- お役立ち記事
- Tapping Techniques and Applications: Machining Methods for Threading and Part Assembly
月間73,982名の
製造業ご担当者様が閲覧しています*
*2025年1月31日現在のGoogle Analyticsのデータより
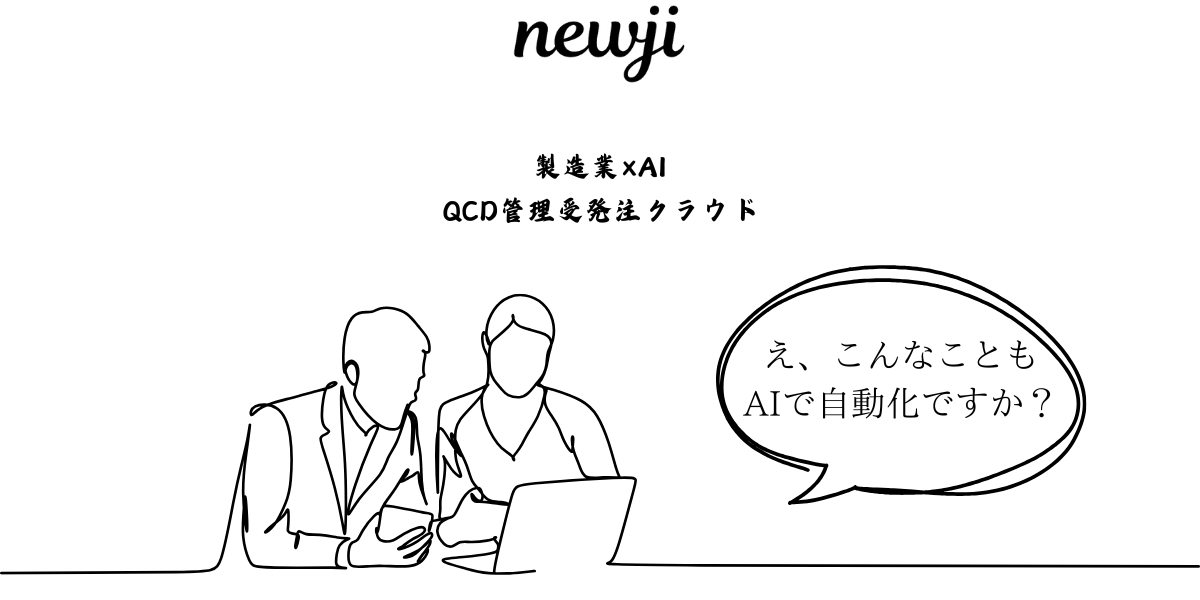
Tapping Techniques and Applications: Machining Methods for Threading and Part Assembly
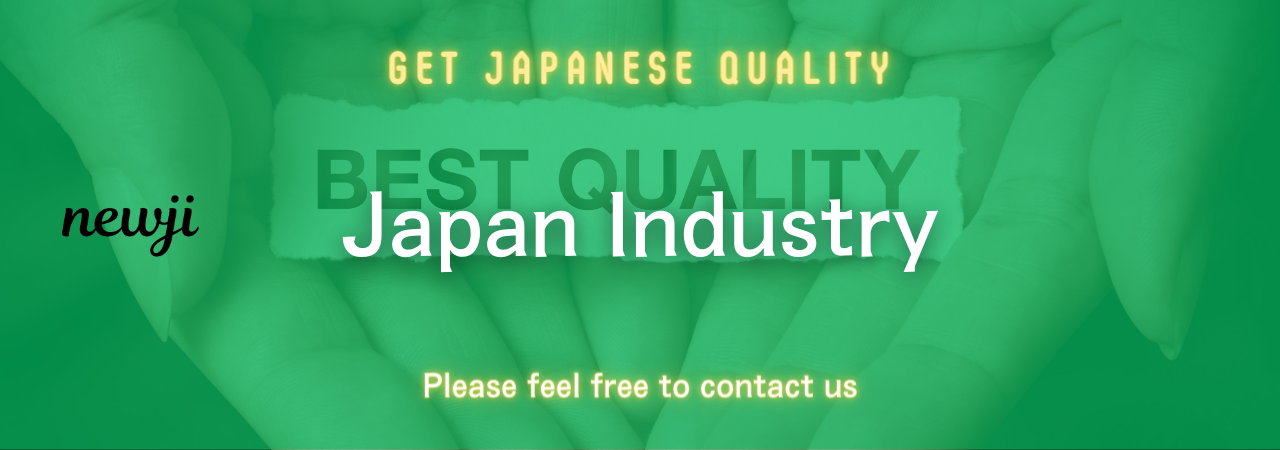
Tapping, a fundamental machining method, involves creating threads in a hole to enable the fastening of bolts or screws. Mastering tapping techniques and applications is essential for precision manufacturing and ensures the longevity and reliability of assembled parts. This article delves into the core aspects of tapping, highlighting its significance, techniques, and practical applications.
目次
Understanding Tapping and Its Importance
Tapping is a process that produces threads inside drilled holes, allowing the insertion of screws or bolts. This threading method is critical in various industries, including automotive, aerospace, and electronics, due to its capability to join components securely.
Threads created by tapping provide the essential grip for fasteners, which is crucial for the structural integrity and functionality of assembled products. From securing engine components to assembling electronic devices, the precision of tapped threads ensures parts remain tightly connected, reducing the risk of loosening or failure during operation.
Key Tapping Techniques
Several tapping techniques are employed based on the material, hole type, and desired thread specifications. Understanding these techniques is pivotal to achieving optimal results in different machining contexts.
