- お役立ち記事
- The basics of quality function deployment (QFD), how to utilize it for quality control, and its key points
月間76,176名の
製造業ご担当者様が閲覧しています*
*2025年3月31日現在のGoogle Analyticsのデータより
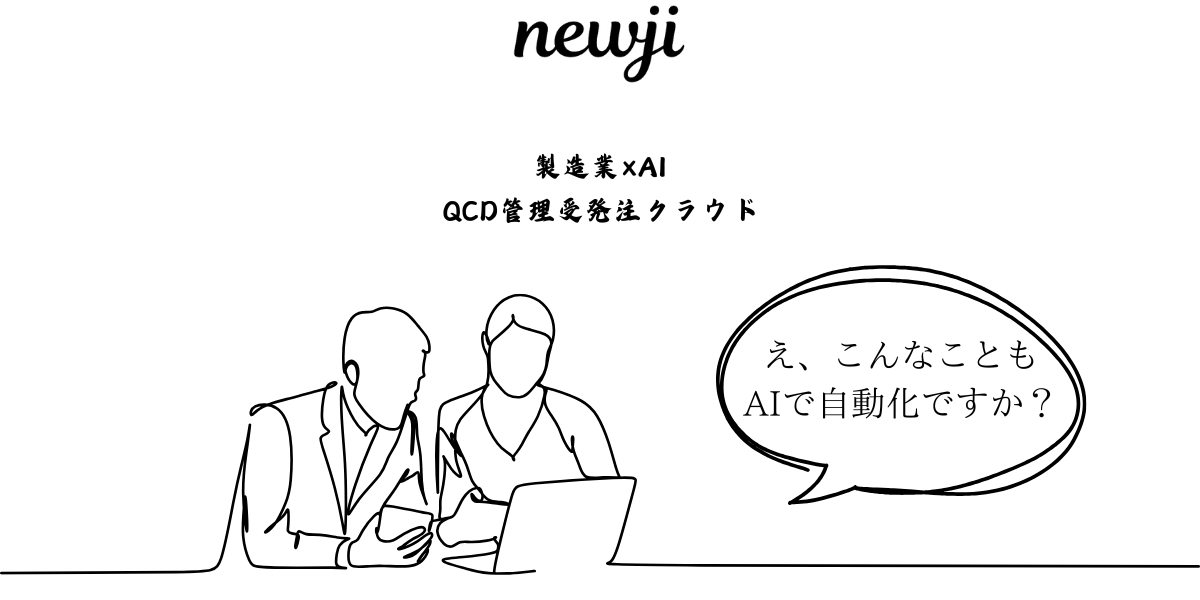
The basics of quality function deployment (QFD), how to utilize it for quality control, and its key points
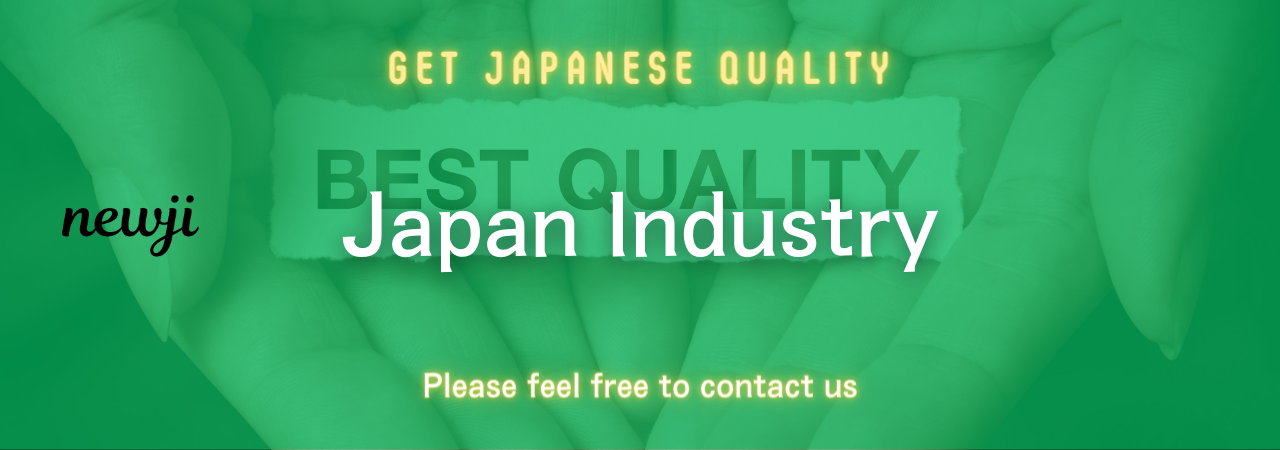
目次
Understanding Quality Function Deployment (QFD)
Quality Function Deployment, commonly abbreviated as QFD, is a tool used in product development and quality management that helps organizations understand and prioritize customer requirements and transform them into specific product attributes or actions.
