- お役立ち記事
- Technical Guide for Optimizing Injection Speed to Improve Productivity
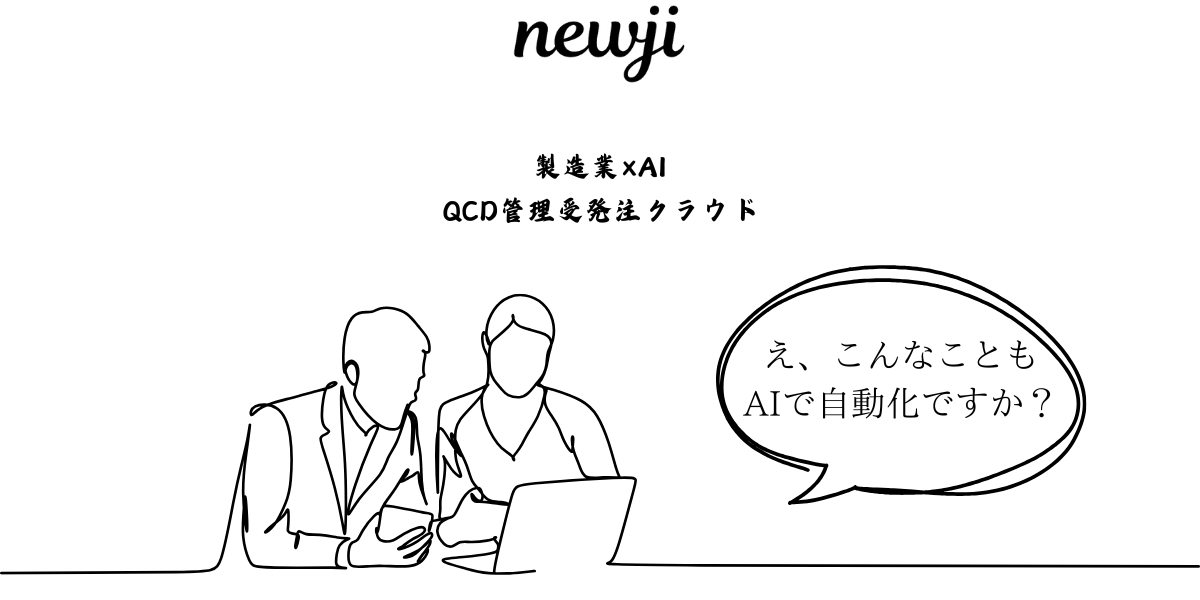
Technical Guide for Optimizing Injection Speed to Improve Productivity
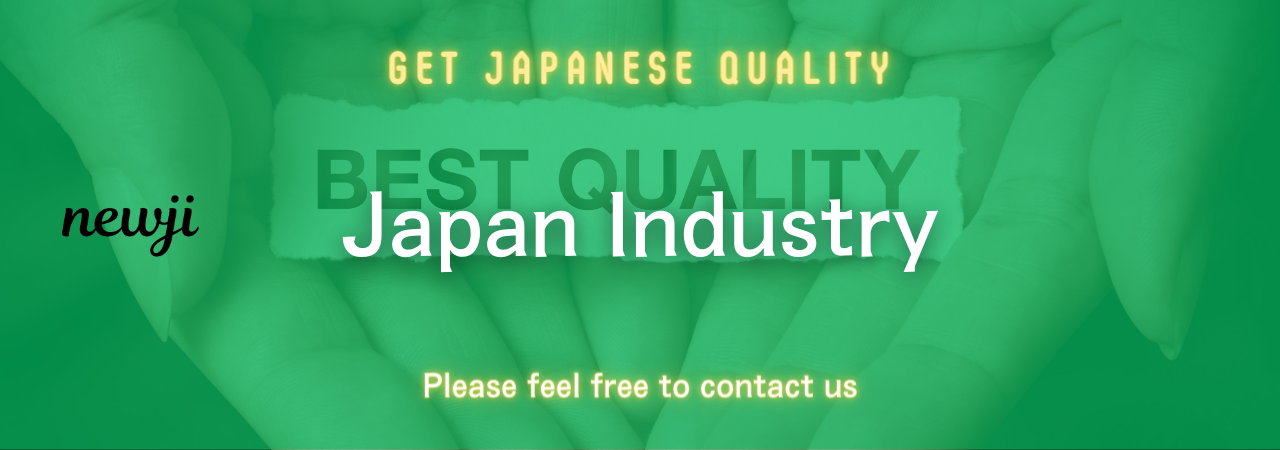
目次
Understanding Injection Speed in Manufacturing
In the manufacturing world, particularly in plastic injection molding, injection speed is a vital factor that greatly influences productivity.
Simply put, injection speed refers to how quickly the material is injected into the mold.
Optimizing this speed can lead to more efficient processes, better product quality, and reduced costs.
This guide aims to provide a comprehensive understanding of injection speed and how to optimize it to enhance productivity.
