- お役立ち記事
- Technological Innovations in Multi-Injection Molding and Case Studies of SME Utilization
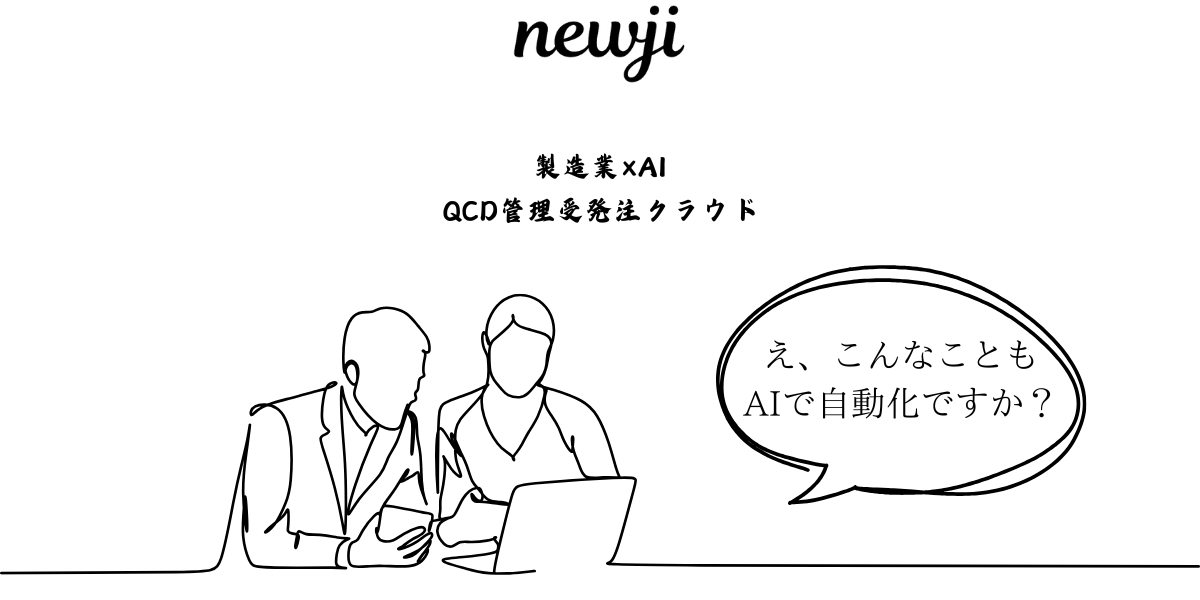
Technological Innovations in Multi-Injection Molding and Case Studies of SME Utilization
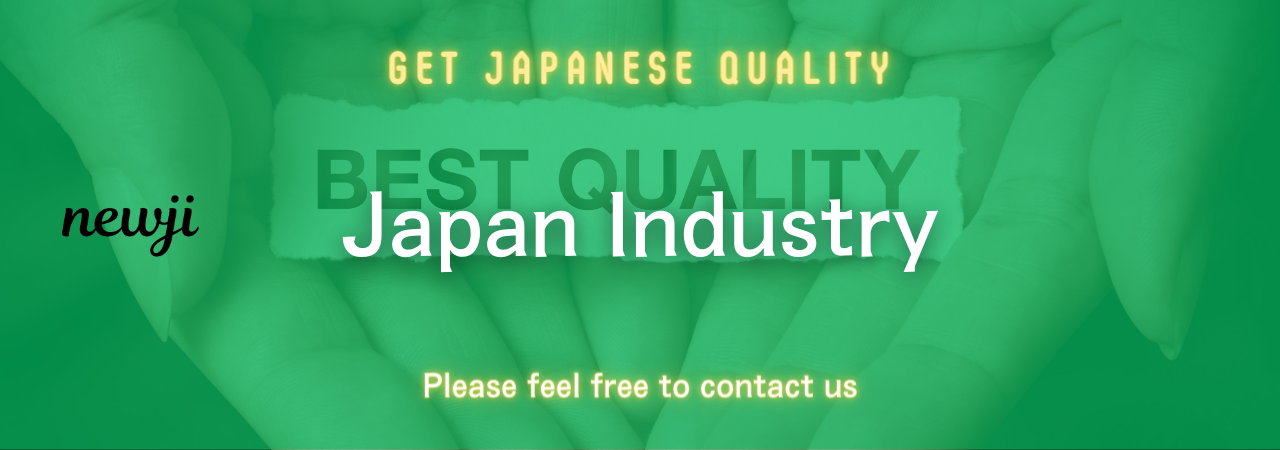
目次
Introduction to Multi-Injection Molding
Multi-injection molding is a revolutionary technology in the manufacturing sector, allowing for the production of complex and multi-material products in a single process.
This method has gained prominence for its ability to combine different materials seamlessly, thus enhancing the functionality and aesthetics of products.
The process typically involves injecting multiple materials through the same mold, either simultaneously or sequentially.
This technology is particularly advantageous in industries where product integrity and innovative designs are critical, such as automotive, consumer electronics, and medical devices.
Key Technological Innovations in Multi-Injection Molding
Recent innovations in multi-injection molding have been pivotal in advancing the capabilities and applications of this technology.
