- お役立ち記事
- Techniques and Benefits of Grinding Processing in Manufacturing
Techniques and Benefits of Grinding Processing in Manufacturing
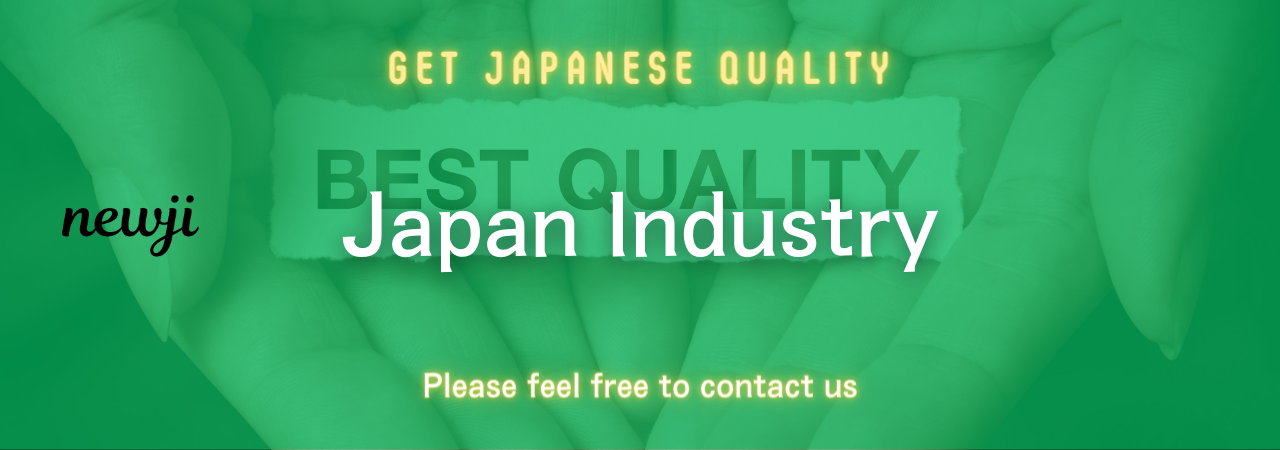
Manufacturing is an industry that has evolved significantly over the years, with new techniques and technologies continually being developed to improve efficiency and product quality.
One of these crucial techniques is grinding processing.
Grinding, which involves the use of abrasive wheels to shape surfaces or remove material, is an essential part of the manufacturing process in many industries.
目次
What is Grinding Processing?
Grinding processing is a machining process that uses an abrasive tool as a cutting medium.
The process involves removing material from a workpiece using abrasive grains held by a cementing matrix.
This method can shape objects, improve surface finish, and achieve precise dimensions.
Types of Grinding Processes
There are several types of grinding processes used in manufacturing, each with its specific applications and benefits.
Surface Grinding
Surface grinding uses a rotating abrasive wheel to smooth the flat surface of a workpiece.
It ensures that the surface is evenly finished and has high precision.
Cylindrical Grinding
This type is used to shape the exterior of an object.
The machine rotates the item, allowing the grinding wheel to remove material as it passes over the workpiece.
It’s commonly used for parts like shafts or rods.
Centerless Grinding
Centerless grinding differs from other forms as it doesn’t use a spindle to hold the object.
Instead, the workpiece is supported by a blade and regulated against a grinding wheel by a control wheel.
This method is excellent for high-throughput production environments due to its efficiency.
Internal Grinding
Internal grinding removes material from the inside of a hollow object.
This type of grinding is critical for components that require high precision on internal surfaces, such as bearings or bushings.
Techniques of Grinding Processing
Grinding processing techniques are designed to achieve specific results.
Here are some commonly used techniques.
Plunge Grinding
Plunge grinding involves passing the grinding wheel directly onto the workpiece without any lateral movement.
It’s particularly useful for parts that are shorter in length but require a high degree of precision.
Creep-Feed Grinding
Creep-feed grinding is a process that allows for high material removal rates.
In this technique, the depth of cut is considerable, resulting in fewer passes and hence a quicker operation.
This method is ideal for creating complex shapes in hard materials.
