- お役立ち記事
- Technology selection and corresponding methods for cutting heat treatment surface treatment of automobile-related parts
月間77,185名の
製造業ご担当者様が閲覧しています*
*2025年2月28日現在のGoogle Analyticsのデータより
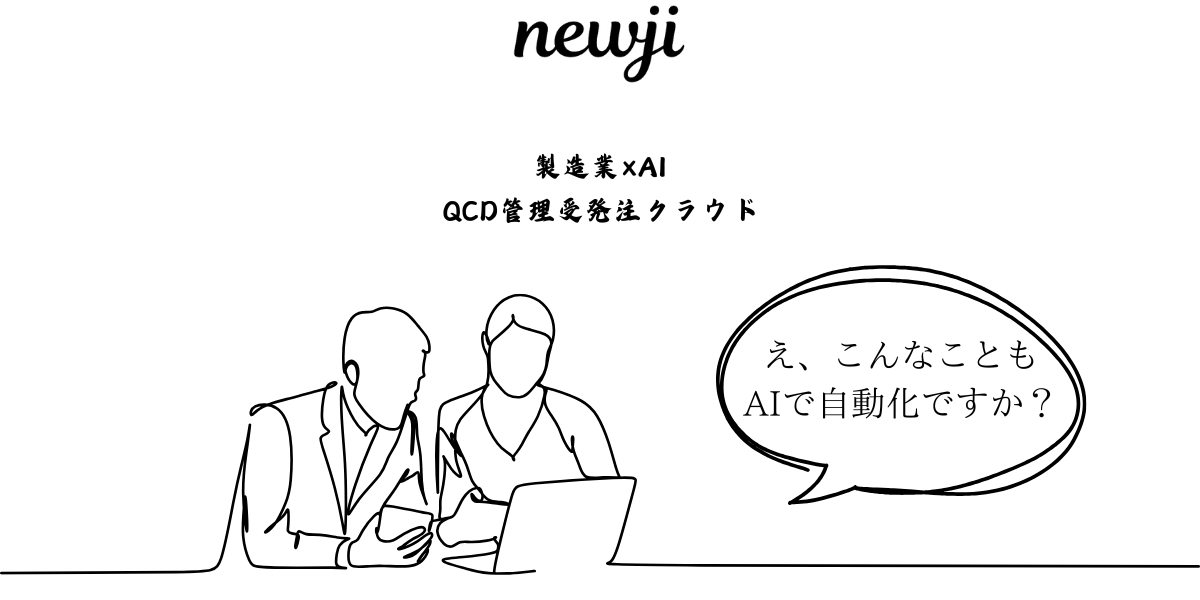
Technology selection and corresponding methods for cutting heat treatment surface treatment of automobile-related parts
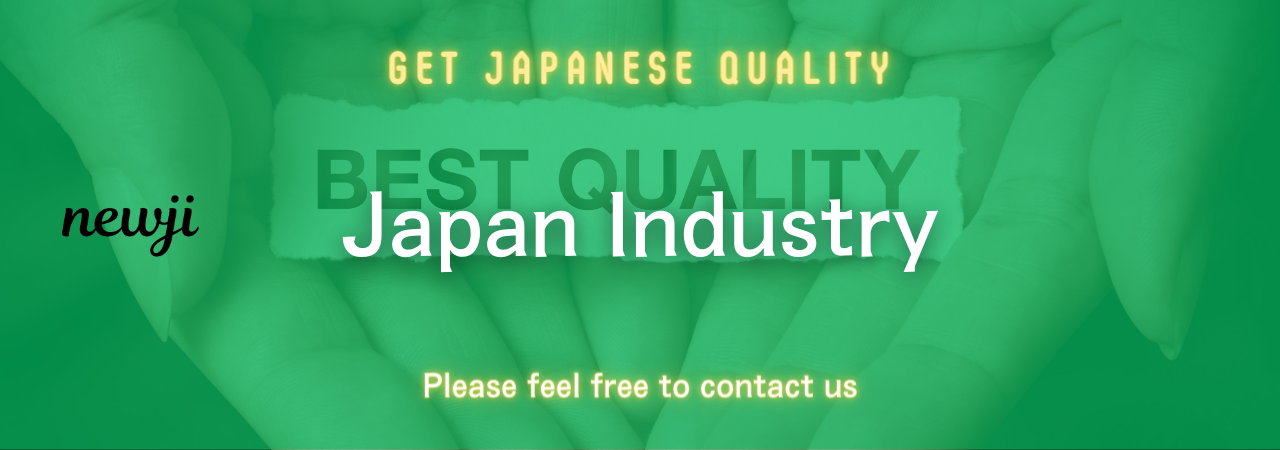
目次
Introduction
In the ever-evolving automotive industry, the production of high-quality parts is crucial for ensuring efficiency, safety, and performance in vehicles.
A significant part of this process involves the selection of appropriate technologies and methods for cutting, heat treatment, and surface treatment of these parts.
This article delves into the considerations for technology selection and offers insights into effective methods for cutting, heat treatment, and surface treatment of automobile-related components.
Importance of Technology Selection
Choosing the right technology for manufacturing automobile parts influences not only the quality but also the cost and time required for production.
Factors such as material properties, desired component characteristics, production volume, and cost constraints must be considered.
Optimally selected technologies can enhance durability, reduce wear and tear, and provide improved resistance to environmental factors.
