- お役立ち記事
- Technology to reduce damage, vibration, and noise through gear basics and high-rigidity design
月間76,176名の
製造業ご担当者様が閲覧しています*
*2025年3月31日現在のGoogle Analyticsのデータより
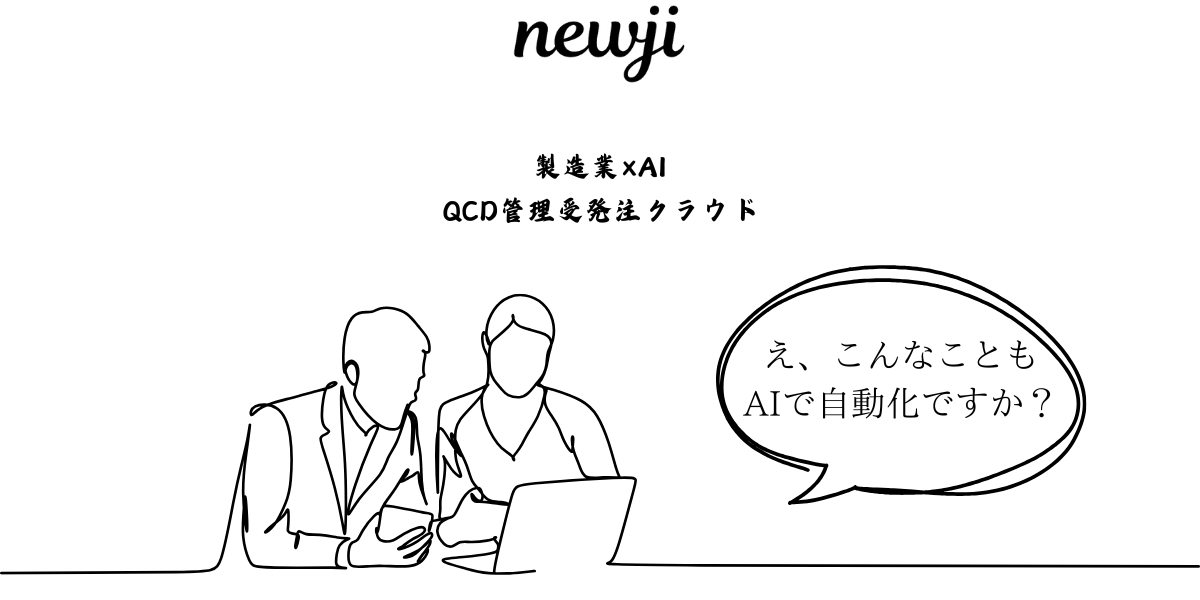
Technology to reduce damage, vibration, and noise through gear basics and high-rigidity design
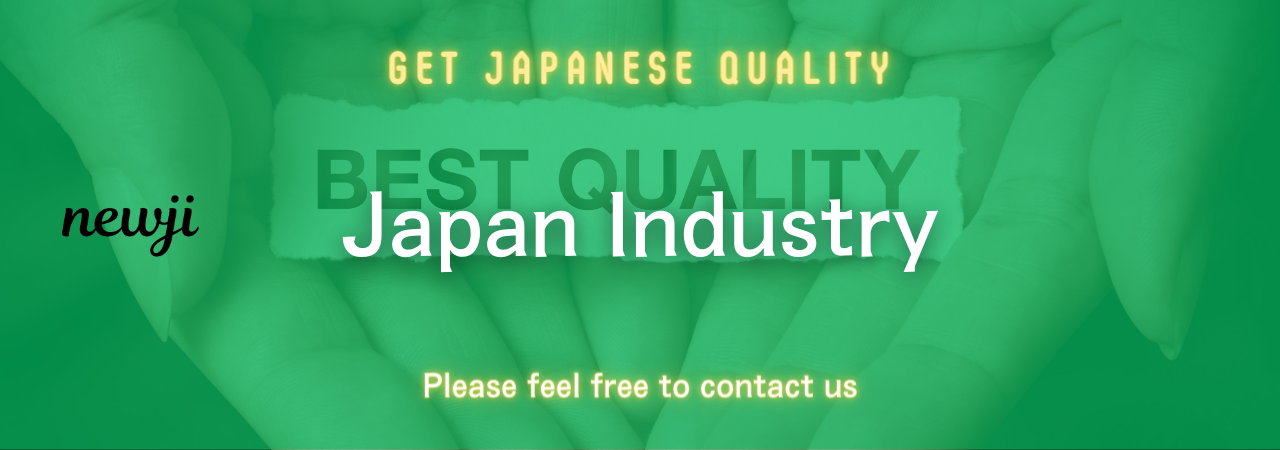
目次
Understanding the Basics of Gears
Gears are fundamental mechanical components that play a critical role in machinery and equipment across various industries.
At their core, gears are wheels with teeth that mesh together to transmit power, motion, and torque between different machine parts.
In a typical setup, when one gear (the driving gear) rotates, it causes the other gear (the driven gear) to rotate as well.
This transfer of motion and force is pivotal in many applications, from simple toys to complex industrial machinery.
Types of Gears
There are several types of gears, each designed for specific purposes and functionalities.
Common types include spur gears, helical gears, bevel gears, worm gears, and rack and pinion gears.
