- お役立ち記事
- Technical elements that should be suppressed through consideration of laminating processing conditions and prototype production
月間77,185名の
製造業ご担当者様が閲覧しています*
*2025年2月28日現在のGoogle Analyticsのデータより
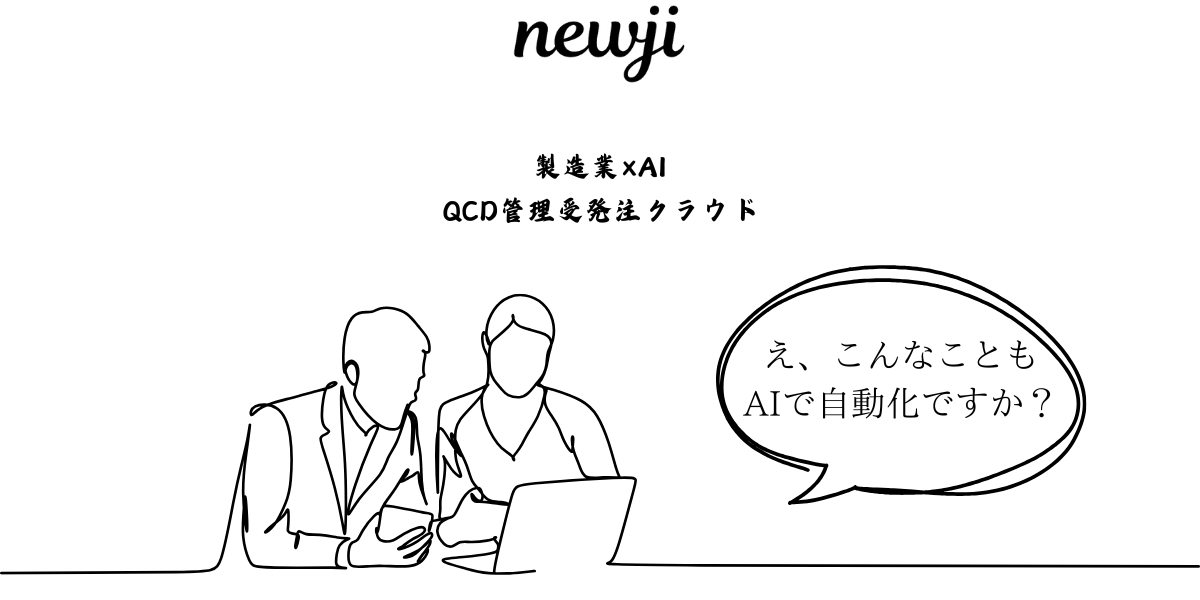
Technical elements that should be suppressed through consideration of laminating processing conditions and prototype production
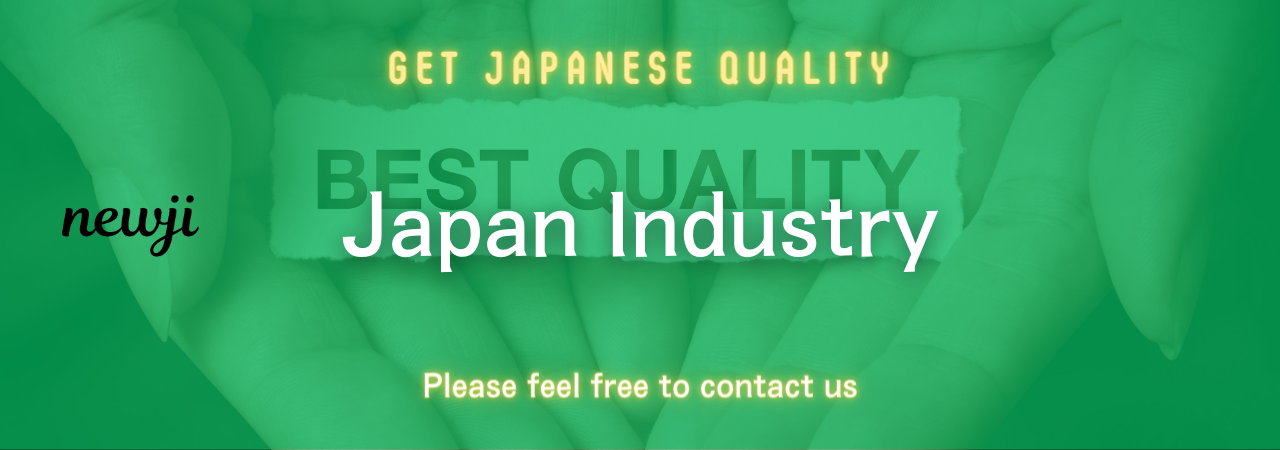
目次
Understanding Laminating Processing
Laminating processing is a manufacturing technique widely used across various industries.
