- お役立ち記事
- Techniques for shortening lead times by streamlining the purchasing process
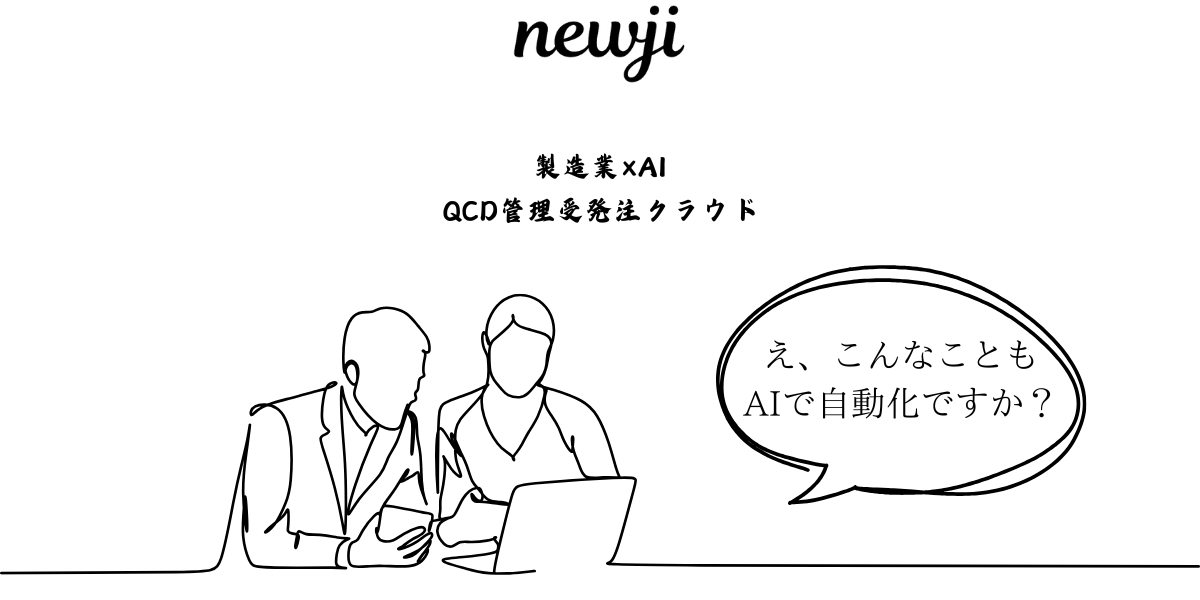
Techniques for shortening lead times by streamlining the purchasing process
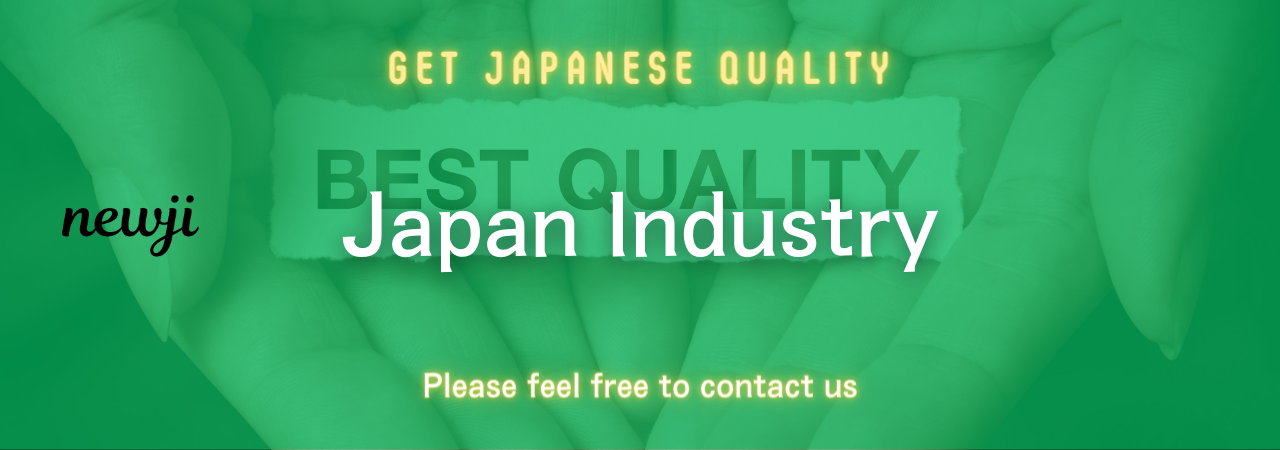
目次
Understanding Lead Times in the Purchasing Process
In any business, especially those involved in the production and distribution of goods, managing lead times effectively can greatly impact overall efficiency and success.
