- お役立ち記事
- Technical approach to FIB circuit modification in semiconductor integrated circuit analysis work
月間77,185名の
製造業ご担当者様が閲覧しています*
*2025年2月28日現在のGoogle Analyticsのデータより
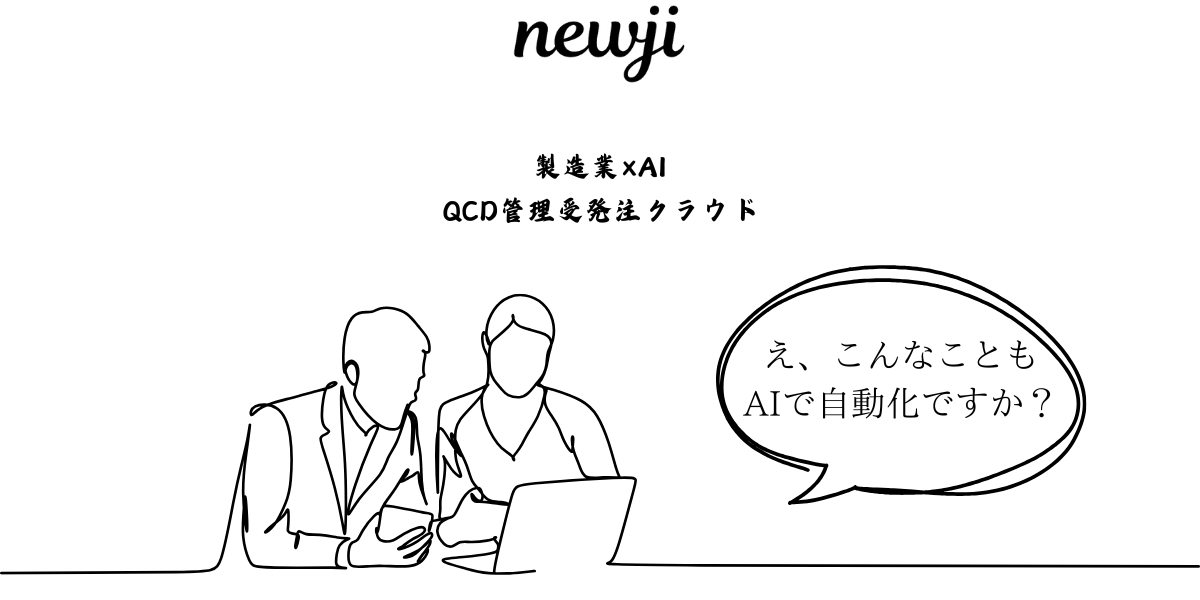
Technical approach to FIB circuit modification in semiconductor integrated circuit analysis work
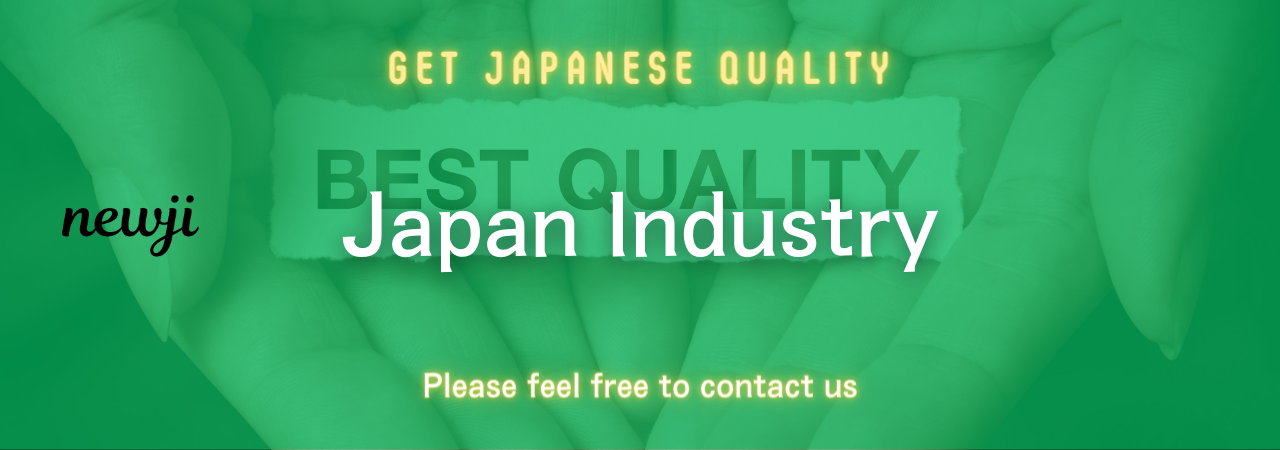
目次
Introduction to FIB Circuit Modification
Focused Ion Beam (FIB) technology has revolutionized the way we approach semiconductor integrated circuit analysis and modification.
It’s a powerful technique that allows precise sculpting and examination of tiny structures at the nanometer scale.
This capability is crucial for understanding, analyzing, and modifying semiconductor devices without the need for photolithographic masks.
In the vast field of semiconductor research and development, FIB circuit modification plays a significant role.
Its applications range from defect analysis and failure diagnosis to circuit modification and prototype testing.
By understanding FIB, engineers and researchers can push the boundaries of what’s possible in semiconductor technology.