Originating from Japan in the late 1960s, QFD was introduced by Yoji Akao to bridge the gap between customer needs and product development.
Over time, it has become an integral part of quality control and management processes worldwide.
Essentially, QFD is a structured approach to defining customer needs (or requirements) and translating them into detailed features or actions for a product or service.
Why QFD is Important
QFD ensures that the voice of the customer is clearly heard throughout the product design and development process.
It aligns business goals with customer demands, promoting more effective communication between departments like marketing, design, engineering, and manufacturing.
By accurately mapping out customer demands, companies can minimize the risk of project failures resulting from incorrect assumptions or overlooked aspects.
It helps to prioritize where improvements can be made for better customer satisfaction and helps in competitive positioning by knowing what aspects are critical to quality.
How to Utilize QFD for Quality Control
Defining Customer Requirements
The initial phase of QFD involves identifying who your customers are and what they need from your product or service.
These requirements are usually framed as qualitative data collected through surveys, interviews, or focus groups.
This data is transformed into a list of What you need to achieve, typically known as “Whats” in the QFD matrix.
Developing the QFD Matrix
The QFD matrix, often referred to as the “House of Quality,” is a conceptual map that provides the means for inter-functional planning and communication.
Starting with the list of customer requirements or “Whats” on the left side, you structure the matrix to see how well the product features or “Hows” align with these needs at the top.
The relationship between “Whats” and “Hows” is then evaluated and scored, creating a robust map that guides development.
Prioritization
Once you have the list of customer requirements and technical requirements in place, the next step is to prioritize these.
This involves determining which requirements have the most significant impact on customer satisfaction and success in the market.
Prioritization can be achieved through a variety of methods, such as scoring systems, pairwise comparisons, or through statistical tools like conjoint analysis.
Deploying QFD in Development
QFD isn’t just about the initial design phase.
Its structured approach means it can be continuously used throughout the lifecycle of product development.
Each stage of development should be revisited with the QFD matrix in hand, ensuring that all decisions align with customer needs and priorities identified earlier.
QFD helps teams stay focused and aligned on objectives by maintaining clear, continuing communication of what is essential from a customer perspective.
Key Points of Implementing QFD
Cross-Functional Collaboration
One of the key strengths of QFD is its reliance on cross-functional collaboration.
This involvement means that teams from various departments such as marketing, development, production, and quality assurance must work together.
Effective collaboration ensures that all perspectives are considered, leading to more holistic and viable product solutions.
Customer-Centric Approach
QFD essentially centers around the customer, ensuring that products are designed with user satisfaction as the priority.
This customer-centric approach leads to the development of products that meet real needs and perform well in the market.
Integrating QFD with Other Tools
QFD doesn’t exist in a vacuum and is often more effective when used in conjunction with other quality management tools such as Failure Mode and Effects Analysis (FMEA) or Six Sigma methodologies.
Doing so allows for a more comprehensive approach to quality control and assurance.
Continuous Improvement
Finally, QFD is not a set-once system; it is an essential part of a continuous improvement strategy.
As customer needs and market conditions change, so must your deployment of QFD.
This flexibility allows organizations to adapt quickly and remain competitive by consistently aligning product offerings with evolving consumer expectations.
Conclusion
Quality Function Deployment (QFD) offers a robust, structured approach to comprehensively understanding customer needs and ensuring they are met through strategic, cross-functional collaboration.
By aligning every aspect of development with customer priorities, organizations can enhance satisfaction, reduce costs associated with rework, and ultimately deliver superior products.
In a world where customer expectations are continually growing, the disciplined application of QFD in quality control processes is an invaluable strategy for achieving competitive excellence.
資料ダウンロード
QCD管理受発注クラウド「newji」は、受発注部門で必要なQCD管理全てを備えた、現場特化型兼クラウド型の今世紀最高の受発注管理システムとなります。
ユーザー登録
受発注業務の効率化だけでなく、システムを導入することで、コスト削減や製品・資材のステータス可視化のほか、属人化していた受発注情報の共有化による内部不正防止や統制にも役立ちます。
NEWJI DX
製造業に特化したデジタルトランスフォーメーション(DX)の実現を目指す請負開発型のコンサルティングサービスです。AI、iPaaS、および先端の技術を駆使して、製造プロセスの効率化、業務効率化、チームワーク強化、コスト削減、品質向上を実現します。このサービスは、製造業の課題を深く理解し、それに対する最適なデジタルソリューションを提供することで、企業が持続的な成長とイノベーションを達成できるようサポートします。
製造業ニュース解説
製造業、主に購買・調達部門にお勤めの方々に向けた情報を配信しております。
新任の方やベテランの方、管理職を対象とした幅広いコンテンツをご用意しております。
お問い合わせ
コストダウンが利益に直結する術だと理解していても、なかなか前に進めることができない状況。そんな時は、newjiのコストダウン自動化機能で大きく利益貢献しよう!
(β版非公開)