedical industries where even minute impurities can affect performance.
It is a dry process, eliminating the need for water or solvents, and is excellent for sensitive surface cleaning.
Laser Cleaning
Laser cleaning uses pulsed laser beams to remove contaminants without abrasive contact.
This environmentally friendly method is precise and can be adjusted to target various levels of contamination without damaging the surface.
Industries such as aerospace consider laser cleaning invaluable due to its precision and minimal waste production.
Choosing the Right Cleaning Technique
Selecting the best surface cleaning technique depends on various factors, including the type of material, the nature of the contaminants, environmental considerations, and cost efficiency.
Here are some guidelines for choosing the right method:
Material Compatibility
Ensure that the cleaning method is appropriate for the substrate material.
For instance, abrasive methods may not be suitable for delicate components.
Contaminant Type
Different contaminants require different cleaning processes.
Oils may need solvent cleaning, while fine dust may be effectively removed using ultrasonic methods.
Environmental Impact
Assess the environmental implications of the cleaning method.
For example, solvent use should be minimized to reduce emissions, and it might be better to use green alternatives like laser or plasma cleaning.
Cost and Efficiency
Factor in the cost and time efficiency of the process.
Though some advanced techniques might have higher upfront costs, they could be more cost-effective over time due to their efficiency and reduced need for reworking.
Conclusion
Surface cleaning in manufacturing is not a one-size-fits-all approach.
It involves understanding the unique challenges of each production environment and choosing the methods that best address those needs.
As technology advances, more efficient and environmentally friendly cleaning processes continue to evolve, helping manufacturers maintain high quality standards while adhering to safety and environmental regulations.
資料ダウンロード
QCD調達購買管理クラウド「newji」は、調達購買部門で必要なQCD管理全てを備えた、現場特化型兼クラウド型の今世紀最高の購買管理システムとなります。
ユーザー登録
調達購買業務の効率化だけでなく、システムを導入することで、コスト削減や製品・資材のステータス可視化のほか、属人化していた購買情報の共有化による内部不正防止や統制にも役立ちます。
NEWJI DX
製造業に特化したデジタルトランスフォーメーション(DX)の実現を目指す請負開発型のコンサルティングサービスです。AI、iPaaS、および先端の技術を駆使して、製造プロセスの効率化、業務効率化、チームワーク強化、コスト削減、品質向上を実現します。このサービスは、製造業の課題を深く理解し、それに対する最適なデジタルソリューションを提供することで、企業が持続的な成長とイノベーションを達成できるようサポートします。
オンライン講座
製造業、主に購買・調達部門にお勤めの方々に向けた情報を配信しております。
新任の方やベテランの方、管理職を対象とした幅広いコンテンツをご用意しております。
お問い合わせ
コストダウンが利益に直結する術だと理解していても、なかなか前に進めることができない状況。そんな時は、newjiのコストダウン自動化機能で大きく利益貢献しよう!
(Β版非公開)