- お役立ち記事
- Temperature Compensation System Design for Precision Measuring Instruments
月間76,176名の
製造業ご担当者様が閲覧しています*
*2025年3月31日現在のGoogle Analyticsのデータより
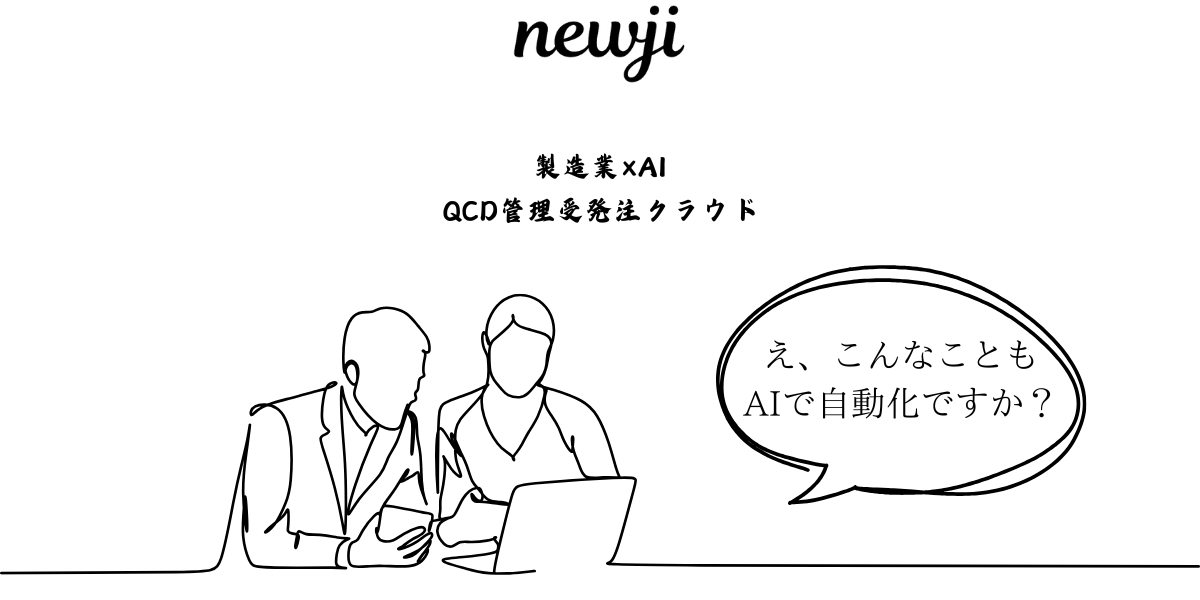
Temperature Compensation System Design for Precision Measuring Instruments
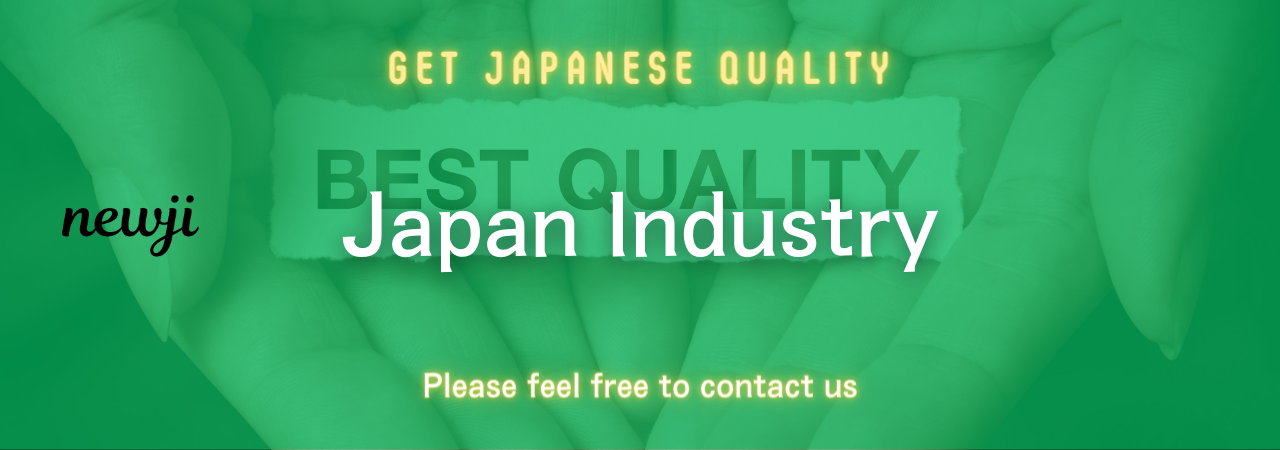
When we talk about precision measuring instruments, accuracy is key.
The slightest variation in environmental conditions can affect measurements significantly.
Temperature is one of the most influential factors that can distort readings, making a temperature compensation system essential.
In this article, we will discuss the design and implementation of temperature compensation systems specifically for precision measuring instruments.
目次
Understanding Temperature Compensation
Temperature compensation is a technique used to adjust the readings of a measuring instrument to account for changes in temperature.
These changes can cause materials to expand or contract, which in turn can affect the instrument’s accuracy.
A temperature compensation system aims to mitigate these effects, ensuring that measurements remain consistent regardless of temperature fluctuations.
Why is Temperature Compensation Important?
Measuring instruments are often made of materials that expand or contract with temperature changes.
