- お役立ち記事
- Symbiosis of People and Technology Human Resource Development and Skill Shift in Manufacturing DX
Symbiosis of People and Technology Human Resource Development and Skill Shift in Manufacturing DX
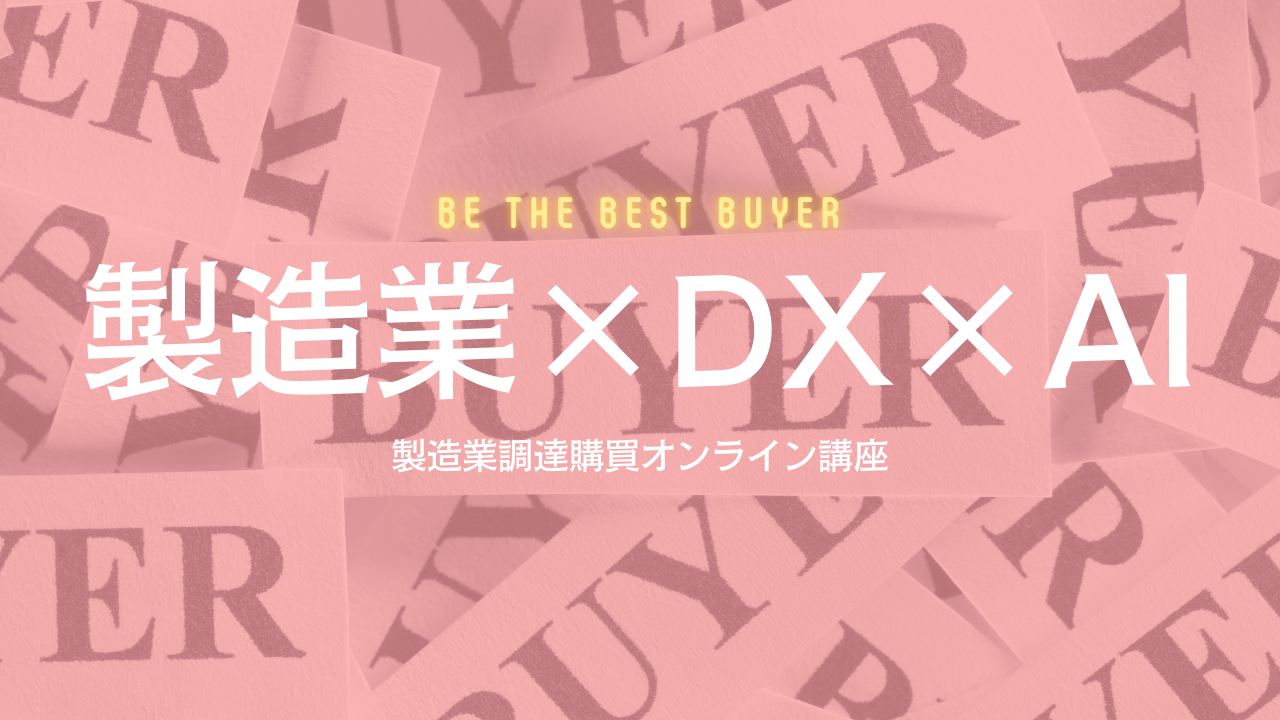
In today’s high-tech world, people and technology are becoming more and more intertwined. New technologies are constantly being developed and introduced into workplaces at a rapid pace. This trend, known as digital transformation or DX, is dramatically impacting the manufacturing industry. As machines take over routine physical and cognitive tasks, humans must adapt their skills to work alongside technology. Successful digital transformation requires strategic human resource development and a shift in the skills of the manufacturing workforce.
Robots and other automated systems are becoming common on modern production lines. They have amazing capabilities like precise movements, heavy lifting, and the ability to work continuously without breaks. This allows manufacturing processes to happen more quickly and consistently than when done solely by human workers. However, while robots excel at standardized, repetitive motions, aspects of creativity, problem-solving, and emotional intelligence remain uniquely human abilities. So as certain jobs are replaced by technology, new types of jobs focused on “human skills” are being created to support and manage the advanced systems.
