- お役立ち記事
- The basics of the Toyota Production System that new employees in the production engineering department should know and its effective implementation.
The basics of the Toyota Production System that new employees in the production engineering department should know and its effective implementation.
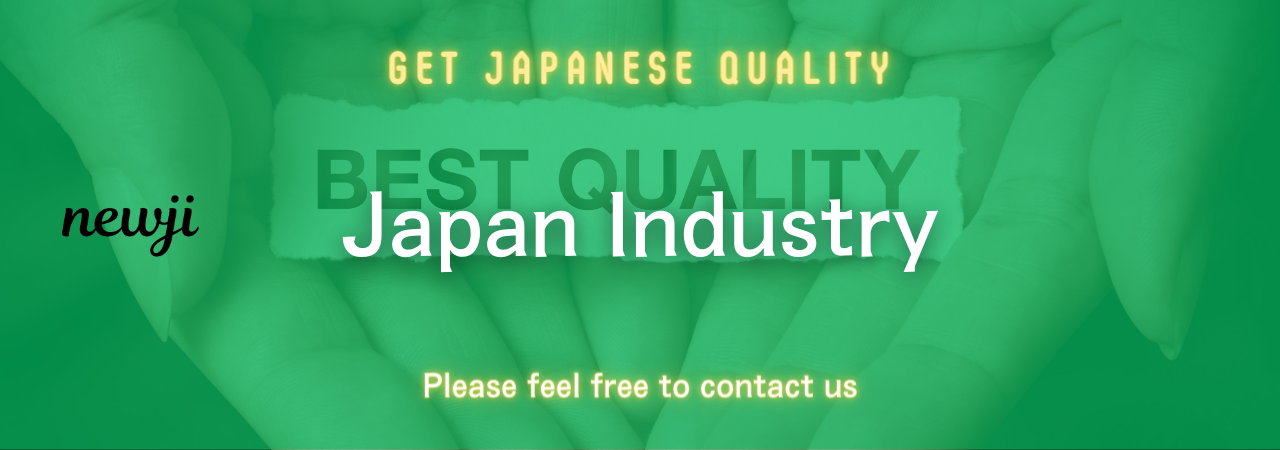
目次
Understanding the Toyota Production System
The Toyota Production System (TPS) is a management philosophy and practice that revolutionized the manufacturing industry.
Developed by Toyota Motor Corporation, TPS is renowned for its efficiency and effectiveness in optimizing production processes.
For new employees in the production engineering department, understanding the basics of TPS is essential as it serves as a foundation for successful implementation in any manufacturing environment.
At its core, TPS is grounded in two key principles: Just-In-Time (JIT) and Jidoka.
Just-In-Time involves producing only what is needed, when it is needed, and in the exact quantity required.
This principle helps reduce waste, improve inventory management, and enhance production efficiency.
On the other hand, Jidoka, or automation with a human touch, ensures that machines and operators stop working as soon as a problem is detected, allowing for immediate quality checks and problem resolution.
By focusing on these principles, TPS aims to eliminate waste, establish a culture of continuous improvement, and enhance productivity.
Understanding these concepts is crucial for new employees, as they will guide their efforts to implement TPS effectively in their roles.
The Pillars of the Toyota Production System
To fully grasp the Toyota Production System, it’s important to understand its two main pillars: continuous improvement, known as “Kaizen,” and respect for people.
Kaizen: The Power of Continuous Improvement
Kaizen is a core component of TPS that emphasizes constant, incremental improvements in all aspects of production.
It is a philosophy that encourages all employees, from the shop floor to top management, to participate in identifying areas for improvement.
This involves a cycle of planning, executing, analyzing, and refining tasks.
In the production engineering department, new employees should engage in Kaizen activities to identify bottlenecks, streamline workflows, and enhance product quality.
By fostering a culture of continuous improvement, companies not only increase efficiency but also motivate employees to think creatively and proactively about optimizing processes.
Respect for People
The second pillar of TPS is respect for people, recognizing that employees are the most valuable resource of any organization.
Toyota believes in empowering its workforce, fostering teamwork, and developing each individual’s potential.
New employees should embrace this philosophy by collaborating with colleagues, sharing knowledge, and valuing each team member’s input.
By showing respect for each person’s contributions, organizations create a supportive environment conducive to innovation and growth.
The Eight Wastes in the Toyota Production System
A critical aspect of the Toyota Production System is identifying and eliminating waste, referred to as “Muda” in Japanese.
TPS categorizes waste into eight types:
1. **Overproduction**: Producing more than is needed leads to excess inventory and wasted resources.
