- お役立ち記事
- Surface Roughness Inspection Techniques in Non-Ferrous Metal Manufacturing: Contact vs. Non-Contact Methods
月間76,176名の
製造業ご担当者様が閲覧しています*
*2025年3月31日現在のGoogle Analyticsのデータより
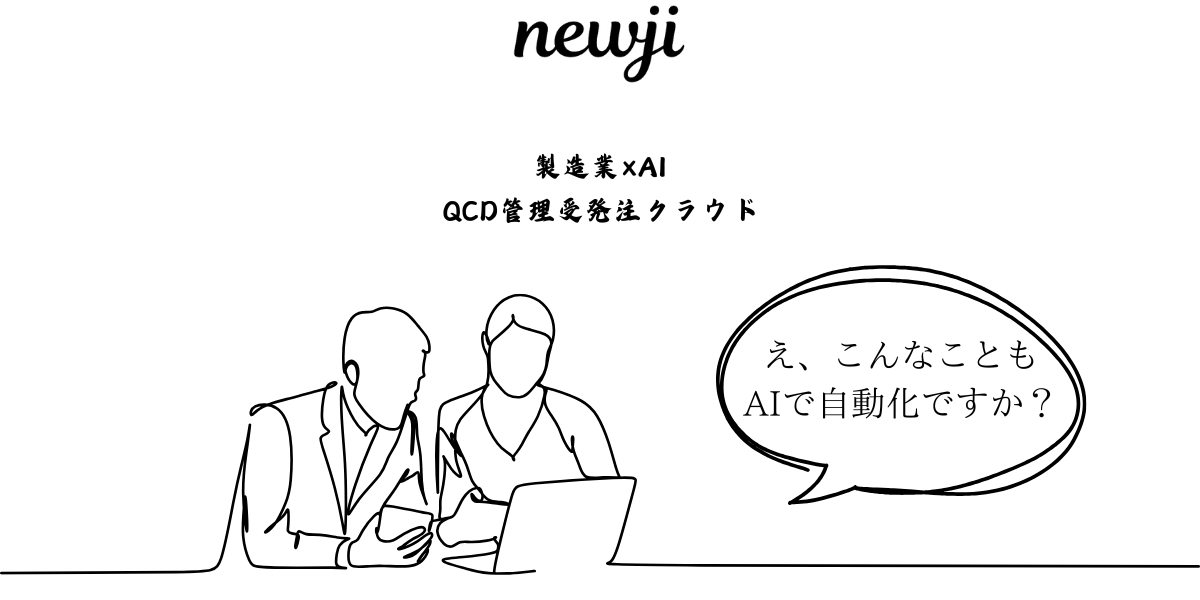
Surface Roughness Inspection Techniques in Non-Ferrous Metal Manufacturing: Contact vs. Non-Contact Methods
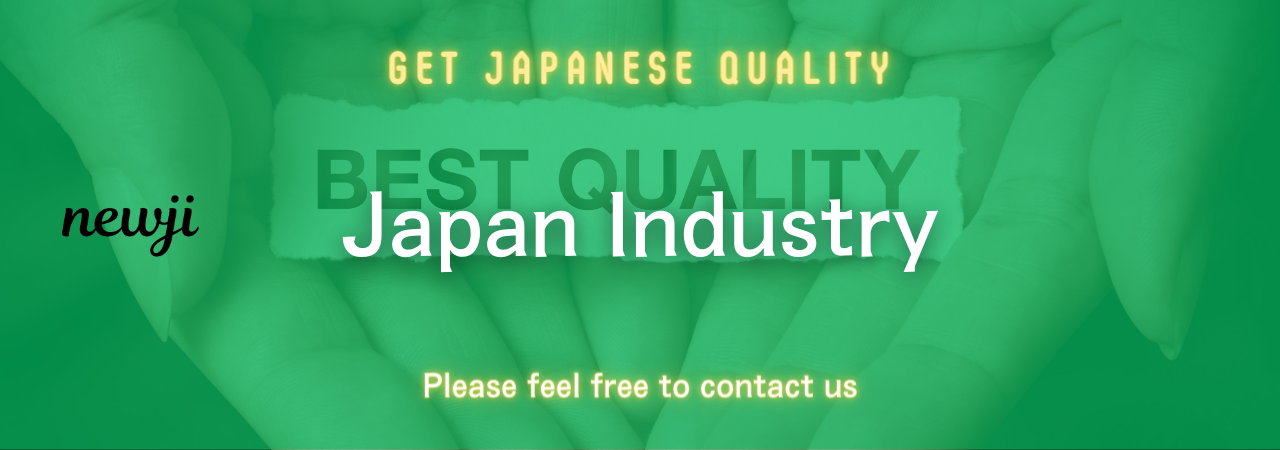
目次
Understanding Surface Roughness in Non-Ferrous Metal Manufacturing
When crafting non-ferrous metals such as aluminum, copper, or brass, achieving the desired surface roughness is crucial.
Surface roughness has a significant impact on the metal’s performance, appearance, and suitability for its intended application.
In the manufacturing process, accurately measuring and inspecting surface roughness is essential to ensure quality control.
Manufacturers rely on two primary methods for surface roughness inspection – contact and non-contact techniques.
