- お役立ち記事
- Surface Roughness Testing and Result Management in Metal Factories
Surface Roughness Testing and Result Management in Metal Factories
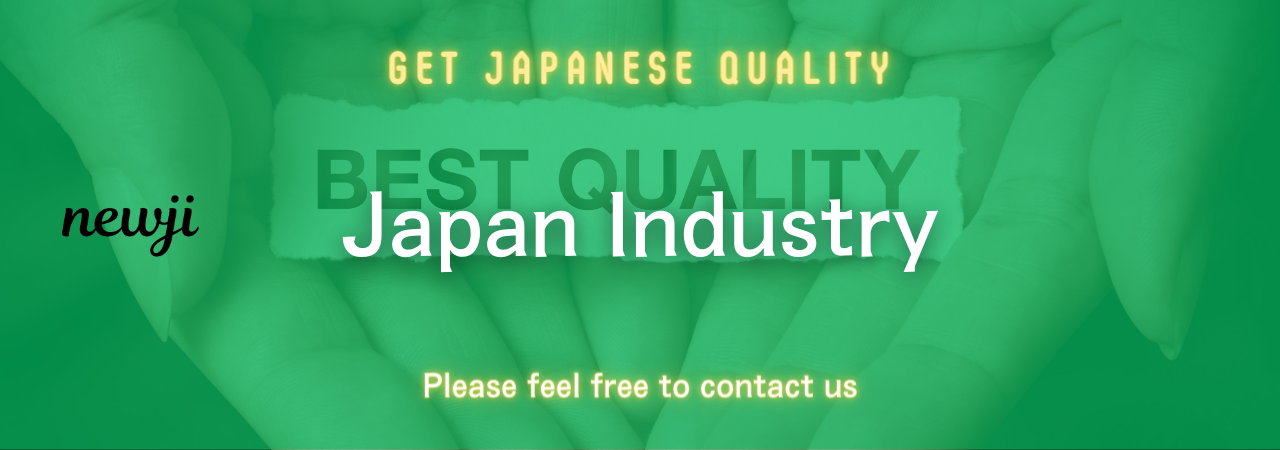
目次
Understanding Surface Roughness in Metal Factories
In metal manufacturing, ensuring the quality of the final product is crucial.
One of the key factors that contribute to the quality of metal parts is the surface roughness.
Surface roughness refers to the texture of a metal surface, characterized by its peaks and valleys.
This parameter can influence the mechanical properties, durability, and performance of metal components.
Why Surface Roughness Matters
A smooth surface can enhance the fatigue strength of a metal, making it more durable and reliable.
Conversely, a rough surface might lead to increased wear and tear, reducing the lifespan of a component.
Additionally, surface roughness can affect how two parts fit together or interact, which is critical in industries like automotive and aerospace.
Beyond mechanical properties, surface texture can also impact aesthetics and resistance to corrosion.
For products where appearance is significant, such as consumer electronics, achieving a flawless surface finish is essential.
Methods of Surface Roughness Testing
Testing surface roughness involves quantifying the texture of a metal surface.
Several methods are available in metal factories to measure surface roughness, each offering distinctive advantages.
Contact Profilometers
A contact profilometer uses a diamond-tipped stylus that moves across the metal surface to measure its texture.
As the stylus travels, it records the surface variations, which are then analyzed to determine roughness.
This method is highly accurate and suitable for a wide range of surface types.
However, it may not be ideal for very soft or delicate surfaces, as the stylus can potentially cause damage.
Optical Profilometers
Unlike contact profilometers, optical profilometers employ light to analyze surface texture.
This non-contact method is excellent for delicate surfaces that might be damaged by a stylus.
Optical profilometers can quickly gather comprehensive data, allowing for detailed analysis.
They are efficient and provide a high-resolution image of the surface, which aids in precise roughness measurement.
Atomic Force Microscopy (AFM)
Atomic force microscopy involves using a microscopic probe to scan surfaces at an atomic level.
AFM can capture a detailed three-dimensional image of the surface texture.
It’s an excellent choice for measuring extremely fine surface finishes.
Due to its high precision, AFM is often used in research and the manufacturing of microelectronics.
Interpreting Surface Roughness Results
Once the roughness data is collected, it is essential to interpret these results accurately to ensure product quality.
Parameters and Units
Surface roughness is generally expressed in terms of parameters like Ra, Rz, and Rq.
The most commonly used parameter, Ra, represents the average roughness value.
Rz measures the vertical distance between the highest peak and the lowest valley in a specific area.
Rq is the root mean square value of the surface’s profile.
Understanding these parameters helps in setting appropriate quality standards and aligning them with the desired product specifications.
Analyzing the Data
Surface roughness data needs to be analyzed in the context of the specific application.
For instance, in applications where two metal parts fit together, a lower Ra value might be desired to ensure tight tolerances.
On the other hand, if a certain level of roughness is required for adhesion purposes, a higher roughness might be acceptable.
These analyses guide adjustments in manufacturing processes to achieve the right balance between smoothness and function.
Surface Roughness Management Strategies
Managing surface roughness involves more than testing and analyzing.
It requires integrating these processes into the overall quality control framework in a factory.
Regular Monitoring
Consistent monitoring throughout the production process is vital.
Routine checks help identify potential deviations from the desired surface finish early on.
By continuously capturing data, manufacturers can maintain high-quality standards and avoid post-production defects.
Adjusting Process Parameters
To achieve the desired surface texture, it’s often necessary to adjust machining parameters.
These parameters may include the feed rate, cutting speed, or tool geometry.
Fine-tuning these settings based on surface roughness data can enhance the precision of manufacturing operations.
Employee Training and Awareness
Educating employees on the significance of surface roughness ensures better handling and execution of production processes.
When workers understand how their actions impact surface quality, they can make informed decisions to maintain and improve manufacturing standards.
Conclusion
In metal factories, surface roughness testing and result management are integral to ensuring product quality and performance.
By implementing advanced testing methods and strategic management practices, manufacturers can optimize the surface finish of metal products, leading to improved reliability and customer satisfaction.
Through ongoing commitment to excellence in surface roughness control, metal factories can achieve a competitive edge and produce components that meet the highest standards of quality.
資料ダウンロード
QCD調達購買管理クラウド「newji」は、調達購買部門で必要なQCD管理全てを備えた、現場特化型兼クラウド型の今世紀最高の購買管理システムとなります。
ユーザー登録
調達購買業務の効率化だけでなく、システムを導入することで、コスト削減や製品・資材のステータス可視化のほか、属人化していた購買情報の共有化による内部不正防止や統制にも役立ちます。
NEWJI DX
製造業に特化したデジタルトランスフォーメーション(DX)の実現を目指す請負開発型のコンサルティングサービスです。AI、iPaaS、および先端の技術を駆使して、製造プロセスの効率化、業務効率化、チームワーク強化、コスト削減、品質向上を実現します。このサービスは、製造業の課題を深く理解し、それに対する最適なデジタルソリューションを提供することで、企業が持続的な成長とイノベーションを達成できるようサポートします。
オンライン講座
製造業、主に購買・調達部門にお勤めの方々に向けた情報を配信しております。
新任の方やベテランの方、管理職を対象とした幅広いコンテンツをご用意しております。
お問い合わせ
コストダウンが利益に直結する術だと理解していても、なかなか前に進めることができない状況。そんな時は、newjiのコストダウン自動化機能で大きく利益貢献しよう!
(Β版非公開)