- お役立ち記事
- Technological approach to improve precision of metal powder injection molded products
月間77,185名の
製造業ご担当者様が閲覧しています*
*2025年2月28日現在のGoogle Analyticsのデータより
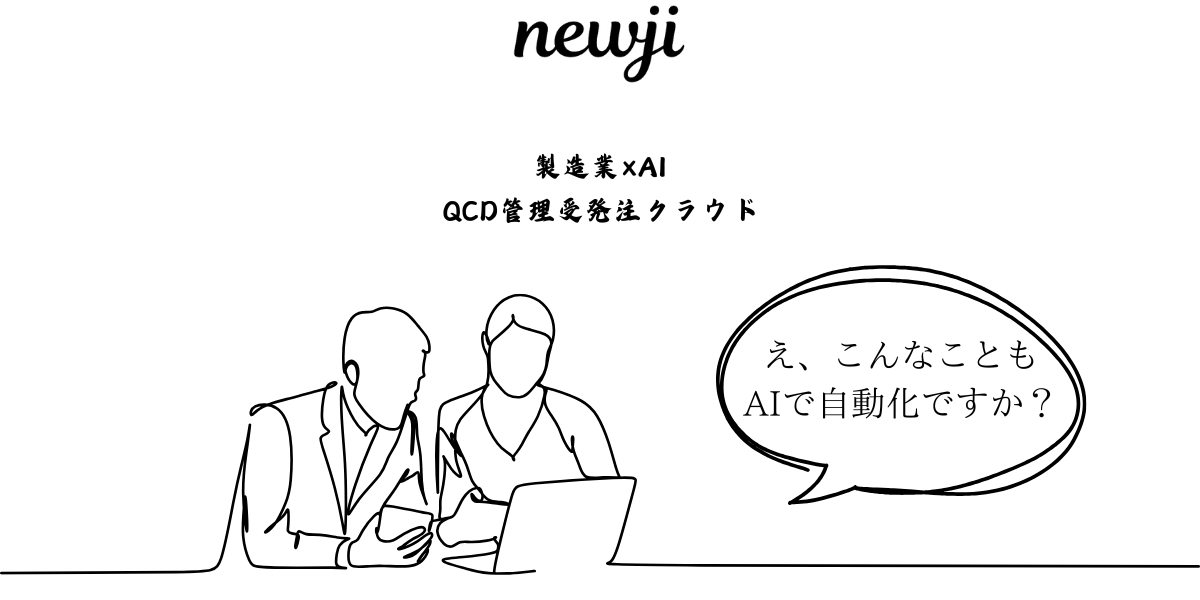
Technological approach to improve precision of metal powder injection molded products
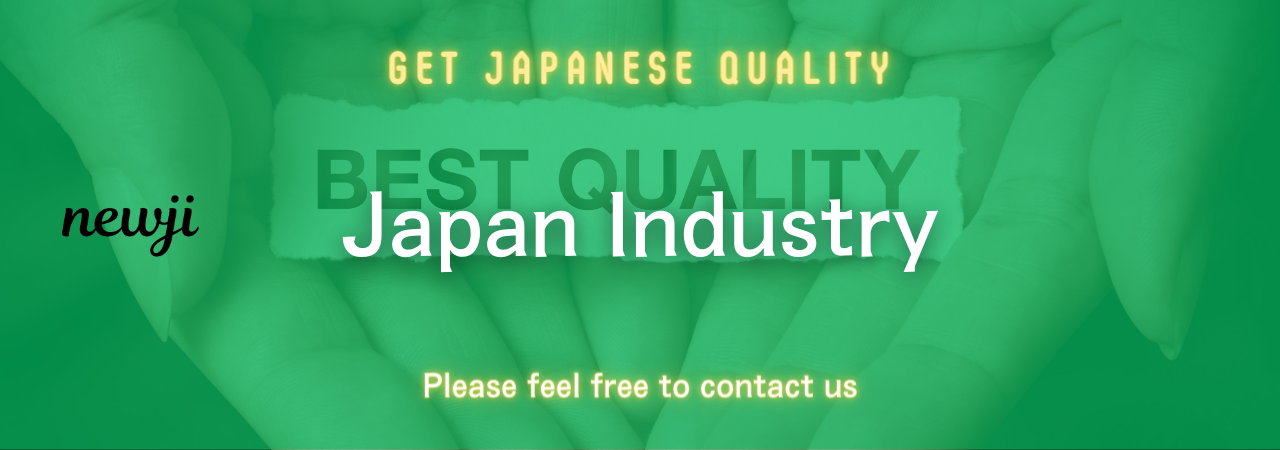
目次
Understanding Metal Powder Injection Molding
Metal Powder Injection Molding (MIM) is a manufacturing process that combines the versatility of plastic injection molding with the strength and integrity of metal powder metallurgy.
It is commonly used to produce complex metal parts with high precision and in large volumes.
The process involves mixing fine metal powders with a binder material to create a feedstock that is injected into a mold cavity.
Once shaped, the binder is removed, and the metal parts are sintered to achieve the desired strength and density.
The Importance of Precision in MIM
In the world of manufacturing, precision is paramount.
For industries such as aerospace, medical, and automotive, the slightest deviation in dimensions can lead to significant issues.