It involves bonding multiple layers of material together to form a solid and stable composite.
This process enhances the durability, appearance, and functionality of products by protecting them against wear and environmental damage.
To achieve the best laminating results, careful consideration of processing conditions and prototype production is crucial.
Key Factors in Laminating Processing
There are several technical elements to consider when embarking on laminating processing.
These include temperature, pressure, time, and material compatibility.
Temperature
Temperature is a critical factor in laminating processing.
Each material responds differently to heat, and the optimal temperature can vary significantly depending on the materials used.
It is essential to ensure that the temperature is high enough to facilitate bonding without causing damage.
Too much heat can warp or degrade the materials, while too little will prevent proper adhesion.
Pressure
Pressure is equally important in laminating.
The right amount of pressure ensures that all layers are uniformly bonded, eliminating any air bubbles and creating a seamless finish.
Both excessive and insufficient pressure can lead to defects in the final product.
Therefore, understanding the correct pressure settings for your materials is crucial for successful lamination.
Time
Time is another significant component of the laminating process.
The duration for which heat and pressure are applied affects the bonding strength between layers.
If the time is too short, the bond may not fully develop, leading to separation over time.
Conversely, excessive exposure can cause material degradation.
Balancing time with the other conditions is crucial for a quality lamination process.
Material Compatibility
Not all materials are compatible in a laminating process.
It is vital to choose materials that can be bonded together without adverse reactions.
This often involves testing different combinations to find those that adhere well and produce a high-quality product.
Material testing can eliminate compatibility issues early in the prototype phase and ensure the final product meets quality standards.
Prototype Production
Prototype production is an essential step in refining the laminating process.
Creating a prototype allows manufacturers to test different laminating conditions and make adjustments as necessary.
Prototypes help identify which settings and materials yield the best results before full-scale production begins.
Testing and Evaluation
When developing a prototype, it is important to conduct rigorous testing.
Evaluate how the materials behave under different temperatures, pressures, and durations.
This testing phase will highlight any potential issues and guide adjustments to processing conditions.
Iterative Refinement
Prototypes offer a chance for iterative refinement.
Manufacturers can repeatedly adjust and test the laminating process until they achieve the desired result.
This trial and error approach ensures that the final product will be robust, reliable, and of high quality.
Cost and Efficiency Considerations
Prototype production also aids in optimizing cost and efficiency.
Through testing, manufacturers can determine the most cost-effective materials and process settings.
This optimization helps reduce waste and improve production efficiency when moving to full-scale manufacturing.
Quality Control in Laminating
Implementing quality control measures is essential throughout the laminating process.
These measures prevent defects and ensure consistency in the final products.
Inspection at Every Stage
Quality control should occur at multiple stages of the laminating process.
This includes inspecting material quality, verifying settings for temperature and pressure, and checking the final lamination’s appearance and integrity.
Regular inspections help identify and correct issues before they become significant problems.
Automated Systems
Where possible, integrating automated systems can enhance quality control.
These systems can monitor and adjust the laminating conditions in real-time, maintaining optimal settings throughout production.
Automation helps increase efficiency, reduce human error, and improve overall product quality.
Conclusion
By understanding and carefully controlling the key technical elements in laminating processing, manufacturers can produce high-quality, durable products.
Prototype production plays a critical role in identifying optimal conditions and ensuring material compatibility.
With thorough testing, iterative refinement, and robust quality control measures, the laminating process can be finely tuned for exceptional results.
Attention to these details will lead to cost-effective, efficient production and products that stand the test of time.
資料ダウンロード
QCD管理受発注クラウド「newji」は、受発注部門で必要なQCD管理全てを備えた、現場特化型兼クラウド型の今世紀最高の受発注管理システムとなります。
ユーザー登録
受発注業務の効率化だけでなく、システムを導入することで、コスト削減や製品・資材のステータス可視化のほか、属人化していた受発注情報の共有化による内部不正防止や統制にも役立ちます。
NEWJI DX
製造業に特化したデジタルトランスフォーメーション(DX)の実現を目指す請負開発型のコンサルティングサービスです。AI、iPaaS、および先端の技術を駆使して、製造プロセスの効率化、業務効率化、チームワーク強化、コスト削減、品質向上を実現します。このサービスは、製造業の課題を深く理解し、それに対する最適なデジタルソリューションを提供することで、企業が持続的な成長とイノベーションを達成できるようサポートします。
製造業ニュース解説
製造業、主に購買・調達部門にお勤めの方々に向けた情報を配信しております。
新任の方やベテランの方、管理職を対象とした幅広いコンテンツをご用意しております。
お問い合わせ
コストダウンが利益に直結する術だと理解していても、なかなか前に進めることができない状況。そんな時は、newjiのコストダウン自動化機能で大きく利益貢献しよう!
(β版非公開)