- お役立ち記事
- The balance between transportation costs and quality control in procurement faced by global purchasing departments
The balance between transportation costs and quality control in procurement faced by global purchasing departments
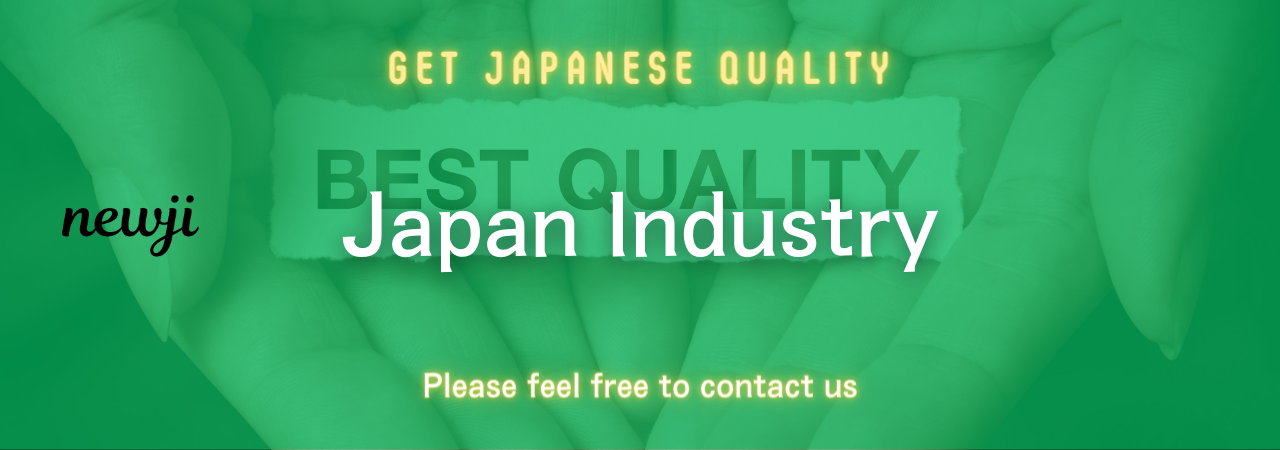
目次
Understanding the Balance in Global Procurement
In the interconnected world of global commerce, procurement teams face unique challenges when sourcing materials and products from across the globe.
One key dilemma is balancing transportation costs with quality control.
This intricate balancing act often determines the efficiency and success of a global purchasing department.
Transportation Costs: The Inevitable Factor
Transportation costs are an inevitable part of the procurement process.
As products are sourced from various parts of the world, logistics play a crucial role in determining the final cost of goods.
This involves several components such as shipping fees, import duties, taxes, and even warehousing charges.
Each of these factors can vary significantly depending on the transportation method chosen.
Air freight, for instance, is the fastest but also the most expensive method.
Meanwhile, sea freight offers a cost-effective alternative but is slower and may not be suitable for all types of goods.
Choosing the right transportation strategy is not simply a matter of costs.
It also involves analyzing the timelines, potential risks, and reliability of each transportation mode.
An efficient strategy can lead to reduced transportation costs, thereby potentially lowering the final cost of products for consumers.
Quality Control: A Non-Negotiable Aspect
While keeping transportation costs in check is critical, maintaining strict quality control standards is paramount.
Consumers and businesses alike expect high-quality products that meet certain standards, regardless of their origin.
Ensuring quality control can be complex when dealing with suppliers from different regions, each with their own standards and regulations.
It may involve on-site inspections, rigorous testing, and close collaboration with suppliers to ensure compliance with quality standards.
Compromises on quality can lead to catastrophic results, including product recalls, brand damage, and loss of customer trust.
Therefore, even in the face of pressure to reduce costs, purchasing departments must prioritize quality to maintain brand integrity and customer satisfaction.
The Role of Technology in Balancing Costs and Quality
Technology plays an instrumental role in helping purchasing departments manage the balance between transportation costs and quality control.
Advanced procurement software can analyze data, forecast demand, and suggest the most cost-effective logistics solutions.
