- お役立ち記事
- Technology for improving pressure resistance of automobile valves and improving engine efficiency
月間77,185名の
製造業ご担当者様が閲覧しています*
*2025年2月28日現在のGoogle Analyticsのデータより
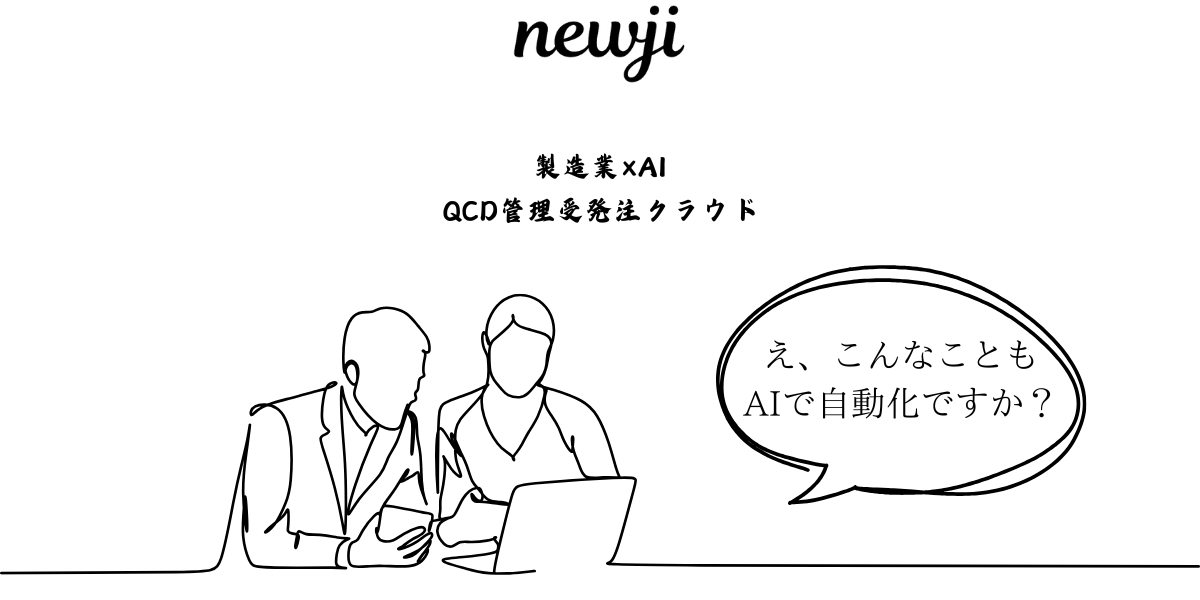
Technology for improving pressure resistance of automobile valves and improving engine efficiency
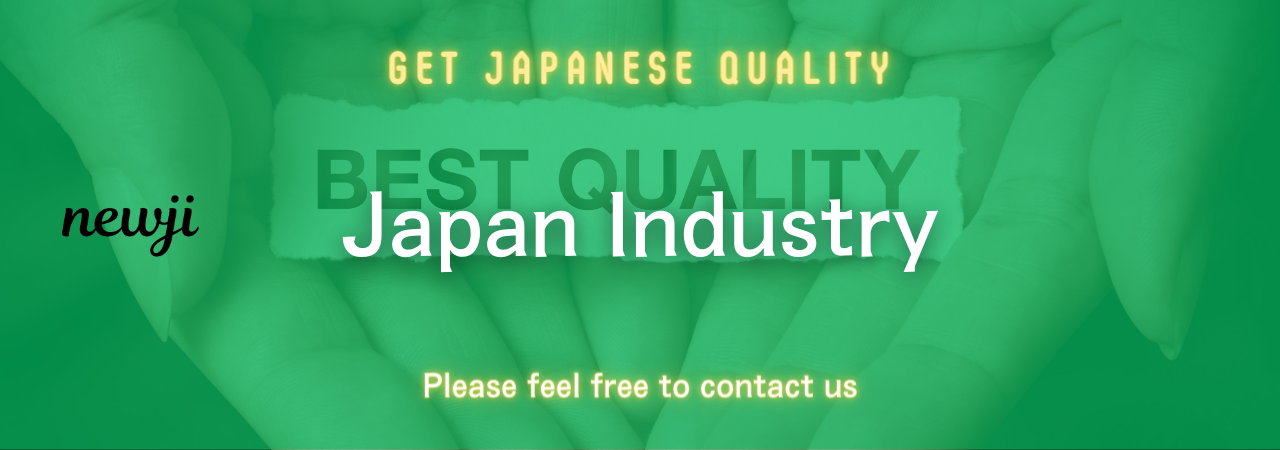
目次
Understanding Automobile Valve Pressure Resistance
In the world of automotive engineering, one key component often overlooked by casual observers is the valve system.
Automobile valves play a critical role in controlling the flow of fuel and air into the engine, as well as managing the exhaust gases leaving it.
A fundamental aspect of these valves is their ability to withstand high pressure within the engine.
Thus, improving pressure resistance is crucial not just for durability, but also for enhancing engine efficiency.
Automobile valves are typically subjected to high combustion pressures and steep temperature gradients.
This makes them vulnerable to wear and damage over time.
Strengthening their pressure resistance involves using advanced materials and manufacturing techniques, which can lead to better performance and longevity.
Advanced Materials for Valve Construction
To increase the pressure resistance of automobile valves, manufacturers often turn to cutting-edge materials.