Spur gears are the simplest form and are used mainly for parallel shaft operations.
Helical gears, with angled teeth, are favored for applications requiring high speed and increased torque.
Bevel gears are used to change the axis of rotation, while worm gears provide high torque and reduced speed.
Each type of gear serves unique purposes and offers distinct advantages for reducing noise and vibration in mechanical systems.
High-Rigidity in Gear Design
High-rigidity design in gears is crucial for ensuring long-term performance, durability, and efficiency of mechanical systems.
Rigidity pertains to the gear’s ability to withstand forces without deforming or experiencing excessive wear.
A high-rigidity design minimizes unwanted movement and maintains alignment between meshing gears, significantly reducing vibration and the accompanying noise.
Materials for High-Rigidity
Selecting the right materials is vital for achieving high-rigidity in gear design.
Common materials include steel, cast iron, and various composites.
Steel is favored for its high strength and durability, making it suitable for high-load applications.
Cast iron is another popular choice due to its good wear resistance and vibration damping properties.
Composite materials, though lighter, offer excellent strength-to-weight ratios and are increasingly used in applications where weight reduction is critical.
Technology to Mitigate Vibration and Noise
Reducing vibration and noise in gear systems is essential for improving efficiency and extending the lifespan of mechanical equipment.
Several technological advancements have been made to address these issues.
Precision Manufacturing
Precision manufacturing is one of the key methodologies for reducing vibration and noise in gear systems.
Advanced machining techniques and equipment ensure accurate gear teeth profiles and high-quality finishes.
This precision allows for smoother meshing, reducing friction and the noise generated during operation.
Consistent quality control processes help maintain this precision across large-scale manufacturing.
Use of Advanced Lubricants
Lubrication plays a crucial role in minimizing friction between gears, thereby reducing noise and vibration.
Advanced lubricants are specifically formulated to provide lasting protection under extreme pressures and temperatures.
They create a thin film that reduces direct metal-to-metal contact, promoting smoother operations and extending gear life.
Innovative Gear Tooth Design
Innovative gear tooth designs, such as asymmetric tooth profiles and specialized surface treatments, have been developed to reduce noise and improve performance.
Asymmetric tooth profiles optimize the contact ratio during gear meshing, resulting in smoother transitions and less impact noise.
Surface treatments, such as case hardening and nitriding, enhance the surface properties of gears, increasing their resilience to wear and fatigue.
The Role of Maintenance in Gear Performance
Regular maintenance is integral to sustaining the performance of gear systems.
Consistent inspections and servicing ensure that gears remain in optimal condition, further reducing the risk of noise and vibration-related issues.
Regular Inspection and Servicing
Scheduled inspections help identify early signs of wear, misalignment, or imbalance in gear systems.
Timely servicing, including lubrication replacement and realignment, prevents minor issues from developing into major problems.
By maintaining the integrity of gear systems, vibration and noise are kept to a minimum, prolonging the equipment’s operational life.
Importance of Training
Educating personnel involved in gear maintenance and operation is crucial for optimizing gear performance.
Training ensures awareness of proper handling practices, enhances troubleshooting skills, and instills preventive maintenance measures.
Skilled technicians can significantly contribute to reducing mechanical noise and vibration in gear systems through their expertise and attention to detail.
Advancements and Future Directions
Technology continues to advance, bringing novel solutions to the challenges of reducing gear system noise and vibration.
Future research is focused on enhancing materials, designs, and manufacturing processes to further minimize these issues.
Continued innovation in gear technology promises not only efficiency improvements but also increases in the operational lifespan of mechanical equipment.
Gear systems are a critical component in countless applications, and their optimization is essential for the performance and reliability of machinery.
Through a combination of high-rigidity design, advanced manufacturing techniques, and diligent maintenance practices, gear systems can achieve greater efficiency and durability.
As technology progresses, the methods for reducing vibration and noise will continue to evolve, resulting in quieter, more efficient mechanical systems.
資料ダウンロード
QCD管理受発注クラウド「newji」は、受発注部門で必要なQCD管理全てを備えた、現場特化型兼クラウド型の今世紀最高の受発注管理システムとなります。
ユーザー登録
受発注業務の効率化だけでなく、システムを導入することで、コスト削減や製品・資材のステータス可視化のほか、属人化していた受発注情報の共有化による内部不正防止や統制にも役立ちます。
NEWJI DX
製造業に特化したデジタルトランスフォーメーション(DX)の実現を目指す請負開発型のコンサルティングサービスです。AI、iPaaS、および先端の技術を駆使して、製造プロセスの効率化、業務効率化、チームワーク強化、コスト削減、品質向上を実現します。このサービスは、製造業の課題を深く理解し、それに対する最適なデジタルソリューションを提供することで、企業が持続的な成長とイノベーションを達成できるようサポートします。
製造業ニュース解説
製造業、主に購買・調達部門にお勤めの方々に向けた情報を配信しております。
新任の方やベテランの方、管理職を対象とした幅広いコンテンツをご用意しております。
お問い合わせ
コストダウンが利益に直結する術だと理解していても、なかなか前に進めることができない状況。そんな時は、newjiのコストダウン自動化機能で大きく利益貢献しよう!
(β版非公開)