- お役立ち記事
- Surface treatment technology for various adherends
Surface treatment technology for various adherends
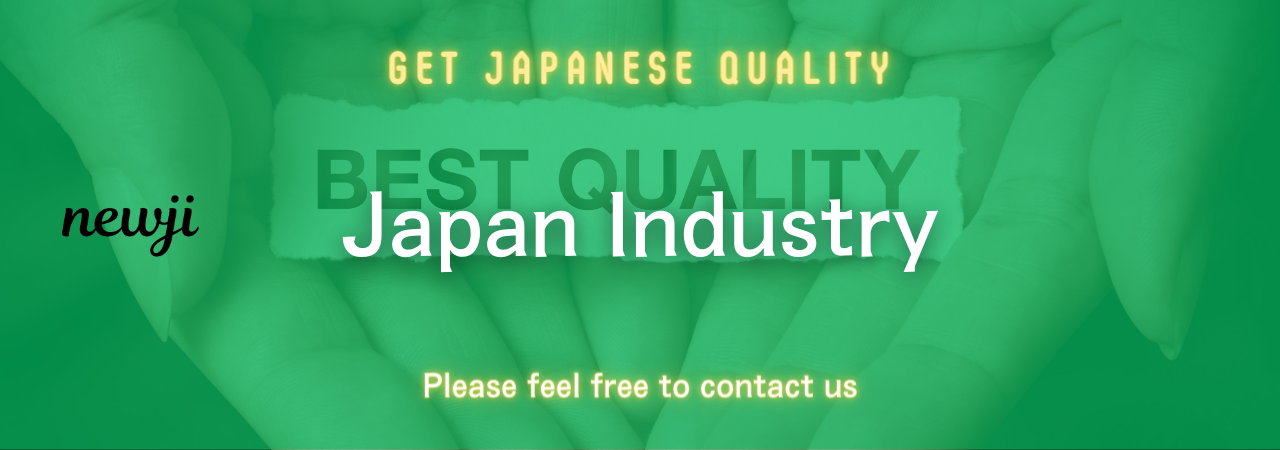
目次
Understanding Surface Treatment Technology
Surface treatment technology is an essential process used in various industries to modify the surface properties of materials without altering their core properties.
These treatments enhance the performance and lifespan of the materials, making them suitable for specific applications.
To understand how surface treatment technology works, it is helpful to explore the different methods available and their applications.
Why Surface Treatment Is Important
The main purpose of surface treatment is to improve the characteristics of an adherend, which is the material’s surface that comes into contact with other substances.
These improvements can include increased corrosion resistance, better adhesion properties, enhanced appearance, and improved durability.
By treating the surface, industries can create materials that are tailored to withstand various environmental conditions and mechanical stresses.
Types of Surface Treatment Methods
There are several methods of surface treatment, each with unique properties designed for different materials and applications.
Here are some of the most common techniques used in industries today:
1. Mechanical Surface Treatment
Mechanical surface treatment involves physically modifying a material’s surface using various tools and machines.
Common methods under mechanical treatment include:
– **Grinding**: This process involves using abrasive materials to smooth out the surface of the adherend. It is often used to prepare metal surfaces for further treatments.
– **Polishing**: Unlike grinding, polishing aims to enhance the surface’s appearance by creating a glossy finish, making it perfect for decorative purposes.
– **Sandblasting**: In this technique, sand or other abrasive materials are blasted onto the surface to clean, roughen, or remove old coatings effectively.
2. Chemical Surface Treatment
Chemical surface treatment employs chemical reactions to change the surface properties of a material.
This method is widely used in industries because of its precision and effectiveness.
Popular chemical treatments include:
– **Anodizing**: Primarily used for aluminum, anodizing is an electrolytic process that forms a protective oxide layer, enhancing corrosion resistance and allowing for dyeing in various colors.
– **Etching**: This method uses acids or bases to remove layers from a surface, creating a desired pattern or texture.
– **Passivation**: Mostly used for stainless steel, passivation involves removing free iron from the surface, forming a protective oxide layer.
3. Thermal Surface Treatment
Thermal treatment uses heat to alter the surface characteristics of a material.
