- お役立ち記事
- Technologies for Optimizing Molding Cycle Times to Improve Productivity
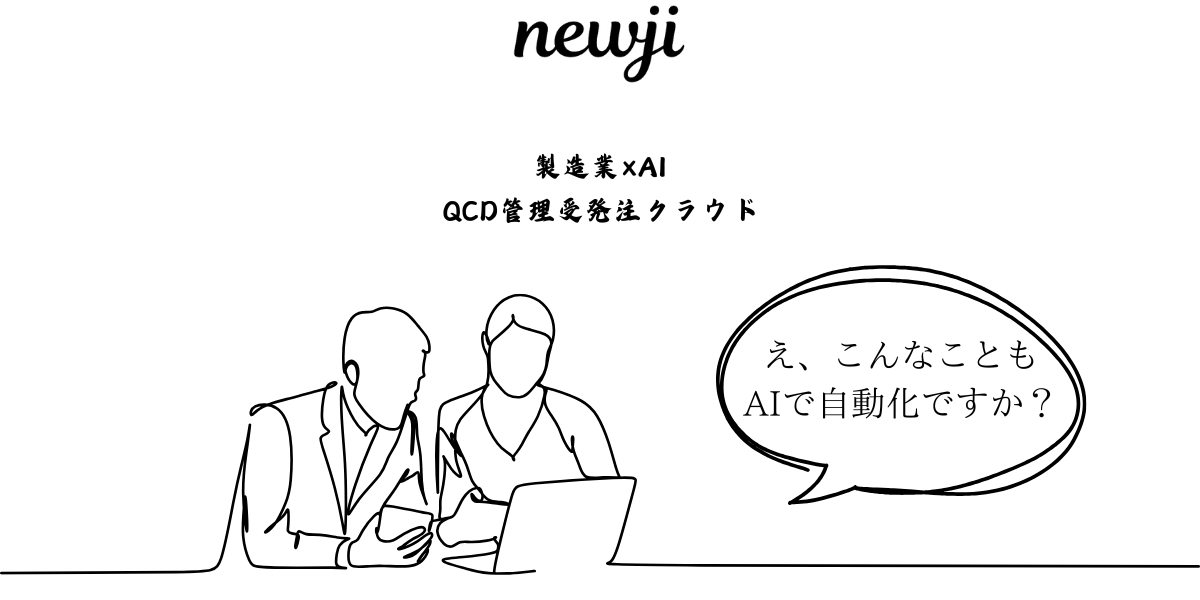
Technologies for Optimizing Molding Cycle Times to Improve Productivity
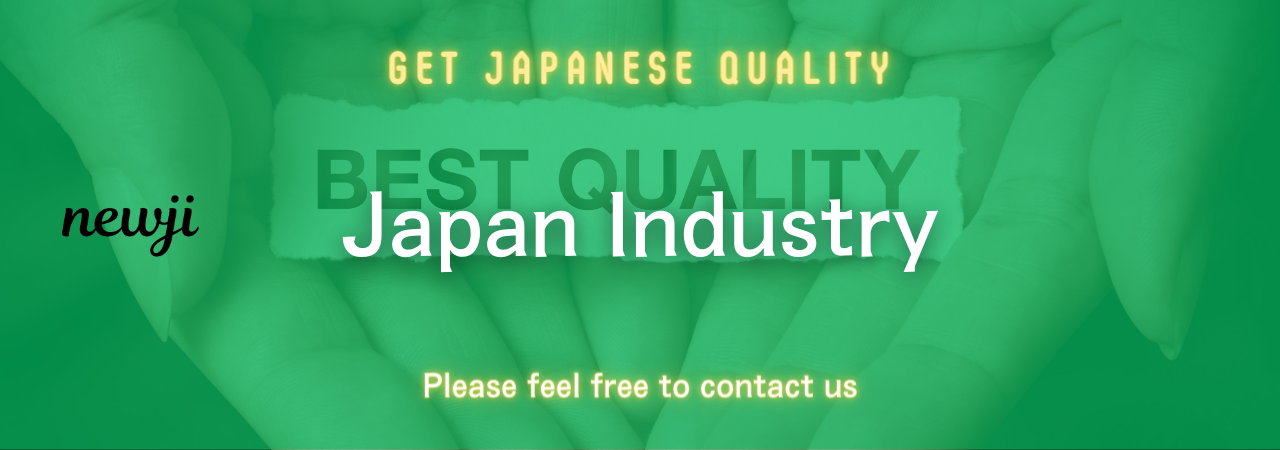
目次
Introduction to Molding Cycle Times
Molding is a critical process in manufacturing where raw materials are shaped into desired forms using molds.
Molding cycle time refers to the duration it takes to complete a single molding operation, from the closing of the mold to the ejection of the final product.
Optimizing molding cycle times is essential for enhancing productivity, reducing costs, and improving overall manufacturing efficiency.
By focusing on this aspect, manufacturers can gain a competitive edge in the market.
Understanding Molding Cycle Components
To effectively optimize cycle times, it is important to understand the various components involved in the molding process.
