- お役立ち記事
- System coordination and technology development in IoT application of machine tools
月間77,185名の
製造業ご担当者様が閲覧しています*
*2025年2月28日現在のGoogle Analyticsのデータより
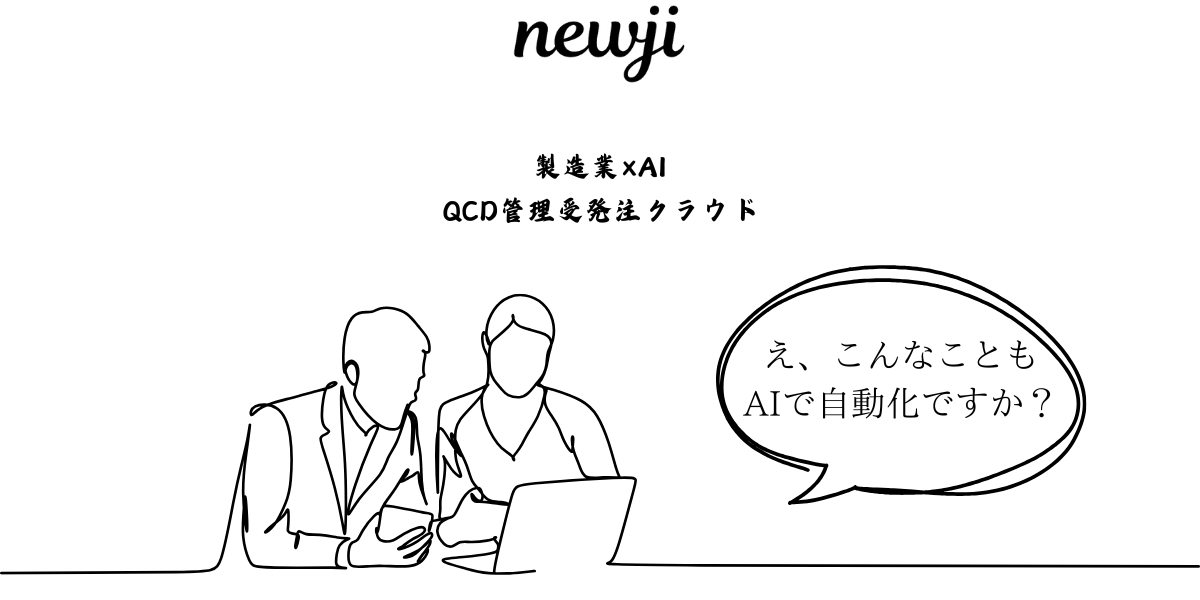
System coordination and technology development in IoT application of machine tools
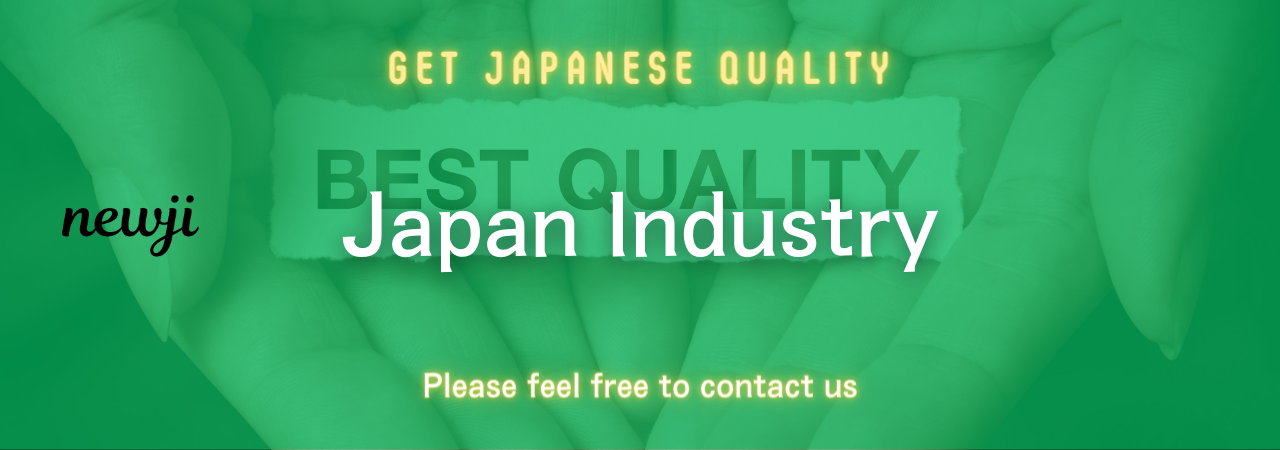
The integration of Internet of Things (IoT) with machine tools is rapidly transforming manufacturing industries. By leveraging IoT, machine tools are becoming smarter and more efficient, leading to increased productivity and reduced downtime. This article explores how system coordination and technology development are playing crucial roles in the IoT applications of machine tools.
目次
The Role of IoT in Machine Tools
The Internet of Things (IoT) refers to the interconnectedness of devices through the internet, enabling them to send and receive data. In the context of machine tools, IoT facilitates seamless communication between machines and systems, helping to optimize operations. This connectivity allows for real-time monitoring and analysis, resulting in improved decision-making and operational efficiency.