It is typically used to enhance hardness and wear resistance.
Techniques include:
– **Heat Treatment**: This involves controlled heating and cooling processes to change the material properties, often used to harden metals.
– **Plasma Treatment**: Using ionized gas, plasma treatment can clean, activate, or etch a surface.
4. Coating and Plating
Applying a layer of material onto the surface of an adherend is one of the most versatile and widely used surface treatment methods.
Coating and plating offer protective, decorative, or functional enhancements.
– **Paint Coating**: Provides a colorful finish and shield against corrosion and wear.
– **Electroplating**: This electrochemical process deposits a metal layer, like chromium or nickel, onto the surface, offering increased corrosion resistance and aesthetic appeal.
– **Powder Coating**: This technique involves applying powder paint to a surface, which is then cured under heat to form a protective layer that is often more durable than traditional paint.
Applications of Surface Treatment Technology
Surface treatment technology is integral to various fields, enhancing materials’ performance according to the demands of specific applications.
Some notable applications include:
Automotive Industry
In the automotive sector, surface treatment is crucial for ensuring the durability and performance of vehicle components.
Processes like electroplating and anodizing are used to protect engine parts and improve aesthetic appeal.
Aerospace Industry
High-performance materials are essential in the aerospace industry.
Surface treatments such as passivation and anodizing are applied to increase corrosion resistance and reduce weight on aircraft components.
Construction Industry
In construction, surface treatment technologies help protect structures from environmental damage.
Coatings and galvanizing are frequently used to enhance the lifespan of materials like steel and concrete.
Electronics Industry
In electronics manufacturing, surface treatment ensures the conductivity and bonding of electronic components.
Processes such as plating help in improving connectivity and reliability.
Choosing the Right Surface Treatment
Selecting the appropriate surface treatment method requires understanding the material involved and the desired outcomes.
Each method has its advantages and suitability for particular materials and usage scenarios.
Material Consideration
Different materials respond distinctly to various surface treatments.
For example, anodizing is suitable for aluminum, but not for steel.
Understanding the specific material properties is crucial for selecting an appropriate treatment method.
Environmental Conditions
It’s essential to consider the environmental conditions that the surface will be exposed to.
For instance, materials used in outdoor applications require treatments that provide enhanced weather and corrosion resistance.
Aesthetic and Functional Requirements
In some applications, the visual appeal of the treated surface is as important as its functionality.
Polishing and painting offer aesthetic improvements, while treatments like passivation or plasma treatment may focus on enhancing functional attributes.
Conclusion
Surface treatment technology is a vital component in modern manufacturing and engineering, enhancing material performance and lifespan.
By understanding the various available methods and their applications, industries can optimize their materials for diverse environments and functions.
With advances in technology, surface treatments continue to evolve, offering even more specialized solutions to meet emerging industrial demands.
資料ダウンロード
QCD調達購買管理クラウド「newji」は、調達購買部門で必要なQCD管理全てを備えた、現場特化型兼クラウド型の今世紀最高の購買管理システムとなります。
ユーザー登録
調達購買業務の効率化だけでなく、システムを導入することで、コスト削減や製品・資材のステータス可視化のほか、属人化していた購買情報の共有化による内部不正防止や統制にも役立ちます。
NEWJI DX
製造業に特化したデジタルトランスフォーメーション(DX)の実現を目指す請負開発型のコンサルティングサービスです。AI、iPaaS、および先端の技術を駆使して、製造プロセスの効率化、業務効率化、チームワーク強化、コスト削減、品質向上を実現します。このサービスは、製造業の課題を深く理解し、それに対する最適なデジタルソリューションを提供することで、企業が持続的な成長とイノベーションを達成できるようサポートします。
オンライン講座
製造業、主に購買・調達部門にお勤めの方々に向けた情報を配信しております。
新任の方やベテランの方、管理職を対象とした幅広いコンテンツをご用意しております。
お問い合わせ
コストダウンが利益に直結する術だと理解していても、なかなか前に進めることができない状況。そんな時は、newjiのコストダウン自動化機能で大きく利益貢献しよう!
(Β版非公開)