These advancements have primarily focused on material compatibility, precision in manufacturing, and efficiency of production cycles.
One of the significant technological strides is in the development of new injection molding machines.
These machines now boast advanced features such as servo-driven processes, which enhance the precision of multi-material injections.
Moreover, advancements in mold-making technologies have played a crucial role.
Modern molds are now equipped with dynamic temperature control systems that ensure optimal material flow and adhesion.
This is particularly important in multi-layered or multi-component products, where material integrity and bonding are crucial.
Furthermore, the integration of digital technology has revolutionized the multi-injection molding process.
Using advanced simulation software, manufacturers can now predict material behavior and optimize the design before the production begins.
This not only reduces the cycle time but also minimizes material waste, leading to cost efficiency.
Material Innovations
The advancements in material sciences have complemented the innovations in multi-injection molding.
New composite materials and polymers have been developed specifically for use in multi-injection processes.
These materials offer superior bonding properties and thermal stability, making them ideal for complex multi-material products.
Additionally, biocompatible and environmentally friendly materials are now being integrated into the process.
This aligns with the growing demand for sustainable manufacturing solutions across various industries.
Benefits of Multi-Injection Molding for SMEs
Small and medium enterprises (SMEs) stand to gain significantly from adopting multi-injection molding technologies.
Firstly, this technology offers a high degree of flexibility, allowing SMEs to diversify their product offerings without the need for significant capital investment in new machinery.
The ability to produce complex products in a single step reduces the need for multiple machines and processes, saving both time and money.
Moreover, the precision of multi-injection molding can reduce material waste, which is a critical concern for SMEs operating on tight budgets.
The integration of digital controls and simulation software further enhances process efficiency, allowing SMEs to troubleshoot and refine designs before prototyping.
This minimizes the risk of errors and assists in maintaining high quality in the finished products.
Potential for Innovation
For SMEs, multi-injection molding opens up new avenues for innovation.
The ability to combine different materials in a single product allows for unique designs and functionalities that can differentiate products in competitive markets.
Additionally, SMEs can respond more swiftly to market trends and customer demands, given the flexibility of this manufacturing process.
The reduced production cycles also mean that SMEs can scale up production without significant delays, thereby improving their capacity to meet increasing demands.
Case Studies of SME Utilization
Several SMEs have successfully implemented multi-injection molding in their production processes, reaping significant benefits in product quality and cost efficiency.
Case Study 1: Electronics Manufacturer
A small electronics manufacturer adopted multi-injection molding to produce more durable and aesthetically appealing smartphone cases.
By combining a hard plastic outer layer with a soft rubber inner lining, the company not only improved the drop resistance of their product but also enhanced its grip.
This innovation led to a considerable increase in sales, as customers appreciated the improved functionality and design quality.
Case Study 2: Automotive Parts Supplier
An SME in the automotive industry utilized multi-injection molding to produce lightweight, multi-material dashboard components.
By integrating materials with different properties, such as rigidity and flexibility, the firm was able to design parts that met stringent industry standards for safety and performance.
The reduced weight of the components also contributed to fuel efficiency in vehicles, adding an environmental benefit to their innovation.
Case Study 3: Toy Manufacturer
A toy manufacturer leveraged multi-injection molding to introduce a new line of educational toys featuring multiple colors and textures in a single product.
This added sensory appeal and educational value, positioning their products as premium offerings in the market.
The success of this venture enabled the company to expand its market share and brand recognition significantly.
Conclusion
Multi-injection molding stands as a testament to how technological innovations can revolutionize manufacturing processes.
For SMEs, it offers an opportunity to enhance product quality, reduce costs, and drive innovation.
With continuous advancements in this field, coupled with material sciences, multi-injection molding is poised to play a critical role in the future of manufacturing.
As more SMEs recognize the potential benefits, this technology will undoubtedly become a staple in many strategic manufacturing processes.
資料ダウンロード
QCD調達購買管理クラウド「newji」は、調達購買部門で必要なQCD管理全てを備えた、現場特化型兼クラウド型の今世紀最高の購買管理システムとなります。
ユーザー登録
調達購買業務の効率化だけでなく、システムを導入することで、コスト削減や製品・資材のステータス可視化のほか、属人化していた購買情報の共有化による内部不正防止や統制にも役立ちます。
NEWJI DX
製造業に特化したデジタルトランスフォーメーション(DX)の実現を目指す請負開発型のコンサルティングサービスです。AI、iPaaS、および先端の技術を駆使して、製造プロセスの効率化、業務効率化、チームワーク強化、コスト削減、品質向上を実現します。このサービスは、製造業の課題を深く理解し、それに対する最適なデジタルソリューションを提供することで、企業が持続的な成長とイノベーションを達成できるようサポートします。
オンライン講座
製造業、主に購買・調達部門にお勤めの方々に向けた情報を配信しております。
新任の方やベテランの方、管理職を対象とした幅広いコンテンツをご用意しております。
お問い合わせ
コストダウンが利益に直結する術だと理解していても、なかなか前に進めることができない状況。そんな時は、newjiのコストダウン自動化機能で大きく利益貢献しよう!
(Β版非公開)