- お役立ち記事
- Technology and quality control required in the assembly of aluminum frame structures
月間76,176名の
製造業ご担当者様が閲覧しています*
*2025年3月31日現在のGoogle Analyticsのデータより
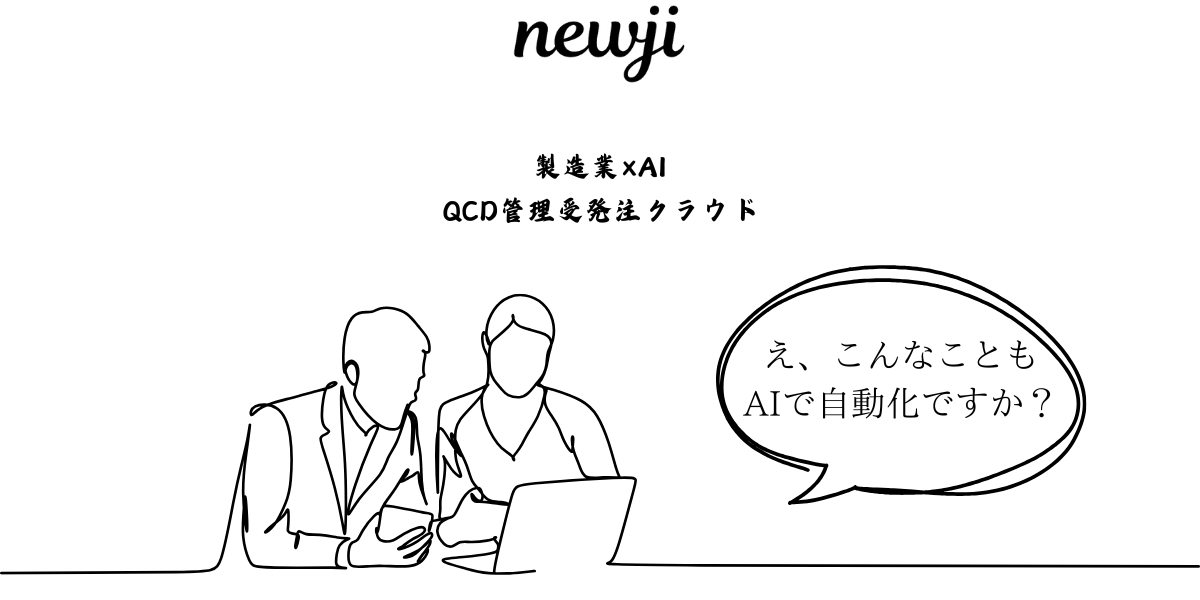
Technology and quality control required in the assembly of aluminum frame structures
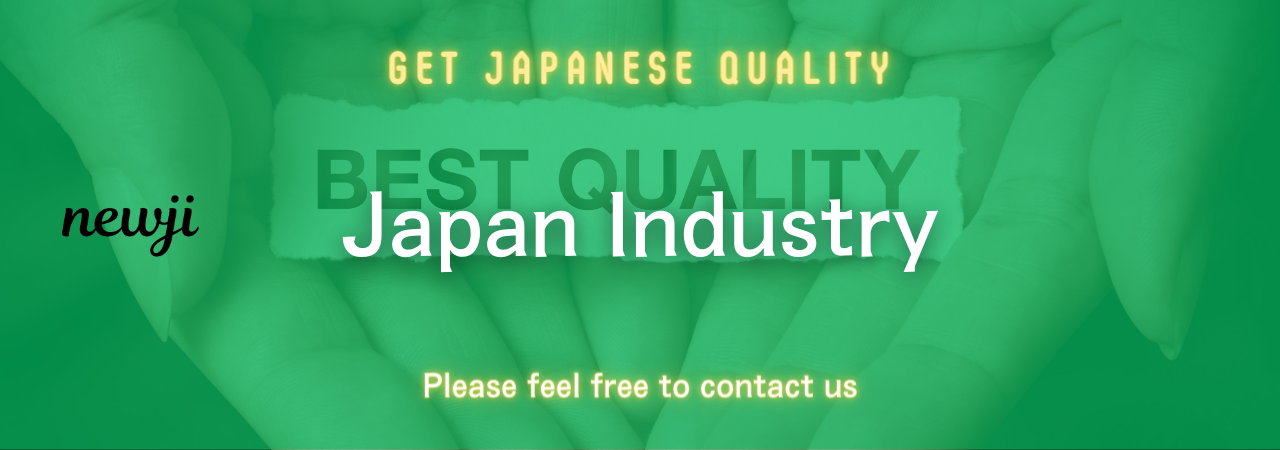
目次
Introduction to Aluminum Frame Structures
Aluminum frame structures are widely used in various industries due to their numerous benefits.
These structures are known for their strength, lightweight nature, and resistance to corrosion, which make them ideal for applications in construction, transportation, and manufacturing.
In recent years, the demand for aluminum frames has increased significantly as industries seek to leverage these advantages.
With the growing use of aluminum frames, quality control and technology have become critical aspects of their assembly.
Ensuring the reliability and durability of aluminum structures involves careful attention to detail during the manufacturing process.
This article discusses the technology and quality control measures required in the assembly of aluminum frame structures to help maintain high standards.
Technology in Aluminum Frame Assembly
Technology plays a vital role in the assembly of aluminum frame structures.