1. Hand Tapping: This traditional method involves using a tap wrench to manually turn the tap into the hole. While suitable for small-scale or low-volume work, hand tapping requires a skilled operator to maintain alignment and avoid damaging the threads.
2. Machine Tapping: Common in modern manufacturing, machine tapping ensures consistent, high-quality threads. It uses automated machinery to drive the tap into the hole, ideal for high-volume production. Machine tapping minimizes human error and offers superior precision.
3. Form Tapping: Unlike cutting taps, form taps create threads by displacing material rather than cutting it. This method is perfect for soft materials like aluminum or copper, as it produces stronger threads and reduces the risk of chipping.
4. Spiral Flute Tapping: Specifically designed for threading blind holes, spiral flute taps efficiently remove chips from the hole, preventing clogging and breakage. This technique is beneficial in applications where chips must be evacuated upwards.
5. Interrupted Thread Tapping: This technique features an interrupted or staggered thread design, reducing tap friction and heat buildup. It’s effective for materials prone to sticking, like stainless steel, and helps extend tap lifespan.
Choosing the Right Tap
Selecting an appropriate tap for the specific application is crucial. Factors like material hardness, hole diameter, and thread tolerance determine the type of tap to use.
1. Material Compatibility: Different tap materials and coatings are optimized for specific materials. High-speed steel (HSS) taps work well for softer materials, while cobalt or carbide taps are needed for harder metals.
2. Thread Class: Taps come in various thread classes (Unified National (UN) or Metric (M)), each suited for different tolerance levels. Choosing the right thread class ensures a proper fit and optimal thread engagement.
3. Hole Type: The nature of the hole (blind or through) influences tap selection. Spiral flute taps are ideal for blind holes, while straight flute taps excel in through holes, where chip removal isn’t a concern.
Applications of Tapping in Manufacturing
Tapping finds extensive applications across industries, primarily in assembling components where secure fastenings are imperative.
1. Automotive Industry: In automotive manufacturing, tapping ensures the reliability of critical components like engine blocks, transmission housings, and chassis parts. Properly tapped threads withstand high torque and vibrations, essential for vehicle safety and performance.
2. Aerospace Sector: Precision is paramount in aerospace technology. Tapping is used to assemble structural components, landing gear, and avionics. The aerospace sector’s stringent quality standards underscore the importance of accurate and robust threads.
3. Electronics Industry: Miniaturization in electronics demands precise threading for small screws and fasteners. Tapping is key in assembling circuit boards, enclosures, and connectors, where even minute deviations can affect functionality.
4. Medical Devices: Accurate threading is vital in medical device manufacturing for assembling surgical instruments, implants, and diagnostic equipment. Tapped threads ensure secure connections in critical healthcare applications.
5. Construction and Infrastructure: Tapping is employed to assemble heavy equipment, scaffolding, and structural frameworks. Strong, reliable threads are crucial to ensure the integrity and safety of large-scale construction projects.
Enhancing Tapping Efficiency
Efficiency in tapping operations directly impacts production speed and cost. Implementing best practices and advanced technologies can significantly enhance tapping efficiency.
1. Lubrication and Cooling: Using appropriate lubricants reduces friction and heat during tapping, prolonging tool life and improving thread quality. Coolants also help dissipate heat and remove chips effectively.
2. High-Performance Taps: Investing in high-performance taps, designed for specific materials and applications, increases tap life and maintains thread quality. Coated taps, like TiN or TiCN, offer superior wear resistance.
3. Tool Monitoring Systems: Automated tool monitoring systems detect tap wear and breakage in real-time, preventing damage to workpieces and minimizing downtime. These systems enhance overall process reliability.
4. Advanced CNC Machines: Modern CNC (Computer Numerical Control) machines equipped with tapping cycles automate the process, ensuring consistent thread quality and reducing human intervention. Multi-axis machining centers further enhance tapping capabilities for complex components.
Mastering tapping techniques and applications is crucial for precision manufacturing, ensuring the reliability and longevity of assembled parts. From hand tapping to high-speed machine tapping, understanding the nuances of various methods and choosing the right tap is essential for optimal results. Tapping’s widespread applications across industries underline its importance in achieving secure, accurate, and durable threaded connections. Embracing advanced technologies and best practices further enhances tapping efficiency, contributing to the overall productivity and quality of manufacturing processes.
資料ダウンロード
QCD管理受発注クラウド「newji」は、受発注部門で必要なQCD管理全てを備えた、現場特化型兼クラウド型の今世紀最高の受発注管理システムとなります。
ユーザー登録
受発注業務の効率化だけでなく、システムを導入することで、コスト削減や製品・資材のステータス可視化のほか、属人化していた受発注情報の共有化による内部不正防止や統制にも役立ちます。
NEWJI DX
製造業に特化したデジタルトランスフォーメーション(DX)の実現を目指す請負開発型のコンサルティングサービスです。AI、iPaaS、および先端の技術を駆使して、製造プロセスの効率化、業務効率化、チームワーク強化、コスト削減、品質向上を実現します。このサービスは、製造業の課題を深く理解し、それに対する最適なデジタルソリューションを提供することで、企業が持続的な成長とイノベーションを達成できるようサポートします。
製造業ニュース解説
製造業、主に購買・調達部門にお勤めの方々に向けた情報を配信しております。
新任の方やベテランの方、管理職を対象とした幅広いコンテンツをご用意しております。
お問い合わせ
コストダウンが利益に直結する術だと理解していても、なかなか前に進めることができない状況。そんな時は、newjiのコストダウン自動化機能で大きく利益貢献しよう!
(β版非公開)