- お役立ち記事
- Technological development method for manufacturing aircraft and aircraft engine maintenance equipment
月間77,185名の
製造業ご担当者様が閲覧しています*
*2025年2月28日現在のGoogle Analyticsのデータより
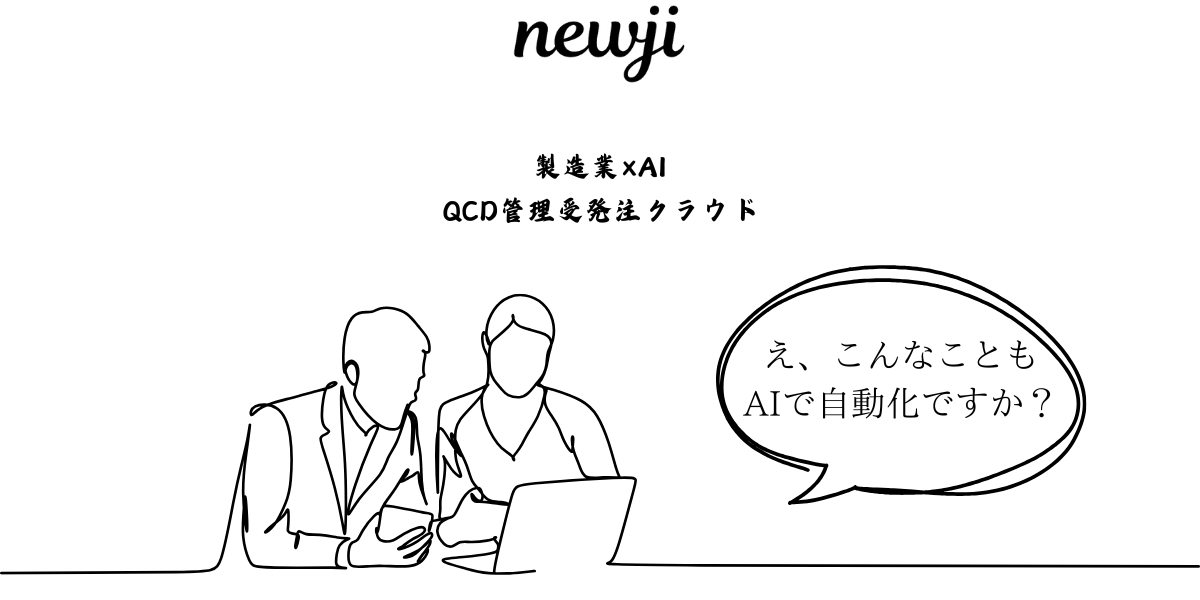
Technological development method for manufacturing aircraft and aircraft engine maintenance equipment
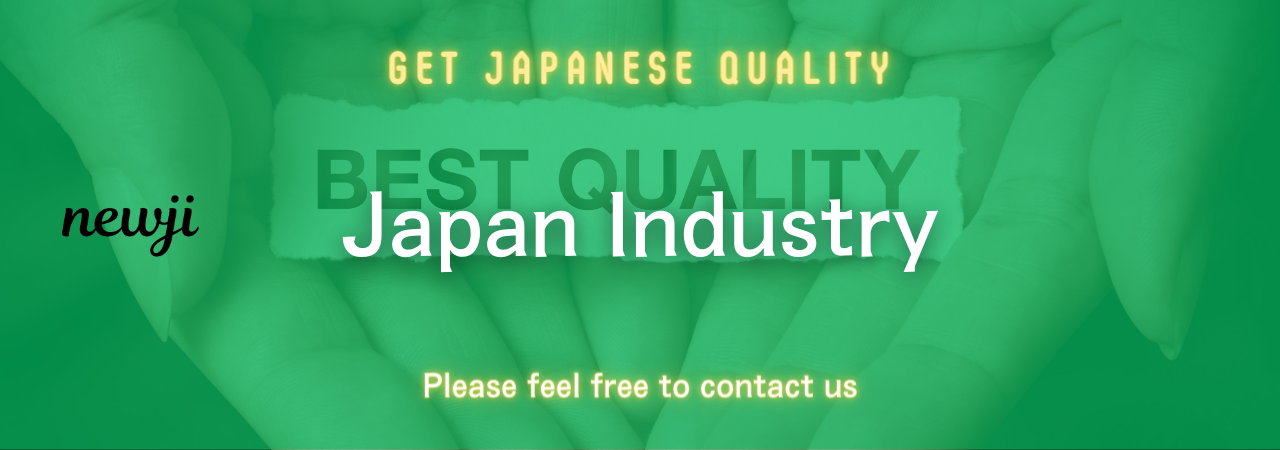
目次
Introduction to Aircraft and Engine Maintenance
Manufacturing aircraft and aircraft engine maintenance equipment is a complex process that involves various cutting-edge technologies and methodologies.
As the aviation industry continues to grow, the demand for advanced maintenance equipment is increasing rapidly.
This growth drives the need for innovative technological development methods that ensure both efficiency and safety.
Aircraft and engine maintenance is critical for ensuring safety in the skies.
Effective maintenance equipment helps in diagnosing issues before they become serious problems, thus extending the life of the aircraft and its components.
Understanding the Basics of Aircraft Manufacturing
Before diving into the intricacies of aircraft engine maintenance equipment, it’s essential to understand how aircraft are manufactured.
