- お役立ち記事
- Technical Explanation of Displacement Sensors and Their Value in Industry
月間76,176名の
製造業ご担当者様が閲覧しています*
*2025年3月31日現在のGoogle Analyticsのデータより
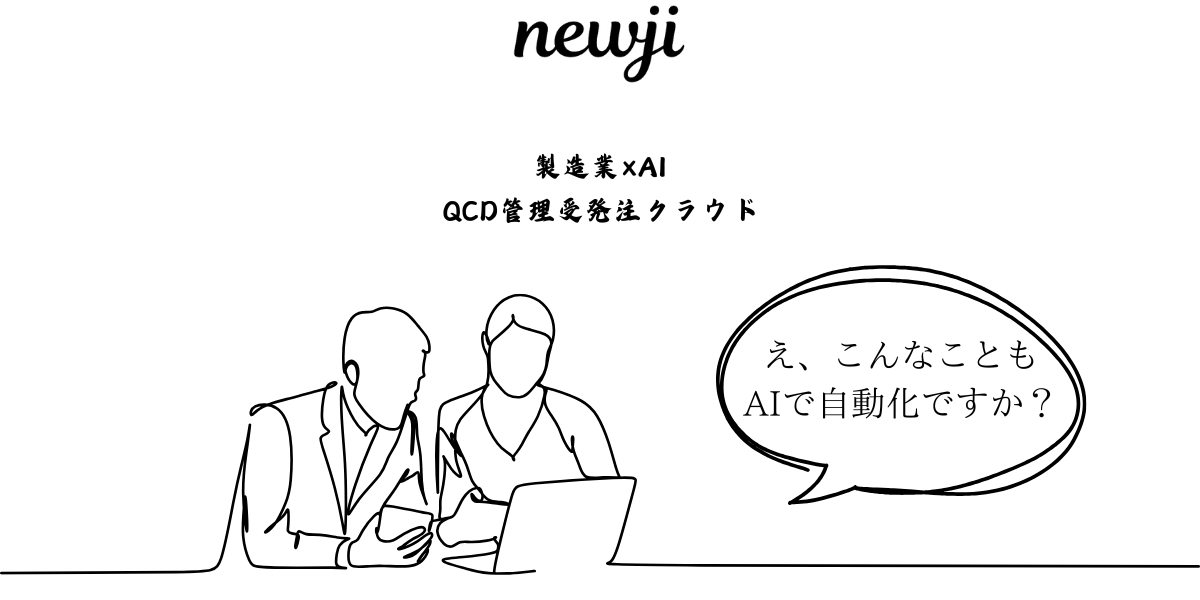
Technical Explanation of Displacement Sensors and Their Value in Industry
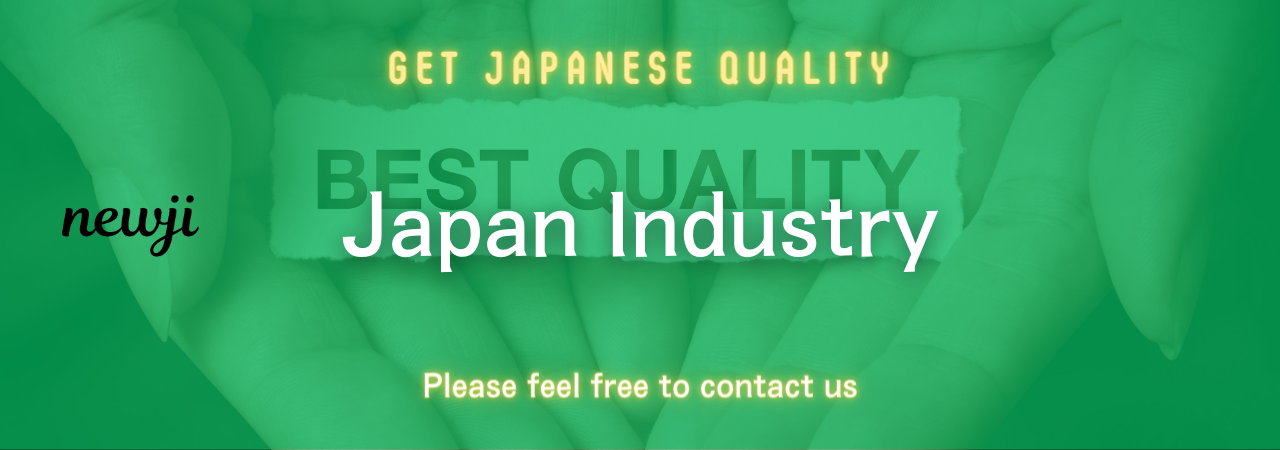
Displacement sensors are essential devices in various industries, providing critical data that help in monitoring and controlling production processes. These sensors measure the physical movement of an object, typically in terms of distance or position, with exceptional accuracy. Let’s delve into a technical understanding of displacement sensors and explore their significant role in the industrial landscape.
目次
Understanding Displacement Sensors
Displacement sensors, also known as position sensors, are devices used to detect and measure the movement or displacement of an object. These measurements can be absolute, indicating the exact position of the object, or relative, indicating the change in position from a reference point. The core function of these sensors is to convert physical movement into a readable electrical signal.
There are several types of displacement sensors, each employing different principles and technologies. Some common types include:
1. Linear Variable Differential Transformers (LVDT):
LVDTs are electromagnetic devices that measure linear displacement. They consist of a primary coil, two secondary coils, and a movable core. When an alternating current is applied to the primary coil, it induces voltages in the secondary coils. The displacement of the core changes the electromagnetic balance, causing a differential voltage output that is proportional to the core’s position.
