- お役立ち記事
- Technical approach and supplier selection for manufacturing and mass production of brackets with protrusions
月間77,185名の
製造業ご担当者様が閲覧しています*
*2025年2月28日現在のGoogle Analyticsのデータより
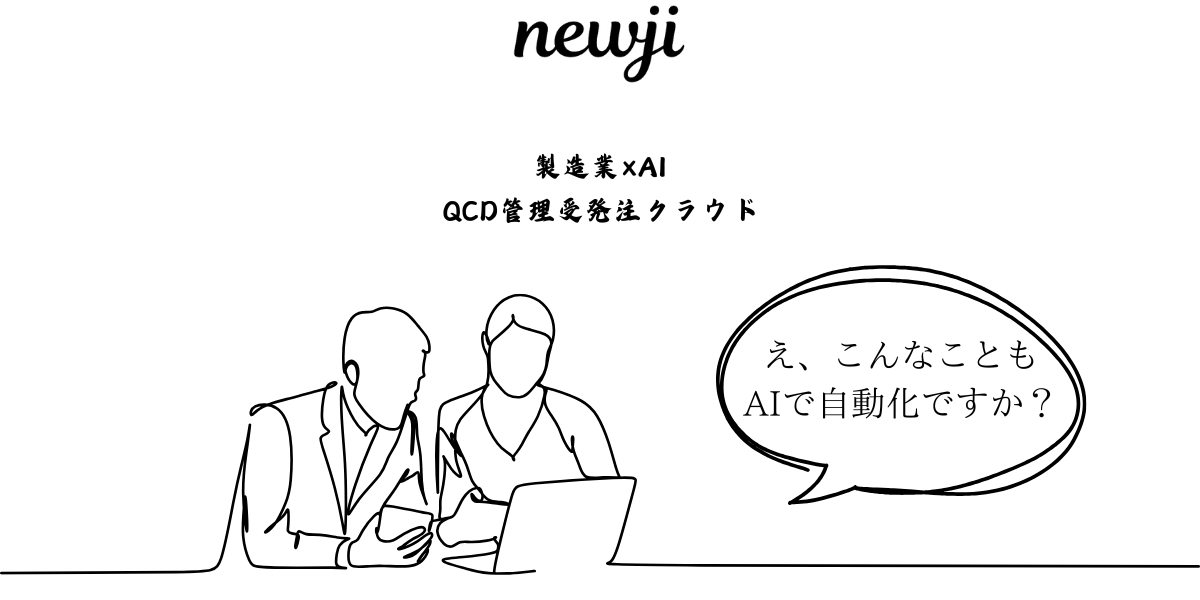
Technical approach and supplier selection for manufacturing and mass production of brackets with protrusions
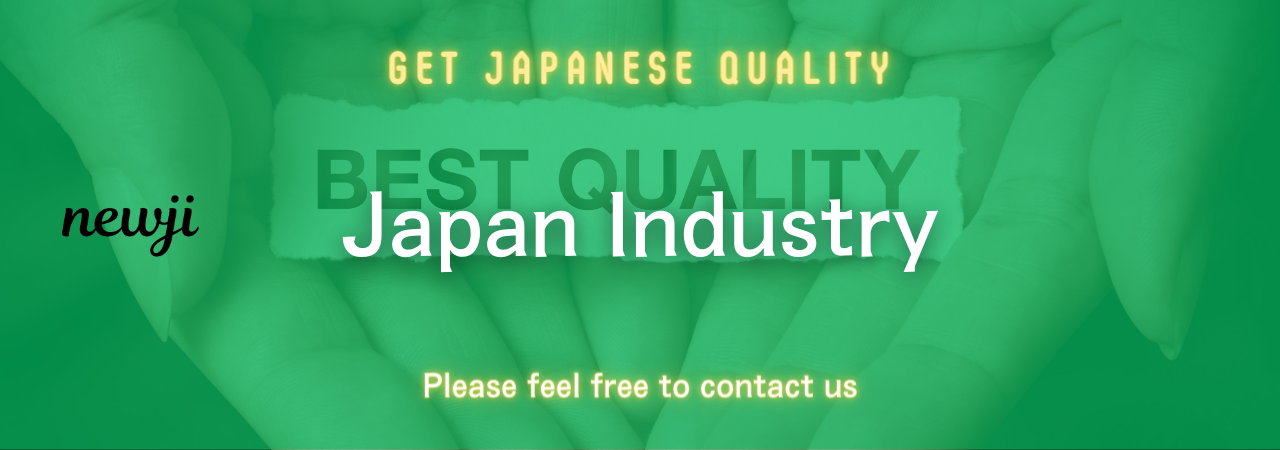
目次
Understanding the Basics of Brackets with Protrusions
Brackets with protrusions are essential components in various industries, providing a secure and stable means to support or join different parts.
These brackets are often used in engineering and construction, where their unique design allows for additional support and strength.
The protrusions help in distributing weight and reducing stress on specific points, enhancing overall durability.
Before diving into the manufacturing process, it’s important to understand the specific requirements of these brackets.
Various factors such as size, material, and specific design features play a critical role.
The materials used in manufacturing these brackets could range from metals like steel and aluminum to plastics, depending on the application and required strength levels.
