- お役立ち記事
- Surface Roughness Testing and Result Management for Non-Ferrous Metals
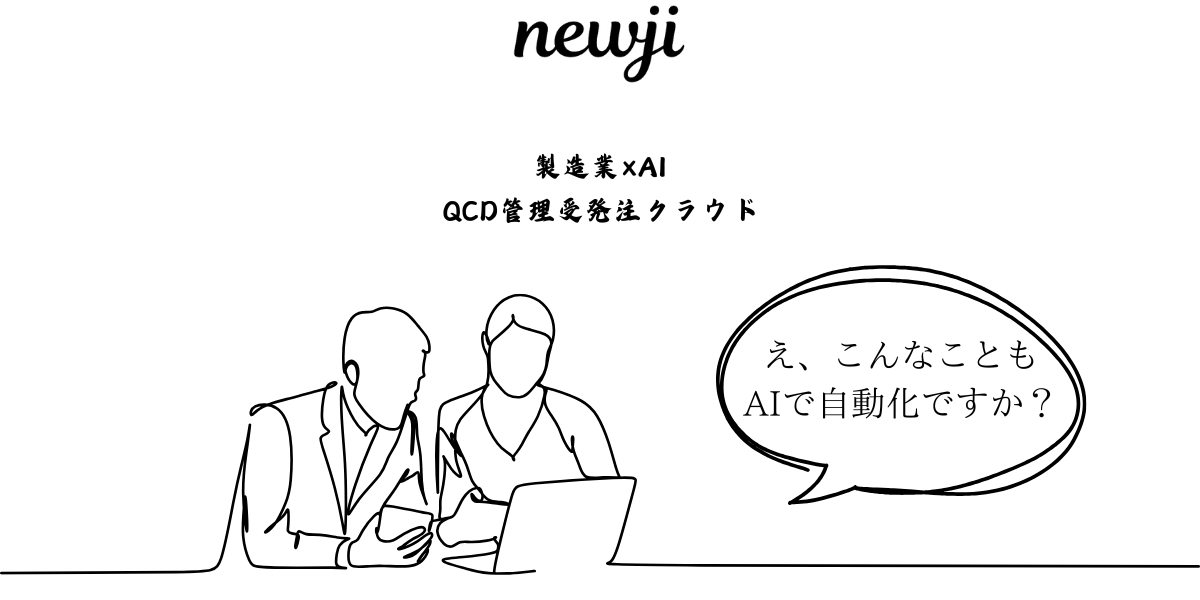
Surface Roughness Testing and Result Management for Non-Ferrous Metals
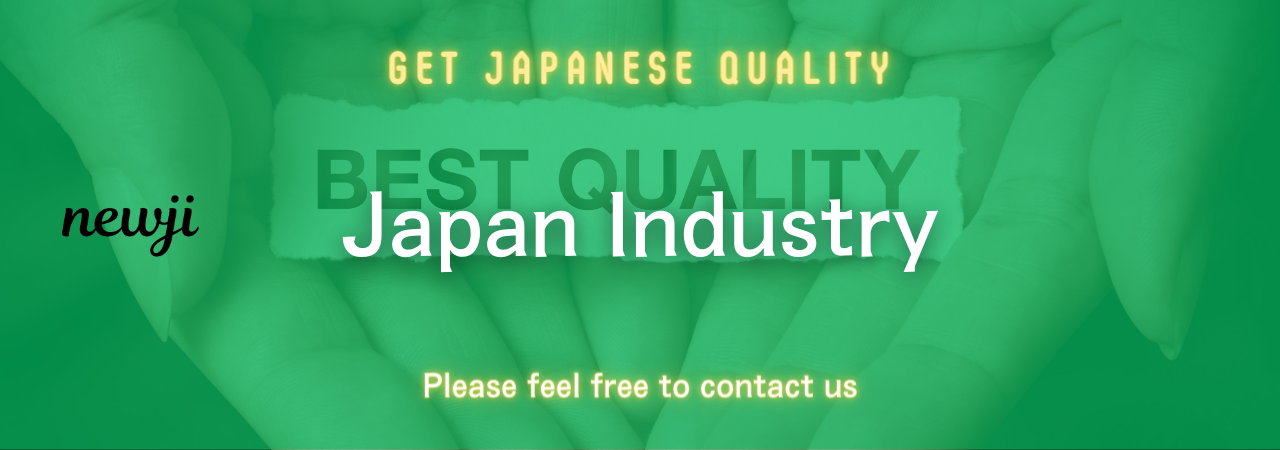
目次
Understanding Surface Roughness
Surface roughness refers to the texture of a surface, characterized by its irregularities and deviations.
These irregularities can range from high peaks to low valleys, affecting the material’s overall functionality and aesthetics.
In the context of non-ferrous metals, such as aluminum, copper, or titanium, surface roughness plays a crucial role.
It influences factors like friction, wear resistance, and the metal’s ability to hold coatings or paints.
A smoother surface might be essential for certain applications, ensuring better performance, durability, and visual appeal.
The Importance of Surface Roughness Testing
Surface roughness testing is vital for various industries that rely on non-ferrous metals, including aerospace, automotive, and electronics.
It helps manufacturers control and improve the manufacturing process, ensuring that product specifications are met.