There is a growing need for highly-skilled jobs like robot programmers, data analysts, predictive maintenance technicians, and digital engineers. These technology-focused roles require education and training in fields like computer science, automation, mechatronics, and coding. Employees must learn to work seamlessly with machines, using their natural human abilities to efficiently oversee and improve automated processes. Workers also need soft skills like teamwork, communication, critical thinking, and adaptability to deal with constant technological change.
To fill emerging roles and upskill current employees, manufacturers are investing heavily in human resource development through internal training programs and external educational partnerships. Company-run courses teach skills related to specific equipment, systems, and software in use at the facility. Hands-on lessons allow staff to learn new technologies on-site through demonstration and practice. Some large corporations have on-campus advanced learning centers where customized workforce development takes place.
Manufacturers also collaborate with vocational schools, community colleges, and universities to develop degree and certificate pathways focused on in-demand manufacturing technologies. This gives current and potential employees clear career roadmaps to transition into high-paying industry 4.0 jobs. Apprenticeship opportunities blend classroom learning with on-the-job training under the guidance of experienced mentors. Scholarships, tuition reimbursement, and training stipends help remove barriers to skills upgrading.
While technical aptitude is critically important, soft skills remain equally vital for human workers in a technologically advanced landscape. As robots do not require personal interaction or emotional intelligence, the ability to productively collaborate with colleagues and resolve conflicts takes on increased value. Manufacturers provide communication, problem-solving, and leadership programs to round out hardened technical competencies. Cultural sensitivity coaching readies global workforces to interact seamlessly across languages and time zones with distributed project teams.
Digital transformation is a journey, not a destination, meaning skills must continuously evolve over a career. Tools like digital badges and micro-credentials allow professionals to showcase mastery of discrete specialized topics on an ongoing basis. Robust internal mobility programs equip employees to move fluidly between functions as technologies alter job requirements within production facilities. Mid-career mentorship and coaching support perpetual learning at all levels throughout lengthy tenures. Staying abreast of changes ensures human staff remain full contributors rather than observers of Industry 4.0.
The human-machine collaboration seen in advanced manufacturing demonstrates how people and technology can empower one another in a virtuous cycle. While some jobs disappear, new types of meaningful, well-compensated employment are being generated that leverage core human capabilities alongside automation. Through substantial and sustained investment in worker training, companies successfully transition their labor forces to thrive amid digital transformation. With strategic human resource development and skill shifting, manufacturers optimize productivity from both automated systems and the people who design, maintain, and oversee intelligent production technologies. The future of industries lies in this symbiosis between humans and the machines they create.
資料ダウンロード
QCD調達購買管理クラウド「newji」は、調達購買部門で必要なQCD管理全てを備えた、現場特化型兼クラウド型の今世紀最高の購買管理システムとなります。
ユーザー登録
調達購買業務の効率化だけでなく、システムを導入することで、コスト削減や製品・資材のステータス可視化のほか、属人化していた購買情報の共有化による内部不正防止や統制にも役立ちます。
NEWJI DX
製造業に特化したデジタルトランスフォーメーション(DX)の実現を目指す請負開発型のコンサルティングサービスです。AI、iPaaS、および先端の技術を駆使して、製造プロセスの効率化、業務効率化、チームワーク強化、コスト削減、品質向上を実現します。このサービスは、製造業の課題を深く理解し、それに対する最適なデジタルソリューションを提供することで、企業が持続的な成長とイノベーションを達成できるようサポートします。
オンライン講座
製造業、主に購買・調達部門にお勤めの方々に向けた情報を配信しております。
新任の方やベテランの方、管理職を対象とした幅広いコンテンツをご用意しております。
お問い合わせ
コストダウンが利益に直結する術だと理解していても、なかなか前に進めることができない状況。そんな時は、newjiのコストダウン自動化機能で大きく利益貢献しよう!
(Β版非公開)