Both methods have their own unique procedures, advantages, and challenges.
Contact Surface Roughness Inspection
How Contact Methods Work
Contact inspection methods involve direct physical contact with the metal surface.
A stylus or probe is typically used to traverse the surface, measuring variations in height to determine roughness.
The most common tool used in contact inspection is the profilometer.
This device moves a diamond-tipped stylus across the metal surface and records deviations to produce a roughness profile.
Advantages of Contact Methods
Contact methods are widely appreciated for their precision and reliability.
They provide highly accurate measurements in terms of microns, making them suitable for applications where tight tolerances are necessary.
Furthermore, contact methods are generally cost-effective in terms of initial equipment investment compared to high-tech alternatives.
They are simple to implement and do not require advanced understanding of software or technology, making them accessible to manufacturing teams with varying levels of expertise.
Challenges with Contact Methods
One of the main challenges with contact methods is their potential to damage delicate surfaces.
Since the stylus must physically touch the surface, there is a risk of scratching or altering the surface finish, especially with soft metals such as some non-ferrous varieties.
Contact methods can be slow, particularly when inspecting large surfaces, as the stylus must traverse the entire inspection area to generate a complete measurement profile.
In addition, small features or intricate patterns could be missed depending on the stylus size and shape.
Non-Contact Surface Roughness Inspection
How Non-Contact Methods Work
Non-contact inspection techniques utilize optical or laser-based technologies for measuring surface roughness.
These methods involve no direct physical contact with the object and instead rely on measurements carried out at a distance.
Optical methods may involve the use of interferometry, confocal microscopy, or laser scanning to capture the surface profile.
The data collected is then processed by sophisticated software to provide a detailed analysis of the surface roughness.
Advantages of Non-Contact Methods
Non-contact methods excel in preserving the integrity of the metal surface since they do not involve physical contact that might scratch or damage the surface.
They are capable of rapidly scanning large areas, making them efficient for inspecting extensive surfaces or high-volume production runs.
Additionally, some non-contact methods offer three-dimensional mapping, providing comprehensive surface data that’s impossible to obtain via contact methods.
These techniques are adept at capturing detailed surface information, including small features and complex geometries.
Challenges with Non-Contact Methods
The primary challenge with non-contact methods is the high initial investment cost, both in terms of equipment and training.
This technology requires a certain level of expertise to operate and interpret results accurately.
Environmental factors such as lighting conditions or surface reflectivity can affect measurement accuracy.
Some techniques may struggle with surfaces that are particularly shiny or transparent, necessitating additional calibration and adjustments.
Choosing the Right Method for Your Manufacturing Process
Selecting between contact and non-contact surface roughness inspection methods depends on several critical factors.
The material properties, required precision, production volume, budget constraints, and specific application requirements all play a role in determining the most appropriate choice.
Material Considerations
For softer metal surfaces that are at risk of damage, non-contact methods are preferable due to their non-invasive nature.
For harder metals where precision is prioritized, contact methods could be more suitable.
Precision and Detail Requirements
In cases where high precision or detailed surface mapping is essential, non-contact methods offer significant advantages with their advanced measuring capabilities.
However, for general purposes where precision does not exceed the capabilities of contact methods, the latter might offer a cost-effective solution.
Production Volume
High-volume productions may benefit from the rapid scanning capabilities of non-contact methods, reducing inspection time and increasing overall efficiency.
Budget Constraints
With limited budgets, initially opting for contact methods might make more sense due to lower equipment costs.
However, if long-term savings from efficiency and reduced surface damage are significant, investing in non-contact technology could prove beneficial.
Conclusion
Both contact and non-contact surface roughness inspection methods play vital roles in non-ferrous metal manufacturing processes.
Understanding the distinct characteristics, advantages, and limitations of each technique enables manufacturers to make informed decisions tailored to their specific requirements.
As technology advances, the capabilities and affordability of both methods will continue to evolve, offering even more refined options for producing high-quality non-ferrous metal products.
資料ダウンロード
QCD管理受発注クラウド「newji」は、受発注部門で必要なQCD管理全てを備えた、現場特化型兼クラウド型の今世紀最高の受発注管理システムとなります。
ユーザー登録
受発注業務の効率化だけでなく、システムを導入することで、コスト削減や製品・資材のステータス可視化のほか、属人化していた受発注情報の共有化による内部不正防止や統制にも役立ちます。
NEWJI DX
製造業に特化したデジタルトランスフォーメーション(DX)の実現を目指す請負開発型のコンサルティングサービスです。AI、iPaaS、および先端の技術を駆使して、製造プロセスの効率化、業務効率化、チームワーク強化、コスト削減、品質向上を実現します。このサービスは、製造業の課題を深く理解し、それに対する最適なデジタルソリューションを提供することで、企業が持続的な成長とイノベーションを達成できるようサポートします。
製造業ニュース解説
製造業、主に購買・調達部門にお勤めの方々に向けた情報を配信しております。
新任の方やベテランの方、管理職を対象とした幅広いコンテンツをご用意しております。
お問い合わせ
コストダウンが利益に直結する術だと理解していても、なかなか前に進めることができない状況。そんな時は、newjiのコストダウン自動化機能で大きく利益貢献しよう!
(β版非公開)