In MIM, achieving high precision is crucial because it directly influences the performance and reliability of the final product.
Accurate dimensions also minimize the need for post-processing, thereby reducing production costs and time.
Technological Advances in MIM
The pursuit of improved precision in MIM has led to several technological advancements, each contributing to a more controlled and reliable manufacturing process.
Advanced Simulation Software
One of the most significant technological contributions to improving precision in MIM is the use of advanced simulation software.
These programs allow engineers to model the entire MIM process, from molding to sintering.
By simulating the process, potential issues like shrinkage, warpage, and porosity can be identified and addressed before actual production begins.
This predictive capability enables more precise control over the process variables, leading to improved dimensional accuracy.
Quality Control with 3D Scanning
Another technological innovation is the implementation of 3D scanning for quality control.
3D scanning technologies enable manufacturers to capture accurate measurements of complex geometries, which are then compared to original CAD models.
This comparison helps identify even the slightest variations in dimensions, ensuring that every part meets the required specifications.
By integrating this technology into the MIM process, manufacturers can achieve a higher degree of precision and consistency across production runs.
Innovative Binder Systems
The development of new binder systems is also a key factor in improving the precision of MIM products.
Binders play a critical role in holding the metal powders together during the molding stage.
Innovative binders that offer superior flow properties and bonding strength lead to better form retention and alignment of metal particles.
As a result, the precision and surface finish of molded parts are significantly improved.
Optimizing the MIM Process
Beyond technological innovations, optimizing the MIM process itself can also contribute to enhanced precision.
Feedstock Formulation
The formulation of the feedstock, which is a blend of metal powders and binders, greatly impacts the quality of the molded parts.
By carefully selecting and blending the right combination of powders and binder materials, manufacturers can optimize the feedstock for better consistency and flow.
This optimization reduces defects and results in parts with more uniform dimensions.
Mold Design and Manufacturing
The design and quality of molds directly influence the precision of MIM products.
Advanced mold manufacturing techniques, such as high-precision CNC machining and EDM (Electrical Discharge Machining), enable the production of highly detailed and accurate molds.
Attention to mold design, including proper gating and venting, ensures balanced filling and minimizes potential defects.
Sintering Optimization
Sintering is a crucial step in the MIM process, where the molded part is subjected to high temperatures to achieve the desired material properties.
The precision of MIM products can be significantly affected by the sintering conditions.
Optimizing the sintering cycle, including temperature, time, and atmosphere, helps achieve consistent density and mechanical properties, crucial for precision and reliability.
The Role of Automation in Precision Improvement
Automation plays a significant role in enhancing the precision of metal powder injection molded products.
Automated systems not only improve efficiency but also reduce the risk of human error, leading to more consistent and accurate production.
Robotic Handling
Integrating robotic handling into the MIM process can ensure precise and repeatable handling of feedstock, molds, and finished parts.
Automated robotic systems can perform complex operations with high accuracy, reducing variability and improving the overall precision of the finished product.
Automated Inspection Systems
Automated inspection systems, including machine vision technologies, provide real-time monitoring and assessment of MIM products.
These systems can quickly detect defects and deviations from specifications, allowing for immediate corrective actions.
By continuously monitoring the production process, manufacturers can maintain high precision and quality standards.
Future Trends in MIM Precision Technology
As technology continues to evolve, further advancements in MIM precision are expected.
Emerging technologies, such as artificial intelligence and machine learning, hold the potential to revolutionize process optimization and defect prediction in MIM.
Additionally, the development of new materials and feedstock innovations will further enhance the capabilities and precision of MIM products.
Conclusion
The technological approaches to improving the precision of metal powder injection molded products are manifold and constantly evolving.
From advanced simulation software to automated inspection systems, each innovation contributes to producing high-quality, precise MIM components.
By embracing these technologies, manufacturers can meet the increasingly stringent demands for precision in a variety of industries, continuing to advance the field of metal powder injection molding.
資料ダウンロード
QCD管理受発注クラウド「newji」は、受発注部門で必要なQCD管理全てを備えた、現場特化型兼クラウド型の今世紀最高の受発注管理システムとなります。
ユーザー登録
受発注業務の効率化だけでなく、システムを導入することで、コスト削減や製品・資材のステータス可視化のほか、属人化していた受発注情報の共有化による内部不正防止や統制にも役立ちます。
NEWJI DX
製造業に特化したデジタルトランスフォーメーション(DX)の実現を目指す請負開発型のコンサルティングサービスです。AI、iPaaS、および先端の技術を駆使して、製造プロセスの効率化、業務効率化、チームワーク強化、コスト削減、品質向上を実現します。このサービスは、製造業の課題を深く理解し、それに対する最適なデジタルソリューションを提供することで、企業が持続的な成長とイノベーションを達成できるようサポートします。
製造業ニュース解説
製造業、主に購買・調達部門にお勤めの方々に向けた情報を配信しております。
新任の方やベテランの方、管理職を対象とした幅広いコンテンツをご用意しております。
お問い合わせ
コストダウンが利益に直結する術だと理解していても、なかなか前に進めることができない状況。そんな時は、newjiのコストダウン自動化機能で大きく利益貢献しよう!
(β版非公開)