- お役立ち記事
- Technology of Preventive Maintenance and Its Applications in Manufacturing
Technology of Preventive Maintenance and Its Applications in Manufacturing
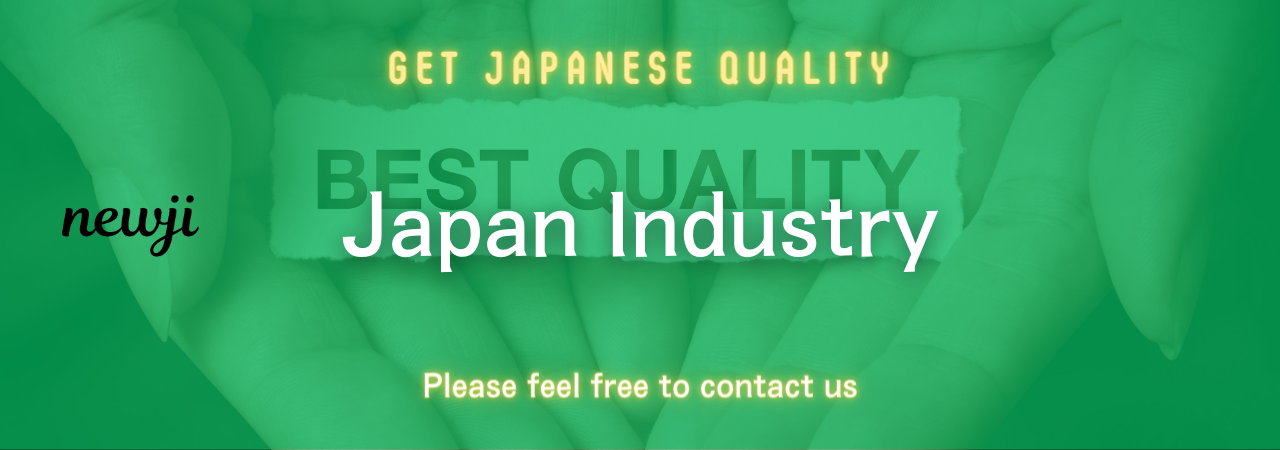
In today’s rapidly evolving industrial landscape, the efficiency and reliability of manufacturing processes are paramount.
To ensure smooth operations, it’s crucial to monitor and maintain equipment regularly.
Preventive maintenance technology has emerged as a game-changer in this regard.
This article delves into the technology of preventive maintenance and its applications in manufacturing.
目次
What is Preventive Maintenance?
Preventive maintenance, often abbreviated as PM, refers to the routine maintenance and servicing of equipment to prevent potential failures and extend its lifespan.
Unlike reactive maintenance, which addresses issues only after they arise, preventive maintenance is proactive.
It helps in identifying potential problems before they become major issues.
The Technology Behind Preventive Maintenance
Advancements in technology have revolutionized how preventive maintenance is approached.
Several key technologies play a vital role in implementing effective preventive maintenance strategies in manufacturing.
1. Internet of Things (IoT)
The Internet of Things is a network of interconnected devices equipped with sensors and software to collect and exchange data.
In the context of preventive maintenance, IoT-enabled devices monitor the health and performance of machinery in real time.
This provides valuable insights into the condition of the equipment, allowing for timely maintenance activities.
2. Predictive Analytics
Predictive analytics involves analyzing historical and real-time data to predict future trends and events.
Using machine learning algorithms and statistical models, predictive analytics can forecast potential equipment failures.
This enables manufacturers to schedule maintenance activities at the most opportune times, minimizing downtime and maximizing productivity.
3. Condition Monitoring
Condition monitoring is a technique used to assess the performance and health of machinery by continuously tracking specific parameters.
These parameters include temperature, vibration, and pressure, among others.
By monitoring these indicators, manufacturers can detect anomalies that may indicate impending equipment failure.
Early detection allows for timely intervention and prevents costly breakdowns.
4. Computerized Maintenance Management Systems (CMMS)
A CMMS is a software solution designed to streamline maintenance management processes.
It helps in planning, tracking, and documenting maintenance activities.
A CMMS can schedule preventive maintenance tasks based on equipment usage and historical performance data.
