- お役立ち記事
- Technology to improve the wear resistance of nickel alloys and their use in the mining industry
月間77,185名の
製造業ご担当者様が閲覧しています*
*2025年2月28日現在のGoogle Analyticsのデータより
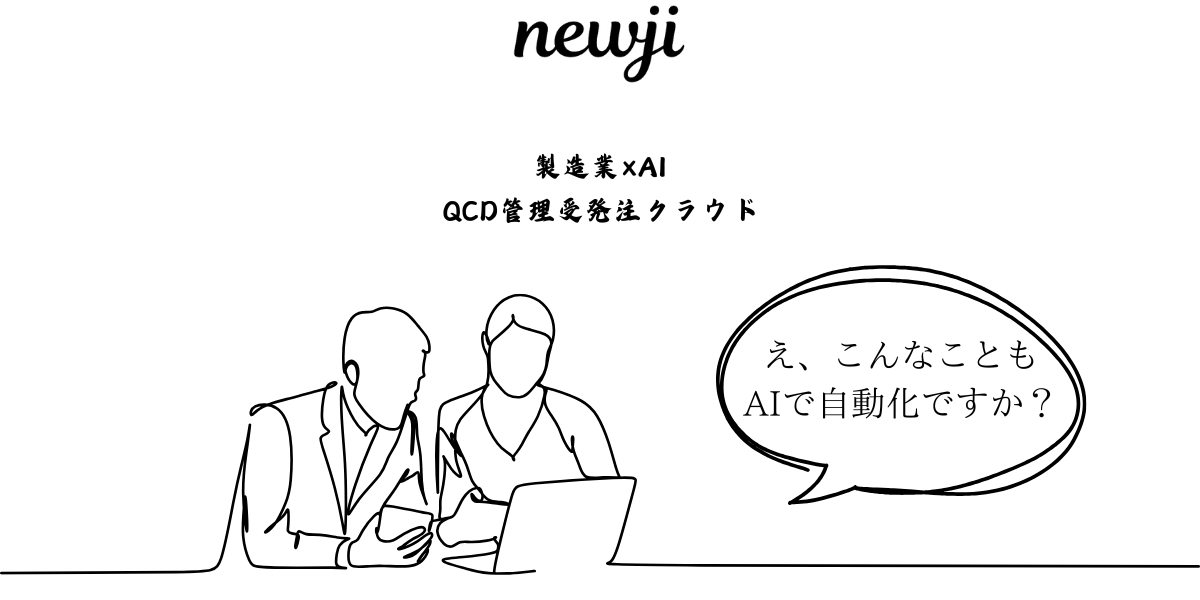
Technology to improve the wear resistance of nickel alloys and their use in the mining industry
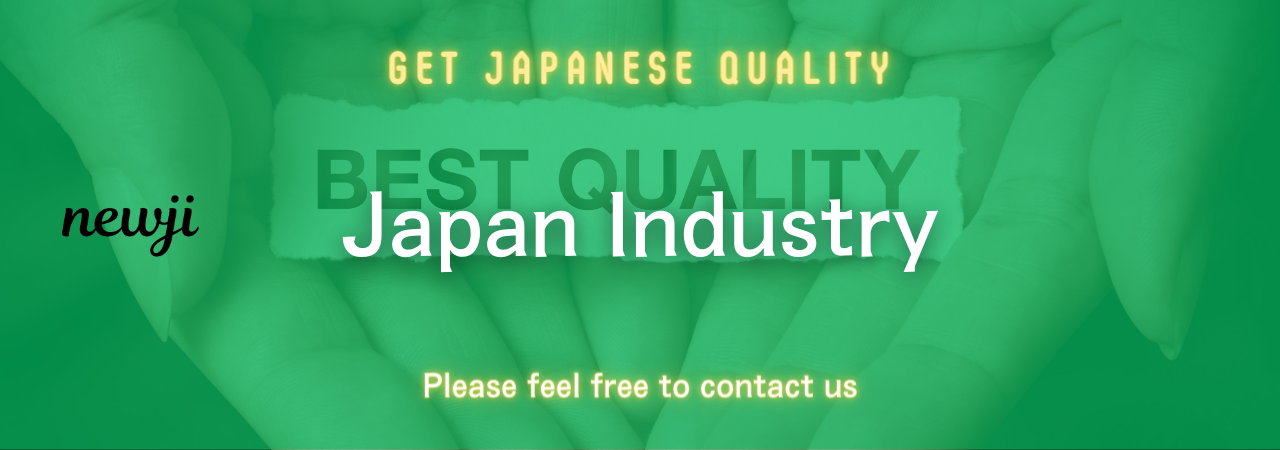
Nickel alloys are widely used in various industries due to their exceptional properties, such as high strength, corrosion resistance, and superior wear resistance.
These characteristics make nickel alloys a preferred choice for applications in demanding environments, especially in the mining industry where equipment must endure harsh conditions.
In recent years, advancements in technology have further enhanced the wear resistance of nickel alloys, thus extending their utility and lifespan in mining operations.
目次
Understanding Nickel Alloys
Nickel alloys are metallic compounds primarily composed of nickel and other elements such as chromium, molybdenum, and iron.
The composition of these elements varies, altering the alloy’s properties to suit different industrial applications.