The process starts with extensive research and design planning.
Engineers use state-of-the-art software and simulation tools to design every component meticulously.
These designs must comply with rigorous safety standards and regulations set by aviation authorities worldwide.
Once the design phase is complete, the manufacturing process begins.
Aircraft are made using a combination of materials such as aluminum, titanium, and composite materials like carbon fiber.
These materials are chosen for their strength, lightweight properties, and durability.
Innovation in Aircraft Engine Maintenance Equipment
Aircraft engines are the heart of an aircraft, and maintaining them involves various technological advancements.
Recent innovations in maintenance equipment aim to make the process more efficient and accurate.
One such technology gaining prominence is predictive maintenance, which utilizes data analytics and sensors to predict potential engine failures before they occur.
Data Analytics and Predictive Maintenance
Predictive maintenance is transforming how maintenance tasks are approached.
By analyzing data from engine sensors and operational history, maintenance teams can identify patterns and predict when parts might fail.
This technology minimizes the risk of unexpected failures and helps airlines schedule maintenance activities without affecting flight operations.
3D Printing in Maintenance Equipment Production
3D printing, also known as additive manufacturing, is revolutionizing the production of aircraft engine maintenance equipment.
This technology allows for the rapid prototyping and production of complex parts with high precision.
3D printing reduces lead times and costs, enabling maintenance teams to access the necessary tools and parts quickly.
This advancement is particularly beneficial for producing specialized tools that might not be easily available through traditional manufacturing methods.
Robotics and Automation in Maintenance Processes
Robotics and automation have become integral to modern aircraft and engine maintenance processes.
Robots are used for tasks that require precision and can be hazardous for humans.
For instance, robotic systems can perform inspections using cameras and sensors, reaching areas that are challenging for human technicians.
Automation also improves the efficiency of maintenance tasks.
Routine checks, such as fluid level evaluations, can now be conducted automatically, freeing up technicians to focus on more complex issues.
Advanced Diagnostics and Imaging Techniques
Advanced diagnostics and imaging techniques are crucial in identifying potential issues within aircraft engines.
Techniques such as ultrasound and thermography provide detailed images of engine components, highlighting any anomalies that need attention.
Ultrasound Diagnostics
Ultrasound diagnostics are non-intrusive, allowing maintenance personnel to inspect engine components without disassembling them.
This method uses sound waves to generate images of internal structures, revealing cracks, corrosion, or other defects.
Thermography for Temperature Monitoring
Thermography is another technology used for monitoring engine conditions.
By capturing thermal images, technicians can detect hot spots or areas overheating, which might indicate potential failures.
This technique helps in proactive maintenance, improving safety and reliability.
Ensuring Regulatory Compliance
Any technology developed for aircraft and engine maintenance must comply with strict regulatory standards.
These standards ensure that all equipment and processes meet the highest safety and performance criteria.
Certification and Testing
Before any maintenance equipment is used in practice, it undergoes rigorous testing and certification.
This process involves comprehensive evaluations to ensure the equipment’s effectiveness and reliability.
Continuous Monitoring and Updates
Regulatory compliance is not a one-time task.
Continuous monitoring and updates are essential to align with emerging regulations and safety requirements.
Future Trends in Aircraft and Engine Maintenance
As technology continues to advance, several trends are shaping the future of aircraft and engine maintenance.
These include the integration of artificial intelligence for smart diagnostics, the use of digital twins to simulate maintenance scenarios, and the expanding role of the Internet of Things (IoT) in real-time monitoring.
The adoption of these technologies will lead to more effective and efficient maintenance processes, ultimately enhancing aircraft safety and performance.
Conclusion
The development and implementation of advanced technological methods in manufacturing aircraft and engine maintenance equipment are crucial for the evolving aviation industry.
With innovations like predictive maintenance, 3D printing, and advanced diagnostics, maintenance processes are becoming more efficient and reliable.
As regulations continue to evolve, ensuring compliance remains a priority, driving the need for continuous improvement and adaptation.
資料ダウンロード
QCD管理受発注クラウド「newji」は、受発注部門で必要なQCD管理全てを備えた、現場特化型兼クラウド型の今世紀最高の受発注管理システムとなります。
ユーザー登録
受発注業務の効率化だけでなく、システムを導入することで、コスト削減や製品・資材のステータス可視化のほか、属人化していた受発注情報の共有化による内部不正防止や統制にも役立ちます。
NEWJI DX
製造業に特化したデジタルトランスフォーメーション(DX)の実現を目指す請負開発型のコンサルティングサービスです。AI、iPaaS、および先端の技術を駆使して、製造プロセスの効率化、業務効率化、チームワーク強化、コスト削減、品質向上を実現します。このサービスは、製造業の課題を深く理解し、それに対する最適なデジタルソリューションを提供することで、企業が持続的な成長とイノベーションを達成できるようサポートします。
製造業ニュース解説
製造業、主に購買・調達部門にお勤めの方々に向けた情報を配信しております。
新任の方やベテランの方、管理職を対象とした幅広いコンテンツをご用意しております。
お問い合わせ
コストダウンが利益に直結する術だと理解していても、なかなか前に進めることができない状況。そんな時は、newjiのコストダウン自動化機能で大きく利益貢献しよう!
(β版非公開)