For example, metal components can expand when heated and contract when cooled.
This may not matter in everyday situations, but in precision measurements, even a micron-level change can be significant.
Without temperature compensation, readings can become inaccurate, leading to errors in data collection and analysis.
Thus, temperature compensation is crucial for maintaining the integrity of measurements.
Key Components in Temperature Compensation System Design
To design an effective temperature compensation system, several components must be considered.
Temperature Sensors
The first and most critical component is the temperature sensor.
These sensors detect the temperature of the environment and send this information to the control system.
Common types of sensors used include thermocouples, thermistors, and resistance temperature detectors (RTDs).
Selecting the right sensor depends on several factors, such as the temperature range, accuracy requirements, and the specific application of the measuring instrument.
Data Acquisition System
Once the temperature sensors gather the data, it needs to be transmitted to a data acquisition system.
This system collects the temperature data and processes it for further analysis.
The data acquisition system should be capable of rapid data collection and should efficiently handle the amount of data generated by the sensors.
Microcontroller/Processor
The data from the acquisition system is then processed by a microcontroller or a processor.
The processor uses algorithms to analyze the temperature data.
Based on this analysis, the system makes real-time adjustments to the readings of the measuring instrument to compensate for temperature effects.
The choice of processor depends on the complexity of the required computations and the speed at which adjustments need to be made.
Compensation Algorithms
The algorithms play a crucial role in the temperature compensation system.
These algorithms take the raw temperature data from the sensors and apply mathematical models to adjust the measurements.
The complexity of these algorithms can vary.
Simple algorithms might involve linear adjustments, while more advanced ones might use polynomial or logarithmic models.
Actuators or Adjustment Mechanisms
In some systems, physical adjustments may be required to compensate for temperature variations.
Actuators or other mechanical adjustment mechanisms can be integrated into the system to make these real-time adjustments.
For example, in a measuring instrument that relies on optical components, actuators might adjust the alignment of lenses to counteract thermal expansion.
Steps to Design a Temperature Compensation System
Designing a temperature compensation system involves several well-defined steps.
Identify the Measurement Variables
First, identify the specific variables that will be affected by temperature changes.
These could be dimensions, electrical properties, or optical properties, depending on the type of measuring instrument.
Select Appropriate Temperature Sensors
Choose temperature sensors that suit your application’s specific needs.
Ensure they have the required range, accuracy, and response time.
Calibrate the sensors for optimal performance.
Design the Data Acquisition System
Create a robust data acquisition system capable of collecting temperature data at the necessary resolution and speed.
Ensure that the system can interface seamlessly with the chosen sensors and the microcontroller or processor.
Develop and Implement Algorithms
Write and test algorithms that can accurately predict and adjust for temperature-induced measurement errors.
Validate these algorithms against known standards or through empirical testing.
Integrate Adjustment Mechanisms
If physical adjustments are necessary, design and integrate actuators that can make these changes in real-time.
Ensure these mechanisms do not introduce additional errors or interfere with the instrument’s primary measurements.
Testing and Validation
Once the system is designed, thorough testing is essential to ensure its effectiveness.
Simulate various environmental conditions to see how well the system compensates for temperature changes.
Use calibration standards to verify accuracy.
Conduct long-term testing to assess the system’s reliability over prolonged periods.
Challenges in Temperature Compensation
Designing an effective temperature compensation system is not without challenges.
Selecting suitable sensors and ensuring their calibration can be complicated.
Designing algorithms that are both accurate and efficient requires expertise in both mathematics and practical engineering.
Furthermore, integrating mechanical or electrical adjustment mechanisms adds another layer of complexity.
Despite these challenges, the benefits of a well-designed temperature compensation system far outweigh the difficulties.
Conclusion
Temperature compensation systems are crucial for ensuring the accuracy of precision measuring instruments.
By carefully designing and integrating key components like temperature sensors, data acquisition systems, processors, algorithms, and adjustment mechanisms, it is possible to maintain the integrity of measurements even in fluctuating temperatures.
While the design process can be challenging, the end result is a system that provides reliable, accurate data, essential for scientific research, manufacturing, and various other fields.
資料ダウンロード
QCD管理受発注クラウド「newji」は、受発注部門で必要なQCD管理全てを備えた、現場特化型兼クラウド型の今世紀最高の受発注管理システムとなります。
ユーザー登録
受発注業務の効率化だけでなく、システムを導入することで、コスト削減や製品・資材のステータス可視化のほか、属人化していた受発注情報の共有化による内部不正防止や統制にも役立ちます。
NEWJI DX
製造業に特化したデジタルトランスフォーメーション(DX)の実現を目指す請負開発型のコンサルティングサービスです。AI、iPaaS、および先端の技術を駆使して、製造プロセスの効率化、業務効率化、チームワーク強化、コスト削減、品質向上を実現します。このサービスは、製造業の課題を深く理解し、それに対する最適なデジタルソリューションを提供することで、企業が持続的な成長とイノベーションを達成できるようサポートします。
製造業ニュース解説
製造業、主に購買・調達部門にお勤めの方々に向けた情報を配信しております。
新任の方やベテランの方、管理職を対象とした幅広いコンテンツをご用意しております。
お問い合わせ
コストダウンが利益に直結する術だと理解していても、なかなか前に進めることができない状況。そんな時は、newjiのコストダウン自動化機能で大きく利益貢献しよう!
(β版非公開)