- お役立ち記事
- Technology to improve the wear resistance of milling machines and its application in the automobile parts market
月間77,185名の
製造業ご担当者様が閲覧しています*
*2025年2月28日現在のGoogle Analyticsのデータより
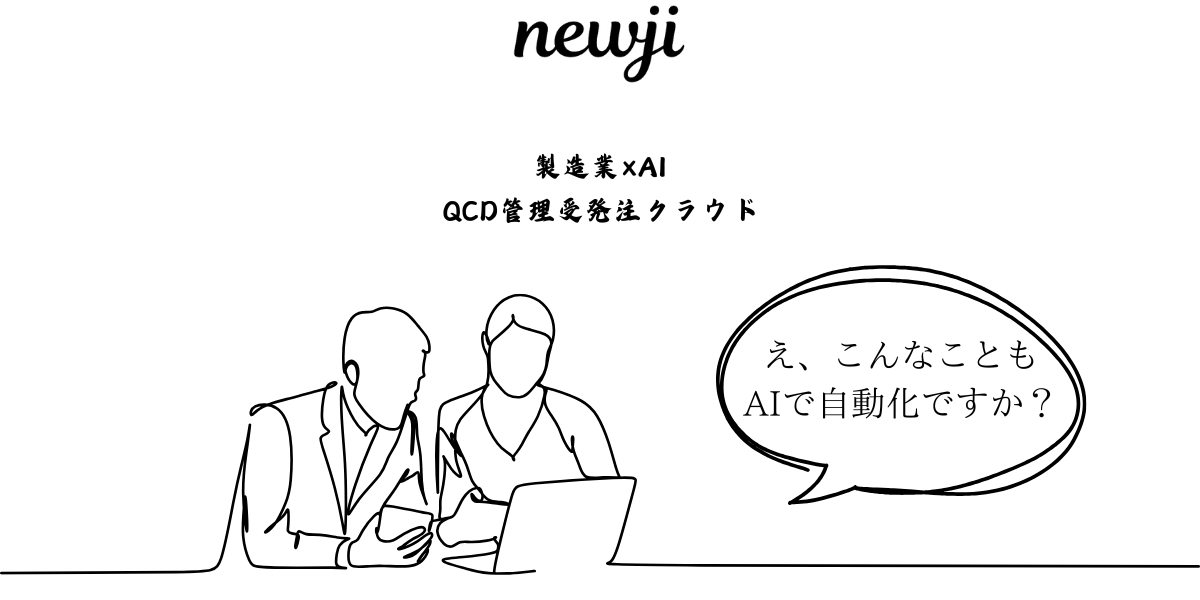
Technology to improve the wear resistance of milling machines and its application in the automobile parts market
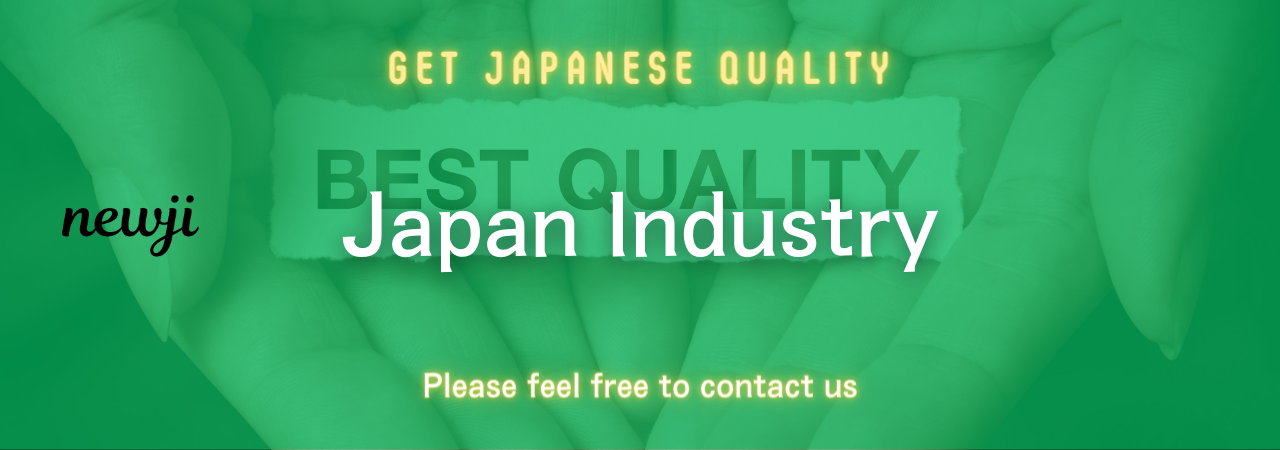
目次
Understanding Wear Resistance in Milling Machines
Milling machines are essential tools in various manufacturing processes, including the automotive industry.
They shape metals and other materials to create specific parts and components.
However, one of the significant challenges faced by these machines is wear and tear.
The process of milling involves high-speed rotation and substantial friction, leading to the gradual degradation of machine parts.
Wear resistance refers to the ability of a milling machine’s components to withstand erosion, abrasion, and other forms of deterioration.
Improving wear resistance is crucial for extending the machine’s lifespan and maintaining high performance levels.
The Importance of Wear-Resistant Technology
The primary significance of wear-resistant technology lies in its potential to reduce maintenance costs and downtime.
