- お役立ち記事
- Technologies and Applications of MEMS (Micro-Electro-Mechanical Systems) in Manufacturing
月間76,176名の
製造業ご担当者様が閲覧しています*
*2025年3月31日現在のGoogle Analyticsのデータより
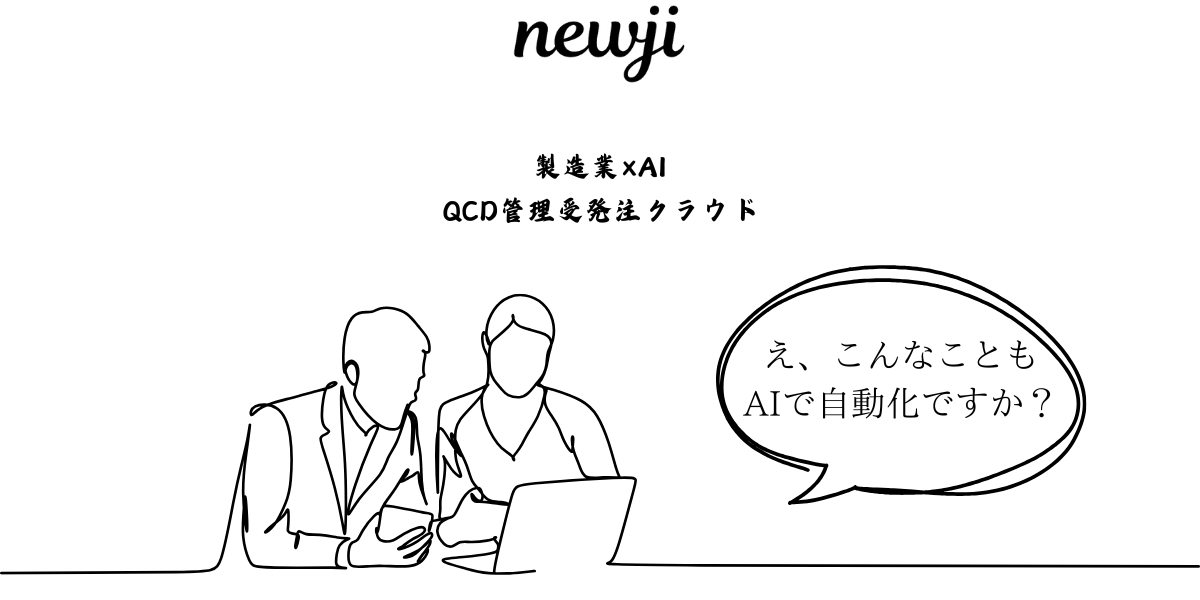
Technologies and Applications of MEMS (Micro-Electro-Mechanical Systems) in Manufacturing
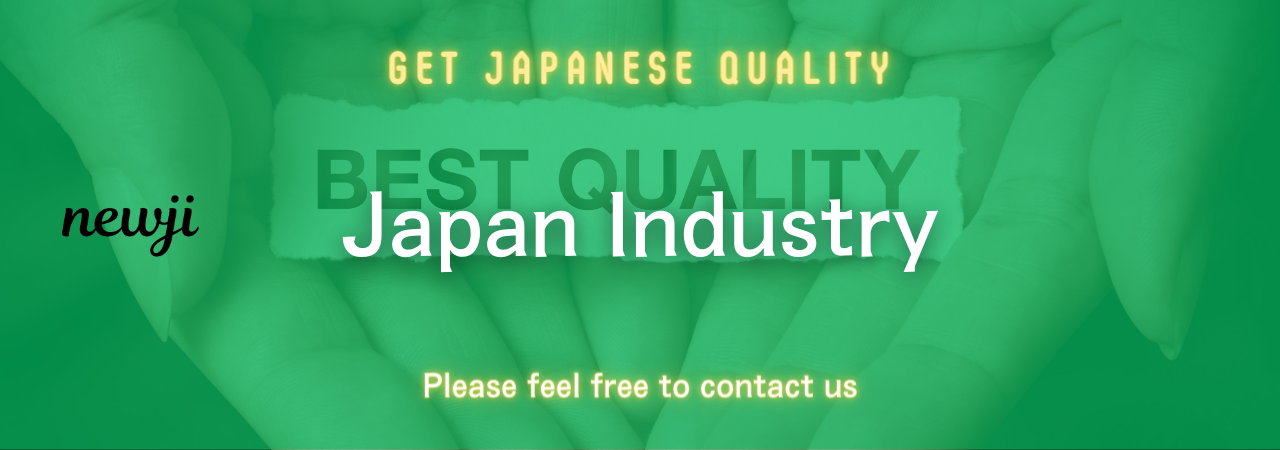
目次
What Are Micro-Electro-Mechanical Systems?
Micro-Electro-Mechanical Systems, often abbreviated as MEMS, are tiny mechanical devices built on silicon wafers.
These minute devices integrate electrical and mechanical components at the microscopic level.
This technology combines microelectronics and micromachining, allowing for the development of highly advanced gadgets.
MEMS devices can include a variety of components, such as sensors, actuators, and microstructures.
The Core Technologies Behind MEMS
Several key technologies drive the development and functionality of MEMS.
Understanding these foundational technologies is essential for grasping the full potential and applications of MEMS in manufacturing.
Microfabrication
Microfabrication refers to the processes involved in creating these minuscule devices.
These processes include lithography, etching, and deposition, which allow for the precise construction of micro-level components.
Microfabrication plays a crucial role in defining the structure and function of MEMS devices.
