- お役立ち記事
- The basics of VE and how to utilize it for rational cost reduction
月間76,176名の
製造業ご担当者様が閲覧しています*
*2025年3月31日現在のGoogle Analyticsのデータより
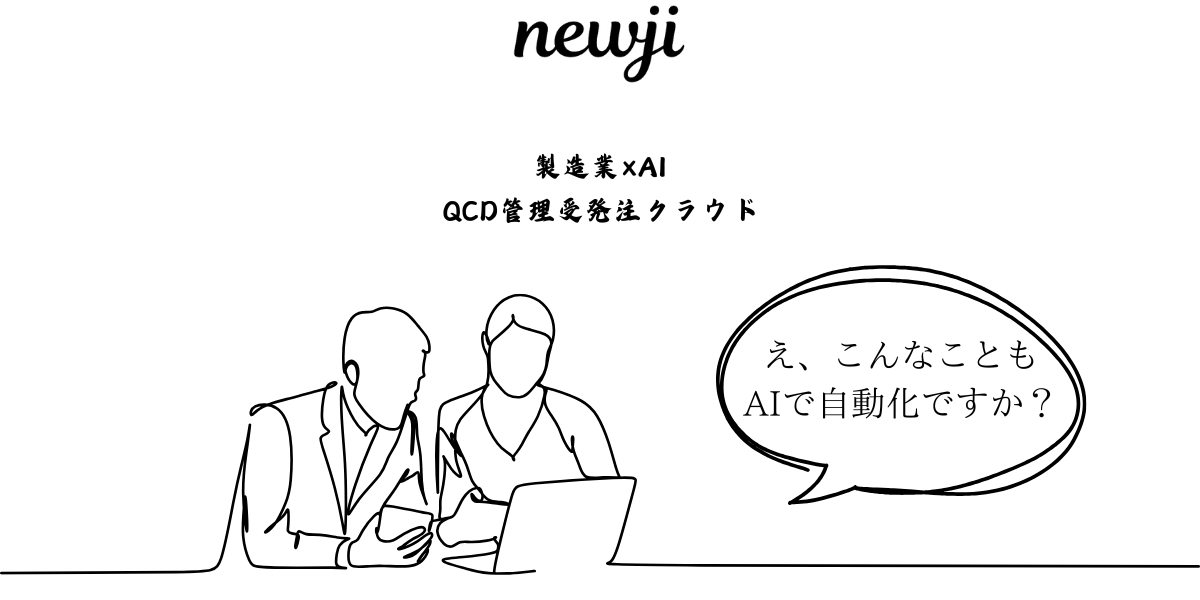
The basics of VE and how to utilize it for rational cost reduction
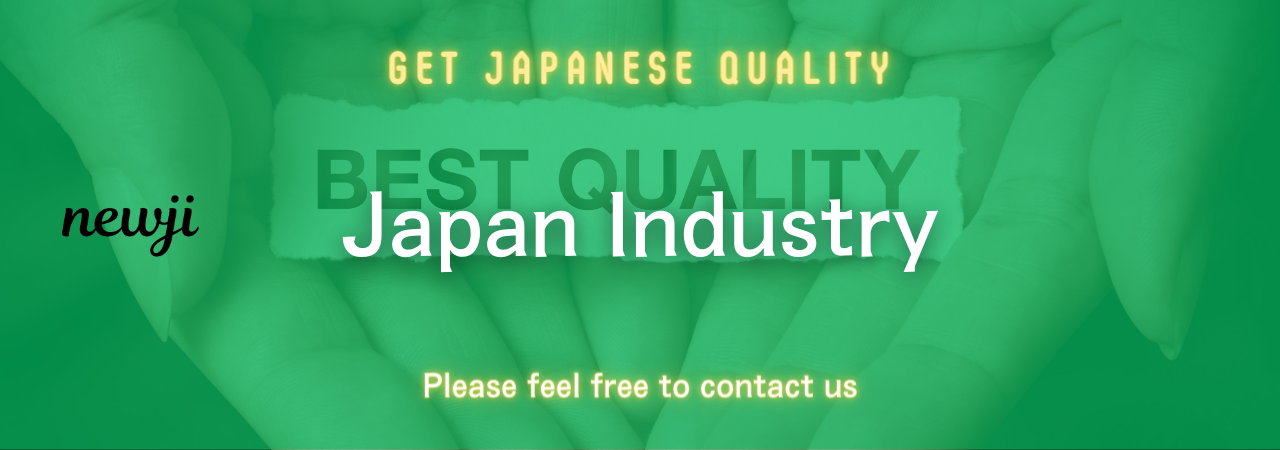
目次
Understanding Value Engineering (VE)
Value Engineering, commonly referred to as VE, is a systematic and organized approach used to improve the value of products or processes.
This methodology focuses on analyzing the functions of systems, equipment, facilities, services, and supplies to ensure the desired functions are achieved at the lowest overall cost.
Value Engineering processes involve creative thinking to explore different solutions, often leading to innovative improvements without compromising quality or performance.
The history of VE dates back to World War II when the scarcity of materials and the need for cost reduction necessitated new ways of thinking in product development.
Today, it is widely utilized in industries ranging from construction and manufacturing to project management and product design.
The Core Principles of Value Engineering
At the heart of Value Engineering are several key principles that guide teams towards effective cost reduction and process improvement.
Function-Oriented Approach
The primary principle of VE is its focus on functions.
It seeks to identify what a product or process is supposed to do and then finds ways to achieve those functions economically.
