- お役立ち記事
- Technological Innovations to Enhance Competitiveness in Precision Grinding
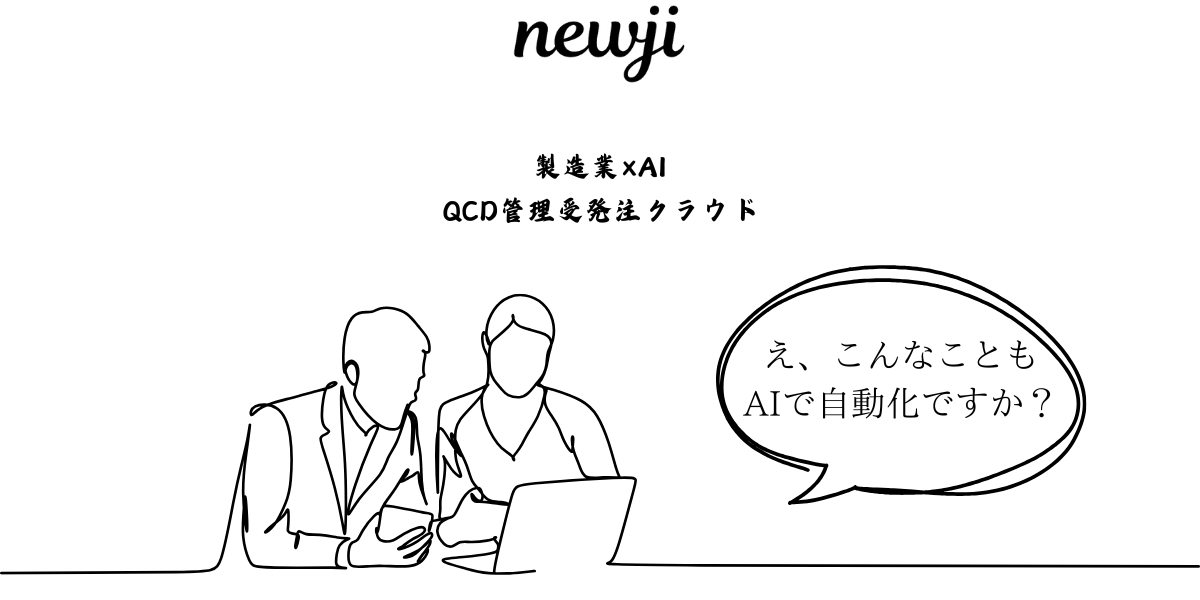
Technological Innovations to Enhance Competitiveness in Precision Grinding
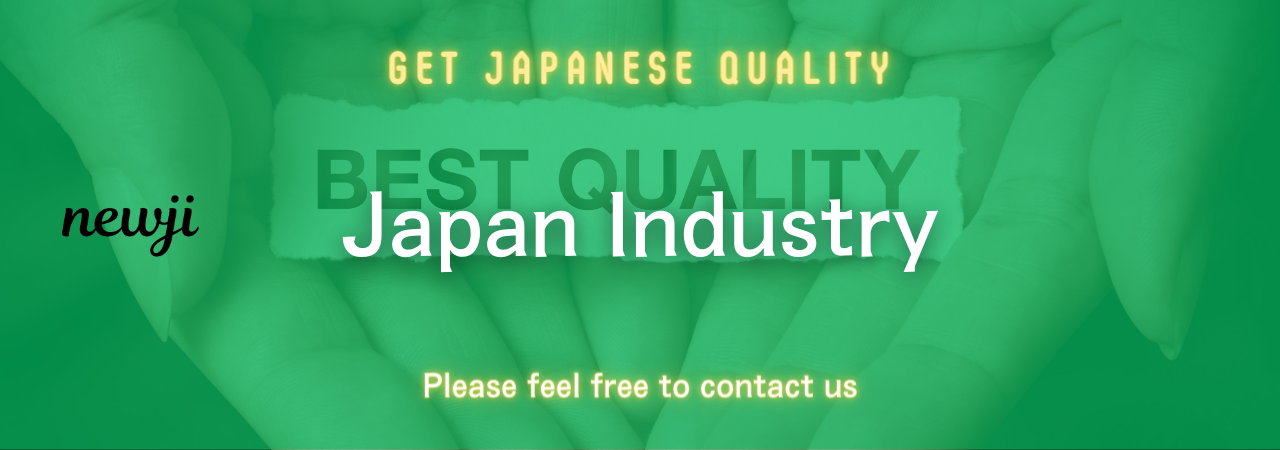
Precision grinding is an essential element in the manufacturing and engineering industries. It involves the removal of material from a workpiece while producing a high surface finish. The importance of precision grinding has surged as industries demand higher efficiency and tighter tolerances. Technological innovations are at the forefront of these advancements, enhancing competitiveness in this critical process. Let’s explore some of these innovative technologies.