By automating these processes, manufacturers can ensure that maintenance activities are carried out systematically and efficiently.
Applications of Preventive Maintenance in Manufacturing
Preventive maintenance technology finds applications across various sectors within the manufacturing industry.
Let’s explore some key areas where it is making a significant impact.
1. Equipment Longevity
One of the primary benefits of preventive maintenance is the extension of equipment lifespan.
By regularly servicing and maintaining machinery, manufacturers can avoid premature wear and tear.
This leads to significant cost savings, as equipment replacement is often much more expensive than regular maintenance.
2. Reduced Downtime
Unexpected equipment failures can lead to costly production interruptions.
Preventive maintenance minimizes the risk of sudden breakdowns by identifying and addressing potential issues beforehand.
Scheduled maintenance activities can be planned during off-peak hours, ensuring minimal disruption to production schedules.
3. Enhanced Safety
Equipment failures can pose serious safety risks to workers.
Preventive maintenance helps in identifying hazards and addressing them before they result in accidents.
Regular inspections and maintenance activities ensure that equipment operates safely and reliably, creating a safer work environment for employees.
4. Cost Savings
While preventive maintenance requires an initial investment in terms of time and resources, it ultimately leads to cost savings.
By avoiding unexpected breakdowns and optimizing equipment performance, manufacturers can reduce repair and replacement costs.
Additionally, improved equipment efficiency results in lower operational costs over the long term.
Implementing Preventive Maintenance Programs
Implementing a successful preventive maintenance program requires careful planning and execution.
Here are some essential steps to consider:
1. Identify Critical Equipment
Start by identifying the critical equipment that plays a crucial role in your manufacturing processes.
Focus your preventive maintenance efforts on these assets to ensure optimal performance and minimize the risk of failure.
2. Develop a Maintenance Schedule
Create a maintenance schedule based on equipment usage, manufacturer recommendations, and historical performance data.
Ensure that maintenance activities are planned at appropriate intervals to prevent unexpected failures.
3. Use Technology
Leverage the latest technologies such as IoT, predictive analytics, and CMMS to monitor equipment health and streamline maintenance processes.
Invest in training your maintenance team to effectively utilize these tools for maximum benefit.
4. Monitor and Adjust
Regularly review the performance of your preventive maintenance program.
Track key metrics such as equipment uptime, maintenance costs, and failure rates.
Use this data to make informed decisions and adjust your maintenance strategies as needed.
Conclusion
In conclusion, preventive maintenance technology is a powerful tool for enhancing the efficiency and reliability of manufacturing processes.
By leveraging technologies such as IoT, predictive analytics, and condition monitoring, manufacturers can proactively identify and address potential issues.
This leads to extended equipment lifespan, reduced downtime, enhanced safety, and cost savings.
Implementing a well-planned preventive maintenance program is essential for staying competitive in today’s dynamic industrial landscape.
Embrace the power of technology and take your manufacturing operations to new heights with effective preventive maintenance strategies.
資料ダウンロード
QCD調達購買管理クラウド「newji」は、調達購買部門で必要なQCD管理全てを備えた、現場特化型兼クラウド型の今世紀最高の購買管理システムとなります。
ユーザー登録
調達購買業務の効率化だけでなく、システムを導入することで、コスト削減や製品・資材のステータス可視化のほか、属人化していた購買情報の共有化による内部不正防止や統制にも役立ちます。
NEWJI DX
製造業に特化したデジタルトランスフォーメーション(DX)の実現を目指す請負開発型のコンサルティングサービスです。AI、iPaaS、および先端の技術を駆使して、製造プロセスの効率化、業務効率化、チームワーク強化、コスト削減、品質向上を実現します。このサービスは、製造業の課題を深く理解し、それに対する最適なデジタルソリューションを提供することで、企業が持続的な成長とイノベーションを達成できるようサポートします。
オンライン講座
製造業、主に購買・調達部門にお勤めの方々に向けた情報を配信しております。
新任の方やベテランの方、管理職を対象とした幅広いコンテンツをご用意しております。
お問い合わせ
コストダウンが利益に直結する術だと理解していても、なかなか前に進めることができない状況。そんな時は、newjiのコストダウン自動化機能で大きく利益貢献しよう!
(Β版非公開)