2. Capacitive Sensors:
These sensors measure changes in capacitance between a sensor plate and a target. The capacitance varies as the distance between the two surfaces changes, which can be translated into a displacement measurement. Capacitive sensors are highly sensitive and suitable for measuring small displacements with high precision.
3. Inductive Sensors:
Inductive sensors use electromagnetic fields to detect the presence or movement of metallic objects. They are often employed to measure linear or angular displacement by detecting changes in inductance caused by the movement of the target near the sensor coil.
4. Optical Sensors:
Optical displacement sensors use light beams, often lasers, to measure the position of an object. The light beam reflects off the target surface, and the sensor’s receiver detects the reflected light. The time it takes for the light to travel to the target and back (time-of-flight) or the angle of reflection is used to calculate the displacement.
5. Piezoelectric Sensors:
These sensors rely on the piezoelectric effect, where certain materials generate an electric charge in response to mechanical stress. Piezoelectric sensors can measure both static and dynamic displacements, making them versatile for various applications.
Key Applications in Industry
Displacement sensors are crucial in many industrial applications, providing precise data that help in enhancing product quality, ensuring safety, and optimizing operational efficiency. Some key applications include:
1. Automation and Robotics:
In automated manufacturing systems and robotic arms, displacement sensors monitor the position and movement of various components. This ensures accurate and consistent performance, reducing errors and enhancing productivity.
2. Machine Tool Positioning:
Precision is paramount in machining processes. Displacement sensors help in controlling and monitoring the position of machine tool components, ensuring precise cutting, drilling, and milling operations.
3. Assembly Line Inspection:
For quality control, displacement sensors are used to inspect products on the assembly line. They can measure dimensions, detect defects, and verify that components are correctly assembled, ensuring that only high-quality products reach the end customer.
4. Material Testing:
Displacement sensors play a vital role in characterizing the mechanical properties of materials. They measure deformation under stress, helping in determining the material’s strength, elasticity, and other critical factors.
5. Automotive Industry:
In automotive manufacturing, displacement sensors are used for various purposes, such as monitoring the position of moving parts in engines and transmissions, ensuring proper alignment during assembly, and conducting crash testing.
Advantages of Using Displacement Sensors
The adoption of displacement sensors in industry comes with numerous benefits that drive efficiency and innovation:
1. High Precision and Accuracy:
Modern displacement sensors offer exceptional accuracy, ensuring precise measurements that are critical for maintaining product quality and process control.
2. Non-contact Measurement:
Many displacement sensors, such as optical and capacitive sensors, provide non-contact measurement. This minimizes wear and tear, reduces maintenance, and allows measurements in environments where contact is not feasible.
3. Real-time Monitoring:
Displacement sensors provide real-time data, enabling timely interventions and adjustments during the manufacturing process. This helps in maintaining optimal performance and preventing potential issues before they escalate.
4. Versatility:
Various types of displacement sensors can be tailored to specific applications, whether measuring linear or angular displacement, small or large movements, in harsh or delicate environments.
5. Efficiency and Cost Savings:
By optimizing processes and reducing errors, displacement sensors contribute to operational efficiency and cost savings. Accurate measurements lead to better resource utilization and fewer rejects, resulting in a more cost-effective production process.
Challenges and Considerations
While displacement sensors offer remarkable benefits, there are also challenges and considerations that need to be addressed:
1. Environmental Conditions:
The performance of some displacement sensors can be affected by environmental factors such as temperature, humidity, and electromagnetic interference. It’s crucial to choose sensors designed to withstand the specific conditions of the application.
2. Installation and Calibration:
Proper installation and calibration are essential for accurate measurements. Misalignment, loose connections, or improper calibration can lead to erroneous readings and impact overall performance.
3. Cost:
High-precision displacement sensors can be expensive. It’s important to balance the cost with the required accuracy and performance for the specific application.
4. Integration with Systems:
Effective integration of displacement sensors with control systems and data management platforms is necessary for leveraging their full potential. Compatibility and communication protocols should be considered during the selection process.
Displacement sensors are invaluable tools in today’s industrial landscape, offering precise measurements that enhance product quality, safety, and operational efficiency. With advancements in technology, these sensors are becoming more sophisticated, reliable, and accessible. By understanding their technical aspects and applications, industries can better harness their capabilities to drive innovation and maintain a competitive edge. Whether in automation, material testing, or machinery positioning, displacement sensors are fundamental components that contribute significantly to modern industrial processes.
資料ダウンロード
QCD管理受発注クラウド「newji」は、受発注部門で必要なQCD管理全てを備えた、現場特化型兼クラウド型の今世紀最高の受発注管理システムとなります。
ユーザー登録
受発注業務の効率化だけでなく、システムを導入することで、コスト削減や製品・資材のステータス可視化のほか、属人化していた受発注情報の共有化による内部不正防止や統制にも役立ちます。
NEWJI DX
製造業に特化したデジタルトランスフォーメーション(DX)の実現を目指す請負開発型のコンサルティングサービスです。AI、iPaaS、および先端の技術を駆使して、製造プロセスの効率化、業務効率化、チームワーク強化、コスト削減、品質向上を実現します。このサービスは、製造業の課題を深く理解し、それに対する最適なデジタルソリューションを提供することで、企業が持続的な成長とイノベーションを達成できるようサポートします。
製造業ニュース解説
製造業、主に購買・調達部門にお勤めの方々に向けた情報を配信しております。
新任の方やベテランの方、管理職を対象とした幅広いコンテンツをご用意しております。
お問い合わせ
コストダウンが利益に直結する術だと理解していても、なかなか前に進めることができない状況。そんな時は、newjiのコストダウン自動化機能で大きく利益貢献しよう!
(β版非公開)