目次
Advancements in CNC Grinding Machines
Computer Numerical Control (CNC) Systems
CNC systems play a pivotal role in precision grinding.
Traditional grinding machines required manual operation, which often led to inconsistencies.
With CNC systems, precision grinding has reached new accuracy levels.
These systems allow for the automation of grinding processes, reducing human error and increasing production speed.
Automation and Robotics Integration
The integration of automation and robotics into CNC grinding machines has revolutionized the industry.
Robots can perform repetitive tasks with high precision, working tirelessly around the clock.
This synergy of automation and CNC systems ensures consistent quality and enhanced productivity.
Advanced Materials for Grinding Wheels
Superabrasives
One of the most significant advancements in precision grinding is the use of superabrasives.
Materials like cubic boron nitride (CBN) and polycrystalline diamond (PCD) are now commonly used.
These superabrasives offer higher hardness and longer tool life compared to traditional abrasives.
Bonding Technologies
Innovations in bonding technologies have also made a significant impact.
Modern bonding methods ensure that abrasive particles remain intact longer, increasing grinding wheel durability.
This leads to fewer wheel changes, reducing downtime and enhancing productivity.
Intelligent Grinding Systems
Real-Time Monitoring and Feedback
Intelligent grinding systems use sensors and advanced algorithms to monitor grinding operations in real time.
These innovations provide valuable feedback, allowing for adjustments on the fly.
Real-time monitoring ensures optimal grinding conditions, minimizing defects and material wastage.
Data-Driven Decision Making
The integration of Big Data and analytics allows manufacturers to make informed decisions.
Data from grinding operations can be analyzed to identify patterns, optimize processes, and predict maintenance needs.
This leads to improved efficiency and cost savings.
Enhanced Cooling and Lubrication Techniques
High-Pressure Coolant Systems
Cooling is crucial in precision grinding to prevent overheating and maintain workpiece integrity.
High-pressure coolant systems have been developed to improve cooling efficiency.
These systems deliver coolant at high pressures, effectively dissipating heat and improving grinding performance.
Minimum Quantity Lubrication (MQL)
Another innovative technique is Minimum Quantity Lubrication.
MQL uses a minimal amount of lubricant, delivered precisely to the grinding zone.
This not only reduces lubricant consumption but also leads to a cleaner working environment and reduced environmental impact.
Simulation and Modeling Software
Digital Twins
Simulation and modeling software have brought forward the concept of digital twins.
A digital twin is a virtual replica of the grinding process, allowing manufacturers to simulate and optimize operations before actual production.
This reduces trial and error, saving time and resources.
Predictive Maintenance
By modeling grinding machines and their components, predictive maintenance strategies can be implemented.
These strategies use data to predict when maintenance is needed, reducing unexpected downtime and improving machine longevity.
Surface Inspection Technologies
Non-Contact Measurement Systems
Surface inspection has become more precise with non-contact measurement systems.
Laser and optical sensors can measure surface finish without physically touching the workpiece.
This ensures accurate measurements and prevents potential damage to the surface.
Automated Inspection
Automated inspection systems use advanced imaging technology to inspect workpieces quickly and accurately.
These systems can detect defects and deviations in real time, ensuring only high-quality products leave the production line.
Conclusion
Technological innovations in precision grinding continue to enhance competitiveness and meet the ever-growing demands of various industries.
From advanced CNC systems and superabrasives to intelligent monitoring and simulation software, these advancements are revolutionizing precision grinding.
By embracing these innovations, manufacturers can achieve higher efficiency, improved quality, and reduced costs, securing their place in an increasingly competitive market.
資料ダウンロード
QCD調達購買管理クラウド「newji」は、調達購買部門で必要なQCD管理全てを備えた、現場特化型兼クラウド型の今世紀最高の購買管理システムとなります。
ユーザー登録
調達購買業務の効率化だけでなく、システムを導入することで、コスト削減や製品・資材のステータス可視化のほか、属人化していた購買情報の共有化による内部不正防止や統制にも役立ちます。
NEWJI DX
製造業に特化したデジタルトランスフォーメーション(DX)の実現を目指す請負開発型のコンサルティングサービスです。AI、iPaaS、および先端の技術を駆使して、製造プロセスの効率化、業務効率化、チームワーク強化、コスト削減、品質向上を実現します。このサービスは、製造業の課題を深く理解し、それに対する最適なデジタルソリューションを提供することで、企業が持続的な成長とイノベーションを達成できるようサポートします。
オンライン講座
製造業、主に購買・調達部門にお勤めの方々に向けた情報を配信しております。
新任の方やベテランの方、管理職を対象とした幅広いコンテンツをご用意しております。
お問い合わせ
コストダウンが利益に直結する術だと理解していても、なかなか前に進めることができない状況。そんな時は、newjiのコストダウン自動化機能で大きく利益貢献しよう!
(Β版非公開)