How FIB Technology Works
FIB technology operates using a focused beam of ions, typically gallium ions, to etch materials at a microscopic level.
This ion beam is concentrated and directed at the target area on a semiconductor wafer or IC (integrated circuit) to perform precise cutting, deposition, or analysis.
The key component of a FIB system is its ability to precisely control the ion beam to manipulate structures with nanometer precision.
When the ion beam strikes the surface of the IC, it sputters away the material, thereby allowing selective removal of layers or even the modification of the circuit pathways.
The process starts with imaging, where a secondary electron detector creates an image by collecting low-energy electrons emitted from the surface due to ion impact.
This provides real-time visualization, crucial for guiding subsequent modifications.
This method’s precision makes it indispensable in various semiconductor applications.
Applications in Semiconductor Analysis
FIB circuit modification is instrumental in several aspects of semiconductor analysis.
One primary application is defect analysis.
When a semiconductor device fails, pinpointing defects is crucial to understand the breakdown process.
FIB can help isolate and expose specific layers of the IC, revealing the exact spots of failure.
Another significant application is failure diagnosis.
FIB allows engineers to modify circuits post-production to test hypotheses on potential fixes.
It’s a valuable tool for diagnosing faults in semiconductor devices, offering insights into redesign and enhancing reliability before mass production.
Moreover, FIB is crucial for inline process monitoring.
Manufacturers can use it for routine inspections to ensure product quality.
By identifying issues early in the production process, companies can minimize waste and improve yield.
FIB in Prototyping and Development
Prototyping new semiconductor devices involves considerable challenges.
FIB technology eases these challenges by enabling rapid modification and testing of circuit designs.
Through FIB, engineers can reroute connections, add or remove specific components, and validate design changes quickly without having to fabricate a new batch of circuits.
This capability is particularly beneficial for industries that require quick turnaround times for product development and innovation.
It ensures that updates and improvements can be tested and implemented promptly, maintaining a competitive edge.
In development, FIB also aids in creating custom chip modifications tailored to specific research needs.
For example, devices used for experimental research can be modified on-demand to incorporate new functions or test new concepts, providing a versatile platform for innovation.
Challenges and Considerations
Despite its advantages, FIB circuit modification is not without challenges.
The process is intricate and requires expertise to avoid unintended damage to the delicate semiconductor structures.
Overexposure to the ion beam can lead to issues such as redeposition of sputtered material, contaminating the sample and impairing functionality.
Additionally, the cost of FIB equipment and the need for highly skilled operators represent significant investments.
Thus, careful consideration must be given to the feasibility and economic viability of using FIB for specific applications.
Moreover, the process is time-consuming for large-scale modifications due to its focused, localized approach.
This aspect makes it more suitable for small-scale, precision adjustments rather than extensive circuit redesigns.
Future Directions of FIB Technology
As semiconductor devices continue to shrink and evolve, the demand for precise and efficient investigation tools like FIB is expected to grow.
Future advancements may include improvements in ion source technology, which could enhance beam precision and reduce modification times.
There’s also ongoing research into expanding FIB capabilities with dual-beam systems that integrate scanning electron microscopy (SEM).
Such advancements could provide more comprehensive analysis by combining the imaging power of SEM with the modification capability of FIB.
Increasing automation within FIB systems is another promising direction.
Enhancing software algorithms for automated defect detection and correction can streamline workflows and reduce reliance on human expertise.
Incorporating machine learning and artificial intelligence could further revolutionize FIB technology, making it more adaptive and efficient in handling complex semiconductor analysis tasks.
Conclusion
In conclusion, FIB circuit modification is a crucial tool in the semiconductor industry’s toolkit.
Its ability to perform precise alterations and analysis at the nanoscale is invaluable in a field where every atom counts.
Despite some challenges, its role in defect analysis, failure diagnosis, and accelerated prototyping makes it an essential part of modern semiconductor research and development.
As technology advances, FIB is poised to remain at the forefront, continuously aiding in the evolution of semiconductor technologies and paving the way for future innovations.
資料ダウンロード
QCD管理受発注クラウド「newji」は、受発注部門で必要なQCD管理全てを備えた、現場特化型兼クラウド型の今世紀最高の受発注管理システムとなります。
ユーザー登録
受発注業務の効率化だけでなく、システムを導入することで、コスト削減や製品・資材のステータス可視化のほか、属人化していた受発注情報の共有化による内部不正防止や統制にも役立ちます。
NEWJI DX
製造業に特化したデジタルトランスフォーメーション(DX)の実現を目指す請負開発型のコンサルティングサービスです。AI、iPaaS、および先端の技術を駆使して、製造プロセスの効率化、業務効率化、チームワーク強化、コスト削減、品質向上を実現します。このサービスは、製造業の課題を深く理解し、それに対する最適なデジタルソリューションを提供することで、企業が持続的な成長とイノベーションを達成できるようサポートします。
製造業ニュース解説
製造業、主に購買・調達部門にお勤めの方々に向けた情報を配信しております。
新任の方やベテランの方、管理職を対象とした幅広いコンテンツをご用意しております。
お問い合わせ
コストダウンが利益に直結する術だと理解していても、なかなか前に進めることができない状況。そんな時は、newjiのコストダウン自動化機能で大きく利益貢献しよう!
(β版非公開)