Understanding the primary use of your brackets, whether in automotive, construction, electronics, or other sectors, is crucial.
This ensures that the design meets both the functional and regulatory standards expected in each industry.
Proper planning and design consideration can significantly impact the efficiency of the production process and the functionality of the final product.
The Manufacturing Process for Brackets with Protrusions
The manufacturing process of brackets with protrusions typically involves several key stages.
This includes design, prototyping, and mass production.
Each stage demands a technical approach to ensure quality and efficiency.
Designing the Bracket
The design phase is crucial, as it forms the foundation for the entire manufacturing process.
Design involves creating detailed schematics, accounting for both functional and aesthetic considerations.
Utilizing CAD (Computer-Aided Design) software, engineers can create precise models of the bracket.
This allows for testing of the design under various simulated conditions, ensuring that the bracket will perform as expected.
Designers also need to consider the best method for incorporating protrusions.
This can be through forging, casting, or welding, and each method has specific benefits and drawbacks.
Choosing the right method affects the bracket’s final strength and durability.
Prototyping and Testing
After finalizing the design, manufacturers create prototypes.
Prototyping serves as a crucial proof of concept, offering a tangible version of the blueprint.
It provides the opportunity to test the design under real-world conditions, checking for potential weaknesses or areas for improvement.
Testing is vital to ensure that the bracket can withstand the stresses it may encounter during its lifecycle.
It involves assessing aspects such as load capacity, wear resistance, and corrosion resistance.
Feedback from this stage is essential, allowing designers to make necessary adjustments before proceeding to full-scale production.
Mass Production Techniques
Once the prototype has been tested and approved, the process moves on to mass production.
This stage involves selecting the most efficient and cost-effective manufacturing techniques.
Common methods include CNC machining, stamping, and injection molding, depending on the material and design of the bracket.
CNC machining is ideal for metal brackets.
It offers precision and flexibility in production, allowing detailed and intricate designs to be produced with consistency.
Stamping is suitable for creating high volumes quickly, although it may have limitations in terms of design complexity.
For plastic brackets, injection molding is commonly used.
It allows manufacturers to produce large quantities efficiently, maintaining uniform quality across each piece.
Selecting the Right Supplier
Choosing the right supplier for manufacturing brackets with protrusions is a critical step that can significantly impact the quality and cost of production.
Several factors should be considered when selecting a supplier.
Experience and Expertise
A supplier’s experience and expertise are paramount.
They should have a proven track record of working with similar products and materials.
An experienced supplier will not only produce high-quality parts but will also offer valuable insights into design improvements and cost-saving measures.
Quality Assurance Practices
Quality assurance is non-negotiable in mass production.
Suppliers should have robust quality control systems in place to ensure that each batch of brackets meets the required standards.
This includes regular inspections and testing protocols at different stages of the production process.
Capacity and Flexibility
It is vital to ensure that your chosen supplier has the capacity to meet your production demands, both in terms of volume and deadlines.
Flexibility is also important if there are changes in demand or design requirements.
A supplier with flexible production capabilities can quickly adapt without compromising on quality or lead time.
Cost-Effectiveness
While price should not be the only consideration, it is an important factor.
The supplier should provide competitive pricing without sacrificing quality.
This involves evaluating not only the upfront costs but also long-term value, including warranties and service agreements.
Ensuring a Successful Partnership
Establishing a successful partnership with a supplier requires more than just choosing the right one.
Effective communication, consistent quality checks, and a collaborative approach are key to maintaining a productive relationship.
Regular meetings and updates can help address any issues that arise promptly, ensuring that the production process remains smooth and efficient.
In conclusion, the manufacturing and mass production of brackets with protrusions involve a comprehensive approach.
From design to prototyping, and through to supplier selection, each stage is interconnected and critical to producing a high-quality, functional product.
By understanding these elements, businesses can ensure efficiency, quality, and cost-effectiveness in their production efforts.
資料ダウンロード
QCD管理受発注クラウド「newji」は、受発注部門で必要なQCD管理全てを備えた、現場特化型兼クラウド型の今世紀最高の受発注管理システムとなります。
ユーザー登録
受発注業務の効率化だけでなく、システムを導入することで、コスト削減や製品・資材のステータス可視化のほか、属人化していた受発注情報の共有化による内部不正防止や統制にも役立ちます。
NEWJI DX
製造業に特化したデジタルトランスフォーメーション(DX)の実現を目指す請負開発型のコンサルティングサービスです。AI、iPaaS、および先端の技術を駆使して、製造プロセスの効率化、業務効率化、チームワーク強化、コスト削減、品質向上を実現します。このサービスは、製造業の課題を深く理解し、それに対する最適なデジタルソリューションを提供することで、企業が持続的な成長とイノベーションを達成できるようサポートします。
製造業ニュース解説
製造業、主に購買・調達部門にお勤めの方々に向けた情報を配信しております。
新任の方やベテランの方、管理職を対象とした幅広いコンテンツをご用意しております。
お問い合わせ
コストダウンが利益に直結する術だと理解していても、なかなか前に進めることができない状況。そんな時は、newjiのコストダウン自動化機能で大きく利益貢献しよう!
(β版非公開)