- お役立ち記事
- Swaging methods and applications: machining techniques for complex part geometries and material cutting
Swaging methods and applications: machining techniques for complex part geometries and material cutting
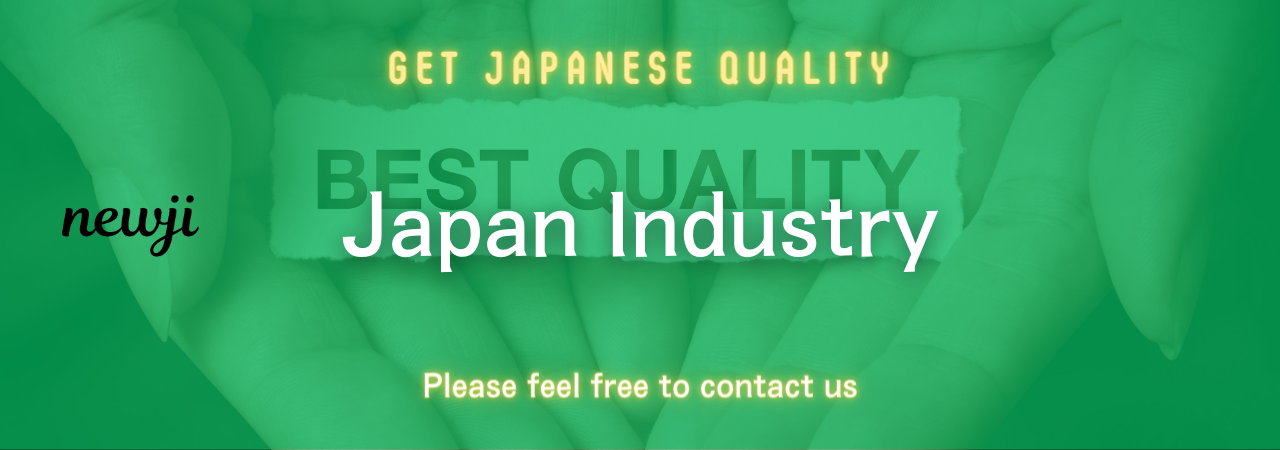
Swaging is a fascinating and versatile metalworking technique utilized in various industries to shape, join, or resize materials, primarily metals.
This article aims to delve into the methods and applications of swaging, exploring how it is employed to create complex part geometries and facilitate material cutting.
Let us break down the essentials and provide insights into this intricate process.
目次
What Is Swaging?
Swaging is a process used to deform a workpiece by applying compressive forces using a die.
The primary objective is to change the diameter or shape of the material to match specific requirements.
Unlike other machining processes, swaging does not remove material; instead, it displaces and reforms it.
This makes it a highly efficient method, as there is minimal waste.
Swaging techniques can be categorized as rotary, tube, or shear swaging, each suitable for different applications and materials.
Types of Swaging Methods
Rotary Swaging
Rotary swaging, also known as radial swaging, involves the use of dies that rotate around the workpiece.
These dies repeatedly strike and compress the material, reducing its diameter and creating a desired shape.
Rotary swaging is widely used in the aerospace and automotive industries to produce components such as drive shafts, steering components, and aircraft parts.
Tube Swaging
Tube swaging is specifically designed for forming and resizing tubular workpieces.
In this method, the tube is placed in a swaging machine, where dies compress it to achieve the desired shape.
Tube swaging is commonly used in the production of medical instruments, bicycle frames, and hydraulic tubes.
Shear Swaging
Shear swaging involves the application of shearing forces to reshape a workpiece.
This method is particularly suitable for cutting and resizing materials with high precision.
Shear swaging finds applications in industries such as electronics, where intricate and precise components are required.
Advantages of Swaging
Swaging offers several advantages that make it a preferred choice for specific machining operations.
Here are a few key benefits:
Efficiency
Swaging is a highly efficient process, as it deforms materials without removing any.
This leads to minimal material waste, making it a cost-effective solution.
Strength
Swaging improves the mechanical properties of materials by inducing strain hardening.