The Importance of Injection Speed
Injection speed is critical because it directly impacts the cycle time of the molding process.
Cycle time is the total time taken to complete one production cycle, including the filling, cooling, and ejection stages.
A faster injection speed can lead to shorter cycle times, which means more products can be manufactured in a given time frame.
Moreover, injection speed affects the quality of the final product.
A speed that is too fast can cause defects such as warping or burn marks, while a speed that is too slow can lead to incomplete filling or cold welds.
Therefore, finding the optimal speed is essential for producing high-quality products consistently.
Factors Influencing Injection Speed
Several factors influence the optimal injection speed, and understanding these can help in making informed adjustments.
First, the material being used plays a significant role.
Different materials have varying viscosities which affect how they flow into the mold.
For instance, a material with higher viscosity may require a slower injection speed to avoid defects.
Second, the design of the mold itself is a critical factor.
Complex mold geometries may need adjustments in speed to ensure complete filling without causing undue stress on the product.
Third, product size and wall thickness can impact the required speed.
Larger parts or those with thicker walls usually benefit from a slightly slower injection speed to ensure proper flow and cooling.
Lastly, machine capabilities must be considered.
Each injection molding machine has specific parameters and limitations when it comes to speed, pressure, and temperature.
Strategies for Optimizing Injection Speed
Optimizing injection speed involves balancing multiple variables to achieve the best possible results.
Here are some strategies to consider:
Conducting Material Trials
Perform trials with different materials to understand their flow characteristics better.
These trials can help determine the ideal speed for each material, reducing the risk of defects and improving the consistency of the production process.
Adjusting Mold Design
Collaborate with mold designers to create designs that allow optimal filling at higher speeds.
Consider adding features such as additional vents or modifying gate sizes to facilitate better material flow.
Implementing Process Monitoring
Utilize advanced process monitoring tools that provide real-time feedback on injection pressure, speed, and temperature.
These tools enable operators to make swift adjustments, ensuring the speed is continuously optimized for each production run.
Continuous Training and Education
Regularly train staff on the latest best practices and technological advancements in injection molding.
Well-informed operators are better equipped to make adjustments that positively impact injection speed and overall productivity.
Benefits of Optimizing Injection Speed
When injection speed is optimized effectively, several benefits can be realized:
Improved Productivity
Faster cycle times result in more parts being produced in the same timeframe, directly boosting overall productivity.
Enhanced Product Quality
Optimizing injection speed reduces the likelihood of defects, ensuring that each product meets the quality standards required.
Cost Savings
Reduced cycle times and fewer defective products mean lower production costs and decreased waste, enhancing profitability.
Common Challenges and Solutions
While optimizing injection speed offers numerous advantages, it is not without challenges.
Here are some common issues and potential solutions:
Inconsistent Material Quality
Solution: Work closely with material suppliers to ensure consistent quality and batch-to-batch uniformity.
Regularly test incoming materials for properties that may affect injection speed.
Machine Limitations
Solution: Invest in regular maintenance and upgrades for molding machines to ensure they perform optimally.
Consider upgrading to more advanced models if needed.
Complex Mold Geometries
Solution: Engage in iterative design processes, using simulation software to predict how different speeds affect filling patterns and identifying any issues before physical mold production.
Conclusion
Optimizing injection speed is a complex but rewarding endeavor that can significantly enhance manufacturing productivity and product quality.
By understanding the factors influencing injection speed and implementing strategies for optimization, manufacturers can achieve more efficient production cycles and higher-quality outcomes.
Investing time and resources into this critical aspect of the molding process is essential for staying competitive in today’s dynamic manufacturing landscape.
資料ダウンロード
QCD調達購買管理クラウド「newji」は、調達購買部門で必要なQCD管理全てを備えた、現場特化型兼クラウド型の今世紀最高の購買管理システムとなります。
ユーザー登録
調達購買業務の効率化だけでなく、システムを導入することで、コスト削減や製品・資材のステータス可視化のほか、属人化していた購買情報の共有化による内部不正防止や統制にも役立ちます。
NEWJI DX
製造業に特化したデジタルトランスフォーメーション(DX)の実現を目指す請負開発型のコンサルティングサービスです。AI、iPaaS、および先端の技術を駆使して、製造プロセスの効率化、業務効率化、チームワーク強化、コスト削減、品質向上を実現します。このサービスは、製造業の課題を深く理解し、それに対する最適なデジタルソリューションを提供することで、企業が持続的な成長とイノベーションを達成できるようサポートします。
オンライン講座
製造業、主に購買・調達部門にお勤めの方々に向けた情報を配信しております。
新任の方やベテランの方、管理職を対象とした幅広いコンテンツをご用意しております。
お問い合わせ
コストダウンが利益に直結する術だと理解していても、なかなか前に進めることができない状況。そんな時は、newjiのコストダウン自動化機能で大きく利益貢献しよう!
(Β版非公開)