- お役立ち記事
- Technologies for Optimizing Cooling Time to Improve Molding Cycle Efficiency
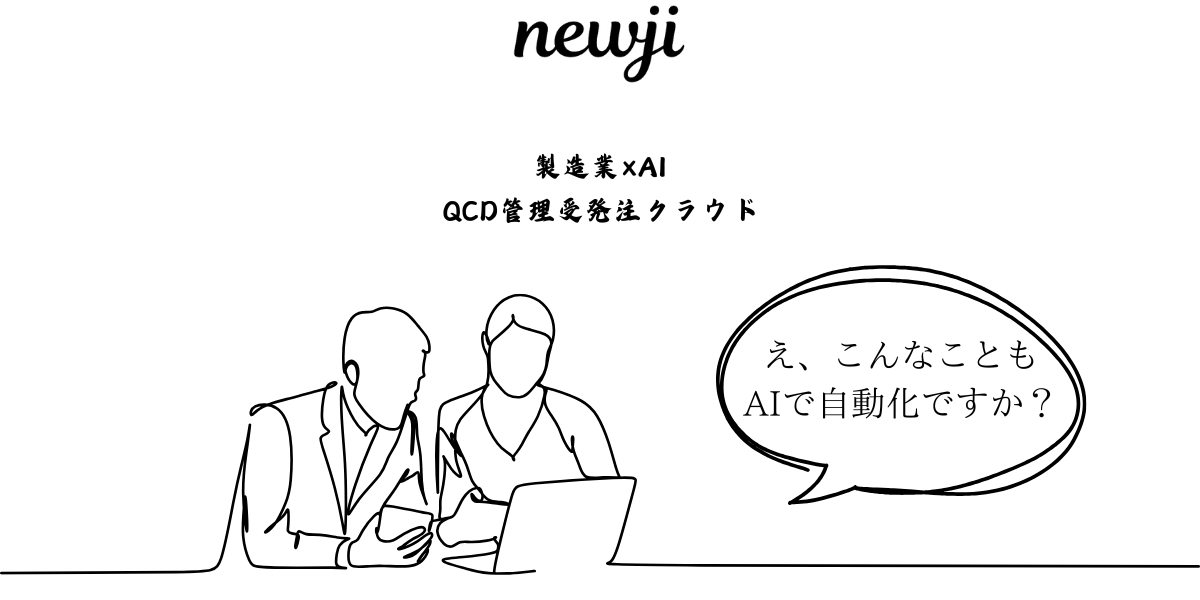
Technologies for Optimizing Cooling Time to Improve Molding Cycle Efficiency
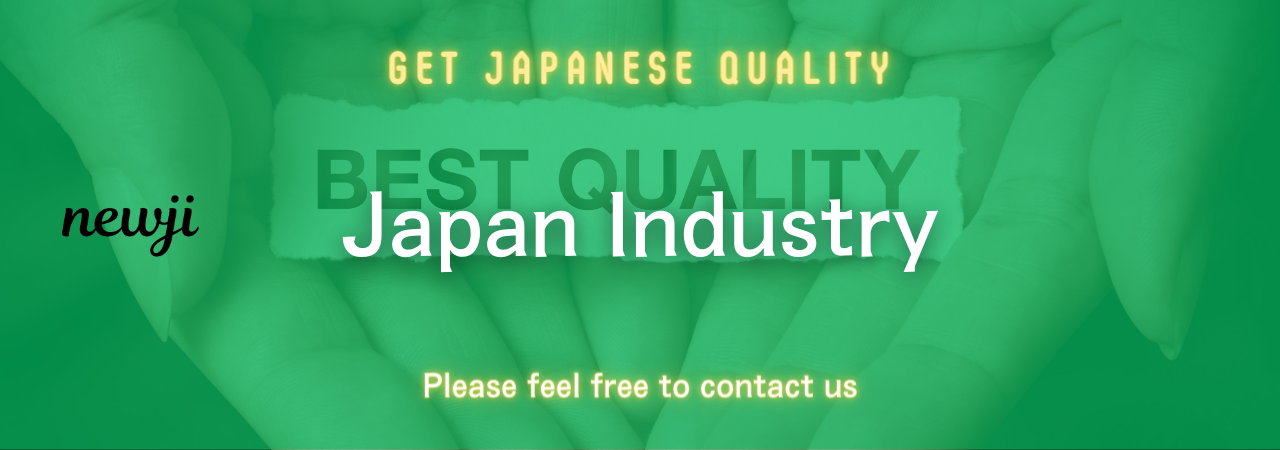
目次
Introduction to Molding Cycle Efficiency
In the manufacturing industry, especially in the realm of plastic manufacturing, optimizing the molding cycle is crucial for improving productivity and reducing costs.
One significant aspect of this optimization is managing the cooling time during the molding process.