Advancements in manufacturing processes have led to more efficient and precise methods for creating these frames.
Let’s take a look at some of the key technologies used in aluminum frame assembly.
CNC Machining
Computer Numerical Control (CNC) machining is a manufacturing process that uses computerized controls to operate tools and machinery.
This technology is crucial in the assembly of aluminum frames, as it allows for precise cutting and shaping of metal components.
CNC machines are capable of producing complex designs with high accuracy, which contributes to the overall quality of the frame.
Robotic Welding
Robotic welding is another technological advancement that has significantly improved the assembly of aluminum frame structures.
This automated process uses robots to perform welding tasks, ensuring consistent and high-quality welds.
Robotic welding minimizes human error, reduces production time, and enhances safety by keeping workers away from potentially hazardous environments.
3D Printing
Although still emerging, 3D printing is becoming an essential technology in aluminum frame assembly.
3D printing allows manufacturers to create prototypes and custom parts with ease, enabling rapid iteration and testing of designs.
It also reduces waste and material costs, as parts are constructed layer by layer rather than cut from larger sections.
Quality Control in Assembly
Quality control is a critical aspect of aluminum frame assembly, ensuring that structures meet industry standards and client expectations.
Several measures are implemented to maintain high levels of quality throughout the manufacturing process.
Material Inspection
Before assembly, it’s essential to conduct thorough inspections of the aluminum materials used.
This process involves evaluating the material’s chemical composition, strength, and resistance to corrosion.
By ensuring that high-quality aluminum is used, manufacturers can maintain the integrity and durability of the frame.
Dimensional Analysis
Dimensional analysis is the process of measuring and verifying the dimensions of aluminum components during assembly.
This ensures that each part fits precisely within the design specifications, reducing the risk of structural weaknesses or failures.
Advanced measurement tools like laser scanners and coordinate measuring machines are often used for this purpose.
Stress Testing
Stress testing is an essential quality control measure that evaluates the frame’s ability to withstand various forces and loads.
This testing simulates real-world conditions to identify any potential points of failure.
By addressing these issues during the assembly process, manufacturers can improve the safety and reliability of the aluminum structure.
Environmental Testing
Aluminum frame structures are often exposed to harsh environmental conditions, such as extreme temperatures, humidity, and UV radiation.
Environmental testing ensures that the frame can maintain its integrity and performance under these conditions.
This testing includes evaluating the frame’s resistance to corrosion, moisture, and thermal expansion.
The Role of Skilled Workers
While technology and quality control measures are essential in aluminum frame assembly, the role of skilled workers should not be underestimated.
Experienced technicians and engineers play a crucial role in overseeing the manufacturing process and ensuring that all procedures are followed correctly.
They are responsible for interpreting design specifications, operating machinery, and addressing any issues that arise during assembly.
Efforts must be made to continuously train and educate workers on the latest technology and quality control techniques.
This not only enhances their skills but also ensures that they are up-to-date with industry standards and best practices.
Challenges in Aluminum Frame Assembly
Despite the advancements in technology and quality control, assembling aluminum frame structures comes with its own set of challenges.
Some of these challenges include:
Material Handling
Aluminum can be difficult to handle due to its lightweight nature and susceptibility to deformation.
Challenges in material handling can lead to defects or misalignments during assembly.
Heat Treatment
Aluminum requires precise heat treatment processes to achieve the desired strength and hardness.
Improper heat treatment can result in material weaknesses and compromise the frame’s integrity.
Cost Management
Balancing the cost of advanced technology and maintaining high-quality standards can be challenging.
Manufacturers need to implement cost-effective solutions without compromising on quality.
Conclusion
The assembly of aluminum frame structures requires a combination of advanced technology, stringent quality control measures, and skilled labor.
By leveraging the latest technologies such as CNC machining, robotic welding, and 3D printing, manufacturers can produce high-quality aluminum frames with precision and efficiency.
Quality control measures such as material inspection, dimensional analysis, and stress testing ensure that aluminum structures meet industry standards and are reliable for their intended applications.
Despite the challenges, continuous innovation and training can help manufacturers overcome obstacles and continue to produce superior aluminum frame structures.
資料ダウンロード
QCD管理受発注クラウド「newji」は、受発注部門で必要なQCD管理全てを備えた、現場特化型兼クラウド型の今世紀最高の受発注管理システムとなります。
ユーザー登録
受発注業務の効率化だけでなく、システムを導入することで、コスト削減や製品・資材のステータス可視化のほか、属人化していた受発注情報の共有化による内部不正防止や統制にも役立ちます。
NEWJI DX
製造業に特化したデジタルトランスフォーメーション(DX)の実現を目指す請負開発型のコンサルティングサービスです。AI、iPaaS、および先端の技術を駆使して、製造プロセスの効率化、業務効率化、チームワーク強化、コスト削減、品質向上を実現します。このサービスは、製造業の課題を深く理解し、それに対する最適なデジタルソリューションを提供することで、企業が持続的な成長とイノベーションを達成できるようサポートします。
製造業ニュース解説
製造業、主に購買・調達部門にお勤めの方々に向けた情報を配信しております。
新任の方やベテランの方、管理職を対象とした幅広いコンテンツをご用意しております。
お問い合わせ
コストダウンが利益に直結する術だと理解していても、なかなか前に進めることができない状況。そんな時は、newjiのコストダウン自動化機能で大きく利益貢献しよう!
(β版非公開)