By defining functions clearly, team members can prioritize efforts to retain or enhance the value of the product while minimizing costs.
Multidisciplinary Team Collaboration
Successful VE initiatives are driven by engaging diverse teams in a collaborative environment.
The teams typically comprise of people from different disciplines, enabling a range of perspectives and expertise that contribute to innovative problem-solving and decision-making.
Systematic Process
Value Engineering follows a structured process, often referred to as the “value methodology”.
This approach includes steps like information gathering, function analysis, brainstorming for creativity, evaluating alternatives, and developing action plans.
By adhering to this systematic process, organizations can ensure thorough evaluations and optimal cost-saving solutions.
The Benefits of Implementing VE
When applied properly, Value Engineering offers multiple benefits that extend beyond mere cost savings.
Improved Product Quality
VE doesn’t only aim at cutting costs.
It emphasizes enhancing the customer’s experience through improved product quality.
By focusing on functions and evaluating alternatives, companies often discover ways to enhance the overall quality and performance of products.
Increased Efficiency
Value Engineering systematically identifies inefficiencies in both products and processes.
By eliminating or altering redundant functions, businesses streamline operations, resulting in higher efficiency and productivity.
Competitive Advantage
Implementing VE gives businesses a competitive edge.
Cost reductions allow companies to price products more competitively while maintaining profitability.
Moreover, innovations arising from VE processes differentiate products in the market, appealing to a broader customer base.
Better Resource Utilization
VE encourages optimal use of materials and resources.
The process identifies unnecessary resource consumption, enabling organizations to redirect savings to other areas like research and development or marketing, further bolstering growth and innovation.
Steps to Utilize VE for Rational Cost Reduction
Effectively employing Value Engineering for cost reduction requires a strategic approach.
Here’s a step-by-step guide to harnessing the potential of VE in your organization:
Step 1: Establish the Scope of the Project
Begin with a clear definition of the project scope.
This includes understanding the objectives, constraints, and requirements.
Clear scope definition guides the entire VE process, ensuring all team efforts align with organizational goals.
Step 2: Gather Information
Collect detailed information about the current product or process.
Understand its design, materials used, functions, and associated costs.
This extensive information-gathering phase provides a comprehensive understanding, laying the groundwork for effective analysis and decision-making.
Step 3: Conduct Function Analysis
Break down the product or process into its essential functions.
Arrange these functions in order of importance and cost implication.
The goal here is to understand which functions are critical and their relationship to cost.
Step 4: Generate Creative Alternatives
Engage the team in brainstorming sessions to generate a wide range of alternatives.
At this stage, creativity is at its peak, encouraging all ideas, even unconventional ones, to surface.
Focus on how different ideas might fulfill the required functions more cost-effectively.
Step 5: Evaluate and Develop Solutions
Assess the feasibility, cost, and effectiveness of all generated alternatives.
Prioritize solutions based on their ability to reduce costs while maintaining or improving function.
Develop detailed plans for implementing the selected alternatives, ensuring that new solutions are thoroughly vetted and aligned with project objectives.
Step 6: Implement and Monitor
Once the best alternatives are identified, move forward with implementation.
This involves coordination among different teams to ensure smooth execution.
Monitor the implementation process closely, making necessary adjustments and ensuring that cost savings are realized without sacrificing quality.
Common Challenges in VE Processes
While Value Engineering offers substantial benefits, it also presents challenges.
Resistance to Change
Cultural resistance within organizations to adopt new methods can impede VE success.
Effective communication and leadership are key to overcoming resistance and fostering an environment open to change.
Maintaining Quality
A common misconception is that cost reduction through VE might compromise quality.
However, a well-conducted VE process maintains, if not enhances, quality by focusing on value rather than just cost.
Comprehensive Data Requirement
VE demands extensive data for analysis, which can be daunting for some organizations.
Establishing efficient data collection systems and involving the right information management personnel can alleviate this challenge.
Conclusion
Value Engineering is a powerful tool for rational cost reduction and innovation.
By focusing on functions, engaging multidisciplinary teams, and following a systematic process, organizations can achieve significant cost savings while elevating quality and efficiency.
Despite challenges, the strategic implementation of VE can result in a strong competitive advantage and sustainable business growth.
資料ダウンロード
QCD管理受発注クラウド「newji」は、受発注部門で必要なQCD管理全てを備えた、現場特化型兼クラウド型の今世紀最高の受発注管理システムとなります。
ユーザー登録
受発注業務の効率化だけでなく、システムを導入することで、コスト削減や製品・資材のステータス可視化のほか、属人化していた受発注情報の共有化による内部不正防止や統制にも役立ちます。
NEWJI DX
製造業に特化したデジタルトランスフォーメーション(DX)の実現を目指す請負開発型のコンサルティングサービスです。AI、iPaaS、および先端の技術を駆使して、製造プロセスの効率化、業務効率化、チームワーク強化、コスト削減、品質向上を実現します。このサービスは、製造業の課題を深く理解し、それに対する最適なデジタルソリューションを提供することで、企業が持続的な成長とイノベーションを達成できるようサポートします。
製造業ニュース解説
製造業、主に購買・調達部門にお勤めの方々に向けた情報を配信しております。
新任の方やベテランの方、管理職を対象とした幅広いコンテンツをご用意しております。
お問い合わせ
コストダウンが利益に直結する術だと理解していても、なかなか前に進めることができない状況。そんな時は、newjiのコストダウン自動化機能で大きく利益貢献しよう!
(β版非公開)