By understanding and implementing advanced technologies to optimize cooling times, manufacturers can significantly enhance their cycle efficiency and output quality.
Understanding Cooling Time in Molding
Cooling time is a critical phase in the plastic molding process.
Once the molten material is shaped in the mold, it needs to cool down and solidify before the mold can be opened, and a new cycle can begin.
The duration of this cooling process directly impacts the overall cycle time and, consequently, the manufacturing throughput.
Reducing the cooling time without compromising the quality of the product is a key objective for many manufacturers.
Technological Innovations in Cooling Optimization
Recent years have seen several technological advancements aimed at optimizing the cooling phase of the molding cycle.
Here, we explore some of the most promising innovations:
Conformal Cooling Channels
Conformal cooling channels are designed to match the geometry of the part and the mold.
Unlike traditional straight-drilled channels, conformal cooling channels are created using advanced techniques such as 3D printing.
This results in a mold with cooling channels that are closer to the surface of the molded part, allowing for uniform cooling and significant reductions in cooling time.
Rapid Heat Cycle Molding
Rapid heat cycle molding, also known as rapid temperature cycling, involves alternately heating and cooling the mold within a single cycle.
This technology enables better control over the molding temperature, improving the surface finish and reducing stress-related defects in the parts.
The dynamic temperature control not only shortens the cycle time but also enhances the quality and durability of the finished product.
Advanced Cooling Fluids
The use of advanced cooling fluids with better thermal conductivity can also optimize the cooling process.
Nanofluids, for example, are engineered fluids with exceptional heat transfer properties.
These fluids replace conventional water-based systems, facilitating faster heat removal from the mold and accelerating the cooling phase.
The Role of Simulation Software
Simulation software plays a vital role in optimizing cooling time.
With advanced simulation tools, manufacturers can predict the thermal behavior of the mold and the part within it.
This allows engineers to experiment with different cooling methods and configurations virtually, saving time and resources.
By analyzing the data provided by these simulations, manufacturers can identify and implement the most efficient cooling strategies in their real-world processes.
Benefits of Optimized Cooling in Molding
An optimized cooling phase offers numerous benefits, including:
Reduced Cycle Time
Reducing the cooling time directly leads to shorter cycle times.
This means more parts can be produced within the same timeframe, significantly boosting manufacturing efficiency and output.
Improved Product Quality
Uniform and efficient cooling results in products with better surface finish and dimensional accuracy.
It also reduces the possibility of defects such as warping and sink marks.
Energy Efficiency
Efficient cooling systems reduce energy consumption, contributing to lower operating costs and a smaller carbon footprint, which aligns with sustainable manufacturing practices.
Challenges in Cooling Time Optimization
While the technologies for optimizing cooling time offer great potential, implementing them comes with its own set of challenges.
The initial investment for implementing new technologies like 3D-printed molds or rapid heat cycle molding systems can be high.
Furthermore, adapting existing processes to incorporate these technologies may require significant changes in workflow and retraining staff.
Moreover, each solution needs to be tailored to the specific requirements of the individual manufacturing process, which might involve trial and error.
Conclusion
Technologies for optimizing cooling time are pivotal for enhancing the efficiency of the molding cycle.
By embracing innovations such as conformal cooling channels, rapid heat cycle molding, and advanced cooling fluids, manufacturers can significantly improve their cycle times and product quality.
Although challenges exist, the benefits of reduced costs, higher efficiency, and improved environmental sustainability present compelling reasons for manufacturers to consider these technologies.
As technology continues to evolve, the possibilities for further optimizing the molding process are endless, paving the way for even greater efficiency and innovation in the industry.
資料ダウンロード
QCD調達購買管理クラウド「newji」は、調達購買部門で必要なQCD管理全てを備えた、現場特化型兼クラウド型の今世紀最高の購買管理システムとなります。
ユーザー登録
調達購買業務の効率化だけでなく、システムを導入することで、コスト削減や製品・資材のステータス可視化のほか、属人化していた購買情報の共有化による内部不正防止や統制にも役立ちます。
NEWJI DX
製造業に特化したデジタルトランスフォーメーション(DX)の実現を目指す請負開発型のコンサルティングサービスです。AI、iPaaS、および先端の技術を駆使して、製造プロセスの効率化、業務効率化、チームワーク強化、コスト削減、品質向上を実現します。このサービスは、製造業の課題を深く理解し、それに対する最適なデジタルソリューションを提供することで、企業が持続的な成長とイノベーションを達成できるようサポートします。
オンライン講座
製造業、主に購買・調達部門にお勤めの方々に向けた情報を配信しております。
新任の方やベテランの方、管理職を対象とした幅広いコンテンツをご用意しております。
お問い合わせ
コストダウンが利益に直結する術だと理解していても、なかなか前に進めることができない状況。そんな時は、newjiのコストダウン自動化機能で大きく利益貢献しよう!
(Β版非公開)