By evaluating roughness, engineers can predict how a metal will behave in terms of strength, lubrication, and contact mechanics.
Moreover, surface roughness affects a product’s reliability and lifespan, often determining its suitability for specific environments or functions.
Common Methods of Surface Roughness Testing
Several techniques are employed to measure surface roughness accurately.
Some of the most commonly used methods include:
Contact Profilometry
This traditional method involves a stylus that physically contacts the surface.
As the stylus moves over the surface, it records the height variations, creating an accurate profilograph of the surface texture.
While highly precise, this method can be slow and may not be suitable for extremely soft or delicate surfaces.
Optical Profilometry
Using light waves to measure surface roughness, optical profilometry offers a non-contact approach.
This method employs white light interference to generate a 3D image of the surface, capturing precise details without physical contact.
It is faster and suitable for a wide range of materials, including those that are easily damaged by traditional methods.
Tactile Roughness Measurement
With tactile sensors, this method senses roughness based on changes in electrical signals as the sensor slides over the surface.
It is a modern technique used in automated systems, providing fast measurements with minimal manual intervention.
Functions of Surface Roughness Testing Instruments
Surface roughness testing instruments serve crucial functions.
They not only measure roughness but also provide insights into manufacturing processes.
These instruments calculate key roughness parameters, which are essential for quality control.
The most common parameters include:
Ra (Roughness Average)
Ra is the most commonly used roughness parameter, providing an average deviation of the surface profile from the mean line.
It offers a generalized view of overall surface texture, making it ideal for many applications.
Rz (Average Maximum Height)
Rz measures the average of the absolute values of the five highest peaks and the five lowest valleys within a sample length.
It is particularly useful for evaluating extreme surface features that might impact performance.
Rt (Total Height of the Profile)
Rt represents the vertical distance between the highest peak and the lowest valley in the entire surface profile.
It gives a snapshot of the total height variation, important for applications with strict surface flatness requirements.
Managing Surface Roughness Results
Once surface roughness testing is completed, managing the results is crucial for maintaining quality assurance.
The data gathered can be used to inform production decisions, guide future projects, and ensure customer satisfaction.
Data Analysis
The first step in result management involves analyzing the collected data.
Using software solutions, manufacturers can assess trends, identify patterns, and detect anomalies in the roughness measurements.
Advanced analytics provide insights into how production adjustments can refine processes, optimize materials, and enhance the quality of non-ferrous metal products.
Documentation and Reporting
Proper documentation of surface roughness data is essential for compliance with industry standards and regulations.
Comprehensive reporting includes the methodology used, measurements obtained, and any deviations from expected standards.
These reports serve as a valuable resource for future audits and evaluations.
Quality Control Integration
Integrating surface roughness results with quality control systems ensures consistency and repeatability in production.
By setting baseline roughness parameters, manufacturers can establish quality benchmarks that every product must meet.
This integration not only improves product quality but also reduces waste and lowers production costs.
Applications of Surface Roughness Testing in Industry
Surface roughness testing is widely applicable across industries using non-ferrous metals.
Several key applications include:
Aerospace Industry
In aerospace, surface roughness affects aerodynamics, fatigue resistance, and the efficacy of protective coatings.
Precise testing ensures that parts meet stringent requirements for safety and performance.
Automotive Industry
For the automotive sector, surface roughness impacts fuel efficiency, noise reduction, and longevity of components.
By maintaining optimal roughness levels, manufacturers can enhance vehicle function and customer satisfaction.
Electronics Industry
In electronics, surface roughness determines the performance of components like heat sinks and circuit boards.
Testing helps in achieving the desired thermal conductivity and electrical resistance.
Conclusion
In conclusion, surface roughness testing is a vital process for industries relying on non-ferrous metals.
Through various testing methods and robust result management, manufacturers can ensure their products meet high standards.
These efforts lead to improved product performance, extended lifespan, and elevated customer satisfaction.
Understanding and controlling surface roughness allows companies to remain competitive and efficient in today’s demanding market.
資料ダウンロード
QCD調達購買管理クラウド「newji」は、調達購買部門で必要なQCD管理全てを備えた、現場特化型兼クラウド型の今世紀最高の購買管理システムとなります。
ユーザー登録
調達購買業務の効率化だけでなく、システムを導入することで、コスト削減や製品・資材のステータス可視化のほか、属人化していた購買情報の共有化による内部不正防止や統制にも役立ちます。
NEWJI DX
製造業に特化したデジタルトランスフォーメーション(DX)の実現を目指す請負開発型のコンサルティングサービスです。AI、iPaaS、および先端の技術を駆使して、製造プロセスの効率化、業務効率化、チームワーク強化、コスト削減、品質向上を実現します。このサービスは、製造業の課題を深く理解し、それに対する最適なデジタルソリューションを提供することで、企業が持続的な成長とイノベーションを達成できるようサポートします。
オンライン講座
製造業、主に購買・調達部門にお勤めの方々に向けた情報を配信しております。
新任の方やベテランの方、管理職を対象とした幅広いコンテンツをご用意しております。
お問い合わせ
コストダウンが利益に直結する術だと理解していても、なかなか前に進めることができない状況。そんな時は、newjiのコストダウン自動化機能で大きく利益貢献しよう!
(Β版非公開)