When milling machines experience less wear, they require fewer repairs and can operate for longer periods without interruption.
This efficiency is vital in industries such as automobile manufacturing, where production speed and precision are critical.
Enhanced wear resistance also improves the quality of the finished products, ensuring that parts are manufactured to exact specifications consistently.
Technological Advances in Wear Resistance
Recent technological advances have revolutionized wear resistance in milling machines.
One of the most notable developments is the use of high-performance coatings.
These coatings are applied to the surfaces of machine components to create a protective barrier that reduces friction and wear.
Materials such as titanium nitride (TiN), diamond-like carbon (DLC), and ceramic coatings are popular choices due to their high hardness and low friction properties.
Material Innovations and Their Impact
Material innovation also plays a crucial role in enhancing wear resistance.
Manufacturers are increasingly using advanced alloys and composites that offer superior hardness and durability.
These materials are specially engineered to withstand the stresses of high-speed milling.
For instance, carbide materials are popular for their exceptional toughness and ability to maintain a sharp cutting edge, even under extreme conditions.
Improved Lubrication Methods
Lubrication is another critical factor in reducing wear.
Innovative lubrication methods, such as minimum quantity lubrication (MQL), have been developed to optimize the amount of lubricant used.
MQL involves applying a small amount of high-performance lubricant directly to the tool’s cutting edge, minimizing friction and heat generation.
This method not only improves wear resistance but also enhances the environmental compatibility of milling processes by reducing the amount of waste oil.
Application in the Automobile Parts Market
The automotive industry demands high-quality, precision-engineered parts, making wear resistance technology indispensable.
In this sector, components such as engine blocks, transmission parts, and brake components must be manufactured with utmost accuracy and durability.
Milling machines equipped with wear-resistant technology are integral to achieving these standards.
Benefits for Automobile Manufacturers
For automobile manufacturers, the application of wear-resistant technology in milling machines offers numerous benefits.
First and foremost, it significantly boosts productivity.
Machines with enhanced wear resistance can operate at higher speeds and for longer periods, resulting in faster production cycles.
This increased efficiency allows manufacturers to meet tight production deadlines and customer demands more effectively.
Cost-Effectiveness and Quality Assurance
Another major advantage is cost-effectiveness.
While the initial investment in wear-resistant technology may be higher, the reduced need for maintenance and repairs translates to lower overall operational costs.
Additionally, the consistent quality of the milled parts reduces the likelihood of defects, minimizing waste and rework.
Staying Competitive in a Dynamic Market
As the automotive market continues to evolve, manufacturers must stay competitive by embracing the latest technological advancements.
Wear-resistant technology enables them to remain at the forefront of innovation, producing high-quality, reliable parts that meet or exceed industry standards.
Future Prospects of Wear Resistance in Milling Technology
The future of wear resistance in milling machines looks promising, with continuous research and development leading to even more advanced solutions.
Nanotechnology, for example, holds great potential in creating ultra-hard coatings and materials that offer unparalleled wear resistance.
The integration of smart sensors and IoT (Internet of Things) technology can also enhance predictive maintenance, allowing for real-time monitoring and early detection of wear issues.
Environmental Considerations
As environmental concerns take center stage, the industry is also exploring eco-friendly alternatives to traditional wear-resistant coatings and lubricants.
Biodegradable materials and sustainable manufacturing practices are being developed to reduce the carbon footprint of milling processes.
Collaborative Efforts in Innovation
Collaboration between manufacturers, research institutions, and technology developers will be key to driving innovation in wear resistance.
By working together, these stakeholders can pool their expertise and resources to create cutting-edge solutions that benefit the entire industry.
In conclusion, improving the wear resistance of milling machines is paramount for their efficiency and longevity, especially in the automobile parts market.
Through technological advancements, material innovations, and improved lubrication methods, the industry continues to make strides in this area.
As we look to the future, the focus will remain on sustainable, cost-effective, and high-performance wear-resistant technologies that meet the evolving demands of the market.
資料ダウンロード
QCD管理受発注クラウド「newji」は、受発注部門で必要なQCD管理全てを備えた、現場特化型兼クラウド型の今世紀最高の受発注管理システムとなります。
ユーザー登録
受発注業務の効率化だけでなく、システムを導入することで、コスト削減や製品・資材のステータス可視化のほか、属人化していた受発注情報の共有化による内部不正防止や統制にも役立ちます。
NEWJI DX
製造業に特化したデジタルトランスフォーメーション(DX)の実現を目指す請負開発型のコンサルティングサービスです。AI、iPaaS、および先端の技術を駆使して、製造プロセスの効率化、業務効率化、チームワーク強化、コスト削減、品質向上を実現します。このサービスは、製造業の課題を深く理解し、それに対する最適なデジタルソリューションを提供することで、企業が持続的な成長とイノベーションを達成できるようサポートします。
製造業ニュース解説
製造業、主に購買・調達部門にお勤めの方々に向けた情報を配信しております。
新任の方やベテランの方、管理職を対象とした幅広いコンテンツをご用意しております。
お問い合わせ
コストダウンが利益に直結する術だと理解していても、なかなか前に進めることができない状況。そんな時は、newjiのコストダウン自動化機能で大きく利益貢献しよう!
(β版非公開)