2. **Waiting**: Idle time when resources are not being used efficiently.
3. **Transport**: Unnecessary movement of materials or products that does not add value.
4. **Extra Processing**: Steps that do not add value to the customer or product.
5. **Inventory**: Excess products or materials that are not immediately needed.
6. **Motion**: Unneeded movement by people that does not add value.
7. **Defects**: Flaws in products requiring rework or scrapping.
8. **Underutilized Talent**: Not leveraging employees’ skills and capabilities to the fullest.
New employees should familiarize themselves with these wastes and work towards minimizing them in their areas of responsibility.
By doing so, they can contribute to increased efficiency, reduced costs, and improved quality in production processes.
Effective Implementation of the Toyota Production System
Implementing the Toyota Production System effectively requires a strategic approach and commitment from all levels of the organization.
Here are essential steps to consider for new employees:
Understand and Adopt the Culture
Before implementing TPS, new employees must understand the company’s culture and align themselves with the principles of TPS.
This involves recognizing the importance of teamwork, open communication, and a shared commitment to continuous improvement.
Embracing this mindset will ensure a cohesive approach to TPS implementation.
Conduct a Thorough Analysis
To implement TPS successfully, employees need to assess their current processes and identify areas for improvement.
This involves analyzing production workflows, identifying bottlenecks, and evaluating resource utilization.
By conducting a thorough analysis, employees can pinpoint opportunities for efficiency and waste reduction.
Develop an Implementation Plan
With a clear understanding of the current state, employees can develop a detailed plan for TPS implementation.
This plan should outline specific objectives, strategies, and timelines for rolling out TPS practices.
By setting measurable goals, employees can track their progress and make necessary adjustments to achieve desired outcomes.
Engage and Train Employees
Successful TPS implementation requires engaging and training employees at all levels.
Provide training sessions to familiarize staff with TPS principles and best practices.
Encourage employee involvement in Kaizen activities and foster a learning environment where ideas for improvement are welcomed and valued.
Monitor, Review, and Refine
After implementing TPS, continuous monitoring and review are critical.
Regularly evaluate the effectiveness of TPS practices and use data-driven insights to refine processes.
By consistently seeking improvement, employees can ensure sustained success in optimizing production processes.
The Benefits of the Toyota Production System
The successful implementation of the Toyota Production System offers numerous benefits for organizations:
– **Increased Efficiency**: By eliminating waste and streamlining processes, companies can significantly improve efficiency and reduce operating costs.
– **Enhanced Quality**: The commitment to Jidoka ensures that quality issues are addressed immediately, leading to higher product quality and customer satisfaction.
– **Employee Empowerment**: Emphasizing respect for people and encouraging Kaizen activities empower employees to take ownership of their work and contribute to organizational success.
– **Flexibility and Adaptability**: TPS enables organizations to respond quickly to changes in demand and market conditions, providing a competitive edge.
– **Sustainability**: With a focus on resource optimization and waste reduction, TPS supports sustainable business practices.
By understanding the basics of the Toyota Production System and implementing its principles effectively, new employees can play a vital role in driving growth and success in their production engineering departments.
TPS is not just a set of tools but a philosophy that fosters innovation, teamwork, and continuous improvement, ultimately leading to excellence in manufacturing.
資料ダウンロード
QCD調達購買管理クラウド「newji」は、調達購買部門で必要なQCD管理全てを備えた、現場特化型兼クラウド型の今世紀最高の購買管理システムとなります。
ユーザー登録
調達購買業務の効率化だけでなく、システムを導入することで、コスト削減や製品・資材のステータス可視化のほか、属人化していた購買情報の共有化による内部不正防止や統制にも役立ちます。
NEWJI DX
製造業に特化したデジタルトランスフォーメーション(DX)の実現を目指す請負開発型のコンサルティングサービスです。AI、iPaaS、および先端の技術を駆使して、製造プロセスの効率化、業務効率化、チームワーク強化、コスト削減、品質向上を実現します。このサービスは、製造業の課題を深く理解し、それに対する最適なデジタルソリューションを提供することで、企業が持続的な成長とイノベーションを達成できるようサポートします。
オンライン講座
製造業、主に購買・調達部門にお勤めの方々に向けた情報を配信しております。
新任の方やベテランの方、管理職を対象とした幅広いコンテンツをご用意しております。
お問い合わせ
コストダウンが利益に直結する術だと理解していても、なかなか前に進めることができない状況。そんな時は、newjiのコストダウン自動化機能で大きく利益貢献しよう!
(Β版非公開)