Lead time refers to the total time it takes for a product to move from the initial order stage to its final delivery.
A streamlined purchasing process plays a crucial role in reducing these lead times, ensuring that businesses remain competitive and responsive to market demands.
Identifying Key Stages in the Purchasing Process
The purchasing process typically involves several key stages that contribute to the overall lead time.
Understanding each stage can help identify potential areas for streamlining.
The primary stages include:
1. **Order Placement**: When a purchase order is raised concerning a specific need or demand.
2. **Supplier Selection**: Choosing the right vendor based on factors such as quality, cost, and delivery time.
3. **Order Processing**: The phase where the supplier processes the order, prepares the inventory, and arranges shipment.
4. **Shipment and Delivery**: The logistic process that involves the transportation of goods from the supplier to the business.
5. **Receipt and Inspection**: Checking the goods upon arrival for quality and quantity accuracy.
Each of these stages must be carefully managed to minimize the time spent and avoid unnecessary delays.
Strategies for Streamlining the Purchasing Process
Implementing Technology Solutions
One of the most effective ways to reduce lead times is by leveraging technology.
Implementing an integrated supply chain management system can improve data flow and enhance communication between suppliers and purchasers.
Such systems can automate order placements, send real-time updates, and predict potential delays, allowing for a proactive approach to purchase management.
Establishing Strong Supplier Relationships
Building strong relationships with suppliers can significantly streamline the purchasing process.
Good communication and cooperation can lead to improved negotiations on contract terms, prioritized order fulfillment, and better collaboration when dealing with unexpected issues.
Consider growing a preferred supplier list to streamline the vetting and approval process, which shortens the time spent selecting vendors.
Optimizing Inventory Management
Effective inventory management is crucial for reducing lead times.
This includes maintaining optimal inventory levels to ensure a smooth production flow without overstocking or understocking.
Utilize techniques like Just-In-Time (JIT) inventory or Economic Order Quantity (EOQ) calculations to align purchasing with actual demand, thus minimizing lead times and storage costs.
Implementing Lean Purchasing Practices
Lean purchasing involves identifying and eliminating waste throughout the procurement process.
This includes reducing unnecessary steps, eliminating bottlenecks, and ensuring the right processes are in place to expedite order placement and processing.
Regularly reviewing and refining purchasing practices can lead to meaningful reductions in lead times.
Enhancing Order Accuracy
Errors in orders can lead to significant delays in the purchasing process.
Ensuring order accuracy from the initial stage is paramount.
This can be achieved by double-checking orders, utilizing electronic ordering systems that handle data transfer with precision, and training employees on best practices for order management.
Monitoring and Measuring Performance
Once strategies for streamlining are in place, it’s essential to continuously monitor and measure their performance.
This involves setting key performance indicators (KPIs) such as order cycle time, delivery reliability, and order accuracy.
Regular assessment of these KPIs can identify areas for further improvements and ensure long-term success in reducing lead times.
Conclusion: The Competitive Advantage of Streamlined Purchasing
Streamlining the purchasing process is not just about reducing lead times; it also contributes to overall efficiency, cost savings, and enhanced customer satisfaction.
By implementing these strategies, businesses can gain a significant competitive advantage, allowing them to respond quickly to market changes and customer demands.
In today’s fast-paced business environment, the ability to innovate and improve purchasing processes is vital for long-term success.
資料ダウンロード
QCD調達購買管理クラウド「newji」は、調達購買部門で必要なQCD管理全てを備えた、現場特化型兼クラウド型の今世紀最高の購買管理システムとなります。
ユーザー登録
調達購買業務の効率化だけでなく、システムを導入することで、コスト削減や製品・資材のステータス可視化のほか、属人化していた購買情報の共有化による内部不正防止や統制にも役立ちます。
NEWJI DX
製造業に特化したデジタルトランスフォーメーション(DX)の実現を目指す請負開発型のコンサルティングサービスです。AI、iPaaS、および先端の技術を駆使して、製造プロセスの効率化、業務効率化、チームワーク強化、コスト削減、品質向上を実現します。このサービスは、製造業の課題を深く理解し、それに対する最適なデジタルソリューションを提供することで、企業が持続的な成長とイノベーションを達成できるようサポートします。
オンライン講座
製造業、主に購買・調達部門にお勤めの方々に向けた情報を配信しております。
新任の方やベテランの方、管理職を対象とした幅広いコンテンツをご用意しております。
お問い合わせ
コストダウンが利益に直結する術だと理解していても、なかなか前に進めることができない状況。そんな時は、newjiのコストダウン自動化機能で大きく利益貢献しよう!
(Β版非公開)