In mining, these alloys are frequently used in the construction of equipment parts that require durability and robustness, such as valves, pumps, and excavation tools.
Their ability to withstand high temperatures and resist corrosion under stress makes them invaluable in mining locations with extreme environmental conditions.
Importance of Wear Resistance in Nickel Alloys
Wear resistance is the ability of a material to resist damage caused by friction and mechanical actions such as abrasion or erosion.
In the mining industry, equipment is constantly subjected to forces that cause wear and tear, which can lead to frequent maintenance or replacement.
This not only incurs higher costs but also leads to downtime that affects productivity.
Enhanced wear resistance in nickel alloys means longer-lasting equipment, reduced maintenance needs, and improved operational efficiency.
This is why continuous research and development efforts are directed towards improving this property in nickel alloys.
Technological Advances in Enhancing Wear Resistance
Several technological advancements have shaped the way nickel alloys are utilized in high-wear environments.
One significant development is the introduction of advanced coating technologies.
Coatings such as thermal spray and physical vapor deposition (PVD) apply a layer of protective material to the surface of the alloy, enhancing its resistance to wear.
Thermal Spray Coatings
Thermal spray coatings involve heating a material and spraying it onto the surface of the alloy, creating a protective layer that resists wear.
This technology allows for the application of various materials, each providing specific enhancements, such as increased hardness or resistance to erosion.
Thermal spraying is particularly effective for extending the life of mining equipment that operates under abrasive conditions.
Physical Vapor Deposition (PVD)
PVD coating is a vacuum deposition process that produces a thin, hard layer on the alloy’s surface.
The process involves vaporizing a solid material in a vacuum and depositing it on the alloy to form a protective film.
This film significantly improves wear resistance without altering the mechanical properties of the alloy.
PVD coatings are widely used in mining for equipment parts subject to high friction and corrosion.
Alloy Composition and Heat Treatment
In addition to coatings, altering the composition of the alloy itself can enhance its wear resistance.
Alloys with higher chromium and molybdenum content, for instance, are more resistant to wear and corrosion.
Moreover, heat treatment processes such as annealing and precipitation hardening can improve the overall durability of nickel alloys.
Applications in the Mining Industry
The mining industry relies heavily on nickel alloys for their exceptional wear resistance and versatility.
Common applications include the use of nickel alloys in earth-moving equipment, where they form the hard-wearing surfaces of loaders, trucks, and excavators.
Nickel-based superalloys are also employed in the construction of slurry pumps and pipes used in transporting mined materials.
Their resistance to wear and corrosion ensures minimal degradation when handling abrasive slurries and chemicals.
Additionally, nickel alloys are used to manufacture drill bits and cutters that require extreme hardness and resilience to penetrate rock and earth effectively.
Benefits of Using Advanced Nickel Alloys in Mining
The use of technologically advanced nickel alloys in mining has numerous benefits.
Primarily, the enhanced wear resistance leads to longer equipment life, reducing replacement and maintenance costs.
This, in turn, results in less downtime and increased productivity.
Furthermore, nickel alloys’ ability to withstand critical conditions such as high temperatures and corrosive environments ensures operational reliability.
Their inherent strength and stability are critical in an industry where equipment failure can have significant financial and safety implications.
Future Trends and Innovations
Ongoing research in material science is poised to bring further innovations in nickel alloy technology.
Future trends may include the use of nanotechnology for creating coatings with superior wear resistance through ultra-fine materials.
Developments in additive manufacturing, or 3D printing, also promise to revolutionize the production of customized nickel alloy components, improving efficiency and reducing waste.
Researchers are also exploring self-healing materials that can repair minor wear damage autonomously, further extending the lifecycle of mining equipment.
Conclusion
Nickel alloys continue to play a crucial role in the mining industry due to their remarkable wear resistance and the ongoing technological improvements that enhance these properties.
With advancements in coatings and material compositions, these alloys have become indispensable in creating durable and efficient mining equipment.
As the industry evolves, the role of innovative material technologies will be paramount in meeting the demands of more challenging mining environments and ensuring sustainable operations.
資料ダウンロード
QCD管理受発注クラウド「newji」は、受発注部門で必要なQCD管理全てを備えた、現場特化型兼クラウド型の今世紀最高の受発注管理システムとなります。
ユーザー登録
受発注業務の効率化だけでなく、システムを導入することで、コスト削減や製品・資材のステータス可視化のほか、属人化していた受発注情報の共有化による内部不正防止や統制にも役立ちます。
NEWJI DX
製造業に特化したデジタルトランスフォーメーション(DX)の実現を目指す請負開発型のコンサルティングサービスです。AI、iPaaS、および先端の技術を駆使して、製造プロセスの効率化、業務効率化、チームワーク強化、コスト削減、品質向上を実現します。このサービスは、製造業の課題を深く理解し、それに対する最適なデジタルソリューションを提供することで、企業が持続的な成長とイノベーションを達成できるようサポートします。
製造業ニュース解説
製造業、主に購買・調達部門にお勤めの方々に向けた情報を配信しております。
新任の方やベテランの方、管理職を対象とした幅広いコンテンツをご用意しております。
お問い合わせ
コストダウンが利益に直結する術だと理解していても、なかなか前に進めることができない状況。そんな時は、newjiのコストダウン自動化機能で大きく利益貢献しよう!
(β版非公開)