Supply chain management systems can also track shipments, manage supplier relationships, and ensure quality standards are met.
These systems enhance visibility across the supply chain, allowing for quick responses to potential disruptions or quality issues.
Additionally, technologies like blockchain can provide transparency and traceability in supply chains, further ensuring that quality control measures are upheld throughout the procurement process.
Strategic Negotiations and Supplier Relationships
Another vital aspect of managing transportation costs and quality control is developing strategic relationships with suppliers.
Strong partnerships can lead to better negotiation outcomes concerning transportation costs and quality standards.
Long-term relationships enable purchasing departments to work closely with suppliers to develop more cost-effective logistics methods.
Collaborating with reliable suppliers who understand the importance of quality can lead to joint innovations in product development and streamlined processes, benefiting both parties.
Purchasing departments should also consider diversifying their supplier base to mitigate risks.
Relying heavily on a single supplier can expose a business to significant risks if problems arise, including quality issues or shipping delays.
Having multiple suppliers ensures that if one fails to deliver, others can fill the gap, thereby maintaining quality and minimizing additional transportation costs.
Case Studies of Successful Procurement Practices
Examining successful case studies can provide valuable insights into best practices for balancing transportation costs and quality control.
Take, for example, a well-known global electronics company that leveraged technology to optimize its supply chain.
By investing in predictive analytics, they were able to forecast demand more accurately and adjust logistics plans accordingly, reducing unnecessary transportation costs.
Additionally, they implemented strict quality control measures that involved continuous supplier audits and quality checks at every stage of production.
This approach not only controlled costs but also maintained their reputation for high-quality products.
Another example is an international fashion brand that established strategic partnerships with regional logistics companies.
By building relationships at a local level, they significantly reduced transportation times and costs while maintaining stringent quality criteria through close monitoring and frequent inspections.
Future Trends in Global Procurement
As global procurement continues to evolve, new trends are poised to influence how purchasing departments manage transportation costs and quality control.
Sustainability is becoming a key driver, with companies seeking to minimize their environmental footprint while also effectively managing costs.
Green logistics practices, such as optimizing packaging and choosing environmentally friendly transportation modes, are gaining traction.
Additionally, digitalization and automation are set to further streamline procurement processes, making balancing costs and quality more efficient.
Understanding and anticipating these trends will be critical for procurement professionals aiming to excel in their roles.
Conclusion: Achieving the Delicate Balance
Balancing transportation costs and quality control in global procurement is indeed a delicate task, requiring careful consideration and strategic planning.
By leveraging technology, fostering strong supplier relationships, and staying informed of industry trends, purchasing departments can successfully navigate these challenges.
Ultimately, achieving this balance ensures that companies can deliver high-quality products to market efficiently and cost-effectively, securing their competitive position in the global marketplace.
資料ダウンロード
QCD調達購買管理クラウド「newji」は、調達購買部門で必要なQCD管理全てを備えた、現場特化型兼クラウド型の今世紀最高の購買管理システムとなります。
ユーザー登録
調達購買業務の効率化だけでなく、システムを導入することで、コスト削減や製品・資材のステータス可視化のほか、属人化していた購買情報の共有化による内部不正防止や統制にも役立ちます。
NEWJI DX
製造業に特化したデジタルトランスフォーメーション(DX)の実現を目指す請負開発型のコンサルティングサービスです。AI、iPaaS、および先端の技術を駆使して、製造プロセスの効率化、業務効率化、チームワーク強化、コスト削減、品質向上を実現します。このサービスは、製造業の課題を深く理解し、それに対する最適なデジタルソリューションを提供することで、企業が持続的な成長とイノベーションを達成できるようサポートします。
オンライン講座
製造業、主に購買・調達部門にお勤めの方々に向けた情報を配信しております。
新任の方やベテランの方、管理職を対象とした幅広いコンテンツをご用意しております。
お問い合わせ
コストダウンが利益に直結する術だと理解していても、なかなか前に進めることができない状況。そんな時は、newjiのコストダウン自動化機能で大きく利益貢献しよう!
(Β版非公開)