IoT enables machine tools to gather vast amounts of data, which can be used to enhance their performance. For instance, sensors embedded in machine tools can collect data on parameters such as temperature, vibration, and cycle time. This data can then be analyzed to detect anomalies and predict potential machine failures. Consequently, maintenance can be scheduled proactively, minimizing unscheduled downtime and extending the lifespan of the equipment.
System Coordination in IoT-Enabled Machine Tools
System coordination is a critical component of IoT applications in machine tools. It involves the integration and synchronization of various processes and systems to ensure optimal performance. Effective system coordination allows manufacturers to automate complex tasks, streamline workflows, and improve resource allocation.
Integration with Existing Systems
For IoT applications to be successful, they must seamlessly integrate with existing systems and processes. This involves ensuring that new IoT-enabled machine tools can communicate effectively with existing equipment and software platforms. This integration requires careful planning and execution, as well as the use of standardized protocols and interfaces.
One of the key challenges in system coordination is data interoperability. Different machines and systems may generate data in various formats, making it difficult to aggregate and analyze the information. To address this, manufacturers must adopt standardized data formats and protocols that facilitate seamless data exchange between devices.
Automation and Workflow Optimization
System coordination in IoT-enabled machine tools also involves automating repetitive tasks and optimizing workflows. Automation reduces the need for manual intervention, allowing operators to focus on more complex tasks. By streamlining workflows, manufacturers can improve productivity and reduce the risk of errors.
IoT-enabled machine tools can automatically coordinate with other systems in the manufacturing process. For example, machine tools can communicate with inventory management systems to ensure that raw materials are available when needed. This coordination helps to minimize bottlenecks and ensure a smooth production process.
Technology Development in IoT-Enabled Machine Tools
Ongoing technology development is essential for the successful implementation of IoT in machine tools. Innovations in hardware and software are driving the evolution of intelligent machines, making them more capable and versatile.
Advanced Sensors and Connectivity
The development of advanced sensors is a key driver of IoT adoption in machine tools. Modern sensors are capable of capturing a range of data points with high precision and accuracy. They are also becoming more affordable, making it feasible for manufacturers to deploy them on a larger scale.
In addition to sensors, connectivity is a crucial aspect of IoT technology development. Machine tools must be equipped with reliable communication interfaces to transmit data effectively. Wireless technologies such as Wi-Fi and Bluetooth are commonly used, allowing machines to connect to local networks and the internet.
Data Analytics and Machine Learning
Data analytics and machine learning are transforming the way manufacturers use the data collected by IoT-enabled machine tools. By applying advanced analytical techniques, manufacturers can derive valuable insights from large datasets, enabling predictive maintenance and process optimization.
Machine learning algorithms can identify patterns and correlations in data that may be difficult for humans to detect. For example, these algorithms can predict when a machine is likely to experience a fault, based on historical performance data. This allows manufacturers to perform maintenance before a failure occurs, reducing the risk of costly downtime.
Challenges and Opportunities
While the IoT applications in machine tools offer numerous benefits, they also present several challenges. Data security and privacy are primary concerns, as interconnected systems can be vulnerable to cyberattacks. Manufacturers must implement robust security measures to protect sensitive information and ensure that their networks are secure.
Additionally, the deployment of IoT solutions requires significant investment in technology and infrastructure. This can be a barrier for smaller manufacturers with limited resources. However, the long-term savings and productivity gains associated with IoT adoption often justify the initial expenditure.
The opportunities presented by IoT in machine tools are immense. By adopting these technologies, manufacturers can enhance their competitiveness and respond more effectively to changing market demands. IoT enables more agile and flexible manufacturing processes, allowing companies to customize products and reduce time-to-market.
Conclusion
The integration of IoT with machine tools is revolutionizing the manufacturing industry. System coordination and technology development are key to unlocking the full potential of IoT applications. By facilitating seamless communication, automating tasks, and enabling data-driven decision-making, IoT is helping manufacturers optimize their operations.
As technology continues to advance, the capabilities of IoT-enabled machine tools will expand, offering even greater benefits. Manufacturers that embrace IoT stand to gain significant competitive advantages, paving the way for a more efficient and innovative manufacturing landscape.
資料ダウンロード
QCD管理受発注クラウド「newji」は、受発注部門で必要なQCD管理全てを備えた、現場特化型兼クラウド型の今世紀最高の受発注管理システムとなります。
ユーザー登録
受発注業務の効率化だけでなく、システムを導入することで、コスト削減や製品・資材のステータス可視化のほか、属人化していた受発注情報の共有化による内部不正防止や統制にも役立ちます。
NEWJI DX
製造業に特化したデジタルトランスフォーメーション(DX)の実現を目指す請負開発型のコンサルティングサービスです。AI、iPaaS、および先端の技術を駆使して、製造プロセスの効率化、業務効率化、チームワーク強化、コスト削減、品質向上を実現します。このサービスは、製造業の課題を深く理解し、それに対する最適なデジタルソリューションを提供することで、企業が持続的な成長とイノベーションを達成できるようサポートします。
製造業ニュース解説
製造業、主に購買・調達部門にお勤めの方々に向けた情報を配信しております。
新任の方やベテランの方、管理職を対象とした幅広いコンテンツをご用意しております。
お問い合わせ
コストダウンが利益に直結する術だと理解していても、なかなか前に進めることができない状況。そんな時は、newjiのコストダウン自動化機能で大きく利益貢献しよう!
(β版非公開)