Microelectronics
Microelectronics forms the backbone of MEMS, responsible for creating the electrical aspects of these systems.
It involves using semiconductors to build circuits at a microscopic scale.
This technology enables the integration of sensors and actuators into a single chip, enhancing device performance and reliability.
Micromachining
Micromachining refers to the techniques used to shape the microstructures within MEMS devices.
It includes a variety of techniques like bulk micromachining, surface micromachining, and high-aspect ratio micromachining.
These methods are crucial for achieving the desired mechanical attributes of the MEMS components.
Applications of MEMS in Manufacturing
MEMS technology has a broad range of applications in the manufacturing sector.
Let’s explore some of the most prominent uses.
Precision Measurement and Sensing
MEMS sensors can measure various physical parameters such as pressure, temperature, and acceleration with high accuracy.
In manufacturing, these sensors are vital for monitoring and controlling processes.
For example, MEMS pressure sensors are used in hydraulic systems to ensure optimal performance.
Temperature sensors help in regulating thermal processes, ensuring consistent product quality.
Additionally, accelerometers can detect vibrations, helping to prevent equipment failures.
Automotive Industry
The automotive industry heavily relies on MEMS technology for improving vehicle performance and safety.
Airbag systems use MEMS accelerometers to detect collisions and deploy airbags promptly.
MEMS gyroscopes assist in vehicle stability control, making driving safer.
Moreover, MEMS sensors monitor tire pressure, providing drivers with crucial information to prevent accidents.
Manufacturing Automation
In automated manufacturing processes, MEMS devices are indispensable.
These systems enable precise positioning and movement control, vital for robotic arms and automated assembly lines.
By integrating MEMS sensors and actuators, manufacturers can achieve fine control over their machinery, enhancing efficiency and reducing errors.
Quality Control
Quality control is crucial in manufacturing, and MEMS technology significantly contributes to this area.
MEMS-based inspection tools can detect defects at a microscopic level, ensuring that only high-quality products leave the production line.
These tools can be used in various industries, from semiconductor manufacturing to pharmaceutical production.
The Advantages of MEMS in Manufacturing
MEMS technology offers several notable advantages that make it indispensable in modern manufacturing.
Miniaturization
One of the most significant benefits of MEMS is their compact size.
This miniaturization allows manufacturers to design smaller, more efficient devices and systems.
For instance, in the medical industry, MEMS enable the creation of micro-implants and wearable health monitors.
High Precision
MEMS devices offer extremely high precision, which is essential in applications requiring meticulous control.
For example, in aerospace manufacturing, MEMS gyroscopes help in navigation systems by providing accurate orientation data.
Low Power Consumption
Compared to traditional mechanical systems, MEMS devices consume remarkably less power.
This efficiency makes them ideal for portable and battery-operated devices, like smartphones and wearable technology.
Cost-Efficiency
Once the initial development costs are covered, MEMS technology can be highly cost-effective.
Using silicon-based fabrication processes, MEMS devices can be produced in large quantities, reducing the per-unit cost.
Challenges and Future Directions
While MEMS technology has numerous advantages, it also faces certain challenges that need to be addressed.
Fabrication Complexity
Creating MEMS devices involves intricate fabrication processes.
Achieving high yields can be challenging, requiring advancements in microfabrication techniques to improve efficiency and reduce costs.
Reliability
Another challenge is ensuring the long-term reliability of MEMS devices.
Mechanical wear and environmental factors can affect performance over time.
Ongoing research aims to enhance the durability and longevity of these devices.
Integration with Other Systems
Integrating MEMS devices with other electronic systems can be complex.
Seamless integration requires development in interface technologies to ensure compatibility and optimal performance.
Future Prospects
The future of MEMS technology in manufacturing looks promising.
As microfabrication and micromachining technologies continue to advance, the capabilities and applications of MEMS are expected to expand.
Innovations in materials science and nanotechnology will further enhance MEMS, leading to even more sophisticated manufacturing solutions.
MEMS is a cutting-edge technology revolutionizing the manufacturing sector.
From precision sensing to automation and quality control, its applications are vast and varied.
Despite certain challenges, the numerous advantages of MEMS make it a vital component of modern manufacturing.
As research and development continue, MEMS is poised to play an even more significant role in the industry’s future.
資料ダウンロード
QCD管理受発注クラウド「newji」は、受発注部門で必要なQCD管理全てを備えた、現場特化型兼クラウド型の今世紀最高の受発注管理システムとなります。
ユーザー登録
受発注業務の効率化だけでなく、システムを導入することで、コスト削減や製品・資材のステータス可視化のほか、属人化していた受発注情報の共有化による内部不正防止や統制にも役立ちます。
NEWJI DX
製造業に特化したデジタルトランスフォーメーション(DX)の実現を目指す請負開発型のコンサルティングサービスです。AI、iPaaS、および先端の技術を駆使して、製造プロセスの効率化、業務効率化、チームワーク強化、コスト削減、品質向上を実現します。このサービスは、製造業の課題を深く理解し、それに対する最適なデジタルソリューションを提供することで、企業が持続的な成長とイノベーションを達成できるようサポートします。
製造業ニュース解説
製造業、主に購買・調達部門にお勤めの方々に向けた情報を配信しております。
新任の方やベテランの方、管理職を対象とした幅広いコンテンツをご用意しております。
お問い合わせ
コストダウンが利益に直結する術だと理解していても、なかなか前に進めることができない状況。そんな時は、newjiのコストダウン自動化機能で大きく利益貢献しよう!
(β版非公開)