Material Considerations
The choice of material is paramount when selecting the appropriate technology.
Materials like steel, aluminum, and composites each exhibit unique characteristics.
Steel offers durability but requires precise cutting and heat treatment to prevent distortion.
Aluminum, known for its lightweight properties, demands careful handling to avoid stress fractures during processing.
Composites, while versatile, may necessitate specialized cutting and surface treatment techniques to maximize performance.
Cost and Efficiency
Cost-effectiveness is essential in the automotive sector.
The right balance between initial investment and operational cost savings is crucial for technology selection.
Advanced technologies might involve high initial costs but can result in reduced waste, lower energy consumption, and faster production times, thereby enhancing overall efficiency.
The choice of technology should aim to achieve the lowest possible cost per unit while maintaining desired quality standards.
Cutting Methods for Automobile Parts
The cutting of automobile parts has evolved significantly, with several advanced methods available to meet precise specifications and achieve superior finishes.
Laser Cutting
Laser cutting is a popular choice in the automotive industry due to its precision and flexibility.
This method utilizes focused laser beams to cut materials into detailed shapes with minimal waste.
Laser cutting offers advantages such as reduced material deformation, high-speed processing, and the ability to handle various material types and thicknesses.
It’s particularly useful for creating intricate designs or cutting difficult geometries.
Waterjet Cutting
Waterjet cutting is another versatile technique, using high-pressure water streams mixed with abrasive materials to cut through components.
One of the distinct advantages of waterjet cutting is that it generates no heat, thus preserving the properties of heat-sensitive materials.
This method is ideal for materials that require intricate cuts without the risk of thermal damage.
Plasma Cutting
For thicker materials, plasma cutting offers a cost-effective solution.
Using an accelerated jet of hot plasma, this method efficiently cuts through conductive metals.
Plasma cutting is faster than laser or waterjet cutting for thick materials and is particularly effective for prototyping or low-precision components.
Heat Treatment Methods
Heat treatment enhances the mechanical properties of automobile parts, including hardness, toughness, and wear resistance.
Different methods are tailored to specific material needs.
Annealing
Annealing is a process where parts are heated and then slowly cooled to remove internal stresses.
This results in improved ductility and softer metals that are easier to work with subsequently.
It’s beneficial for enhancing machinability and reducing brittleness.
Quenching and Tempering
Quenching involves rapid cooling from a high temperature, usually employing water, oil, or air.
Post-quenching, components are typically quite hard but also brittle.
Tempering follows quenching, where parts are reheated to a lower temperature and then allowed to cool.
This process enhances toughness and reduces brittleness, making it ideal for components requiring strength and flexibility.
Case Hardening
Case hardening, or surface hardening, is used to increase the surface strength while maintaining a ductile core.
Methods like carburizing or nitriding introduce additional elements onto the surface, resulting in a hard outer layer.
This treatment is beneficial for parts that experience surface wear but need to retain internal toughness.
Surface Treatment Methods
Surface treatments are crucial for enhancing the longevity and performance of automobile parts by improving resistance to corrosion, wear, and fatigue.
Electroplating
In electroplating, a metal coating is applied using an electric current.
This process provides a protective surface that enhances corrosion resistance and aesthetic appeal.
Common coatings include chromium, nickel, and zinc, widely used for both functional and decorative purposes.
Powder Coating
Powder coating entails applying a dry powder, which is then cured under heat to form a protective coating.
This method provides a durable, corrosion-resistant finish in a variety of colors and textures.
It is environmentally friendly, generating less waste compared to traditional liquid coatings.
Anodizing
Specifically useful for aluminum parts, anodizing enhances corrosion resistance and wear resistance.
By creating a protective oxide layer, anodizing improves the component’s ability to withstand environmental challenges while also offering an attractive finish.
Conclusion
Selecting the appropriate technologies for cutting, heat treatment, and surface treatment is vital for manufacturing superior automobile parts.
By considering factors such as material properties, cost, and desired component characteristics, manufacturers can harness advanced techniques to enhance the performance and longevity of automotive components.
Staying abreast of technological advancements ensures that manufacturers can continually improve their processes and stay competitive in the dynamic automotive industry.
資料ダウンロード
QCD管理受発注クラウド「newji」は、受発注部門で必要なQCD管理全てを備えた、現場特化型兼クラウド型の今世紀最高の受発注管理システムとなります。
ユーザー登録
受発注業務の効率化だけでなく、システムを導入することで、コスト削減や製品・資材のステータス可視化のほか、属人化していた受発注情報の共有化による内部不正防止や統制にも役立ちます。
NEWJI DX
製造業に特化したデジタルトランスフォーメーション(DX)の実現を目指す請負開発型のコンサルティングサービスです。AI、iPaaS、および先端の技術を駆使して、製造プロセスの効率化、業務効率化、チームワーク強化、コスト削減、品質向上を実現します。このサービスは、製造業の課題を深く理解し、それに対する最適なデジタルソリューションを提供することで、企業が持続的な成長とイノベーションを達成できるようサポートします。
製造業ニュース解説
製造業、主に購買・調達部門にお勤めの方々に向けた情報を配信しております。
新任の方やベテランの方、管理職を対象とした幅広いコンテンツをご用意しております。
お問い合わせ
コストダウンが利益に直結する術だと理解していても、なかなか前に進めることができない状況。そんな時は、newjiのコストダウン自動化機能で大きく利益貢献しよう!
(β版非公開)