This results in stronger, more durable components.
Precision
Swaging allows for precise control over the dimensions and shape of the workpiece, ensuring tight tolerances are maintained.
Versatility
Swaging can be used on a variety of materials, including metals, alloys, and even some plastics.
Its versatility makes it suitable for numerous industries.
Industrial Applications of Swaging
Swaging finds applications in diverse sectors, thanks to its ability to create complex geometries and perform material cutting with high precision.
Aerospace Industry
In the aerospace industry, swaging is used to manufacture components that require high strength and precision.
Rotary swaging, in particular, is employed to produce parts like landing gear components, engine parts, and structural elements.
Automotive Industry
The automotive sector relies on swaging for the production of various components such as axles, drive shafts, and exhaust systems.
Swaging ensures these parts meet stringent performance and safety standards.
Medical Industry
Swaging plays a crucial role in the medical field, where it is used to manufacture surgical instruments, implants, and medical devices.
Tube swaging, for example, is employed to create precise and sterile instruments used in surgeries.
Electronics Industry
In the electronics industry, shear swaging is utilized to produce intricate components such as connectors, terminals, and pins.
The process ensures high precision and reliable electrical performance.
Construction Industry
Swaging is also used in the construction industry to produce structural elements such as cables, rods, and fasteners.
The technique ensures these components meet the required strength and durability standards.
Swaging Machines and Tools
To perform swaging, specialized machines and tools are required.
These machines vary in their design and functionality, depending on the type of swaging being performed.
Rotary Swaging Machines
Rotary swaging machines consist of a series of dies mounted on a rotating spindle.
The dies repeatedly strike the workpiece, gradually deforming it into the desired shape.
These machines are available in various sizes and configurations to accommodate different workpiece dimensions.
Tube Swaging Machines
Tube swaging machines are designed to handle tubular workpieces specifically.
They use dies to compress the tube uniformly, ensuring a consistent shape and diameter.
These machines are widely used in industries that require precise and reliable tubular components.
Shear Swaging Machines
Shear swaging machines are equipped with shearing tools that apply controlled forces to reshape the workpiece.
These machines are ideal for cutting and resizing materials with high precision.
They are commonly used in industries where intricate and precise components are required.
Conclusion
Swaging is a versatile and efficient metalworking process that finds applications in numerous industries.
From aerospace and automotive to medical and electronics, swaging plays a crucial role in shaping complex part geometries and facilitating material cutting.
By understanding the various methods and applications of swaging, manufacturers can harness its benefits to produce high-quality components with precision and efficiency.
As technology continues to advance, we can expect swaging techniques to evolve further, enabling even more innovative applications and pushing the boundaries of what is possible in metalworking.
資料ダウンロード
QCD調達購買管理クラウド「newji」は、調達購買部門で必要なQCD管理全てを備えた、現場特化型兼クラウド型の今世紀最高の購買管理システムとなります。
ユーザー登録
調達購買業務の効率化だけでなく、システムを導入することで、コスト削減や製品・資材のステータス可視化のほか、属人化していた購買情報の共有化による内部不正防止や統制にも役立ちます。
NEWJI DX
製造業に特化したデジタルトランスフォーメーション(DX)の実現を目指す請負開発型のコンサルティングサービスです。AI、iPaaS、および先端の技術を駆使して、製造プロセスの効率化、業務効率化、チームワーク強化、コスト削減、品質向上を実現します。このサービスは、製造業の課題を深く理解し、それに対する最適なデジタルソリューションを提供することで、企業が持続的な成長とイノベーションを達成できるようサポートします。
オンライン講座
製造業、主に購買・調達部門にお勤めの方々に向けた情報を配信しております。
新任の方やベテランの方、管理職を対象とした幅広いコンテンツをご用意しております。
お問い合わせ
コストダウンが利益に直結する術だと理解していても、なかなか前に進めることができない状況。そんな時は、newjiのコストダウン自動化機能で大きく利益貢献しよう!
(Β版非公開)