Through-Feed Grinding
Through-feed grinding, often used in centerless grinding, involves feeding the workpiece continuously between the grinding wheel and a control wheel.
It’s a highly efficient process for mass production of cylindrical parts.
Form Grinding
Form grinding is used to create the specific shape of an object.
By using a specialized grinding wheel with a particular profile, the workpiece can be precisely shaped in a controlled manner.
This technique is ideal for producing complex geometries.
Benefits of Grinding Processing
Grinding processing provides numerous advantages, making it indispensable to modern manufacturing.
High Precision
One of the most significant benefits of grinding is the high degree of precision it offers.
Grinding can achieve tight tolerances and fine finishes, which are essential for many industrial components.
This high level of accuracy is crucial for parts that must fit together perfectly in machinery.
Improved Surface Quality
Grinding improves the surface finish of a workpiece, making it smoother and free from significant defects.
A better surface finish reduces friction, wear, and tear, extending the life of the component.
Versatility
Grinding is versatile and can be used on a wide range of materials, including metals, plastics, and ceramics.
This flexibility makes it useful across various industries, from automotive to aerospace.
Material Efficiency
Grinding is an efficient material removal process, capable of handling hard materials that other machining methods may struggle with.
It reduces the waste generated during production, making it a more sustainable option.
Cost-Effective
Although grinding machinery and abrasive materials can be costly, the process itself is highly efficient.
Reduced labor, quicker production times, and minimal material waste contribute to the cost-effectiveness of grinding.
Applications of Grinding Processing
Grinding processing finds its applications in diverse industries.
Here are a few examples highlighting its importance.
Automotive Industry
In the automotive industry, grinding is used to manufacture and refine various engine components, such as crankshafts, camshafts, and gear shafts.
Precision is critical for these parts to ensure optimal performance and longevity of the vehicle.
Aerospace Industry
In aerospace, grinding is crucial for producing turbine blades, landing gear components, and other critical parts.
The high precision and excellent surface finish achieved through grinding ensure these parts can withstand extreme conditions and stresses.
Medical Industry
The medical industry relies on grinding to produce surgical tools, implants, and other high-precision instruments.
The process allows for the creation of intricate and precise components necessary for medical applications.
Tool and Die Making
Grinding is essential for manufacturing cutting tools, dies, and molds.
These components require exact dimensions and smooth surfaces to ensure they function correctly and produce high-quality parts.
Conclusion
Grinding processing is a cornerstone of modern manufacturing, offering versatility, precision, and efficiency.
From automotive to medical industries, its applications are vast and critical.
The various types and techniques of grinding ensure that the specific needs of each industry can be met.
As new technologies emerge, the grinding process will continue to evolve, providing even more benefits and applications for future manufacturing challenges.
Understanding the techniques and benefits of grinding will help companies optimize their production processes and remain competitive in an ever-changing market.
資料ダウンロード
QCD調達購買管理クラウド「newji」は、調達購買部門で必要なQCD管理全てを備えた、現場特化型兼クラウド型の今世紀最高の購買管理システムとなります。
ユーザー登録
調達購買業務の効率化だけでなく、システムを導入することで、コスト削減や製品・資材のステータス可視化のほか、属人化していた購買情報の共有化による内部不正防止や統制にも役立ちます。
NEWJI DX
製造業に特化したデジタルトランスフォーメーション(DX)の実現を目指す請負開発型のコンサルティングサービスです。AI、iPaaS、および先端の技術を駆使して、製造プロセスの効率化、業務効率化、チームワーク強化、コスト削減、品質向上を実現します。このサービスは、製造業の課題を深く理解し、それに対する最適なデジタルソリューションを提供することで、企業が持続的な成長とイノベーションを達成できるようサポートします。
オンライン講座
製造業、主に購買・調達部門にお勤めの方々に向けた情報を配信しております。
新任の方やベテランの方、管理職を対象とした幅広いコンテンツをご用意しております。
お問い合わせ
コストダウンが利益に直結する術だと理解していても、なかなか前に進めることができない状況。そんな時は、newjiのコストダウン自動化機能で大きく利益貢献しよう!
(Β版非公開)