Injection Stage
The injection stage is the first and often the most time-consuming part of the cycle.
During this phase, raw materials, usually in the form of pellets or powder, are heated until molten and injected into a mold cavity.
The injection time depends on factors such as material viscosity, pressure, and the geometry of the part being molded.
Optimizing injection speed and pressure can significantly reduce cycle times while ensuring high-quality product formation.
Cooling Stage
After the material is injected, it needs to cool and solidify within the mold cavity.
Cooling time accounts for a substantial portion of the overall cycle time.
Efficient cooling is critical as it directly affects part quality and cycle time.
Techniques such as optimizing mold design, using efficient cooling channels, and employing thermal analysis software can help reduce cooling duration.
Ejection Stage
Once the material is solidified, the mold opens, and the finished product is ejected.
This stage, though comparatively shorter than injection and cooling, still offers opportunities for optimization.
Ensuring proper mold release techniques, using suitable mold release agents, and timely maintenance of ejection systems can lead to smoother and faster ejection processes.
Technologies for Cycle Time Optimization
Various technologies and strategies can be employed to optimize molding cycle times.
Advanced Mold Materials
The choice of mold material can have a significant impact on cycle times.
Using advanced materials with better thermal conductivity, such as aluminum alloys, can reduce cooling times as they dissipate heat quicker than traditional steel molds.
This leads to faster production without compromising on the quality of the molded parts.
Computer-Aided Design (CAD) and Simulation Tools
Modern CAD and simulation tools allow engineers to design molds with precision and analyze the flow of materials and heat dissipation.
These tools help identify potential bottlenecks and optimize mold design for quicker cycle times.
Virtual simulations enable manufacturers to test different scenarios before physical production, saving time and resources.
Robotics and Automation
Implementing robotics and automation in the molding process can significantly boost productivity.
Automated systems handle tasks like part removal, inspection, and packaging, reducing idle time between cycles.
Robots also contribute to a consistent and repeatable process, minimizing human error and enhancing overall efficiency.
Real-Time Monitoring Systems
Real-time monitoring systems track key parameters such as temperature, pressure, and cycle times across the molding process.
With this data, manufacturers can make data-driven decisions to quickly address any issues, adjust process variables, and maintain optimal conditions.
These systems help in identifying unexpected variances and allow for quick corrective action, leading to reduced cycle times.
Best Practices for Cycle Time Reduction
In addition to adopting advanced technologies, implementing best practices can further optimize cycle times.
Regular Maintenance and Mold Care
Scheduled maintenance of molds and machinery prevents unexpected downtime and ensures smooth operations.
Proper care includes timely cleaning, inspection for wear and tear, and repair of molds and related equipment.
Maintaining molds in optimal condition minimizes defects and speeds up the molding process.
Training and Skill Development
Investing in employee training and skill development ensures operators are knowledgeable about the latest technologies and optimization strategies.
Skilled operators can efficiently manage machines, identify potential issues early, and implement the best practices for optimized cycle times.
Lean Manufacturing Principles
Applying lean manufacturing principles such as reducing waste, streamlining processes, and employing continuous improvement methodologies can enhance overall efficiency.
Lean techniques ensure each step of the molding process adds value, thereby reducing unnecessary cycle delays and boosting productivity.
Conclusion
Optimizing molding cycle times is crucial for manufacturers aiming to improve productivity and maintain high-quality standards.
By understanding the components of the molding cycle and employing advanced technologies such as CAD tools, robotics, and real-time monitoring systems, manufacturers can achieve significant efficiency gains.
Coupled with best practices like regular maintenance, employee training, and lean principles, these strategies help create a competitive manufacturing environment capable of meeting market demands efficiently.
As technology advances, continuous efforts in optimizing cycle times will contribute to sustained growth and success in the manufacturing sector.
資料ダウンロード
QCD調達購買管理クラウド「newji」は、調達購買部門で必要なQCD管理全てを備えた、現場特化型兼クラウド型の今世紀最高の購買管理システムとなります。
ユーザー登録
調達購買業務の効率化だけでなく、システムを導入することで、コスト削減や製品・資材のステータス可視化のほか、属人化していた購買情報の共有化による内部不正防止や統制にも役立ちます。
NEWJI DX
製造業に特化したデジタルトランスフォーメーション(DX)の実現を目指す請負開発型のコンサルティングサービスです。AI、iPaaS、および先端の技術を駆使して、製造プロセスの効率化、業務効率化、チームワーク強化、コスト削減、品質向上を実現します。このサービスは、製造業の課題を深く理解し、それに対する最適なデジタルソリューションを提供することで、企業が持続的な成長とイノベーションを達成できるようサポートします。
オンライン講座
製造業、主に購買・調達部門にお勤めの方々に向けた情報を配信しております。
新任の方やベテランの方、管理職を対象とした幅広いコンテンツをご用意しております。
お問い合わせ
コストダウンが利益に直結する術だと理解していても、なかなか前に進めることができない状況。そんな時は、newjiのコストダウン自動化機能で大きく利益貢献しよう!
(Β版非公開)