Traditionally, valves were made from steel alloys, but today’s high-performance valves frequently incorporate exotic elements like titanium and Inconel.
Titanium is lauded for its light weight and excellent mechanical properties, making it ideal for high-stress environments.
By reducing the overall weight of the valve, the engine’s moving parts operate more freely, enhancing fuel efficiency.
Inconel, a nickel-chromium-based super alloy, is another popular choice for its exceptional strength and resistance to heat and corrosion.
This makes it ideal for high-temperature applications, ensuring that the valves can withstand the intense conditions within the combustion chamber without degrading.
By choosing the appropriate materials, engineers can significantly enhance the pressure resistance of valves, contributing to overall engine longevity and performance.
Optimizing Valve Design
Beyond material selection, the design of the valve plays a significant role in its ability to withstand pressure.
Engineers continually innovate in valve design to optimize engine dynamics and efficiency.
The shape of the valve head is particularly important.
A well-crafted valve head can facilitate better airflow, leading to improved combustion efficiency.
Designs such as tulip and flat head styles each have their own benefits depending on the specific engine requirements.
Furthermore, advanced simulation software enables precise modeling of air and fuel flow dynamics.
These tools allow engineers to test different valve designs in a virtual environment, identifying the most effective configurations for pressure resistance and efficiency without the need for costly physical prototypes.
Improving Surface Treatments
Engine manufacturers also employ a variety of surface treatment techniques to enhance valve durability and pressure resistance.
These treatments create a hardened exterior that can withstand the high pressures and temperatures experienced during operation.
One common treatment is nitriding, which diffuses nitrogen into the surface of the valve, enhancing its hardness and wear resistance.
Similarly, PVD (Physical Vapor Deposition) coatings can increase surface strength while reducing friction, leading to smoother operation and reduced wear.
Such treatments not only improve pressure resistance but also contribute to more efficient engine functioning by ensuring consistent valve performance over time.
The Role of Precision Manufacturing
In achieving optimal valve pressure resistance, precision in manufacturing cannot be overstated.
The production process needs to adhere to stringent tolerances to ensure all valve components fit perfectly within the engine assembly.
State-of-the-art CNC (Computer Numerical Control) machines are often employed to produce valve components with high precision.
These machines can carve out intricate designs required for modern valve technology with exceptional accuracy, ensuring each valve is of the highest quality.
Moreover, manufacturers employ rigorous quality control measures to identify any defects early in the manufacturing process.
This minimizes the risk of failure under pressure, safeguarding both the vehicle’s engine and the driver.
Innovative Testing Protocols
To guarantee the effectiveness of the materials, design, and manufacturing methods used, rigorous testing is necessary.
Manufacturers implement comprehensive testing protocols to validate the pressure resistance and efficiency of the valves.
Endurance tests simulate the stresses valves will encounter in real-world conditions.
By subjecting valves to prolonged high-pressure cycles, engineers can observe their durability and identify potential areas for improvement.
Advanced techniques such as thermal imaging and acoustic emission testing can detect even the smallest signs of wear or damage that may not be visible to the naked eye.
These tests provide insight into how valves behave under stress, informing further enhancements in pressure resistance technology.
Benefits of Improved Pressure Resistance
Enhancing the pressure resistance of automobile valves has several tangible benefits for engine efficiency.
Firstly, it leads to improved combustion efficiency.
This means better fuel economy and reduced emissions as the engine burns fuel more completely and effectively.
Moreover, robust valves reduce the likelihood of premature engine wear and failure.
This not only prolongs the life of the engine but also ensures consistent performance over time, which is a huge benefit for consumers and manufacturers alike.
Finally, with improved pressure resistance, engines can operate at higher stresses, potentially unlocking new levels of power and performance.
This can lead to faster vehicles or more efficient use of resources, depending on the design goals.
In conclusion, the technology for improving the pressure resistance of automobile valves is crucial for advancing engine efficiency.
Through advanced materials, precision engineering, and rigorous testing, the automotive industry continues to push the boundaries of what engines can achieve, leading to vehicles that are not only more efficient but also more reliable and durable.
資料ダウンロード
QCD管理受発注クラウド「newji」は、受発注部門で必要なQCD管理全てを備えた、現場特化型兼クラウド型の今世紀最高の受発注管理システムとなります。
ユーザー登録
受発注業務の効率化だけでなく、システムを導入することで、コスト削減や製品・資材のステータス可視化のほか、属人化していた受発注情報の共有化による内部不正防止や統制にも役立ちます。
NEWJI DX
製造業に特化したデジタルトランスフォーメーション(DX)の実現を目指す請負開発型のコンサルティングサービスです。AI、iPaaS、および先端の技術を駆使して、製造プロセスの効率化、業務効率化、チームワーク強化、コスト削減、品質向上を実現します。このサービスは、製造業の課題を深く理解し、それに対する最適なデジタルソリューションを提供することで、企業が持続的な成長とイノベーションを達成できるようサポートします。
製造業ニュース解説
製造業、主に購買・調達部門にお勤めの方々に向けた情報を配信しております。
新任の方やベテランの方、管理職を対象とした幅広いコンテンツをご用意しております。
お問い合わせ
コストダウンが利益に直結する術だと理解していても、なかなか前に進めることができない状況。そんな時は、newjiのコストダウン自動化機能で大きく利益貢献しよう!
(β版非公開)